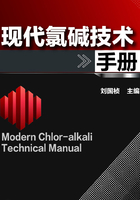
2.2 饱和盐水的制备
2.2.1 盐水的制备过程
进入氯碱电解工序的盐水必须是符合质量指标的合格饱和盐水,将固体氯化钠用不饱和淡盐水和工艺添加水进行溶解成饱和盐水,这一过程称为盐水制备。其主要工艺过程是氯化钠的固定床固液传质过程,即固体氯化钠溶解过程,同时伴随氯化钠的杂质也溶解到盐水中并同溶液中的化学物质发生化学反应,因此也伴随化学反应过程。在盐溶解的同时,为保持恒定的工艺条件,要不断补加溶解掉的固体盐,同时要尽可能保持化盐水条件与溶解盐相匹配。因此要控制化盐时间、盐水流速、盐层高度、化盐温度和淡盐水有害阴离子浓度等指标。
2.2.2 化盐工艺
(1)地上桶式化盐工艺。化盐桶全部位于地上,盐水自底部进入,顶部流出,盐由皮带机自动加入到化盐桶上部中间位置。地上桶式溶盐方式适合于各盐种使用,特别适合于自流精制工艺,即精制、沉淀、过滤全部靠位差自流完成。该方法有如下优点:盐水自流过程中不会破坏杂质颗粒,有利于杂质颗粒的沉降,盐水输送设备较少,动力消耗低,泄漏点少,清理桶中的淤泥比较方便,可以定期从底部直接排出。
(2)地下桶式化盐工艺。化盐桶全部或部分位于地下,盐水自底部进入,顶部流出,流入缓冲罐然后由泵送出。化盐桶一般为混凝土结构,使用寿命较长。适合使用铲车直接上盐,减少了皮带机建设和维护成本。现新建设企业大部分采用此种方式,但该结构检修、清污不方便。
2.2.3 化盐的工艺控制
化盐的工艺控制点主要有:化盐盐层的高度控制、化盐的温度控制以及化盐水的控制三点。
2.2.3.1 化盐盐层的高度控制
为了保证盐水的饱和度,化盐桶的盐层高度必须保证。一般控制高度为2.5~3.0m。为化盐桶上盐,应在化盐桶上部设计一个中心储盐桶,它可以对盐层进行恒定给料,相对准确地控制盐层高度,有利于避免使用精制盐时细盐粒夹带溢出、堵塞管路,保证盐水质量(图2-3)。

图2-3 带中心储盐桶的化盐池示意图
上盐采用皮带运盐机或铲车,都可满足化盐需求。
2.2.3.2 化盐的温度控制
为了制取饱和的盐水,必须采用热法化盐,化盐温度一般为55~65℃,并应相对恒定。化盐温度可对以下几方面产生影响。
(1)影响盐的溶解度。如图2-4所示,盐的溶解度随温度的上升而增大。其溶解度还会受其他阴离子的影响,硫酸根和氯酸根可直接影响盐的溶解度,所以当系统中的氯酸根和硫酸根浓度大时,氯化钠的饱和浓度将相应下降。

图2-4 氯化钠在水中的溶解度和温度曲线
(2)影响盐溶解速度。氯化钠的溶解速度主要受控于氯化钠结晶体向溶液的传质速度,它依赖于固液相对速度和液体的黏度。一般认为在较高温度下,由于黏度降低,溶解度随之加大。
图2-5所示为饱和氯化钠溶液的黏度与温度的关系。由于溶盐温度高,溶盐黏度低,溶解速度快,达到饱和的时间可缩短,提高了化盐设备的生产能力。

图2-5 饱和氯化钠溶液的黏度与温度的关系
(3)促进沉淀物反应的完全及加快沉淀物沉降速度,温度越高,沉降越快,但溶解度较高。
(4)对除Ca2+有利。在相同条件下,CaCO3在低温时生成沉淀需要一定的时间,所以在沉淀曲线上也产生时间的偏移。60℃以上时,CaCO3的实际生成反应时间将大大缩短。
(5)提高过滤速度。盐水的过滤速度是由液体的黏性、泥浆的物理化学特性、压差等决定的,所以温度对它的影响较大。沉淀物的过滤阻力随温度的上升而减小,因此升高温度能提高过滤速度。
综上所述,热法化盐对盐水精制的各个工序都有好处,化盐的温度一般控制在55~65℃之间。低于该范围,对上述五项均有影响;高于该范围,能源消耗太大,经济性不佳。
2.2.3.3 化盐水的控制
为使化盐过程可控进行,需要对化盐水特殊控制,主要控制内容为碱含量、游离氯含量等。配水的主要目的是对化盐水中的碱含量进行稳定控制,使化盐水中的碱含量能尽可能地与当时使用的原盐质量相匹配,防止化盐过程中碱性出现大的波动,对精制反应及盐水质量造成影响;游离氯的控制日益引起关注,主要是化盐系统如果没有防腐,就要严格防止化盐水中的游离氯对设备管路的腐蚀,并造成盐水中铁离子浓度的升高。
2.2.4 化盐设备
(1)化盐设备。化盐的主要设备为化盐桶(见图2-6)。

图2-6 化盐桶结构图
化盐桶一般为钢制,采用钢制防腐、混凝土防腐,其结构见图2-6。化盐水通过底部进入,通过喷帽分布器均匀分布溶盐水,防止偏流。中间有折流挡板,上部有盐水溢流槽及铁栅。
原盐由上部持续加入储盐中心桶,一般保持盐层高度在2.5~3m以上。化盐水从化盐桶底部进入,与盐层逆流接触上升,一般保持化盐温度在55~65℃,化盐水停留时间不少于30min。
(2)化盐桶主要尺寸的确定
①直径
D=[4Q/(πq)]-2
式中 D——化盐桶的直径,m;
Q——化盐水的流量,m3/h;
q——生产强度,一般取8~12m3/(m2·h)。
设计时,q的取值尽可能小一点。它可以有效降低盐水上升速率,防止细小颗粒的盐带出桶外,保证盐水的饱和度,并可以延长化盐桶清理周期。
上述介绍的为地上桶式化盐法,如采用其他方式化盐,可先计算化盐设备的截面积,再根据总体平面布局要求确定化盐设备的尺寸。
式中 S——化盐设备的截面积,m2;
Q——化盐水的流量,m3/h;
q——生产强度,一般取8~12m3/(m2·h)。
②化盐桶的高度。原则上化盐桶高度取决于盐水达到饱和所需的盐层高度(当然与化盐桶直径相关),并必须考虑其清理周期内底部积存的盐泥高度,这需根据所用工业盐的品种来确定,一般取5m左右。
若采用地下化盐设备,可加大化盐设备的截面积,降低其高度,但取值原则上也不能低于3m。但化盐设备的截面积取值也不能太大,否则将影响化盐水及固体盐堆积的均匀性。采用低位化盐方法,从化盐设备出来的粗饱和盐水要进入后道工序时必须用泵来输送,而输送泵叶轮的高速旋转将会打碎盐水中已形成的杂质颗粒,从而影响后道工序盐水的澄清。当前氯碱工业技术进步较快,上述现象对后道工序的影响已不大。
若盐水处理采用自流工艺,宜采用地上化盐设备。为了考虑化盐设备溢流出来的盐水能自流进入澄清系统,可将化盐桶的基础高度适当提高。化盐桶的实际高度原则上取决于后水澄清设备的高度。一般化盐桶的出口高度比澄清设备的盐水进口高0.5~1.0m。
③化盐桶的设计。与生产能力及使用工业盐的品种等都有关联,还需注意以下几个方面。
a.底部要设置化盐水分布器。其结构形式多种多样,但最好在化盐水出口上方设置尖顶的“菌帽”,这样可以有效防止盐或杂质堵塞化盐水出口,又可防止盐层形成搭桥。一般采用多个带有“菌帽”装置的化盐水出口,沿化盐桶截面均匀分布。
b.中部应设置环形挡圈。它可以改变化盐水流体方向,防止化盐水走短路,影响盐水饱和度。挡圈一般与桶体成45°夹角,挡圈内径不宜过小,以免造成局部截面化盐水流速过大而将细小颗粒盐带出桶外,同时可防止盐层搭桥形成假盐层假象,影响盐水质量。挡圈的宽度一般取150~250㎜。
c.上部要设置盐水溢流槽及杂质拦截网。有些厂家使用一定直径的圆钢制成铁栅,这不合理,易造成盐水偏流,同时造成杂质清理困难。最好利用钢板上开孔,这样既能保证盐水均匀从四周溢流,不易造成盐水走短路现象,也便于清理化盐桶中的杂质。但要注意开孔率及均匀性,孔径一般在ϕ10mm左右。
d.设置中心桶。“精制盐”逐步为氯碱行业所接受,但因精制盐的颗粒极小,极易造成浮盐夹带到后道工序,一方面易造成盐水输送管道的堵塞,另一方面使未溶解的盐在澄清过程中随盐泥排出系统,造成盐消耗上升。因此,在化盐桶中上部应设置中心桶,这样就可有效解决浮盐夹带问题。中心桶的上部可设置扩口,以防止上盐时部分盐直接撒落在化盐桶的水面上。设置中心桶的原理是使干燥的“精制盐”先要经过一定距离的水层才能进入化盐水上升区,而此时细小颗粒的盐已充分浸湿,增加了盐的重度,从而不易形成浮盐,此种设计可适用于各盐种。