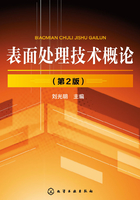
2.6 化学镀
化学镀也称为无电解镀,是一种不使用外电源,而是利用还原剂使溶液中的金属离子在基体表面还原沉积的化学处理方法,即
Men++还原剂 Me+氧化剂
化学镀是一个自催化的过程,也就是基体表面及在其上析出的金属都具有自催化的能力,使镀层能够不断增厚。
化学镀的溶液组成一般包括金属盐、还原剂、络合剂、pH缓冲剂、稳定剂、润湿剂和光亮剂等。当镀件进入化学镀溶液时,镀件表面被镀层金属覆盖以后,镀层本身对上述氧化和还原反应的催化作用,保证了金属离子的还原沉积得以在镀件上继续进行下去。
与电镀相比,化学镀有以下优点。
①在复杂结构的镀件上可以形成较均匀的镀层;
②镀层的针孔一般比较小;
③可以直接在塑料等非导体上形成金属镀层;
④镀层具有特殊的化学、机械或磁性能;
⑤不需要电源,镀件表面无导电触点。
早在1844年A.Wurtz就发现了次亚磷酸盐在水溶液中能还原出镍的现象,以后相继还有一些报道,但都没有实用价值。而美国国家标准局的A.Brenner和G.Riddell开发了可工作的镀液并进行了相关的研究,因此,他们被认为是化学镀技术真正的奠基者。第二次世界大战末的1944年,A.Brenner和G.Riddell正在从事轻武器的改进研究,他们考虑在枪管内壁电镀热硬性好的镍-钨合金。由于所得的合金内应力很高,总是开裂,他们将之归咎于镀液中柠檬酸的氧化分解。为了克服这一缺点,他们尝试给镀液中添加各种还原剂,当加入次亚磷酸钠时,意外发现虽然仅在钢管中装了阳极,但外表面也沉积了镀层,并且电流效率高达理论值的130%,这是常规电镀无法达到的。经过反复试验研究,他们最终确认镍在次亚磷酸盐溶液中具有自催化还原性质,并于1946年在《国家标准局研究杂志》上发表了实用化学镀镍的第一篇文章,并于1950年获得了最早的两个化学镀镍专利。经过几十年的发展,化学镀金属的种类不断增加,目前已经能用化学镀的方法得到镍、铜、钴、钯、铂、金、银等金属或合金的镀层。化学镀既可以作为单独的加工工艺用来改善材料的表面性能,也可以用来获得非金属材料电镀前的导电层。化学镀在电子、石油化工、航空航天、汽车制造、机械等领域有着广泛的应用。
2.6.1 化学镀镍
(1)化学镀镍技术的发展
在前面已经介绍过,化学镀就是从化学镀镍开始发展的。迄今为止,化学镀镍已经有50多年的发展历史。经过半个多世纪的发展,化学镀镍不仅在工艺方面得到了很大的发展,而且在实际生产中的应用也越来越广泛。
自A.Brenner和G.Riddell发明了化学镀镍技术后,G.Gutzeit在他们的工作基础上比较系统地论述了化学镀镍的机理,还原剂、络合剂的性质和作用,称为化学镀镍的理论基础。1955年在美国通用运输公司建成了第一条试生产线,用化学镀镍镀覆运输苛性碱贮槽内壁,开始了化学镀镍的工程应用。但由于成本高、镀液寿命短,而且含有某些有毒物质,使应用受到限制。到了20年代70年代,科学技术的发展和工业的进步,极大地促进了化学镀镍的应用和研究。化学镀镍在工艺、配方、监控、维护、废液处理等方面都获得了迅速的发展。20世纪80年代后,化学镀镍技术有了很大的突破,是化学镀镍技术研究、开发和应用飞速发展时期。一方面开发了耐蚀性较好的含磷9%~12%(质量分数)的高磷非晶结构镀层;另一方面初步解决了化学镀镍中长期存在的一些问题,如镀液寿命、稳定性等;同时基本实现了镀液的自动控制,使连续化的大型生产有了可能。因此,化学镀镍的应用范围和规模进一步扩大。尤其是西方工业化国家化学镀镍的应用,与其他表面处理技术激烈竞争的情况下,年净增长速度曾达15%。20世纪80年代末90年代初,含磷1%~4%(质量分数)的低磷镀层和其他化学镀镍工艺相继被开发出来。低磷镀层具有硬度高、耐磨性好及可焊性好等优点,其镀态硬度可达HV700,耐磨性与硬铬相近,其粘着磨损、微振磨损、疲劳磨损都远低于中磷和高磷镀层,而且低磷镀层在碱性介质中有着极佳的耐腐蚀性,但其在酸性介质中耐蚀性较差。低磷镀层的这些特点进一步拓展了化学镀镍的应用范围。
化学镀镍-磷镀层可以通过控制镀层磷含量和热处理工艺来改变镀层的功能特性,比如经过热处理可以使非晶沉积态的镀层转变为结晶态的镀层,从而提高镀层的硬度。除工业上大量机械零件都要求镀层有耐磨、耐蚀性能外,镀层的导电性、可焊性、扩散阻挡性在电子工业中有重要用途。计算机硬盘要求镀层无磁性、无缺陷和可抛光性,光学反光镜则要求镀层内应力接近零,膨胀系数与基底接近以及可抛光性好等。因为化学镀镍层同时具有镀层厚度与零件形状无关、硬度高、耐磨性好和具有天然润滑性以及优良的耐腐蚀性等优点,并且还有许多可随磷含量而改变的磁性、可焊性和可抛光性等功能特性,因此,化学镀镍层被誉为“设计者的镀层”。
由于镀层的质量取决于镀液、工艺条件等因素,因此对镀液的研究十分重要。伴随着化学镀镍技术的发展,对镀液成分进行了不断的革新。1955年,美国通用运输公司在做了大量研究的基础上,第一次提出了商品化的“卡尼根”(Kanigen,Catalytic Nickel Generation 的简写,意为“新一代催化镀镍”)法,并应用于运输氢氧化钠溶液的槽车贮槽内壁获得成功。1964年和1968年又相继开发了Duraposit和Durnicoat法。1978—1982年又开发成功以“诺瓦台克”(Novotect)为代表的第三代化学镀镍商品镀液,这一镀液不用金属和含硫化合物作稳定剂,所得镀层有非常好的耐蚀性。
若按化学镀镍溶液所使用的还原剂进行分类,可将其分为以次磷酸盐为还原剂的化学镀镍,以硼氢化物为还原剂的化学镀镍,以氨基硼烷为还原剂的化学镀镍和以肼为还原剂的化学镀镍。目前,以次磷酸盐为还原剂的化学镀镍占整个化学镀镍总量的99%以上。
(2)化学镀镍原理
以次磷酸盐还原镍离子的化学镀镍的过程的总的反应可以写成如下的形式。
3NaH2PO2+3H2O+NiSO4 3NaH2PO3+H2SO4+2H2+Ni (2-34)
上述总反应的分布反应如下
(2-35)
(2-36)
(2-37)
(2-38)
(2-39)
(2-40)
从式(2-34)~式(2-40)可以看出,采用次磷酸盐为还原剂化学镀镍过程除了还原金属镍外,还还原出磷。所以,以次磷酸盐为还原剂得到的化学镀镍层实际上是镍磷合金镀层。当用含硼的还原剂时,除了还原出金属镍外,也还原出硼。当然,有时可以同时添加两种还原剂,在基体表面沉积出Ni-P-B复合镀层。
化学镀镍溶液一般由镍盐、还原剂、络合剂、pH缓冲剂以及各种添加剂组成。以次磷酸盐为还原剂的化学镀镍溶液有酸性和碱性两种。酸性镀液的特点是化学稳定性好且易于控制、沉积速率较高,镀层含磷量也较高,在生产中得到广泛的应用。碱性镀液的特点是pH范围较宽,镀层的含磷量较低,但镀液对杂质较敏感,镀液的稳定性差,故碱性镀液在生产中应用较少。表2-30为酸性化学镀镍工艺镀液的组成及工艺规范。
表2-30 酸性化学镀镍镀液组成及工艺规范

①主盐 化学镀镍溶液中的主盐为镍盐,一般采用氯化镍或硫酸镍,有时也采用氨基磺酸镍、醋酸镍等无机盐。早期酸性镀镍液中多采用氯化镍,但氯化镍会增加镀层的应力,现大多采用硫酸镍。目前已有专利介绍采用次亚磷酸镍作为镍和次亚磷酸根的来源,一个优点是避免了硫酸根离子的存在,同时在补加镍盐时,能使碱金属离子的累积量达到最小值。但存在的问题是次亚磷酸镍的溶解度有限,饱和时仅为35g/L。次亚磷酸镍的制备也是一个问题,价格较高。如果次亚磷酸镍的制备方法成熟以及溶解度问题能够解决的话,这种镍盐将会有很好的前景。
②还原剂 化学镀镍的反应过程是一个自催化的氧化还原过程,镀液中可应用的还原剂有次亚磷酸钠、硼氢化钠、烷基胺硼烷及肼等。在这些还原剂中以次亚磷酸钠用得最多,这是因为其价格便宜,且镀液容易控制,镀层抗腐蚀性能好等优点。
③络合剂 化学镀镍溶液中的络合剂除了能控制可供反应的游离镍离子的浓度外,还能抑制亚磷酸镍的沉淀,提高镀液的稳定性,延长镀液的使用寿命。有的络合剂还能起到缓冲剂和促进剂的作用,提高镀液的沉积速度。化学镀镍的络合剂一般含有羟基、羧基、氨基等。
在镀液配方中,络合剂的量不仅取决于镍离子的浓度,而且也取决于自身的化学结构。在镀液中每一个镍离子可与6个水分子微弱结合,当它们被羟基、氨基取代时,则形成一个稳定的镍配位体。如果络合剂含有一个以上的官能团,则通过氧和氮配位键可以生成一个镍的闭环配合物。在含有0.1mol的镍离子镀液中,为了络合所有的镍离子,则需要含量大约0.3mol的双配位体的络合剂。当镀液中无络合剂时,镀液使用几个周期后,由于亚磷酸根聚集,浓度增大,产生亚磷酸镍沉淀,镀液加热时呈现糊状,加络合剂后能够大幅度提高亚磷酸镍的沉淀点,即提高了镀液对亚磷酸镍的容忍量,延长了镀液的使用寿命。
不同络合剂对镀层沉积速率、表面形状、磷含量、耐腐蚀性等均有影响,因此选择络合剂不仅要使镀液沉积速率快,而且要使镀液稳定性好,使用寿命长,镀层质量好。
④缓冲剂 由于在化学镀镍反应过程中,副产物氢离子的产生,导致镀液pH值会下降。试验表明,每消耗1mol的Ni2+同时生成3mol的H+,即是在1L镀液中,若消耗0.02mol的硫酸镍就会生成0.06mol的H+。所以为了稳定镀速和保证镀层质量,镀液必须具备缓冲能力。缓冲剂能有效的稳定镀液的pH值,使镀液的pH值维持在正常范围内。一般能够用作pH值缓冲剂的为强碱弱酸盐,如醋酸钠、硼砂、焦磷酸钾等。
⑤稳定剂 化学镀镍液是一个热力学不稳定体系,常常在镀件表面以外的地方发生还原反应,当镀液中产生一些有催化效应的活性微粒——催化核心时,镀液容易产生激烈的自催化反应,即自分解反应而产生大量镍-磷黑色粉末,导致镀液寿命终止,造成经济损失。
在镀液中加入一定量的吸附性强的无机或有机化合物,它们能优先吸附在微粒表面抑制催化反应从而稳定镀液,使镍离子的还原只发生在被镀表面上。但必须注意的是,稳定剂是一种化学镀镍毒化剂,即负催化剂,稳定剂不能使用过量,过量后轻则降低镀速,重则不再起镀,因此使用必须慎重。
所有稳定剂都具有一定的催化毒性作用,并且会因过量使用而阻止沉积反应,同时也会影响镀层的韧性和颜色,导致镀层变脆而降低其防腐蚀性能。试验证明,稀土也可以作为稳定剂,而且复合稀土的稳定性比单一稀土要好。
⑥加速剂 在化学镀溶液中加入一些加速催化剂,能提高化学镀镍的沉积速率。加速剂的使用机理可以认为是还原剂次磷酸根中氧原子被外来的酸根取代形成配位化合物,导致分子中H和P原子之间键合变弱,使氢在被催化表面上更容易移动和吸附。也可以说促进剂能起活化次磷酸根离子的作用。常用的加速剂有丙二酸、丁二酸、氨基乙酸、丙酸、氟化钠等。
⑦其他添加剂 在化学镀镍溶液中,有时镀件表面上连续产生的氢气泡会使底层产生条纹或麻点。加入一些表面活性剂有助于工件表面气体的逸出,降低镀层的孔隙率。常用的表面活性剂有十二烷基硫酸盐、十二烷基磺酸盐和正辛基硫酸钠等。
稀土元素在电镀液中可以改善镀液的深镀能力、分散能力和电流效率。研究表明,稀土元素在化学镀中同样对镀液的镀层性能有显著改善。少量的稀土元素能加快化学沉积速率,提高镀液稳定性、镀层耐磨性和腐蚀性能。
(3)印制线路板化学镀镍
印制线路板(Printed Circuit Board)英文简称PCB[图2-7(a)和(b)所示],PCB上常用化学镀镍来作为贵金属和贱金属的衬底镀层,对某些单面印制板,也常用作面层。对于重负荷磨损的一些表面,如开关触点、触片或插头金,用镀镍作为金的衬底镀层,可提高耐磨性。当用来作为阻挡层时,镍能有效地防止铜和其他金属之间的扩散。镀哑镍/金组合镀层常常用来作为抗蚀刻的金属镀层,而且能适应热压焊与钎焊的要求,镍还能够作为含氨类蚀刻剂的抗蚀镀层,而不需热压焊又要求镀层光亮的PCB,通常采用光镍/金镀层。镍镀层厚度一般不低于2.5μm,通常采用4~5μm。目前国内生产的PCB化学镀液已具有良好的性能,如深圳市宏达秋科技有限公司生产的化学镀Ni液,在线路板上制备的镀层镍含量非常稳定(92%±2%重量百分比),在84℃条件下,镍层析出速度达到6~8μinch/min(1inch=25.4mm),结晶致密[图2-7(c)和(d)所示],耐蚀性优良。其镍磷合金层有良好的平整性及挠折性,特别适合于FPC低应力镀膜严苛要求下的高延展性化学镀镍金配套药水,满足焊锡性、打线性能、低表面电阻等多项功能要求。

图2-7 PCB板化学镀镍金(由深圳市宏达秋科技有限公司提供)
(a)硬板化学镀镍金;(b)软板化学镀镍金;(c)镀镍金层表面形貌图;(d)镀镍金截面形貌图
2.6.2 化学镀铜
化学镀铜主要用于非金属材料的表面金属化和印制电路板孔的金属化及电子仪器的屏蔽层。化学镀铜层通常很薄,只有0.1~0.5μm。作为功能镀层时厚度较大,为1~10μm。化学镀铜层的物理机械性能与金属铜差异很大,尤其是延展性和韧性较金属铜差很多。如化学镀铜时氢渗入镀层、有机杂质等夹杂在镀层中,都有可能使镀层呈脆性。适当的添加剂、镀后处理及加强搅拌可改善其延展性。镀层的硬度较高,电阻率比实体金属铜大。
由不同镀液得到的化学镀铜层均为纯铜(与化学镀镍不同)。铜的标准电极电位为正值,较易从溶液中析出。化学镀铜时最常用的还原剂为甲醛,但甲醛有强烈的臭味,对人体有害。因此,近年来也采用其他还原剂,如肼、次磷酸钠、硼氢化物和乙醛酸等,但应用较少。化学镀铜时,常用的络合剂为酒石酸钾钠和乙二胺四乙酸钠(EDTA)。前者价格便宜,后者的镀液稳定性更好。
化学镀铜时的化学反应包括
Cu2++2HCHO+4OH- Cu+2HCOO-+H2↑+2H2O (2-41)
该反应为主反应,在化学镀铜时还发生如下的副反应
2HCHO+OH- CH3OH+HCOO- (2-42)
2Cu2++HCHO+5OH- Cu2O+HCOO-+3H2O (2-43)
Cu2O+H2O Cu+Cu2++2OH- (2-44)
其中甲醛歧化的副反应是自身无意义的消耗,第二个副反应的Cu2O会歧化生成分散在镀液中的铜微粒,导致镀液分解。因此,应尽量减少这些副反应,如加络合剂、稳定剂等添加剂。表2-31酒石酸钾钠化学镀铜镀液组成及工艺规范。
表2-31 酒石酸钾钠化学镀铜镀液组成及工艺规范

化学镀铜的主盐常用硫酸铜,也可以用硝酸铜、氯化铜、碳酸铜、氧化铜和酒石酸铜等。铜盐浓度增加,沉积速度逐渐增加至一定值。镀层质量与铜盐浓度关系不大。添加剂包括稳定剂、加速剂和表面活性剂。
稳定剂的作用域络合剂一样,是为了提高镀液稳定性。化学镀铜的稳定剂多为含氮或硫的化学物,如氰化物、硫化物、硫氰化物、亚铁氰化钾、吡咯、硫脲等。如果同时含有硫和氮,效果会更好。
加速剂有去极化作用,因而能加快沉积速度。常用的有苯并二氮唑、胍、2-球基本并噻唑等,许多稳定剂同时也是加速剂。
表面活性剂使表面张力降低,有助于氢气的析出,以减少镀层的脆性。非离子型表面活性剂效果较好,如脂肪醇聚氧乙烯醚、脂肪醇胺等。
2.6.3 非金属表面化学镀
在非金属表面镀覆一层金属可使其既具有非金属的特点也具有金属的特点。近年来,已能成功地在玻璃、陶瓷、纤维以及其他一些非金属制品表面镀覆一层金属层。目前,在塑料表面镀覆金属仍是应用最广的。塑料的金属化可用作装饰,被广泛应用于汽车、游轮、飞机上,以实现其轻量化和获得豪华的外观。此外,电子电器类也是装饰性塑料和树脂电镀的重要应用领域,目前流行的手机、U盘、笔记本等产品的外壳大都采用金属化的塑料。在家庭用品、文具、建筑装饰、工艺品、艺术品等领域,塑料金属化也起到举足轻重的作用。
金属化的塑料易于加工成型,因此被广泛应用于功能材料上,具体可分成两大类。首先是机械类的应用。以齿轮和齿条为例,未金属化的塑料齿轮、齿条由于其机械性能不佳,只能应用于玩具和非精密仪器上,但是金属化后的塑料在机械强度和耐磨性上都有所提高,可应用于更广阔的领域。对于强度要求更高的制品,可以采用玻璃纤维增强的树脂,如玻璃钢(FRP)。其次是电子方面的应用,如高频电器屏蔽、印刷板孔位金属化、燃料计电极、无涡流开关、电波反射体、选择性透光体等。电子类产品的功能性要求大多与电子传递、电波传送及导磁导电有关,通常只要求材料的表面赋有金属的性能即可,这就为塑料表面金属化的应用提供了舞台。例如,在塑料表面化学镀一层非磁性的Ni-P合金,使其具有较好的耐磨性和耐蚀性,而且能屏蔽磁性,可用作磁储存材料,推动了信息技术和信息产业的发展。
非金属材料表面金属化的方法有很多,包括电镀、化学镀等。其中,非金属材料表面电镀的关键也是需要通过化学镀的方法在其表面生成一层导电层以便进行电镀。所以,化学镀方法是目前较为广泛采用的非金属材料表面金属化的方法。
非金属材料表面化学镀金属层的镀液与金属基体相比差别不大。非金属基体的镀前处理是获得良好金属层的关键。根据化学镀的原理,化学镀是利用材料表面的自催化特点将溶液中的金属离子还原成金属并沉积在其表面的过程。依照化学镀镍反应中不同基体的表面情况,可将之分为5 类:①本身对化学镀镍具有催化活性的金属,如Fe、Co、Ni、Pd 等,施镀前作简单的预处理即可;②不具有催化活性但能从镀液中置换出金属镍的金属,如Zn、Mg、Al 等,镀前作简单的预处理,但要防止金属溶解对镀液可能造成的危害;③无活性也不能置换出金属镍的导体,如Cu、黄铜、石墨等,镀前必须采取适当的诱发或活化工艺;④非导体,如塑料、橡胶、陶瓷等,镀前必须作活化处理;⑤导体与非导体的复合体,如PCB,一般需要对导体部分进行化学镀处理。
对于非金属材料在化学镀之前的预处理主要包括除油、粗化、敏化及活化等过程。
粗化的目的在于提高零件表面的亲水性和形成适当的粗糙度,以保证镀层有良好的附着力。粗化的方法有许多种,效果不一。就提高镀层附着力而言,化学侵蚀粗化>溶剂溶胀粗化>机械粗化,有时也可同时采用几种粗化方法。现在工业生产中,ABS塑料已经不采用机械粗化与溶剂粗化这两种粗化而仅采用化学粗化法。
化学浸蚀粗化(化学粗化)溶液一般由铬酐、硫酸组成。在配置这样的粗化溶液时,应先用水将铬酐溶解,在搅拌下倒入硫酸,最后加水至所需的体积。随着现代工业对环保的要求越来越高,一些不含铬酐的粗化剂正在研发中。
粗化处理之后的零件,一般还需要进行敏化及活化处理。敏化是使粗化后的零件表面吸附一层有还原性的二价锡离子,以便在随后的离子型活化处理时,将银或者钯离子还原成有催化作用的银或钯原子。敏化液一般由氯化亚锡、盐酸组成,具体的配方可参考相关资料。
活化处理是在敏化后进行的,其目的是使零件表面形成一层有催化作用的贵金属层,以使化学镀能够自发进行。最常见的活化液是氯化钯和盐酸的混合溶液,该溶液对化学镀铜、镍、钴等都有催化活性作用,而且溶液比较稳定,缺点是钯盐价格昂贵。
随着非金属表面金属化工艺的发展,新型非金属材料化学镀、电镀之前的表面处理工艺不断涌现。上面介绍的是常规的、最常用的处理工艺。
2.6.4 化学复合镀
化学复合镀是化学镀与复合电镀的结合,即在化学镀中加入非水溶性固体微粒,当这些悬浮在镀液中的微粒与金属共沉积,就形成化学复合镀层。化学复合镀所应具备的条件和影响因素与化学镀和复合电镀相近,组成更复杂,管理更难。
化学复合镀综合了化学镀与复合电镀的优点。随固体微粒的不同,可以获得耐磨、润滑、耐腐蚀、耐高温等不同性能的化学复合镀层,而且厚度均匀,平滑致密。原则上,能进行化学镀的许多金属都可以进行化学复合镀。但至今研究与应用最多的是化学复合镀镍。Ni-P-SiC、Ni-P-Al2O3、Ni-B-Al2O3和Ni-P-SiO2化学复合镀层的硬度和耐磨性比电镀镍和化学镀镍高得多。经过热处理后硬度更高,其耐磨性高于复合电镀镍层。一般,各种镀镍层的硬度按照下列顺序依次增加:电镀镍,化学镀Ni-P合金,经热处理的化学镀Ni-P合金,化学复合镀Ni-P-SiC镀层,经热处理的Ni-P-SiC化学复合镀层。Ni-P-PTFE(聚四氟乙烯),Ni-P-(CF)n和Ni-P-MoS2化学复合镀层具有良好的自润滑性能,摩擦系数低,抗黏着力强,耐磨损性好。化学复合镀镍在工业领域,如汽车、机械、模具和电子工业等中有所应用。
化学复合镀液中固体微粒含量越高,镀层中微粒含量也就越高。一般,镀液中微粒的含量应是镀层中共析量的10倍左右。而镀层中金属与微粒的比可通过调节镀液的组成来控制。一般来说,镀液中微粒的最佳体积分数为5%左右。现在所应用的化学复合镀层中微粒的体积分数为20%~30%,微粒适宜的粒径在1~10μm的范围,镀层厚度多为12~25μm。化学复合镀镍通常用次磷酸钠为还原剂的基础镀液。