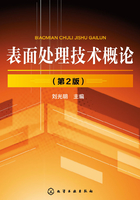
2.2 单金属电镀
2.2.1 镀锌
锌是一种银白色微带蓝色的金属。金属锌较脆,只有加热到100~150℃才有一定延展性。锌的硬度低,耐磨性差。锌是两性金属,既溶于酸也溶于碱。特别是当锌中含有电位较正的杂质时,锌的溶解速度更快。但是电镀锌层的纯度高,结构比较均匀,因此在常温下,锌镀层具有较高的化学稳定性。
锌镀层主要镀覆在钢铁制品的表面,作为防护性镀层。锌的标准电极电位为-0.76V,比铁的电位负,为阳极性镀层。在钢铁表面镀锌层既有机械保护作用,又有化学保护作用。镀锌层经钝化后形成彩虹色或白色钝化膜层,在空气中非常稳定,在汽油或含二氧化碳的潮湿空气中也很稳定,但在含有SO2、H2S、海洋性气氛及海水中镀锌层的耐蚀性较差,特别是在高温、高湿及含有有机酸的气氛中,镀锌层的耐蚀性极差。
电镀锌是生产上应用最早的电镀工艺之一,工艺比较成熟,操作简便,投资少,在钢铁件的耐蚀性镀层中成本最低。作为防护性镀层的锌镀层的生产量最大,约占电镀总产量的50%左右,在机电、轻工、仪器仪表、农机、建筑五金和国防工业中得到广泛的应用。近来开发的光亮镀锌层,涂覆护光膜后使其防护性和装饰性都得到进一步的提高。
镀锌溶液种类很多,按照其性质可分为氰化物镀液和无氰化物镀液两大类。氰化物镀锌溶液具有良好的分散能力和覆盖能力,镀层结晶光滑细致,操作简单,适用范围广,在生产中曾被长期采用,但镀液中含有剧毒的氰化物,在电镀过程中逸出的气体对工人健康危害较大,其废水在排放前必须严格处理。无氰化物镀液有碱性锌酸盐镀液,氯化铵镀液、硫酸盐镀锌及无铵盐氯化物镀液等。其中碱性锌酸盐和无铵盐氯化物镀锌应用最多。
2.2.1.1 氰化物镀锌
氰化物镀锌工艺自20世纪初投入工业生产并沿用至今。该工艺的特点是电镀液以氰化钠为络合剂的络合物型电镀液,具有较好的分散能力和深镀能力。允许使用的电流密度范围和温度范围都较宽,电解液对杂质的敏感性小,工艺容易控制,操作及维护都很简单。
(1)氰化物镀锌镀液的组成及作用
氰化物镀锌溶液根据氰含量多少分可为高氰、中氰、低氰三种类型,其镀液组成及工艺条件见表2-2。
表2-2 氰化物镀锌电镀液组成及工艺条件

高氰镀液含氰化钠量在80g/L以上,镀液稳定性好,镀层结晶细致,适用于电镀形状复杂和镀层较厚的零件,但氰含量高,对环境污染严重。目前应用较多的是中氰镀液,这类镀液含锌量也低,其氰化钠与锌的比值接近于高氰,因此,镀层质量也比较好。低氰镀液氰化钠含量10g/L左右,一般需配合使用合适的光亮剂来提高镀层质量和镀液的分散能力。氰化物镀液的电流效率较低,随电流密度的升高其电流效率迅速降低。氰化物剧毒,要求采用良好的通风设备和必要的安全管理措施和三废处理措施。
氧化锌是提供锌离子的物质,为主盐。配制镀液时,氧化锌与氰化钠、氢氧化钠反应生成[Zn(CN)4]2-和[Zn(OH)4]2-,锌含量升高使电流效率提高,但镀层粗糙;锌含量过低,电流效率下降,分散能力和覆盖能力增加。锌含量在0.125~0.5mol/L的范围为宜,生产上常控制在0.5mol/L左右。
氰化钠是主络合剂,氢氧化钠是辅助络合剂(在低氰、微氰镀锌液中是主络合剂)。除与Zn2+络合外,还应有少量游离氰化钠和游离氢氧化钠,才能使复层结晶细致。通常,氢氧化钠用量为60~90g/L,NaOH∶Zn(质量比)为2∶2.5,NaOH∶NaCN(质量比)为1∶1。
硫化钠是一种主要的添加剂。镀锌液中常常带入一些铅、铜、镉等重金属杂质。由于这些金属的电位较正,易在阴极与锌共沉积而影响镀层的质量。加入适量的硫化钠可使之生成硫化物沉淀以保证镀层质量。除此以外,硫化钠还具有使镀层产生光亮的作用,加入量为0.5~3g/L。含量过低,起不到光亮作用,含量过高,会使镀层脆性增大。
甘油的作用是为了提高阴极极化,有利于获得均匀细致的镀层,加入量为3~5g/L。
(2)电极反应
阴极主反应
[Zn(CN)4]2-+4OH- [Zn(OH)4]2-+4CN- (2-5)
[Zn(OH)4]2- Zn(OH)2+2OH- (2-6)
Zn(OH)2+2e- Zn+2OH- (2-7)
阴极副反应
2H2O+2e- H2↑+2OH- (2-8)
氰化物镀锌的阳极主反应
Zn Zn2++2e- (2-9)
Zn2+再分别与CN-和OH-络合
Zn2++4CN- [Zn(CN)4]2- (2-10)
Zn2++4OH- [Zn(OH)4]2- (2-11)
当阳极钝化时,还将发生析出氧气的副反应
4OH- 2H2O+O2+4e- (2-12)
2.2.1.2 锌酸盐镀锌
从锌酸盐电镀液中电沉积金属锌早在20世纪30年代就有人研究过。但是,从单纯的锌酸盐电镀液中只能得到疏松的海绵状的锌。为了获得有使用价值的锌镀层,人们寻找了各种添加剂,其中包括金属盐、天然有机化合物以及合成有机化合物。直到20世纪60年代后期才研制出合成添加剂、采用两种或两种以上的有机化合物进行合成,以其合成产物作为锌酸盐镀锌的添加剂,可以获得结晶细致而有光泽的镀锌层。中国于20世纪70年代初将这一添加剂应用于电镀锌的生产。
锌酸盐镀锌可用氰化物镀锌设备,镀液成分简单,易于管理,对设备腐蚀小,废水处理方便,但均镀和深镀能力较氰化物镀液差,电流效率比较低。
(1)锌酸盐镀锌电镀液的成分及作用
锌酸盐镀锌典型镀液配方及工艺见表2-3。
表2-3 锌酸盐镀锌镀液组成及工艺条件

①氧化锌 是镀液中的主盐,提供所需要的锌离子。氧化锌与氢氧化钠作用生成[Zn(OH)4]2-络离子。锌含量对镀液性能和镀层质量影响很大。锌含量偏高,电流效率高,但分散能力和深镀能力下降,镀层粗糙。锌含量偏低时,阴极极化增加,分散能力好,镀层结晶细致,但沉积速度慢,零件的边缘及凸出部位易烧焦。
②氢氧化钠 在锌酸盐镀锌液中,氢氧化钠是络合剂,作为强电解质,它还可以改善电解液的导电,因此,过量的氢氧化钠是镀液稳定的必要条件。氢氧化钠与氧化锌的最佳比值(质量比)是12∶1,生产上一般控制在10~(13∶1)。氢氧化钠含量过高,将加速锌阳极的自溶解,使镀液的稳定性下降。氢氧化钠含量过低,将使阴极极化下降,镀层粗糙,且容易生成Zn(OH)2沉淀。
③添加剂 若无添加剂,锌酸盐镀锌只能得到黑色海绵状镀层。所以在一定程度上,锌酸盐镀锌的添加剂可视为镀液主要成分。现有添加剂品种很多,大致可分为两类。一类是极化型添加剂,为有机胺和环氧氯丙烷缩合物,如DPE系列、DE系列、Zn2、NJ-45、GT-1等。但单独使用这些添加剂时性能并不好,还需要加入第二类添加剂,即所谓光亮剂,为金属盐、芳香醛、杂环化合物及表面活性剂,如ZB-80、ZBD-81、KR-7、WBZ系列、CB-909等。
镀液中杂质铜可以用锌粉、铝粉置换处理,铅可以用硫化钠沉淀除去,有机杂质可先加双氧水,再加活性炭处理。
(2)电极反应
阴极主反应
[Zn(OH)4]2-+2e- Zn+4OH- (2-13)
阳极主反应
Zn Zn2++2e- (2-14)
2.2.1.3 氯化钾(钠)镀锌
氯化物镀锌可以分为氯化铵镀锌和无铵氯化物镀锌两大类。氯化铵镀锌由于对设备腐蚀严重,废水处理困难等原因,已经逐渐被淘汰。20世纪70年代后期发展起来的氯化钾(钠)镀锌,不仅完全具备了氯化铵镀锌的优点,而且还克服了其存在的缺点,因此得到了迅速的发展。目前根据粗略统计,在我国氯化钾(钠)镀锌溶液的体积已经超过了镀锌溶液总体积的50%。
氯化钾(钠)镀锌电解液成分简单,与氰化物镀锌及锌酸盐镀锌相比,镀液的稳定性高,而且电解液呈微酸性(pH值在5~6.5),对设备的腐蚀小。氯化钾(钠)镀锌电解液中的Cl-离子与Zn2+离子的络合能力很弱,其废水处理简单容易。在电镀过程中除了极少量氢气和氧气逸出外,无其他碱雾、氨气等污染,无需排风设备。另外,该工艺所得到的镀层极适宜在低铬酸和超低铬酸钝化液中进行钝化处理,这就大大减轻了钝化废水处理的负担。
(1)氯化钾(钠)镀锌电解液的组成及作用
氯化钾(钠)镀锌电解液的组成及工艺条件见表2-4。
表2-4 氯化钾(钠)镀锌电解液的组成及工艺条件

①氯化锌 氯化锌是提供锌离子的主盐,浓度较低,由于锌离子扩散快,浓差极化大,镀层细致光亮,分散能力和覆盖能力好。但是,如果浓度太低,则高电流区易烧焦。浓度偏高时,阴极电流密度可以开大,沉积速度也快,但覆盖能力和分散能力差。一般较佳浓度为70~80g/L,对难以电镀的铸铁件,槽液中锌含量可取上限,夏季镀液温度高,锌含量取下限,冬季含量可略高一些。
②氯化钾(钠) 是电解液中的导电盐。从导电性来看,氯化钾优于氯化钠,一般复杂零件用钾盐为宜,因钠盐价格低,简单零件用氯化钠也可以。镀液中氯化物的增加可使镀液的导电性和分散能力增加并能活化阳极使其正常溶解。另外,氯离子对锌离子有微弱的络合作用,能起到增加阴极极化和改善镀液分散性的作用。
氯化物含量过低不但溶液导电性差,分散能力也差,而且镀层不光亮,易产生黑色条纹。但含量过高时,阴极沉积速度降低,而且影响光亮剂的水溶性。氯化钾(钠)与氯化锌的质量比一般为(2.5~3)∶1。
③硼酸 硼酸为缓冲剂,含量一般控制在20~35g/L为宜,能够使氯化钾(钠)镀锌电镀液的pH值维持在5~6.5之间。
④光亮剂 氯化钾(钠)镀锌使用的是组合光亮剂,由主光亮剂、载体光亮剂和辅助光亮剂组合而成。
主光亮剂能吸附在阴极表面,增大阴极极化,是镀层结晶细致、光亮。主要有三类:芳香族类,如芐叉丙酮、苯甲酰胺;氮杂环化合物,如3-吡啶甲酰胺;芳香醛类,如肉桂醛。其中以芐叉丙酮效果最好,国内市场销售的商品添加剂都是以芐叉丙酮为主光亮剂。
芐叉丙酮很难溶于水,必须加入一定量的助剂,使主光亮剂以极高的分散度分散在电镀液中,才能在电镀过程中发挥作用。这些助剂在电镀中被称为载体光亮剂,常用的有OP-乳化剂和聚氧乙烯脂肪醇醚等。
辅助光亮剂与主光亮剂配合使用可增大阴极极化,特别是对低电流密度区影响更大,能够在低电流密度区得到光亮的镀层,同时使镀液的分散能力提高。目前生产中采用的辅助光亮剂主要有:芳香族羧酸盐,如苯甲酸钠;芳香族羧酸,如肉桂酸;磺酸盐,如亚甲基双萘磺酸钠。
(2)电极反应
虽然Cl-离子也能与Zn2+离子络合,但络合能力很弱。因此氯化钾(钠)镀锌仍属于简单盐电解液电镀,其阴极反应为Zn2+离子还原为金属锌,反应方程式如下
Zn2++2e- Zn (2-15)
同时还有可能发生H+离子还原为氢气的副反应
2H++2e- H2↑ (2-16)
阳极反应为金属锌的电化学溶解
Zn Zn2++2e- (2-17)
当阳极电流密度过高时,阳极进入钝化状态,此时还将发生析出氧气的副反应
4OH- 2H2O+O2+4e- (2-18)
2.2.2 镀镍
镍镀层是应用最普遍的一种装饰、防护镀层。自从1840年英国人J.Shore获得第一个电镀镍专利以来,镀镍工艺得到了不断发展,镀种不断增多,其应用也从传统的防护、装饰性镀层发展到多种功能性镀层。镀镍层的应用几乎遍及现代工业的所有部门,在电镀行业中,镀镍层的产量仅次于镀锌层而居于第二位。
金属镍具有很高的化学稳定性,在稀酸、稀碱基有机酸中具有很好的耐蚀性,在空气中镍与氧相互作用可形成保护性氧化膜而使金属镍具有很好的抗大气腐蚀性能。但由于镀镍层的孔隙率较高,且镍的电极电位比铁更正,使得镍镀层只有在足够厚且没有空隙时才能在空气和某些腐蚀性介质中有效地防止腐蚀。因此常采用多层镍铬体系及不同镍镀层组合来提高防护性能。
镀镍主要应用在日用五金产品、汽车、自行车、摩托车、家用电器、仪器、仪表、照相机等的零部件上,作为防护—装饰性镀层的中间镀层。由于镍镀层具有较高的硬度,在印刷工业中用来提高表面硬度,也用于电铸、塑料成型模具等。
镀镍工艺按镀层的外观、结构特征可分为普通镀镍(暗镍)、光亮镀镍、黑镍、硬镍、多层镍等。按镀液的成分可分为硫酸盐型、氯化物型、柠檬酸盐型、氨基磺酸盐型、氟硼酸盐型等。其中应用最为普遍的是硫酸盐低氯化物镀镍液(即瓦特镀液)。氨基磺酸盐镀液镀层内应力小,沉积速度快,但成本高,仅用于特定的场合。柠檬酸盐镀液常用于锌压铸件上镀镍。氟硼酸盐镀液适用于镀厚镍,但这几种类型镀液的成本都较高。
这里主要介绍普通镀镍,光亮镀镍和黑镍等。
(1)普通镀镍
普通镀镍又称为电镀暗镍或无光泽镀镍,是最基本的镀镍工艺。暗镍镀液主要由硫酸镍、少量氯化物和硼酸组成。用这种镀液获得的镍镀层结晶细致、易于抛光、韧性好、耐蚀性也比亮镍好。暗镍常用于防护—装饰性镀层的中间层或底层。
①普通镀镍镀液组成及作用 常用的普通镀镍电镀液组成及工艺规范见表2-5。依使用目的,普通镀镍液常分为预镀液和常规镀液两类。预镀液主要用于增强钢铁基体与镀层(如镀铜层)之间的结合。
表2-5 普通镀镍液的组成及工艺条件

普通镀镍镀液一般由主盐、阳极活化剂、缓冲剂、防针孔剂和导电盐等部分组成。
a.主盐 硫酸镍是镀镍溶液中的主盐,提供镀镍所需要的Ni2+离子,浓度一般在100~350g/L。镍盐浓度低,镀液分散能力好,镀层结晶细致,但沉积速度比较慢;镍盐浓度高,镀液可以使用较高的电流密度,沉积速度快,容易沉积出色泽均匀的无光亮镀层,适于快速镀镍及镀厚镍。但镍盐浓度过高将降低阳极极化,并使镀液的分散能力下降。
b.阳极活化剂 氯化镍或氯化钠中的Cl-是镀液中的阳极活化剂。电镀镍所使用的镍阳极在电镀过程中容易钝化而阻碍其继续溶解,镀液中的Cl-通过在镍阳极上的特征吸附,去除氧、羟基离子和其他钝化镍阳极表面的异种粒子,从而保证镍阳极的正常溶解。但钠离子对镀液是无益的,可能引起阳极腐蚀、导致镀层粗糙等。所以宜用氯化镍,不过氯化镍的成本较高。
c.缓冲剂 普通镀镍镀液的pH值一般控制在3.8~5.0,可用稀硫酸或稀盐酸调节,并以硼酸做缓冲剂。硼酸也有助于使镀层结晶细致,提高电流效率。但含量过高时,硼酸可能结晶析出,造成镀层毛刺,一般控制在30~45g/L。
d.防针孔剂 十二烷基硫酸钠是暗镍镀液中常用的防针孔剂,它是一种阴离子表面活性剂,通过在阴极表面吸附,降低电极与镀液间的界面张力,使形成的氢气气泡难以在电极表面滞留,从而减少了镀层中的针孔。其用量为0.1g/L左右,浓度过低不能有效地清除针孔,浓度过高去针孔效果并不会增加,还会使泡沫过多,不易清洗。
e.导电盐 硫酸镁是暗镍镀液中常用的导电盐,它的加入可提高镀液的电导率,改善镀液的分散能力,并有利于降低槽电压。
②电极反应
a.阴极反应 镀镍液中的阳离子有Ni2+、H+、Mg2+、Na+等。由于Mg2+与Na+的电极电位远低于Ni2+和H+,因而镀镍过程的阴极反应为Ni2+的还原和析氢副反应。
b.阳极反应 镀镍过程中的阳极反应为镍阳极的溶解。若阳极发生钝化,则在阳极极化较大时,会有氧气析出的副反应发生。若镀液中有Cl-存在,则在阳极极化较大时,阳极会有氯气析出,反应式为
2Cl- Cl2+2e- (2-19)
由于镍的交换电流密度很小,镍离子放电时极化较大,因而暗镍镀镍液即使不含添加剂也可以得到结晶紧密细致的镍镀层。
(2)光亮镀镍
对于装饰防护性镀层,常常要求镀层具有镜面光泽的外观。最初人们是通过对暗镍镀层进行机械抛光来获得具有镜面光泽度的镀镍层。电镀光亮镍工艺的出现,使得人们仅仅通过在普通镀液中加入光亮剂即可获得具有镜面光泽的镍镀层。镀光亮镍可以省去繁杂的抛光工序,从而改善工作环境,还能提高镀层的硬度,有利于自动化生产。但光亮镀层中含硫,内应力和脆性较大,耐蚀性不如普通镀镍层。
①光亮镀镍液的成分及作用 在瓦特镀液中加入光亮剂就成为光亮镀镍液。常用的镀液配方及工艺规范见表2-6。镀液中除光亮剂外,其他成分的作用在前面的普通镀镍中都有过介绍,下面仅介绍光亮剂的作用。
表2-6 电镀光亮镍镀液组成及工艺规范

镀镍光亮剂多为有机化合物,根据作用效果及作用机理的不同可分为三类:初级光亮剂、次级光亮剂、辅助光亮剂。一般认为,镀液中加入光亮剂后使得镀层变得平整均匀,晶粒细化,从而获得镜面光泽。
a.初级光亮剂 初级光亮剂是含有C-SO2结构的有机含硫化合物。常用的有糖精、对甲苯磺酰胺、苯亚磺酸钠、萘磺酸钠等。初级光亮剂通过不饱和碳键吸附在阴极的生长点上,增大阴极极化,从而显著减小层的晶粒尺寸,使镀层产生柔和的光泽,但不能获得镜面光泽。初级光亮剂加入还将使镀层产生压应力。初级光亮剂在阴极还原后,将以硫化物的形式进入镀层,使镀层的硫含量增加。
初级光亮剂加入量一般为0.3~3g/L,使用上浓度限制不严格。但浓度越高,镀层中的硫含量也将越高。
b.次级光亮剂 次级光亮剂是含有CO、C
C、C
N、
、
、N—C
S等不饱和基团的有机物。普遍使用的是丁炔二醇及其衍生物,其次是香豆素等。
次级光亮剂能显著改善镀液的整平性能,与初级光亮剂配合使用可获得具有镜面光泽的镀层,且镀层延展性良好。单独使用次级光亮剂,虽然能获得光亮镀层,但镀层张应力大,脆性大,故一般不单独使用。次级光亮剂的加入量因种类不同而有较大的差异,其范围可达0.05~5g/L。
c.辅助光亮剂 常用的辅助光亮剂有烯丙基磺酸钠、烯丙基磺酰胺、乙烯磺酸钠、丙炔磺酸钠等,其结构特点是既含有初级光亮剂的C—S基团,又含有次级光亮剂的CC基团。辅助光亮剂单独使用时并不能使镀层获得很好的光亮性,但若与初级光亮剂和次级光亮剂配合使用,则可以起到下列一种或多种作用:加快出光和整平速度;减少其他光亮剂的消耗; 减少针孔。
②电极反应 光亮镀镍的电极反应与普通镀镍的电极反应相同,可参看前面的内容。
半光亮镀镍是在瓦特镀液中加入不含硫的有机物即次级光亮剂。加入量在0.05%~0.8%之间。半光亮镀镍液的成分及工艺条件可参阅相关的参考书。一般来说,半光亮镀镍很少单独使用,通常与光亮镀镍组合成双层镍或三层镍,有效地起到防护作用。
(3)镀多层镍
光亮性镀镍层,它们在防护钢铁零件上属于阴极性镀层,要达到防护—装饰作用,提高镍镀层的防护能力,常采用多层镀镍的方法来解决。镀多层镍是在同一基体上选用不同的镀液及工艺条件所获得的双层或三层镀镍层。
电镀双层镍的结构为:钢铁/半光亮镍/光亮镍/铬,电镀三层镍的结构为:钢铁/半光亮镍/高硫镍/光亮镍/铬。在镍层上镀覆的一层铬,既能提高耐磨性又能改善防护性能。
①电镀双层镍 常用电镀双层镍的镀液配方及工艺规范见表2-7。
表2-7 电镀双层镍镀液组成及工艺规范

双层镍是先沉积一层含硫少或无硫的半光亮镍或普通的暗镍。然后再镀一层含硫较高(硫含量约为0.5%)的全光亮镍层。由于外层和底层的含硫量不同,它们在腐蚀介质中的腐蚀电位也不同。镀镍层的硫含量越高,腐蚀电位越低。当控制半光亮镍层与光亮镍层间的腐蚀电位差在120mV以上时,腐蚀一旦发生,半光亮镍层与光亮镍层构成的腐蚀原电池中,表层光亮镍层将成为阳极而优先腐蚀,以保证电镀双层镍有优良的耐蚀性。
双层镍的总厚度一般为20~40μm,半光亮镍的厚度应补少于镀层总厚度的60%,一般半光亮层与光亮层的厚度比为3∶1。由于镀镍层表面在空气中和在水洗时容易钝化导致电镀双层镍层间的结合力下降,在两次电镀之间应尽量减少镀件在空气中的停留时间,并简化中间水洗过程。
②电镀三层镍 电镀三层镍是在电镀双层镍之间再镀一薄层含硫量更高的高硫镍层(含硫量约为0.1%~0.2%),其腐蚀电位在三层中最低。通过控制三层镍中各层的含硫量使高硫镍层与半光亮镍层之间的腐蚀电位差达到240mV,高硫镍层与光亮镍层间的腐蚀电位差达到80~100mV时,腐蚀一旦发生,高硫镍层将取代光亮镍层成为腐蚀原电池的阳极而优先腐蚀,使腐蚀在高硫镍层中横向发展,从而保证了电镀三层镍即使在厚度很薄时仍具有很好的耐蚀性。常用电镀高硫镍层的工艺规范见表2-8。
表2-8 电镀高硫镍镀液组成及工艺规范

电镀三层镍中,一般半光亮镍层厚度不应小于总厚度的50%,高硫镍层的厚度应不超过总厚度的10%,光亮层的厚度应不少于总厚度的20%。
(4)电镀黑镍
黑镍镀层主要用于光学工业、武器制造业和各种铭牌,也可以利用其对太阳能的高吸收率来制备太阳能集热板。镀层往往很薄(约2μm),耐蚀性能较差,镀后需要涂透明保护漆。
镀黑镍的镀液有两大类。第一类镀液中含有硫酸锌和硫酸氰盐,电镀液组成及工艺规范见表2-9。由这类镀液得到的黑镍镀层是一种含有镍(40%~60%)、锌(20%~30%)、硫(10%~15%)及少量氮、碳、有机物(约10%)的合金镀层。第二类镀液中含有钼酸盐,电镀组成及工艺规范见表2-10。
表2-9 第一类电镀黑镍镀液组成及工艺规范

表2-10 第二类电镀黑镍镀液组成及工艺规范

电镀黑镍时需要严格控制镀液的pH值,镀件需带电入槽,要经常用盐酸退去挂具上的黑镍镀层,以保证导电良好,同时要注意镀液中的锌盐浓度及电流密度大小,只有这样才能得到满意的黑镍镀层。
一般黑镍镀层的耐蚀性及耐磨性均较差,与基体的结合力也不好。为此,在镀黑镍前需要在钢铁件或铜及铜合金件上预镀暗镍、锌、铜等底层之后再镀黑镍。
(5)镍封闭
镍封闭是一种复合镀镍工艺,是制取高抗蚀性微孔铬的一种方法。在光亮镀镍后,再将零件放入悬浮有直径为0.02μm左右的不溶性非导电微粒的光亮镀镍液中,微粒与镍同时沉积,称为镍封闭镀层。然后镀上装饰性铬层,在非导体微粒处形成微孔,即得到微孔镀层,是腐蚀电池比较均匀地分散于整个镀层上,从而防止产生大而深的直贯整个金属基体的少量腐蚀沟纹和凹坑,向横向发展。也就减缓了穿透基体的腐蚀速度,进一步提高了防护性能。
镍封闭镀液的成分及工艺规范见表2-11。
表2-11 镍封闭镀液组成及工艺规范

固体微粒的直径在0.01~0.5μm为宜,不能大于2μm,否则镀层粗糙,影响光亮性和整平性。微粒的含量以15~25g/L为宜,不应过高,否则镀件难以清洗;太小时抗蚀性能又降低。一般微孔数在10000~30000/cm2时耐蚀性最好。
因为镀液中存在一定数量的不溶物,必须在强烈的搅拌下才能使镀液中的微粒均匀地分散在镀液中,镀件在入槽前就必须搅拌,多采用压缩空气进行搅拌,整个系统中要有空气净化装置,必须严防机油带入镀液,在空气搅拌的同时也可用阴极移动配合电镀过程。
(6)镀缎面镍
如在光亮镀镍液或半光亮镀镍液中加入较镍封闭工艺中更大的非导体微粒,可得到缎面镍。近年也有新的缎面镍工艺是不加非导体固体微粒,而只是加低浊点表面活性剂,也可以获得缎面镍,这种方法也称乳化法。比如在瓦特镀液中加入光亮剂(Velous D100,2~4mL/L)和乳化剂(Velous M30,8~50mL/L),就成为缎面镀镍液。但这种镀层厚度要大于6μm才有明显的缎面效果。
(7)镀高应力镍
在光亮镍层上再镀一层厚度约0.5~3μm的高应力镍层,然后在标准镀铬液中镀一层0.2~0.3μm的铬层。由于高应力作用使捏成和铬层都产生均匀的微裂纹,所以也称之为微裂纹镀铬,国外也称之为冲击镍(PNS)。电镀高应力镍镀层镀液的组成及工艺规范见表2-12。
表2-12 电镀高应力镍镀液组成及工艺规范

注:MCN-1、MCN-2为上海日用五金研究所研制,GYN-1、GYN-2为上海轻工研究所研制,PN-1、PN-2为武汉材料保护研究所研制。
2.2.3 镀铬
铬是一种微带天蓝色的银白色金属。虽然金属铬的电位很负(标准电极电位为-0.74V),但是由于其具有强烈的钝化能力,其表面上很容易生成一层极薄的钝化膜,使其电极电位变得比铁正得多。因此,在一般腐蚀性介质中,钢铁基体上的镀铬层属于阴极镀层,对钢铁基体无电化学保护作用。只有当镀铬层致密无孔时,才能起到机械保护作用。
金属铬的强烈钝化能力,使其具有较高的化学稳定性。在潮湿的大气中镀铬层不起变化,与硫酸、硝酸及许多有机酸、硫化氢及碱等均不发生作用。但易溶于氢卤酸及热的硫酸中。
金属铬的硬度很高,一般镀铬层的硬度也相当高,而且通过调整镀液的组成和控制一定的工艺条件,还可以得到硬度更高的镀铬层,使其硬度值超过最硬的淬火钢,因此耐磨性好。
(1)电镀铬的发展及特点
镀铬在电镀工业中占有极其重要的地位,并被列为3大镀种之一。有关镀铬的历史可以追溯到19世纪中叶,1854年法国的Robet Baoson教授首次从煮沸的氯化亚铬溶液中实现了铬电沉积,1856年德国的Gerther博士发表了第一篇关于从铬酸盐溶液中电镀铬的研究报告,从而掀起了六价铬电镀的研究高潮。而电镀铬的工业化要归功于Fink和Scdwartz等在1923—1924年间的工作。至今电镀铬工业已经有了近百年的历史,并成为电镀工业必不可少的镀种之一。现在普遍使用的是Sargent于1920年发明的六价铬镀铬工艺。电镀铬除了具有与其他单金属镀层共同之处外,还有自身所独有的特点,是一个比较特殊的镀种,其特点如下。
①阴极电流效率很低,工业化生产中仅为12%~15%,生产时由于放出大量氢气和氧气,加上温度高,产生了毒性很大的铬雾。
②镀液的分散能力及覆盖能力差,如欲获得均匀的镀层,必须采取人工措施,如设计象形阳极或保护阴极。
③镀铬生产对温度控制要求很高,如欲获得光亮镀层,不但要严格控制温度变化,电流密度也必须根据所用温度选定。
④电镀铬的阳极不用金属铬,而是选择不溶性铅或铅合金阳极。
⑤六价铬是公认的致癌物质,对人体健康危害极大。
正是基于以上原因,人们不断地探索改进传统的电镀铬工艺,并且尝试使用PCVD、化学镀镍等方法来取代镀铬工艺。20世纪70年代来,人们在六价铬镀铬工艺的基础上先后开发了自调节镀铬、超高浓度镀铬、稀土低浓度镀铬、松孔镀铬、微裂纹镀铬、无裂纹镀铬、镀黑铬等各种工艺,但这些工艺与Sargent工艺相比较,虽然有进步但并无根本突破。
三价铬电镀工艺自1975开始推广应用,其明显的优势表现为低的环境污染问题及较好的分散和覆盖能力,由此引发了一场研究三价铬电镀工艺的热潮。但三价铬电镀工艺至今仍存在一些不足,表现为镀液的稳定性不好、成分复杂、分析监控比较难、镀层的质量及外观比较差,特别是三价铬电镀层厚度一般仅为3~4μm,只能用于装饰性镀铬。
其他有望取代电镀铬的工艺如PCVD等成本很高,不能为一般厂家接受,短期内全面取代电镀铬不大可能。因此,从根本上取代六价铬电镀铬体系的时机还不成熟。目前应着眼于对现行工艺进一步完善,特别是引入新型添加剂,以使镀液性能及镀层质量得到提高。
(2)镀普通铬
①电镀液组成及作用 普通镀铬溶液成分简单,易于管理。通常将电镀铬溶液分为高浓度、中浓度和低浓度镀液。其中含铬酐250g/L的镀液习惯上称为标准镀铬液,应用较广。高浓度镀液导电性和深镀、均镀能力好,电流效率较低,主要应用于复杂零件镀铬。低浓度镀液电流效率较高,镀层硬度较大,但覆盖能力较差,用于简单零件镀铬。普通镀铬液以硫酸根作催化剂。如果以硫酸根和氟离子或氟硅酸根离子作催化剂就是所谓复合镀铬。如用硫酸锶和氟硅酸钾作催化剂就成为自动调节镀铬溶液。这两种镀液虽然有沉积速度较快、均镀、深镀能力较好等优点,但腐蚀性强,耗能多,对杂质敏感,应用较少。如在普通镀液中加入硼酸和氯化镁,电流密度可提高,沉积速度快,其镀层与金属基体的结合力好,该镀液被称为快速镀铬液。
表2-13、表2-14分别为普通镀铬和其他几种镀铬工艺的镀液组成及工艺规范。
表2-13 普通镀铬镀液组成及工艺规范

a.铬酐 铬酐是镀铬电解液中的主要成分,是铬镀层的来源。在镀铬工艺中,其浓度可在很大的范围内变化。在一定的工艺条件下均可获得光亮的镀层。但铬酐浓度的高低,对镀液性能和镀层的性质有很大的影响。在一定的条件下,随铬酐浓度的逐渐增高,溶液的电导率逐渐增加,当铬酐的浓度达到某一数值时,溶液的电导率最大。继续提高铬酐浓度,溶液的电导率反而下降。
电流效率随铬酐浓度的降低有所提高。电解液的分散能力随铬酐浓度的增加而降低。与高浓度镀铬溶液相比,稀的镀液中,获得光亮镀层的工作范围较大。铬酐浓度对镀层硬度也有一定的影响,随着铬酐浓度的增加,铬层硬度有一定的减少,浓度低的镀液能获得较高硬度的镀层,并增加了镀层的耐磨性。但较低浓度导致镀液成分不稳定,需要定期分析调整。
表2-14 几种镀铬液组成及工艺规范

b.催化剂 硫酸、氟化物、氟硅酸盐、氟硼酸盐等,常常作镀铬的催化剂,没有催化剂无法实现铬的沉积,其含量的高低与铬酐的比值的关系很大。
镀液中铬酐与硫酸的比值对电流效率、分散能力和覆盖能力等都有重要的影响。标准镀铬液中CrO3/S最佳值为100∶(0.8~1.2)。比值过高,镀层光泽度降低,沉积速度降低,外观偏白,镀液覆盖能力变差,还可能出现条纹。如比值过低,电流效率降低,覆盖能力下降,外观偏黑,高电流密度处还有可能烧焦。
镀铬溶液中加入一定量达到含氟阴离子(F-、Si、B
)作催化剂,其加入量为铬酐含量的1.5%~4%。
含有Si的镀液覆盖能力和电流效率较普通镀铬溶液好。普通电解液电流效率最高值为18%,而用Si
作催化剂的电解液的电流效率最高可达25%。
②电极反应
a.阴极反应 镀铬电解液的组成很简单,但铬的沉积机理却很复杂。采用示踪原子法对铬酸镀铬过程的研究表明,镀铬层是由六价铬还原得到的,而不是三价铬。
铬酐在镀液中主要以Cr2的形式存在。Cr2
与Cr
之间存在如下平衡
Cr2+H2O
2Cr
+2H+ (2-20)
镀铬电解液是强酸性电解液(pH<1),六价铬在溶液中主要是以重铬酸根(Cr2)形式存在,也含有一定量的铬酸跟(Cr
)。由此可见,镀铬电解液中存在的离子除了上述两种外,还有硫酸根离子和氢离子。除硫酸根离子外,其他离子都参与阴极反应过程。
阴极上的主反应是
Cr+8H++6e-
Cr+4H2O (2-21)
同时阴极上还进行如下的副反应
Cr2+8H++6e-
Cr2O3+H2O (2-22)
2H++2e- H2↑ (2-23)
当镀液中没有硫酸时,在阴极上只能析出氢气,不发生铬的还原。这是因为,在铬酸电解液中镀铬时,首先在阴极表面上生成的是碱式铬酸铬的胶体膜[Cr(OH)2Cr(OH)CrO4],将阴极紧紧包住,只有离子半径最小的氢离子才能穿透膜层进行还原反应。硫酸根离子的存在能使碱式铬酸铬胶体膜发生局部溶解,暴露出电极表面,使得真实电流密度很高,极化作用很大,才能使六价铬直接在阴极表面上还原成金属铬。在新生成的铬层表面又会生成新的胶体膜,膜的生成与溶解交替进行。只有这样,铬层的沉积才能不断进行。因此,胶体膜的存在是Cr6+还原为Cr0的必要条件。
b.阳极反应 镀铬所使用的是铅及铅合金等不溶性阳极,这是镀铬不同于一般镀种的特点之一。不用金属铬作阳极的原因主要是金属铬镀层是由六价铬直接还原得到的,而金属铬阳极溶解时却主要是以三价铬离子的形式进入溶液,这将导致镀液中三价铬迅速增加,结果使电解液变得极不稳定而且无法控制。
在正常生产中,铅及铅合金阳极的表面上生成一层黄色的二氧化铅膜
Pb+2H2O PbO2+4H++4e- (2-24)
这层膜不影响导电,阳极反应仍然可正常进行,其电极反应如下
2Cr3++7H2O Cr2
+14H++6e- (2-25)
2H2O O2+4H++4e- (2-26)
由上述反应可以看出,在阴极上生成的Cr3+离子在阳极上又重新生成Cr2离子,从而使电解液中的Cr3+离子浓度保持在一定的水平,以保证电镀铬生产的正常进行。在生产中一般控制阳极面积∶阴极面积=(2∶1)~(3∶2)时,即可使Cr3+离子浓度保持在工艺允许的范围内。
(3)镀硬铬
镀硬铬与前面讲的普通装饰性镀铬在本质上并无区别,只不过镀层较厚,通常为0.1~0.2mm,甚至有时候可达0.5mm。硬铬镀层充分利用了铬层硬度大、耐磨性好、摩擦系数小的特征,在工业上应用相当广泛,尤其是重负荷、高摩擦的工况下。
镀硬铬可以用复合镀铬液,但通常情况下用中浓度普通镀铬液,如标准镀铬液。只是温度和电流密度应稍高:45~55℃和40~60A/dm2。操作上与普通镀铬的主要区别在于,镀硬铬后要进行热处理以消除氢减少内应力,一般是将镀件放在烘箱或油槽中150~250℃保温0.5~5h。
镀层的硬度一般随厚度的增加而提高,但当厚度增加到一定值后,硬度达到最大值。再继续增加厚度,硬度不再增加。镀铬液浓度越低,铬层硬度越大,但低浓度镀铬液稳定性差。
(4)镀黑铬
黑铬镀层具有特别优良的物理化学性能,不仅有瑰丽庄重的装饰外观,而且耐腐蚀、耐高温,甚至当温度升至500℃左右,黑铬镀层也能保持不变色、不发脆,其热稳定性良好。因此黑铬镀层比其他镀层如电镀黑镍、镀锌钝化、阳极化着黑色等更具特色,广泛用于作为降低反射系数的防护装饰镀层或作为有特殊要求的功能性镀层,在轻工、仪器仪表、航空航天等领域有十分广泛的应用和发展前景。
黑铬镀层的黑色是由于镀层的物理结构所致,它不是纯金属铬层,而是由铬和三氧化铬的水合物组成,呈树枝状结构,由于对光波的完全吸收而呈黑色。黑铬镀层的耐蚀性优于普通镀铬层,其硬度虽然低,但耐磨性与普通镀铬层相当。
电镀黑铬的工艺配方很多,较常用的见表2-15。
表2-15 黑铬镀液组成及工艺规范

与普通镀铬液相比,电镀黑铬液中不能含有硫酸根离子。当有硫酸根离子时,镀层呈淡黄色而不是黑色,可用碳酸钡或氢氧化钡使硫酸根离子生成沉淀而除去。镀液中的发黑剂为硝酸钠、醋酸。它们的含量过低时,镀层不黑,镀液电导率低,槽压高。浓度过高时,镀液的分散能力和深镀能力均恶化。通常,硝酸钠的浓度控制在7~12g/L之间,醋酸的浓度控制在6~7mL/L之间。
黑铬镀层可以直接在铁、铜、镍和不锈钢上进行施镀,也可以先镀铜、镍或铜锡合金作底层,再镀黑铬层,以提高抗腐蚀性和装饰性。
(5)镀微裂纹铬和微孔铬
从标准镀液中得到的普通防护装饰性镀铬层厚度约为0.25~0.5μm。但由于铬镀层在电沉积过程中产生较大的内应力,使镀层出现不均匀的粗裂纹。金属铬的钝化能力很强,钝化后的镀铬层,在腐蚀介质中的电极电位要比底层或基体金属的电位正,铬镀层是阴极,裂纹处的底层是阳极,因此遭受腐蚀的总是裂纹处的底层或基体金属。腐蚀速度取决于腐蚀电流的大小,对于具有不均匀粗裂纹的普通防护装饰性镀铬层,腐蚀电流就分布在少数的粗裂纹中。由于裂纹处暴露出的底层金属面积与铬镀层相比很小,因而腐蚀电流密度很大,腐蚀速度很快,而且腐蚀一直向纵深发展。20世纪60年代中期开发出了多层镍与微裂纹镀铬层和微孔镀铬层构成的组合镀层,它既能大大提高防护性能,同时又不降低其装饰性能。这主要是由于镀铬层具有众多的裂纹或孔,暴露出来的镍层面积增大但又很分散,遇到腐蚀介质时,腐蚀电流也被高度分散,使镍层表面上的腐蚀电流密度大大降低,腐蚀速度也大为减缓,从而提高了组合镀层的耐蚀性,还可以使镍层的厚度减少5μm。
①微裂纹镀铬层 微裂纹镀铬层是指表面具有数目众多、分布均匀的、很细微的裂纹的镀铬层。微裂纹的密度为300~400条/cm2。
镀微裂纹铬除前面的高应力镀镍法外,还有单层法和双层法。单层法在成本与管理方面优于双层法,所以单层法应用较多。其镀液组成及工艺规范见表2-16。
表2-16 微裂纹镀铬镀液组成及工艺规范

②镀微孔铬 微孔铬层可用镍封闭法制取,也可以用含非导电性固体微粒的镀铬液和用有机表面活性剂作为镀镍层中微粒添加剂的方法,但应用较多的是镍封闭法。
(6)镀松孔铬
在高负荷的摩擦条件下,通常要求材料具有很好的润滑性。松孔铬镀层的孔中可以储存润滑油,增强了润滑性能,减小了材料的摩擦磨损。松孔镀铬层可用喷砂法、盐酸腐蚀法获得,但主要应用的是电解法。在镀铬电解液或氢氧化钠溶液中放入镀硬铬的工件,进行阳极刻蚀,是镀层上微裂纹扩展、加深。适宜的镀铬条件是温度58℃左右,电流密度55A/dm2左右,铬酐浓度为250g/L,CrO3∶S=100∶1.05。阳极刻蚀条件可用:温度35~45℃,电流密度25~35A/dm2。但是,对不同的金属基材和不同厚度的镀铬层,工艺条件有所不同。
(7)三价铬镀铬
三价铬盐镀铬电解液为络合物电解液,一般多采用甲酸盐(甲酸钾或甲酸铵)或草酸铵做络合剂。主盐采用氯化铬或硫酸铬,加入一定量的导电盐(氯化钾或硫酸钠),用硼酸做缓蚀剂,在加入少量润湿剂。表2-17是三价铬镀铬的镀液组成及工艺规范。
三价铬电镀铬的阴极反应可以分为两步,第一步是铬的三价铬的络合离子得到一个电子称为二价铬络合离子
[Cr(H2O)5L]2++e- [Cr(H2O)5L]+ (2-27)
式中L-表示配位体。
第二步是将二价铬络合离子还原成金属铬
[Cr(H2O)5L]++2e- Cr+5H2O+L- (2-28)
三价铬电沉积过程的控制步骤是[Cr(H2O)5L]2+络离子向阴极表面传递的扩散步骤所控制。在阴极还有氢气的析出的副反应,反应式见前面的相关叙述。
三价铬镀铬的阳极反应为氧气的析出,除此之外,还有可能发生氯的析出和三价铬氧化为六价铬的副反应。
表2-17 三价铬镀铬镀液组成及工艺规范

三价铬盐镀铬电解液的最大特点是可在室温下操作,不需要加温设备。阴极电流也较低,一般控制在10A/dm2左右。由于是络合物电解液,三价铬镀铬电解液的阴极极化较大,因此镀层的结晶细致。而且,镀液分散能力和深镀能力都比铬酸镀铬电解液好。但存在镀液稳定性差、镀层色泽不理想以及不能镀厚镀层等缺点。
2.2.4 镀铜
铜是粉红色富有延展性的金属。质软而韧,易于抛光。铜具有良好的导电性和导热性。铜的化学稳定性较差,易溶于硝酸,也易溶于加热的浓硫酸中,但在盐酸和稀硫酸中溶解很慢。铜在空气中易氧化,尤其是在加热的情况下,会失掉本身的颜色和光泽。在潮湿空气中与二氧化碳或氯化物作用后,表面生成一层碱式碳酸铜或氯化铜薄膜,当受到硫酸作用时,将生成深褐色的硫化铜。铜的标准电位为+0.339V,比铁正,钢铁零件上的镀铜层是阴极镀层。当镀铜层有空隙或受到损伤时,在腐蚀介质作用下,裸露出来的钢铁表面称为阳极,受到腐蚀,故一般不单独使用镀铜层作为防护性的装饰性镀层。
镀铜层常用于钢铁零件底镀层和其他镀层的中间层,以提高基体金属盒表面镀层之间的结合力,同时也有助于表面镀层入槽初镀时的顺利沉积。如在钢铁零件上镀镍、铬时,先以铜为中间层,这样不但可以减少镀层空隙,而且可以节约镍的消耗量,即常用厚铜薄镍镀层。镀铜层也用于钢铁件的防止渗碳和塑料电镀等方面。
可以用来电镀铜的电解液的种类很多,按电解液组成可分为氰化物电解液和非氰化物电解液两大类。非氰化物电解液又有硫酸盐镀液、焦磷酸盐镀液、氟硼酸盐镀液等。
(1)氰化物镀铜
氰化物镀铜自1915年开始获得工业上的应用,到20世纪30年代在工业部门得到广泛采用。该电解液的特点是导电性好,分散能力和深镀性能好,镀层结晶细致,且镀层与基体的结合力好,操作简单。但电解液的毒性大,生产过程中产生的废水、废气和废渣对环境污染严重,三废治理费用大。
①氰化物镀铜电镀液也的组成及作用 氰化物镀铜电解液的组成及工艺规范见表2-18。
表2-18 氰化物镀铜镀液组成及工艺规范

a.氰化亚铜 电解液中提供铜离子的主盐。氰化亚铜必须在氰化钠溶液中溶解,形成铜氰络离子。在实际生产中通常是控制金属铜的含量,在预镀溶液中铜与游离氰化物的比值为1∶(0.5~0.7)。在含有酒石酸盐的镀液中,铜含量与游离氰化物的比值为1∶(0.3~0.4)。铜含量低时,电流效率低,允许的电流密度也低。
b.氰化钠 电镀液中的络合剂,它与铜离子形成络阴离子。不同浓度的氰化钠,可以形成不同配位数的络离子。一般认为在氰化镀铜电解液中络离子存在的主要形式为[Cu(CN)3]2-。为了生成[Cu(CN)3]2-络离子,所需要的氰化钠的量是氯化亚铜量的1.1倍,除此之外多余部分的氰化钠称之为游离氰化钠。镀液中含有游离氰化钠能使铜氰络盐稳定,增加阴极极化,防止阳极钝化。游离氰化钠含量高时,阴极电流效率低,阴极上有大量的氢气析出,阳极发亮。当游离氰化钠含量太少时,镀层发暗而成海绵状,阳极不能正常溶解,阳极表面形成淡青色的薄膜促成阳极钝化。同时溶液浑浊,严重时溶液呈浅蓝色。为了使镀铜过程正常工作,应控制铜和氯化钠的比例。
c.氢氧化钠 强电解质,在氰化镀铜溶液中它的主要作用是改善电解液的电导,从而提高镀液的分散能力;它还能与二氧化碳作用生成碳酸钠,较少氰化钠的消耗,起到稳定电解液的作用。
d.碳酸钠 碳酸钠可以提高电解液的电导,并能抑制氰化钠和氢氧化钠吸收二氧化碳的反应,对电解液有稳定作用。其来源主要为氢氧化钠与二氧化碳的反应,有时也在配置镀液时有意加入。碳酸钠的含量在75g/L以下时,对电镀过程没有明显的不良影响,超过这个范围就会造成电流效率下降,镀层疏松,光亮范围减少,产生毛刺以及阳极钝化等故障。
e.酒石酸钾钠 酒石酸钾钠是阳极去极化剂,在氰化镀铜电解液中加入一定量的酒石酸钾钠有利于阳极溶解,并可适当降低氰化钠的含量。另外,还可以使镀层结晶细致,平滑。
f.硫氰酸钾 也是阳极去极化剂,可以保证阳极正常溶解,还可以除去锌等有害杂质。
g.光亮剂 起改善镀层结晶结构,提高镀层的光亮度的作用。硫酸锰与酒石酸盐和硫氢酸钾共同使用,再配合周期换向电流(这点是必需的),可获得高光亮的镀层。醋酸铅也可作为镀铜溶液的光亮剂,用量为0.015~0.03g/L。
②电极反应
a.阴极反应 氰化物镀铜电解液为络合物电解液,铜络离子存在的主要形式是[Cu(CN)3]2-。因此阴极上的主反应为[Cu(CN)3]2-离子还原为金属铜,反应方程式为
[Cu(CN)3]2-+e- Cu+3CN- (2-29)
与此同时,阴极上还有析氢的副反应发生,反应方程式与前面其他镀种种阴极析氢副反应相同。
b.阳极反应 氰化物镀铜工艺中采用的阳极为可溶性阳极。阳极的主要反应为金属铜氧化为铜离子,反应方程式为Cu+离子与CN-离子反应生成[Cu(CN)3]2-络离子。
Cu Cu++e- (2-30)
在氰化物镀铜电解液中,阳极电流一般不超过2.5A/dm2,超过此范围阳极容易发生钝化,此时阳极上将有氧气析出,反应方程式与前面讲的析氧反应相同。氧气的析出不仅使阳极电流效率下降,同时还加速了NaCN的分解,造成其大量消耗。
③工艺条件的影响
a.阴极电流密度 在预镀铜溶液中,电流密度高时,阴极极化作用加剧,电流效率下降,析氢严重,使镀层疏松、分布不均。电流密度过低,沉积缓慢,镀层发暗不亮。为了在较高的电流密度下仍保持高的电流效率,以获得高的沉积速率,可以提高铜的浓度,降低游离氰化物的浓度,同时加入阳极去极化剂。
b.温度 提高温度能降低阴极极化作用,可提高电流密度和电流效率,但对氰化物的稳定性有不利的影响。在生产中为了得到高的沉积速率,经常采用加热措施,有时甚至高达60~80℃。
(2)硫酸盐镀铜
硫酸盐镀铜电解液分普通镀液和光亮镀液两种。普通镀液早在1843年久已经在商业上应用,光亮镀液是20世纪70年代中期在普通镀液基础上发展起来的,在添加某些光亮剂后可直接获得光亮的铜镀层,从而省去了抛光工艺。
①镀液组成及作用 硫酸盐镀铜电解液成分简单,主要是由硫酸铜和硫酸组成,稳定性好,便于管理,成本低。镀液为强酸性,腐蚀性大。在钢铁和锌合金基体上施镀时要预镀。镀液组成及工艺规范见表2-19。在加入光亮剂后就成为光亮镀铜溶液,常用的光亮剂多为组合光亮剂。按照光亮剂的作用,可分为主光亮剂、整平剂和光亮剂载体。
表2-19 硫酸盐镀铜镀液组成及工艺规范

a.硫酸铜 硫酸铜是提供Cu2+离子的主盐,其含量在150~220g/L。含量过低,允许使用的电流密度下降,阴极电流效率和镀层光亮度均受影响。含量过高,硫酸铜容易结晶析出,镀液的分散能力不好。
b.硫酸 提高镀液的电导率,改善镀液的分散能力,保证阳极的正常溶解,还能防止铜盐水解生成氧化亚铜而沉淀析出,增加镀液的稳定性。含量通常在50~70g/L,含量过低,镀液的分散能力下降,镀层粗糙,阳极易钝化;含量过高,镀层的光泽度及整平性下降,还会造成一些光亮剂的分解。
c.氯离子 在硫酸盐光亮镀液中必须含有一定量的氯离子,它可以提高镀层的光亮度及整平性,并且可以降低由于加入添加剂后产生的内应力。
d.光亮剂 硫酸盐光亮镀铜目前所采用的光亮剂多为组合光亮剂,包括:主光亮剂,主要为聚硫有机磺酸,主要作用为提高阴极电流密度和使镀层晶粒细化;整平剂,常用的有2-四氢基噻唑硫酮等,这类化合物在一定电流密度范围内能吸附在阴极表面上,增大阴极极化,主要作用是改善镀液的整平性能,并能改善地电流密度区的光亮度;光亮剂载体,常用的有聚乙二醇(M=6000)、OP-乳化剂等,这类化合物属于表面活性剂,能够吸附在电极表面,降低界面张力,增强溶液对电极的润湿作用,减少针孔,还能增大阴极极化,使镀层均匀细致。
②电极反应 硫酸盐镀铜的电极反应比较简单,阴极的主反应为Cu2+离子还原成金属铜,当电流密度小时,有可能发生Cu2+的不完全还原,生成Cu+,当电流密度较大时,发生的副反应为析氢反应。
阳极反应为金属铜氧化为Cu2+,副反应为析氧反应。当电流密度小时,还有可能发生金属铜的不完全氧化,生成Cu+离子。
(3)焦磷酸盐镀铜
焦磷酸盐镀铜在我国生产上是应用的比较广泛的工艺之一,属于络合物型电解液。它的主要特点是电解液比较稳定,分散能力和覆盖能力比较好,镀层结晶细致,阴极电流效率高,可获得较厚的镀层,且在电镀过程中没有刺激性气体逸出。其不足之处是,在钢铁件上镀铜时,需要增加预镀或预处理措施,以保证镀层与基体的结合力,另外镀液的配置成本较高。
①镀液的组成及作用 电解液的组成及工艺规范见表2-20。
表2-20 焦磷酸盐镀铜镀液组成及工艺规范

a.焦磷酸铜 焦磷酸铜是主盐,为镀液提供铜离子。镀液中的铜含量一般控制在22~27g/L,对于光亮镀铜溶液铜含量控制在27~35g/L。铜含量过低,允许使用的工作电流密度范围窄,镀层的光亮度和整平性差;铜含量过高,阴极极化作用下降,镀层粗糙。
b.焦磷酸钾 为电解液中的主要络合剂。由于其溶解度大,能够相应地提高镀液中的铜含量,从而提高允许的工作电流密度和电流效率。且钾离子的电迁移数比较大,可以提高镀液的电导,改善镀液的分散能力。镀液中保留一些游离焦磷酸钾可以使镀液中的络合物更加稳定,防止焦磷酸铜沉淀,改善镀层质量,提高镀液的分散能力,保证阳极的正常溶解。
c.柠檬酸钠 为镀液中铜离子的辅助络合剂,对改善镀液的分散能力,提高允许使用的工作电流和镀层的光亮度,增强镀液的缓冲作用,促进阳极的溶解都有一定的作用。
d.光亮剂 在焦磷酸盐镀铜溶液中加入含巯基的化合物,可使镀层光亮,还有一定的整平作用。使用效果较好的是2-巯基苯并咪唑。生产中还常常加入SeO2或者亚硒酸盐,作为辅助光亮剂与2-巯基苯并咪唑配合使用,不仅可以增加光亮效果,还可以降低镀层的内应力。
②电极反应 焦磷酸盐镀铜电解液属于络合物电解液,镀液的pH值控制在8~9之间。在这样的条件下,铜络离子的主要存在形式为[Cu(P2O7)2]6-,因此,阴极的主反应是[Cu(P2O7)2]6-还原为金属铜,反应方程式为同时阴极上还会发生析氢的副反应。
[Cu(P2O7)2]6-+2e- Cu+2P2
(2-31)
焦磷酸盐镀铜采用的是可溶性阳极,阳极的主反应为金属铜氧化成二价铜离子。当阳极电流密度过大,还将发生析氧反应。
2.2.5 镀银
银是一种银白色金属,可塑、可锻。在所有的金属中银的电阻率最小,导电性最好,导热性也最好,易焊接,并且易抛光,有极强的反光能力,还具有优美的银色。
金属银具有较高的稳定性,能耐碱和一些有机酸的腐蚀,在洁净的空气中与氧不发生作用,但在有硫化物存在时,极易失去光泽并变色,使得接触电阻增大,焊接性能下降。因此对镀银层必须进行防变色处理。目前镀银层的防变色问题仍然是镀银生产中的重要课题之一。
银的标准电极电位为+0.799V,属于正电性较强的金属,对于大多数基体金属来说,银镀层是阴极性镀层。由于银的价格昂贵,一般不用做一般防护性镀层,但在化学工业中用作某些特殊腐蚀介质中的防护镀层。
银镀层的主要的通途是在电子工业、仪器仪表工业,以降低金属表面的接触电阻,提高焊接性能,另外,还用作餐具及各种工艺品的装饰。
(1)零件镀银前处理
镀银件的基体一般为铜及铜合金,也有一些钢铁件。它们的标准电极电位都比银负的多,当它们与镀银液接触的时候,将发生置换反应,在零件表面生成一层疏松、结合力差的置换银层。同时,置换过程中产生的铜和铁离子还会污染镀液。因此,镀件在进入镀槽之前,除进行常规的镀前处理外,还必须进行特殊的前处理。目前生产上对铜及铜合金常用的方法主要有汞齐化、浸银和预镀银。对于钢铁件或其他金属件则先镀一层铜,然后按照铜件进行处理。
①汞齐化 将铜或铜合金零件在含有汞盐的溶液中浸3~10s,使零件表面很快生成一层铜汞合金的工艺叫汞齐化。这层铜汞合金薄而均匀,具有银白色光泽,与基体结合良好,而且电极电位比银正。但由于汞有毒,对环境的污染严重,近年来已逐渐被浸银和预镀银取代。
②浸银 浸银溶液一般由银盐、络合剂或添加剂组成。络合剂的含量很高,而银离子的含量则较低,这样可以增大阴离子还原为银的阻力,减缓置换反应的速度,使零件表面产生的银层比较致密,并且有良好的结合力。
③预镀银 预镀银是在专用的镀银溶液中,在零件表面镀上一层很薄而结合力很好的银层,然后再电镀银。预镀银电解液采用高浓度络合剂和低浓度银盐组成。预镀银法质量稳定,但设备较复杂,需增加直流电源。
(2)氰化物镀银
氰化物镀银是最早的一个电镀工艺,1840年英国人Elkington获得了氰化物电解液镀银专利,标志着电镀工业的开始,到现在已经160多年的历史。银是正电性较强的金属,并且银离子在还原时的交换电流密度较大,也就是阴极电化学极化小,所以从简单盐电解液中沉积的银镀层结晶粗大。为了获得结晶细致、紧密的银镀层,必须采用络合物电解液。而氰化物是镀银电解液中最好的络合剂。虽然人们在无氰镀银方面做了大量的工作,但一直没有取得重大的突破。
① 氰化物镀银镀液的组成及作用 氰化物镀银电解液主要由银氰络盐和一定量的游离氰化物组成。该镀液的分散能力和深镀能力都很好,镀层呈银白色,结晶细致。加入适量的添加剂,可得到光亮镀层或硬银镀层。缺点是氰化物剧毒。
氰化物镀银镀液的配方很多,常见的见表2-21。
表2-21 氰化物镀银镀液组成及工艺规范

a.银盐 银盐是镀银电解液中的主盐,可以是氯化银、氰化银或是硝酸银。提高镀液中银盐的含量,可以提高阴极电流密度,从而提高沉积速度。降低银盐浓度,同时又保持相对较高含量的游离氰化钾时,则可以改善镀液的分散能力。
b.氰化钾 氰化钾是镀液中的络合剂。用氰化钾而不是氰化钠作络合剂主要是钾盐的导电性比钠盐要好,允许使用较高的电流密度,阴极极化作用稍高,镀层均匀细致。氰化钾的含量除了保证形成络离子外,还应有一定的游离量,以保证络离子的稳定。
c.碳酸钾 为强电解质,能够提高镀液的电导率,增加阴极极化,有助于提高镀液的分散能力。
d.酒石酸钾钠 可以防止银阳极钝化,促进阳极溶解并提高阳极电流密度,还能使镀层出现光泽。
e.酒石酸锑钾 可以提高镀层的硬度,还有氯化钴和氯化镍也可以起到提高银镀层硬度的作用。
f.光亮剂 常用的光亮剂为1,4丁炔二醇和2-巯基本并噻唑,它们能够吸附在阴极表面,增大阴极极化,使镀层结晶细致,并可使银镀层的结晶定向排列,呈现镜面光泽。
②电极反应
a.阴极反应 阴极的主反应为[Ag(CN)2]-还原为金属银,反应方程式为
[Ag(CN)2]-+e- Ag+2CN- (2-32)
此外,还有可能发生析氢副反应。
b.阳极反应 氰化镀银采用金属银作可溶性阳极,因此阳极的主反应为银的电化学溶解,形成Ag+离子。溶解下来的Ag+离子又与游离的CN-离子形成[Ag(CN)2]-络离子。
当发生阳极钝化时,还会有析氧反应发生。
(3)硫代硫酸盐镀银
氰化物是剧毒的化学品。采用氰化物的镀液进行生产,对操作者、操作环境和自然环境都存在极大的安全隐患。因此,开发无氰电镀新工艺一直是电镀技术工作者努力的目标之一,并且在许多镀种已经取得了较大的成功。比如无氰镀锌、无氰镀铜等,都已经在工业生产中广泛采用,但是无氰镀银则一直都是一个难题。无氰镀银工艺所存在的问题主要有以下三个方面。
①镀层性能 目前许多无氰镀银的镀层性能不能满足工艺要求,尤其是工程性镀银,比起装饰性镀银有更多的要求。比如镀层结晶不如氰化物细腻平滑;镀层纯度不够,镀层中有机物夹杂,导致硬度过高、电导率下降等;还有焊接性能下降等问题。这些对于电子电镀来说都是很敏感的。有些无氰镀银由于电流密度小,沉积速度慢,不能用于镀厚银,更不要说用于高速电镀。
②镀液稳定性 无氰镀银的镀液稳定性也是一个重要指标。许多无氰镀银镀液的稳定性都存在问题,无论是碱性镀液还是酸性镀液或是中性镀液,不同程度地存在镀液稳定性问题,这主要是替代氰化物的络合剂的络合能力不能与氰化物相比,使银离子在一定条件下会产生化学还原反应,积累到一定量就会出现沉淀,给管理和操作带来不便,同时令成本也有所增加。
③工艺性能 工艺性能不能满足电镀加工的需要。无氰镀银往往分散能力差,阴极电流密度低,阳极容易钝化,使得在应用中受到一定限制。
硫代硫酸盐镀银属于非氰化物镀银工艺的一种,在该电解液中采用硫代硫酸盐作络合剂,有钠盐、铵盐和钾盐,使用最多的是硫代硫酸钠。主盐可以选用氯化银、溴化银或硝酸银。
硫代硫酸盐镀银工艺的优点是镀液成分简单,配置方便,分散能力好,镀层色泽银白,结晶细致,钎焊性好。缺点是镀液稳定性差,阴极电流密度范围窄,镀层含有少量的硫,增加了银镀层的脆性。
硫代硫酸盐镀银典型镀液配方及工艺规范见表2-22。
表2-22 硫代硫酸盐镀银镀液组成及工艺规范

配方中硝酸银为主盐,硫代硫酸钠为络合剂,而醋酸钠为缓冲剂,可使镀液的pH值稳定在5~6的范围内,硫代氨基脲是表面活性剂,可使镀层结晶细致,并促使阳极正常溶解。
银的标准电极电位(0.799V)比氧的标准电极电位(1.229V)低,当有氧气存在时,银在热力学上是不稳定的,可以被空气中的氧气所氧化,生成黑色的Ag2O吸附在银层表面,使银层变色。银及其合金对大气环境中存在的H2S也特别敏感,易生成暗色的Ag2S,从而使银层变色。即便在镀银层上镀金,Ag2S可以从金镀层微孔中蔓延出来,从而覆盖在金层上。空气中的有机硫如甲基硫醇和二硫化碳的存在也会加快银层变色。此外,紫外光作为一种外加能源,可以促进金属银离子化,加速Ag的腐蚀变色。Ag2S的生成不但影响了镀银的外观,而且增大了银的表面电阻,极大地影响了其电气性能和钎焊性能。有研究资料表明,变色使镀银层表面电阻增加约20%~80%,从而使电子设备的稳定性、可靠性大为降低。因此,无论作为功能性材料,还是装饰性用途的镀银层,镀后都必须经过防变色处理,以提高其抗腐蚀性能。国内如深圳市思源达科技有限公司开发出镀银保护剂可有效防止镀银层在空气中的变色。对于镀银、镀金等贵金属的镀层,使用保护剂可在减少镀层厚度且不影响导电性和外观的情况下保持镀层的耐蚀性,有利于降低成本,节约资源。