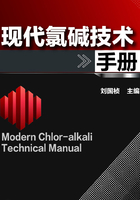
2.4 传统固液分离精制
2.4.1 传统固液分离精制工艺流程简述
从化盐桶顶部溢流出的达到饱的和状态的盐水,经折流槽进入盐水反应器。在折流槽的一定位置相继加入氢氧化钠、纯碱、氯化钡(或不加),进入盐水反应桶,经充分反应后的盐水再经折流槽进入澄清设备,在盐水进入澄清设备前加入助沉剂(通常使用聚丙烯酸钠高分子聚凝剂)。澄清后的盐水进入砂滤器,再经过碳素烧结管过滤器或白煤过滤器(隔膜法制碱工艺不需要)以进一步除去盐水中的悬浮物,使盐水中的悬浮物含量达到1mg/L以下,该盐水称为离子膜一次精制盐水。澄清和过滤产生的泥浆经板框压滤后作废渣处理(图2-18)。

图2-18 传统固液分离精制工艺流程示意图
2.4.2 一次盐水控制指标
经精制后,不同工艺对一次盐水的要求可见表2-17,一次盐水的控制指标如下。
NaCl:≥315g/L
NaOH:0.4~0.6g/L
Na2CO3:0.4~0.6g/L
Ca2++Mg2+: ≤5mg/L
:≤5g/L
Sr2+:≤2.5g/L
Fe3+:≤1mg/L
:≤10g/L
SiO2:≤7.5g/L
Ba2+:≤0.5mg/L
Hg:≤10mg/L
Mn2+:≤1mg/L
Al:≤0.1mg/L
Ni:≤10mg/L
I2 ≤0.2mg/L
NH3≤0.1mg/L
pH:8.5~9.5
SS:≤1.0mg/L
表2-17 不同电解装置一次盐水主要质量指标

2.4.3 一次盐水精制的工艺控制
2.4.3.1 氢氧化钠的添加
(1)添加氢氧化钠是为了除去盐水中存在的Mg2+。
(2)NaOH添加量的控制。100℃以下,Mg(OH)2的溶解度很小,一般在2×10-4~7×10-4mol/L的范围内波动,Mg2+和OH-在pH 8时开始反应,pH 10.5~11.5时,反应迅速完成,并形成胶状絮状物。在NaOH过量0.05~0.1g/L时,盐水中含Mg2+在1~2mg/L,因此在精制反应时,NaOH过量指标控制在0.1~0.3g/L为宜:过低,反应不完全,过高,一则浪费NaOH,使生产成本上升;二则碱性太高会影响后续盐水的澄清操作。
2.4.3.2 纯碱的添加
添加纯碱(Na2CO3)是为了除去盐水中存在的Ca2+。Na2CO3添加量的控制要求,当pH 10.5~11.5时,与反应生成CaCO3沉淀物。在一定温度条件下,Ca2+是否除得彻底,决定于两个因素,即反应时间的长短和Na2CO3的过量程度。若Na2CO3按理论用量加入,要搅拌数小时才能反应完全,但当Na2CO3过量0.3~0.5 g/L、温度大于50℃时,其反应可以在约30min内完成,盐水中的Ca2+含量可在5mg/L以下。
2.4.3.3 氯化钡的添加
添加氯化钡是为了除去盐水中的离子(现在大部分企业均不采用此法,而采用膜法,后有专项介绍)。Ba2+与
的反应是瞬间完成的,而Ba2+剩余量将对离子膜产生很大的影响,所以BaCl2的加入量应严格控制。其沉淀反应过程是一个可逆过程,当Ba2+或
在溶液中的含量相对较高时,根据同离子效应,反应向右进行。因Ba2+会对离子膜产生影响,应适当增加
的含量,而BaCl2的加入量主要根据澄清盐水中
的含量来决定。氯碱生产行业历来控制标准为小于5g/L,但在离子膜制碱工艺中为了防止Ba2+对离子膜产生二次污染,可将
含量的控制指标调整为6~8g/L。
的含量控制太低,将会使Ba2+在盐水中的含量相对增加,而控制太高,它会阻碍氯离子的放电,并且
在阳极放电的可能性增加:一方面,它的放电会产生游离氧[O],游离氧的存在对阳极的腐蚀是严重的;另一方面,它的放电会产生氧气,使氯气的含氧量上升,并且也消耗电能。根据离子膜使用的经验,Ba2+的存在对离子膜的危害程度比
6~8g/L含量下对电极的危害程度更大些。
BaCl2的添加处应与Na2CO3添加处相隔一定距离,必须先加Na2CO3后加BaCl2,否则过高的Ba2+会与反应生成BaCO3,从而白白消耗了两种辅助原料,同时使指标的控制更难以掌握。有条件的最好在Na2CO3添加0.5h后再添加BaCl2,或者在化盐前的化盐水中先添加BaCl2除
,去除BaSO4沉淀后,再在化盐桶出口添加Na2CO3除去Ca2+,这样可以使BaCl2、Na2CO3的消耗降低。
2.4.3.4 聚丙烯酸钠(TXY)助沉剂的添加
助沉剂有许多品种,但事实证明高分子聚丙烯酸钠作助沉剂是一个较好的选择,只要不过量添加,它不会对后道工序形成影响。
(1)聚丙烯酸钠助沉原理。高分子聚丙烯酸钠的分子量在150万以上,有的达到1000万以上,其分子链有亲水基团和吸附基团且足够长,具有良好的水溶性和吸附性。由于其分子链上的负电荷基团的相互排斥,使得整个分子链呈伸展状并表现出可绕性,这造成其分子链上吸附基团充分暴露,而有利于与悬浮粒子的接触,它的负电荷基团正好可以抵消不溶性钙、镁盐粒团上的正电性,促使其脱析沉降。这个过程是当盐水中投入聚丙烯酸钠时,聚丙烯酸钠分子迅速被吸附在悬浮粒子的表面上,首先是一个分子占据微表面上的一个或数个吸附位,而分子的其余部分伸展到溶液中去,这些伸展的分子链节再结合到另一个悬浮粒子的吸附位上,如此继续下去,结果就形成悬浮粒子间的吸附桥架,其总体质量不断上升,产生助沉作用。
(2)聚丙烯酸钠的选择。聚丙烯酸钠是一种高分子聚合物,它的分子量的大小对助沉的凝聚效果影响较大,经验数据显示,其分子量最好控制在500万以上,低于此值,絮凝效果不佳。聚丙烯酸钠有8%、10%或其他含量的液态物,也有98%以上含量的固态物,两者在作为凝聚物的特征上没有根本区别。但液态物运输相对困难,包装成本高,但它配制成低浓度的稀溶液相对容易些。固态物包装成本低,运输、储存较易,但它在配制时相对困难些,配制不当易形成团状物,易堵塞输送管道和计量仪表。
(3)聚丙烯酸钠的配制。不管是将液态还是固态聚丙烯酸钠配制成0.01%~0.05%浓度的稀溶液,均不宜进行剧烈搅拌,因为这样会破坏它的分子链,使分子链断裂,从而影响其凝聚效果,可采用低压压缩空气多点小量或低转速机械搅拌(一般选择10~20r/min)来进行溶液混合。配制水质最好使用有一定温度的纯水,采用不锈钢设备作容器,配制过程不宜带入其他杂质,否则会形成絮凝团状物堵塞输送管道或计量仪表,或对盐水造成二次污染。其稀溶液应现配现用,存放时间不要超过2天。
(4)聚丙烯酸钠稀溶液输送。配制好的聚丙烯酸钠稀溶液最好能自流进入盐水中,若要采用远距离输送形式,不宜采用高转速离心泵。因为它同样会产生上述(2)项所述的不良后果,甚至其破坏性更强,可选择往复式压缩输送设备,且流速不宜过快。
(5)聚丙烯酸钠溶液添加量。其添加量必须严格控制在标准范围内,一般控制为5×10-5~10×10-5 (聚丙烯酸钠与盐水的质量比)为佳,但在实际操作中,取上限或稍高于上限为好:太少了,凝聚效果差;太多了,它所起的作用恰恰相反,起到了分散剂的作用,使盐水中杂质离子无法有效沉淀,也就是所谓的盐水“不分层”,并且过量的聚丙烯酸钠会在离子膜或隔膜表面沉积,从而影响膜的性能。
(6)聚丙烯酸钠添加位置。聚丙烯酸钠在工艺中的投放位置要认真选择,既要为它与粗盐水的混合均匀创造凝聚条件,又要避免激烈搅拌,以免凝聚团被打碎而影响沉降。它最好添加在粗盐水进入澄清设备前端,当它与粗盐水充分混合后正好进入澄清桶内,过早或过迟添加都会影响其絮凝效果。
2.4.4 传统的盐水固液分离
2.4.4.1 密度差法固液分离
(1)密度差法固液分离的原理。密度法固液分离一般是根据重力作用的原理,即悬浮于盐水中的固体粒子与盐水的密度差别,比盐水密度大的固体粒子在重力的作用下而自由沉降,使杂质粒子与清液分离。其典型的设备类型有:道尔型澄清桶、斜板式(蜂窝)澄清桶、反应式澄清桶。依照斯托克斯定律,固体粒子在重力作用下的沉降速度可用公式表示为:
式中 d——固体粒子直径;
r1——固体粒子密度;
r2——清液密度;
μ——悬浮液黏度。
从公式中可以看出,固体悬浮粒子的沉降速度与悬浮粒子直径的平方、固体悬浮粒子的密度与清液密度之差成正比,与悬浮液黏度成反比。因此,在实际生产中,我们以向悬浮液中添加凝聚剂的方法来增加悬浮粒子的直径和密度;用提高悬浮液温度的方法来降低悬浮液的黏度,就是为了加速悬浮粒子的沉降速度并促使沉淀颗粒长大,提高澄清设备的生产能力。
比盐水密度小的固体粒子在气浮的作用下而自由上升,使杂质粒子与清液分离,其典型的设备是浮上澄清桶。
(2)密度差法固液分离的典型装置
①道尔型澄清桶
a.结构及原理。道尔澄清桶结构见图2-19,桶的底部为圆锥形,倾角为8°~9°,桶的中央有一个中心筒,筒中有一根长轴,轴的下端连接有泥耙。筒中长轴的上端与传动装置相连,带动泥耙转动,转速为(控制泥耙的尖端线速度不超过0.6m/s)。桶的上部有一个环形溢流槽。粗盐水由中心筒的上部进入,入口管呈S形,位置处在液面以下0.5~0.7m处,使粗盐水在中心筒中做旋转运动,中心筒好似旋流式反应室(容积一般保持进料盐水有10~15min的凝聚反应时间)。但在中心筒的下部必须装井字形整流方格,一般高0.8m,每格大小约为0.5m×0.5m,以消除液体的旋流,防止影响盐水中杂质的沉淀。中心筒的下部出口处设置为扩口,以减慢盐水流速,防止破坏泥封层。粗盐水挟带絮凝的沉淀离开中心桶扩口后,速度减慢,又经底部泥浆沉淀层的阻留,继续向下沉降,部分沉淀物下沉到桶底,经缓缓转动的泥耙集中,定时从排泥口排放到泥浆槽。澄清的盐水则不断上升,连续从澄清桶上部边缘的溢流堰流出。澄清在上部的澄清的盐水,在底部生成增浓的泥浆。清盐水上升的速度应小于固体颗粒沉降的速度。清液区应有足够的深度,防止细微的颗粒随着溢流的清盐水流出。

图2-19 道尔型澄清桶结构图
1—传动装置;2—中心筒;3—粗盐水入口;4—溢流槽;5—澄清盐水出口;6—泥耙;7—排泥口
澄清桶的生产能力取决于盐水在澄清桶中的上升速度、澄清桶的截面积及悬浮的固体颗粒的沉降速度。澄清桶的高度对其生产能力也有一定的影响。道尔型澄清桶的优点是桶身容积大,稳定性能好,对盐质变化、过碱量变化的适应性强,生产的弹性比较大,不易受各种因素变化的影响;缺点是体积庞大,投资费用较多。
b.道尔型澄清桶主要尺寸的确定
ⅰ.直径
D2=4Q/(πV)
式中 D——道尔型澄清桶直径,m;
Q——盐水的流量,m3/h;
V——澄清的盐水上升的速度一般取0.4~0.6m/h,优质盐取上限,劣质盐取下限,m/h。
ⅱ.高度按照澄清原理,澄清桶能力主要与澄清面积有关,而与高度关系不大。生产实践表明,为了稳定澄清操作,保持适当的泥封层,澄清桶应有一定的高度,国内一般采用5~7m。
ⅲ.中心筒直径及高度应根据盐水在其中进行的凝聚反应时间计算。凝聚反应时间一般为10~15min。
式中 T——凝聚反应时间,min;
f——中心筒截面积,m2;
H0——中心筒高度,m;
Q——盐水流量,m3/min。
中心筒直径:d2=4f/π,单位为米(m)。
中心筒的高度一般取:
H0=(0.8-0.9)H
式中 H——道尔型澄清桶直桶部分高度,m。
ⅳ.集水装置。当澄清桶直径小于4m时,采用环形集水槽;当直径大于4m时,应另加辐射向集水槽4~8条,以保证集水均匀。
假设流体在槽内均匀流动:
式中 h1——集水槽流体所需的断面高,m;
q——集水槽的流量,m3/s;
v——集水槽内流速,一般取0.6~0.7m/s,m/s;
b——集水槽宽度,m。
式中 h2——速度压头损失高度,m;
λ——摩擦系数,0.024;
L——槽长,以环形槽为例,L最大为/ m;
R——水力半径,R=F/Π,m;
F——浸液的截面积,m2;
Π——浸渍周边,m。
式中 H3——孔眼离槽底高度,m;
d0——孔眼直径,一般取10mm,m。
式中 H4——孔上水深,一般取0.02~0.03m,m;
V1——孔眼流速,一般取0.4~0.5m/s,m/s;
μ——流量系数,一般取0.62。
集水槽高度还应加上为发挥设备潜力和调整安装水平留有的保护高度H5,所以,槽总高=H3+H4+H5。
淹没式孔眼的数量:
小孔总截面积(m2):∑f=Q/V1
孔数:
小孔的分布应使各区域的流量均匀为原则。
②斜板式澄清桶
a.斜板式澄清桶的工作原理及结构对于液相非均匀分离的设备必须具备在单位容积设备内,其有效澄清面积尽可能大,沉降距离小,液流呈稳定的层流,分离出的固相能易于连续排除等条件。
澄清桶在一定的流量和固体颗粒沉降的速度下,其沉降效率η与澄清桶的截面积成正比。
式中 η——沉降效率;
V——固体颗粒沉降的速度,m/s;
A——澄清桶的截面积,m2;
Q——盐水的流量,m3/s。
而在直立的澄清桶内加设一定的斜板后,在理论上可以数倍地提高其澄清效率,斜板式澄清桶就具备了上述条件,其结构如图2-20所示。反应后的浑浊盐水经S形进料管和中间筒的扩大口折返向上,沿着斜板缓缓上升,在每个水平截面上各点的上升速度都是相同的。当盐水中大的悬浮颗粒下沉速度大于盐水上升速度时,就沉向底部;颗粒较小的悬浮物随着盐水通过斜板间隙继续上升,并逐渐沉降在斜板上,当斜板倾角大于盐泥摩擦角,盐泥沿斜板滑落,聚积在澄清桶底,定期从排泥口排出。清盐水继续上升至溢流堰,经清盐水出口流出,斜板的倾角一般为60°。斜板式澄清桶的主要优点是设备体积小,占地面积少,沉降效率高;缺点是设备制造、检修比较麻烦,而且受盐的质量、Mg2+与Ca2+比值、盐水温度等影响,敏感性强,稳定性比道尔型澄清桶差。

图2-20 斜板式澄清桶结构图
1—盐水进口;2—桶盖;3—溢流堰;4—桶体;5—喇叭口;6—人孔;7—排泥口;8—斜板;9—清盐水出口;10—传动装置
b.斜板式澄清桶的尺寸的确定
ⅰ.所需斜板面积
式中 F1——道尔型澄清桶所需面积,m 2;
V1——道尔型澄清桶的盐水上升速度,m/h;
Q——流量,m3/h。
则斜板的实际面积:F=F1/(cos60°×0.6)
式中,0.6为系数,斜板效率。
ⅱ.斜板式澄清桶的直桶部分高度(h1)一般不小于3m。
ⅲ.斜板的垂直高度:h2=1~1.5m。
ⅳ.凝聚反应室容积按下式计算:
式中 T——凝聚反应停留时间,取10~15min;
Q——盐水流量,m3/min;
V——凝聚反应室容积,m3。
ⅴ.从凝聚反应室向外按间距计算斜板面积,待满足要求,再按几何图形算出斜板式澄清桶上部的直桶部分直径D1和斜板式澄清桶下部的直桶部分直径D及中心桶上部直径D2。
ⅵ.校核最小界面的雷诺数,使Re<2100。
ⅶ.溢流槽尺寸计算
式中 F——溢流堰内液体流过截面,m2;
V——溢流堰内盐水流速,取0.6~0.7m/s。
③蜂窝形澄清桶。蜂窝形澄清桶外形与斜板式澄清桶类似,主要由蜂窝、筒体、整流栅等构成。粗盐水从底部进入凝聚区,较大的絮状粒子被悬浮层截留。通过悬浮层的粗盐水上升经整流栅稳流继续流入扩大部分,在此减缓流速后,进入蜂窝澄清区。固体悬浮杂质沉降在蜂窝的斜面上,清液继续上升,经集水管溢流槽而流出桶外。盐泥由于蜂窝的倾角大于盐泥的摩擦角而下滑至桶底排出。
蜂窝形澄清桶的主要优点是生产能力大,盐水质量稳定,操作简单平稳,对温度变化不太敏感;缺点是澄清桶容积小,盐水在其中停留时间短,对过碱量和凝聚剂比较敏感。
④反应式澄清桶。反应式澄清桶是结合了几种重力沉降分离技术优点开发的反应澄清设备,其结构如图2-21所示。反应式澄清桶由中心锥形带六层搅拌的反应区和外锥形主体组成,粗盐水先从上部进入反应区,经充分反应并有足够的停留时间,然后自下而上通过倒锥形变速率上升澄清区,经上部溢流管的侧孔汇集到中心溢流堰后经排出管排出。

图2-21 反应式澄清桶结构图
其特点是:中心反应体积大;盐水上升分布均匀;澄清变速率流动,对温度差、浓度差等密度差变化敏感度低。反应式澄清桶澄清区内壁和外壁有斜板效应,盐水上升速率较高,变速澄清使小颗粒在下部相互碰撞结合成大颗粒沉降。
⑤浮上澄清桶。浮上澄清桶对于含镁高的原盐具有较好的适应性,一些盐水精制技术中,有对粗盐水进行先除镁再除钙的要求,而要单独除镁就必须采用浮上澄清桶。
a.浮上澄清桶的结构和工作原理。浮上澄清桶的工作原理是使空气溶解在粗盐水中,然后将加压的粗盐水突然减压,溶解在盐水中的空气就形成微小的气泡释放出来,并在凝聚剂的作用下与盐水中的杂质颗粒附着在一起。附着了气泡的杂质颗粒的假密度大大降低,在盐水中所受的浮力使其克服本身重力和液体摩擦阻力,以一定的速度向上浮起从上面排出,剩余的盐泥则随盐水通过斜板下降分离沉积于桶底,从底部排出,清净盐水通过上升管由桶外侧导回桶内,从桶上部引出。所以现代的浮上澄清桶结合了浮上桶和斜板式澄清桶的原理,是综合功能澄清桶,被广泛采用,其结构见图2-22。

图2-22 浮上澄清桶结构图
1—下排泥口;2—上排泥口;3—清水出口;4—溢流口;5—进粗盐水口;6—人孔
浮上澄清法的一种流程是通过循环少量的清盐水,将浮上澄清法所需要的空气引入系统。带有饱和空气的少量循环盐水经释放装置在凝聚反应室内释放出大量的细微气泡,与进入室内的粗盐水中的悬浮物充分接触而附聚在沉淀颗粒上,并上浮到液面,由顶部刮板将浮泥集中在上部的泥槽,从排泥口排出。清盐水从凝聚反应室出来,折流向下,通过折流圈经澄清盐水出口流出,较少一部分清盐水由循环泵打到立式填充吸收塔的顶部,落下时与进入塔内的压缩空气接触而形成饱和空气的盐水。
浮上澄清法的最佳效果取决于:精制反应充分完成;空气与清盐水有足够的接触机会,并保持一定的压力;溶于盐水中的空气在凝聚反应室内完全释放成为细微的气泡;粗盐水中加入适量的凝聚剂;及时排除浮泥和沉泥。
浮上澄清法的优点是适合于含镁量较高的原盐,受温度变化的影响较小,清液分离速度快,生产能力大;缺点是辅助设备多,动力消耗大,操作比较麻烦。
b.浮上澄清桶的主要尺寸的确定
浮上桶直径:
式中 D——浮上桶直径,m;
V——浮上速度,一般采用1.0~2.0m/h,m/h;
Q——盐水流量,m3/h;
F——浮上桶横截面积,m2。
ⅰ.凝聚室容积。凝聚反应室由搅拌区及反应区组成,在搅拌区入口流速约0.8~1m/s时,停留时间约1min,反应区停留时间约5.5~8min,出口端流速约6~10m/h。
式中 Q——盐水流量,m3/h;
T——凝聚反应时间,min。
ⅱ.凝聚室出口端速度(m/h):
ⅲ.向下折流速度(m/h):
取W1/W2=3.3~4.5。
ⅳ.出中心斜板处速度:
取W3=11.5~18m/h。
ⅴ.出中心斜板处后的上升速度:
取W3/W4=2.3~3.3。
ⅵ.清水通道速度:
式中 n——清盐水通道管管子根数,一般取12~16;
r5——清盐水通道管管子半径,m;
W5——一般按自然流速取0.5m/s。
清水通道出口端应有液面调节装置。
ⅶ.沉泥斗容积:沉泥斗应有8h的储泥量,使沉泥在其中得到浓缩。
ⅷ.浮泥槽也有8h的储量。
ⅸ.浮上槽的高度根据经验选取。
c.浮上加压槽的计算
ⅰ.容积确定
式中 V——浮上加压槽容积,m3;
G1——盐水质量流量,kg/h;
G2——空气质量流量,kg/h;
G——盐水与空气混合后的体积流量,m3/h;
r——盐水密度,一般r=1.16~1.18;
t——盐水在加压槽内的停留时间,一般取t=3min;
n——填充系数,取0.75。
ⅱ.直径的确定
式中 D——浮上加压槽直径,m。
根据生产经验,加压槽内盐水流速W取0.025~0.031m/s。
ⅲ.高度的确定
式中 D——加压槽直径,一般取H/D=3~4,m;
V——加压槽体积,m3;
H——加压槽高,不包括封头,m。
ⅳ.盐水进出管管径计算
式中 D——盐水进出管管径,m;
G——盐水体积流量,m3/s;
W——盐水流速,一般取1~2m/s。
ⅴ.平衡管管径的确定。平衡管管径一般可取0.05m。
ⅵ.加压盐水泵的选择。泵流量Q根据设备生产负荷确定,其泵扬程H计算如下:
式中 H——泵扬程,m液柱;
P1——加压槽内压力,m液柱;
ΔP——盐水管阻力降,m液柱;
H1——泵入口处的压力,m液柱 (入泵盐水液面在泵吸入口之下,H1为正值;入泵盐水液面高于泵吸入口时,H1为负值);
H2——盐水升扬高度,裕量系数取2~5m液柱,m液柱。
2.4.4.2 传统过滤法固液分离
过滤法固液分离原理是利用某种过滤介质,当含有少量悬浮固体颗粒的清盐水通过该过滤介质时,因通道的原因,使大于过滤介质通道的悬浮固体颗粒被过滤介质截留,清盐水及小于过滤介质通道的悬浮固体颗粒则能通过,以此达到固液再分离的目的,使一次盐水中悬浮固体颗粒的含量达到控制的要求。
2.4.4.3 传统过滤法固液分离的典型设备
(1)虹吸式过滤器
①虹吸式过滤器的结构及工作原理。虹吸式过滤器主要是由过滤器本体、进水分配箱、水封槽、虹吸系统、过滤层等构成,结构见图2-23。过滤器被中间隔板分为滤料层及洗水储槽两部分。过滤层底部设有百叶式滤阀作为盐水透过通道,其上铺有各种直径的石英砂或其他材质滤料,顶部和下部的人孔用来装卸滤料和检修。

图2-23 虹吸式自动反洗过滤器原理图
1—进水总管;2—水分配高位槽;3—排气箱;4—进水口;5—联通管;6—虹吸反洗管;7—清盐水出水管;8—虹吸辅助管; 9—虹吸破坏管;10—水喷射真空泵; 11—过滤器本体;12—洗水储槽;13—虹吸反洗管最高点;14—水封槽;15—虹吸反洗液最低点
澄清后的清盐水从澄清桶上部溢出进入分水箱,分别平均流入各过滤器,然后经排气槽进入滤料过滤层,盐水自上而下经过滤层后,所夹带的悬浮物颗粒绝大部分被截留下来,清水通过联通管进入上部洗水储槽,再由出口管溢流出。随着过滤时间的延长,滤料截污越来越多,其阻力越来越大,虹吸管液位不断上升,当达到虹吸辅助管高度后,通过虹吸辅助管和水喷射真空泵形成虹吸作用,用储水箱中的过滤后盐水对滤料进行反洗。当反洗水储槽液面下降到虹吸破坏管低位后,空气从虹吸破坏管中进入虹吸管,虹吸中断,反洗停止,过滤自动进入下一过滤周期。出过滤器后的清盐水作为过滤盐水,过滤盐水可以满足隔膜电解需要。但是离子膜精盐水使用此过滤器存在硅与铝离子的影响,应使用高纯石英砂或其他材质滤料。
图2-23中水分配高位槽2与虹吸反洗管最高点13的位差为进水推动力,用以克服进水管道阻力,一般在300~500mm;洗水储槽12的溢流水面与虹吸反洗管最高点13之间的位差为过滤最大阻力,一般控制在1500~1800mm,过滤料层高度根据计算确定。
②虹吸式过滤器的主要尺寸的确定
a.反冲水储槽容积的计算
过滤器反冲水量:
式中 Q——反冲洗水量,m2;
P——冲洗强度,一般取15L/(s·m2),L/(s·m2);
T——冲洗时间,一般取240s,s;
F——过滤器横截面积,m2。
当两个过滤器共用一个反冲水储槽时,中间应用隔板隔开,一个反冲洗,另一个仍进行过滤,清盐水只供一个冲洗用。
b.过滤器直径计算
式中 D——过滤器直径,m;
V——滤速,石英砂滤料V取7~10m/h,m/h;
G——盐水过滤量,m3/h。
c.滤料最上一层即过滤层,粒径为0.5~1.0mm,冲洗膨胀率为40%~50%,滤料层高700mm左右。整个过滤滤料可分为砾石支撑层和滤料层,砾石支撑层的作用是支撑石英砂滤料,滤料层的作用是过滤。过滤单元各层的要求如表2-18所示。
表2-18 过滤单元各层要求

d.过滤器的起始水头损失ΔH
(a)卵石支撑层阻力h1
式中 H——支撑层厚度,m;
Q——冲洗强度,L/(m2·s)。
(b)石英砂滤料阻力h2
式中 ρ2——石英砂密度;
ρ1——盐水密度;
m0——石英砂膨胀前的孔隙率;
L0——石英砂膨胀前的厚度,m。
(c)沿程阻力h3
式中 λ——摩擦系数,0.024;
L——管长,m;
D——管内直径,m;
W——盐水在管内的流速,m/s;
g——重力加速度,m/s2。
过滤器的起始水头损失:
最终水头损失一般为1.3~1.7mH2O(1mmH2O=9.80665Pa,下同),一般取1.4mH2O。
e.虹吸系统管径的选择
(a) 虹吸上升管与虹吸下降管D1(m)
式中 W——管内流速,一般为2~3m/s,m/s;
G——盐水流量,m3/s。
(b)盐水进口管D2
式中 W——管内流速,一般为1~2m/s,m/s;
G——盐水流量,m3/s。
(2)白煤过滤技术 白煤过滤器是我国于1994年引进迪诺拉离子膜电解槽时的配套工程装置,该装置采用马来西亚椰壳生产的白煤(活性炭)作为过滤介质应用于盐水的过滤,具有长周期高效率的运转性能和良好的耐腐蚀特点,也可除去盐水中游离氯且运行成本很低。
①白煤过滤器的工作原理。白煤过滤器也是重力式过滤器,过滤原理除与砂滤器基本相同外,还有吸附悬浮物和去除游离氯的作用,同时不增加盐水中硅的含量,它主要是由过滤器本体、挡圈、白煤层等构成。过滤器内上部有溢流堰用来分配进料盐水以及收集洗水,挡圈防止滤液短路。过滤器底层铺有直径为5~20mm的白煤,厚度约为700~900mm;其上部有直径2~3mm的白煤,厚度约为2500mm;顶部和下部的人孔用来装卸填料和检修,上部人孔盖上有平衡管便于排除空气(图2-24)。

图2-24 白煤盐水过滤器原理图
盐水中的固体颗粒堵塞填料床,造成过滤器液压升高,液位也因此上升,当液位上升至允许最高限时,过滤器就要清洗。采用空气反吹将堵塞和吸附在活性炭填料床的固体颗粒和悬浮物吹出,然后用过滤后盐水通过反洗泵在相当强度条件下,反洗悬浮物并带走,达到反洗再生目的。
②白煤过滤器的主要尺寸。生产5万吨烧碱所需设备具体规格是:ϕ3000mm×6200mm共三台,过滤速度为6m3/(h·m2),通常情况下设备采用的是钢衬低钙镁橡胶,三台设备同时运行,再生时一台反洗,其他正常生产运行。
③白煤过滤器的操作
a.正常生产界区外的盐水经泵入白煤过滤器,盐水经过滤层后,所夹带的悬浮物颗粒绝大部分被截留下来,出过滤器后的清盐水作为二次过滤盐水经泵直接进入螯合树脂塔进行精制。
b.反洗过程白煤过滤器反洗操作步骤:
(a)过滤器停车。将选择开关置于“清洗”位置,关闭盐水入口管线上的手动阀,过滤器排空至出口虹吸液位部分。
(b)空气吹洗开始。逐渐增加空气量,大约2min内达到65m3/h,空气压力为0.5kgf/cm2(1kgf/cm2=98.0665kPa,余同),5min后结束空气吹洗。
(c)开始盐水反洗。逐渐增加盐水流量,1min内流量升至200m3/h反洗10~15min结束。
(d)过滤器排空静止。盐水排空至填料顶部液位,时间为10min。
(e)恢复过滤器运行。缓慢开阀,打开盐水入口管线的手动阀,使盐水流量达到要求值(2min内达到设定流量),检查过滤器压力,正常则投入运行。
(3)碳素管过滤 1961年德国Schleicher & Schnell公司最早开发了碳素管过滤器(tubular module) ,其卓越的效果使其可以应用于一切液体物料的过滤,并具有长周期高效率的运转性能和良好的耐腐蚀特点。过滤元件为碳素烧结管,碳素烧结管是由纯碳加石油焦(主要成分为碳)成型后的多孔碳素材料经烧结而成,具有较好的耐腐蚀化学性能,除不可用于强氧化剂外,在温度≤200℃的酸性、碱性溶液中均可使用。通常情况下,碳素管过滤器的容器以及部件采用的是钢衬低钙镁橡胶。
①碳素管过滤器的工艺流程图见图2-25。

图2-25 碳素管过滤器工艺流程图
1—盐水储槽;2—盐水泵;3,4—盐水过滤器;5—预涂槽;6—预涂泵;7—本体给料槽;8—本体给料泵;9—压缩空气管线开关阀;10,11—清洗加压时开关阀;12,21—盐水流量调节阀;13,22—进入过滤器盐水管线开关阀;14,24—清洗排液阀;15,23—预涂液开关阀;16,25—预涂液混合开关阀;17,26—冲液排气阀;18,27—预涂液混合开关阀;19,28—过滤盐水开关;20,29—反洗盐水开关阀;30—过滤盐水进入预涂槽开关阀;31,32—预涂液循环开关阀
②碳素管过滤器的结构及工作原理
a.碳素管过滤器的结构如图2-26所示。

图2-26 碳素管过滤器结构示意图
碳素管过滤器的主体设备材质为钢衬低钙镁橡胶或衬PO,中间设置有钢衬低钙镁橡胶或衬PO的花板,在花板上固定碳素管过滤元件。碳素管元件外形及组装件如图2-27和图2-28所示。

图2-27 碳素管元件外形图

图2-28 碳素管组装件示意图
b.碳素管过滤器的工作原理。先用泵将盐水和α- 纤维素配制成的悬浮液送入过滤器中,并且不断循环,使碳素烧结管表面涂上一层厚度均匀的α- 纤维素(助滤剂),叫作预涂过程,目的是形成初始滤层,提高过滤质量、避免碳素管被镁钙堵塞;然后把澄清盐水送入过滤器,同时用定量泵把与盐水中SS质量成比例的α- 纤维素与澄清盐水一起送入过滤器,这样做的目的是过滤过程中生成的泥饼有一个适当的骨架,增大过滤流量,在返洗时易碎成小块剥落;此时加入的α- 纤维素称为本体给料,加入量太少会导致过滤器压差上升很快,加入太多会占用不必要的过滤空间而缩短过滤周期,由于α- 纤维素的骨架作用,α- 纤维素和截留在预涂层表面的SS混合,形成新的过滤层,此新的过滤层也能通过滤液,使过滤器能在SS含量为10mg/L时,通过添加等量的α- 纤维素,保证在设计流量下,48h内过滤器的压差不超过0.2MPa的状况下安全运转。
③碳素管过滤器的主要尺寸的确定。一般碳素管的盐水通率为2m3/(h·m2),因此年生产1万吨烧碱需要的碳素管数量计算如下。
a.过滤面积的计算。年生产1万吨烧碱,以年运行时间8000h计,每小时需产碱量为:10000÷8000=1.25(t/h)
每生产一吨烧碱需要盐水量为:9.5 m3/h
每小时需要通过过滤器的盐水总量为:
1.25×9.5=11.875(m3/h)
需要碳素管的总过滤面积为:
11.875m3/h÷2m3/(h·m2)=5.9375m2
b.碳素管数量的计算。假设选取内径70mm、外径120mm、长度500mm的碳素管,每根碳素管的过滤面积为:
S=πD外L=3.14×120×500×10-6=0.1884(m2)
年生产1万吨烧碱需要的碳素管数量为:
5.9375m2÷0.1884m2=31.5(取数为32根)
c.外形尺寸的确定。一般碳素管组件如图2-28所示,可两根碳素管为一组,然后根据组数来确定花板的开孔数。花板上的开孔以正三角形布置,孔间距以碳素管的外径1.5倍左右来确定,然后根据此来确定设备的外形尺寸。
④过滤助剂α- 纤维素及其使用
a.α-纤维素是由精制棉水解制得,其分子式为(C6H10O5 )n ,其中n=170~200 ,α-纤维素:粒度为250μm、200~250μm、150~200μm、100~150μm、50~100μm 的α- 纤维素所占的比例分别为30%、17%、26%、26%和1.0%。α- 纤维素的粒度分布与碳素管的滤孔尺寸(平均110μm) 有关。若纤维过细,容易堵塞毛细管,造成过滤阻力增大;纤维过粗,附着力不强,容易脱落,造成α- 纤维素用量增大,过滤效果也不佳。因此,纤维素的颗粒要求较粗且均匀。
b.α-纤维素的使用。α-纤维素的使用是采取预涂层法及掺浆加料法。采用预涂层法是为防止碳素管微孔的堵塞,并提高过滤精度。过滤之前,先将过滤助剂α-纤维素(以碳素管过滤面积每平方米1kg α-纤维素计算) 分散于盐水中,配制成预涂液,并在预涂槽与过滤器之间进行循环。通过一定时间的循环,即可在碳素管表面形成厚度约为2~3mm的预涂层。
主体给料过滤,即在进入过滤器的一次精制盐水中连续加入助滤剂。所加的助滤剂在盐水中起晶核的作用,而且对微小的SS 起助凝作用,从而提高过滤精度。这种过滤方法可以迟缓过滤阻力,延长过滤周期,减少单位盐水所耗用的助滤剂量,主体给料助剂浓度为10.4g/L,流量控制为10L/(万吨·h)。
⑤碳素管过滤器的操作及注意事项。碳素管过滤器的操作步骤如下:
a.碳素管预涂在预涂罐内,添加适量的α-纤维素,一般是碳素管过滤面积每平方米1kg,然后加入过滤后盐水配成2.7g/L预涂液,充分搅拌10min,用已经过过滤的精盐水向过滤器充液,直到盐水溢流入废液池为止;然后开动预涂泵,向过滤器内输送预涂液,通过过滤器前出口回到预涂罐,使α-纤维素和盐水充分混合,混合时的流量为设计流量的1.3~1.4倍左右,混合时间10min,预涂流量为2.5m3/(m2·h)。
切换阀门,使预涂液出口由过滤前改为过滤后出口就开始预涂。在这种状态下,预涂液由碳素管外侧流向内侧,这时α-纤维素在元件表面形成均匀的预涂层,预涂进行30min,此时预涂罐内的液体应异常澄清透明。
切换阀门,用一次盐水代替预涂液,一次盐水流量为设计流量,并让过滤后盐水返回一次盐水罐,目的是把质量可能不好的过滤盐水返回一次盐水罐,此时需要10min,这个过程一般称为原液循环。
预涂步骤为:
(a)充液。过滤器首先进行充液,进液至高位。充液时用液面计监测液面,由于充液时过滤器压力的变化往往会对液面计显示的准确性产生不利影响,所以要对过滤器充液做认真监视。
(b)混合。液体在过滤器与预涂槽之间循环,目的是使预涂液浓度均匀,混合时间为10min。
(c)预涂。混合10min后,过滤器开始预涂,预涂时间为35min。
(d)通液。预涂35min以后,如果另外一台过滤器处于通液状态,预涂过滤器便进入预涂,保持状态直到切换为止。预涂时间达到以后,如果另外一台过滤器处于停止状态,则预涂过滤器在完成预涂以后,该过滤器即由预涂状态进入原液循环状态。
运行中的过滤器当压差达0.2MPa或过滤时间达48h将自动停止通液,所以在运行过滤器的压差达0.2MPa或过滤时间达48h以前必须完成待机过滤器的预涂,以便及时自动切换,保证连续通液,一般规定在运行过滤器的压差达0.15MPa或过滤时间达46h待机过滤器做预涂准备,提前完成预涂。
运行中的过滤器在压差或过滤时间达到规定时,如果待机过滤器不能及时投入运行,DCS可保持运行过滤器的继续通液,然而在运行的过滤器压差达0.25MPa时,则必须停止过滤。
b.正常运行原液循环结束,则切换阀门,使过滤后盐水进入过滤盐水罐,过滤后10min后,启动主体给料泵,定量地向粗盐水泵加入α- 纤维素悬浮液,直到运转时间达到48h,或者过滤器的差压达到0.2MPa时停止运转,进入返洗。
c.返洗过滤器运转48h之后,或者差压达到0.2MPa之后,这台过滤器就应退出运转,把这台过滤器内碳素管上的过滤层全部洗清,以便再经过预涂之后,重新工作,这个过程叫作返洗。返洗总共进行4次,操作程序如下:
一次返洗:排液,待液排完后,关闭排液阀门,打开空气阀门,待过滤器内压力达到设定点跳开(约0.4~0.5MPa),快速打开污水排放蝶阀,过滤器内侧液体通过碳素烧结管,使过滤层脱落,过程约20s,然后继续通入空气,排净过滤器内液体,过程约60s。
二次返洗:向过滤器内加过滤后盐水,待有液体外溢,溢流15s后,打开排空阀门,待过滤器内液位达到一定高度并有液体溢出后停止加液;向过滤器内注入压缩空气,待压力达到0.4~0.5MPa后,快速打开污水排放蝶阀,使过滤器内侧液体通过碳素烧结管,使残余过滤层脱落,程序一次返洗。
三次返洗:过程与二次返洗相同,把方向阀进行切换。
四次返洗:过程与二次返洗相同,把方向阀进行切换。
返洗操作到此结束,采用三个方向操作,目的是冲洗过滤器上部及孔板下面附着的滤饼。这样的操作方法比单一操作更干净。一般均用过滤后盐水来返洗,也有把二次、三次、四次返洗过程用纯水替代过滤后盐水,对于稳定生产、降低生产成本有利。
操作过程中的注意事项:
(a)一次精盐水中游离氯(主要以ClO-的形式存在)的含量偏高,游离氯会与碳素管的碳发生化学反应,同时也与起黏结作用的石油焦发生化学反应,使碳素管的滤孔阻力增大,严重时会造成碳素管破裂。因此,在进入过滤器的一次精盐水中必须加入亚硫酸钠溶液,以去除一次精盐水中的游离氯。
(b)在进入过滤器的一次精盐水中必须连续稳定地加入α- 纤维素悬浮溶液,否则会影响过滤器的过滤周期及效果。
(c)进入过滤器的一次精盐水必须有稳定的流量,且过滤流量波动不能低于额定流量的60%,否则会影响过滤器的预涂层及过滤效果。
进入过滤器的一次精盐水中不能夹带空气,否则会影响过滤器的过滤效果。
注意相对稳定,每小时的流量变化不得超过设计流量的40%,流量的急剧变化会导致过滤器内返浑,影响过滤效果。
注意进料盐水是否夹带气泡,气泡进入过滤器会吸附到预涂层上或冲刷预涂表面,导致过滤层穿孔和破坏预涂层,影响过滤效果。通液流量最小不得低于30%。
典型的由澄清桶、砂滤器和白煤过滤器组成的传统盐水精制流程见图2-29。