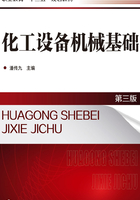
2.1 换热器
换热器是化工生产过程中主要的换热设备。在石油、化工生产中通常对流体加热或冷却,液体汽化或蒸气冷凝等过程都有热量交换,因而都需要换热器。换热器的种类很多,结构形式也各不相同,但它们通常都应尽量满足下列要求:工艺条件所规定的要求;具有较高的传热效率,换热器所用的材料传热性能要好,传热面积足够且流体阻力要小;具有足够的机械强度和刚度,整体结构可靠,节省材料;此外,还应便于制造、安装及维修。
目前,换热器的种类主要有两大类,一类是板式换热器,另一类是管式换热器。本节主要介绍最具代表性的列管式换热器。
2.1.1 列管式换热器的基本结构形式
列管式换热器是圆筒形的设备,主要由管箱、管板、壳体、换热管、折流板及附件等组成,如图2-1所示。这种换热器有许多排列整齐的管子,称为换热管。图2-1中B流体从管内流过,A流体从管外流过,由于两种流体存在温度差,于是它们通过管壁进行热量交换,简称传热。从管内流过的流体所经过的路程或空间称为管程,从管外(壳体内)流过的流体所经过的路程或空间称为壳程。管箱是收集或分配管程流体的部件,它通过法兰连接或焊接连接的方式,与管板连接在一起;换热管通常通过“胀接”(在力的作用下使管子膨胀而增大直径并紧紧压在管板的孔上,称为胀接)或焊接与管板连接在一起,是换热器中主要的换热元件;很多换热器还设置了折流板,折流板可以使换热管外的流体(即壳程流体)改变流向,发生湍流,增强传热效果,还对换热管具有支承作用,防止换热管发生较大挠性变形。

图2-1 列管式换热器的基本结构形式
1—壳体;2—支座;3—管板;4—管箱;5—换热管;6—折流板
2.1.2 列管式换热器的主要类型
由于管束、管板和壳体的结构和连接方式不同,列管式换热器又可分为固定管板式、浮头式、填料函式和U形管式四种。
2.1.2.1 固定管板式换热器
固定管板式换热器由换热管、管板和壳体组成。这类换热器的优点是结构紧凑、简单;在相同的壳径内分布的换热管数最多;更换或维修个别管子时不影响其他管子;管内清洗方便,但管外清洗较困难,因而壳程适宜通过清洁且不易结垢的流体。另外,管束两端的两块管板由管束支承,故列管式换热器管板最薄,造价也低,因而其得到较为广泛的应用。但是,这种换热器在管程与壳程换热介质的温度差较大时,换热管与壳体的温差也可能增大,使两者的热膨胀伸长量不同,从而会产生较大的“温差应力”(简单地说,应力是指材料内部单位面积上受到的材料相互之间的作用力,温差应力是由于温度改变而引起的应力)。改进的常用方法之一是在壳体上设置膨胀节,如图2-2所示。产生温差应力的原因分析和降低温差应力的方法如下。

图2-2 固定管板式换热器
(1)温差应力的产生
如图2-3所示,圆筒与管子在装配时的温度均为To,此时两者的长度均为L,如图2-3(a)所示。在操作时,设壳体壁内的平均温度为Ts,管壁内的平均温度为Tt,由于壳程、管程所流的介质温度不同,因而Ts与Tt不相等。当Tt>Ts时,则如图2-3(b)所示,管子自由膨胀量ΔLt比壳体自由膨胀量ΔLs大;事实上,圆筒和管子是通过管板固定在一起的,它们的伸长量必须相等,都为ΔL,如图2-3(c)所示。圆筒除了自由膨胀量ΔLs外还被拉长了(ΔL-Ls),而管子被压缩了(ΔLt-ΔL),这说明圆筒受到拉力作用,管子受到压力作用。当Tt<Ts时,圆筒与管子的受力正好相反。这种由于圆筒与管子之间的温度变化不同,导致它们之间变形不协调而存在的相互之间的作用力F,称为温差轴向力。圆筒(或管子)单位壁横截面上所受到的温差轴向力称为温差应力。

图2-3 管子与壳体的温差应力示意图
(2)温差应力的补偿
在工程实际中,温差应力的危害是不容忽视的。如果管壁、壳壁受拉伸和压缩的总应力超过了材料允许的应力,管子或壳体就会失效。管子是胀接或焊接在管板上的,如果管子所受的轴向力过大,会使管子从管板连接处拉脱。另外,温差应力过大,还会使管板发生翘曲,破坏管板密封处的密封性。因而必须对温差应力予以适当的补偿,从而减小(或消除)温差应力的危害。常采用的措施有以下两种。
①减小管束与壳体之间的膨胀差。因为管子和壳体的自由膨胀量与它们的材料和温度变化量有关,这就要求在进行设计和使用换热器时,尽量使它们的热膨胀系数和温度变化量相近,这样才能使它们在操作时膨胀量相近(或相等),以减小或消除温差应力。
②设置膨胀节。膨胀节是装在固定管板式换热器壳体上的构件(它在轴向容易变形),当管子和壳体壁温不同而产生膨胀差时,由于膨胀节的变形,使总变形量容易趋于协调一致,可以大大减小温差应力。
固定管板式换热器中采用的膨胀节主要有U形膨胀节、平板焊接式膨胀节及Ω形膨胀节,如图2-4所示。最常用的U形膨胀节允许采用两个半波零件焊接而成,其波壳可以是单层板结构,也可以是多层板结构。当要求更大补偿量时可用多波膨胀节,多波膨胀节可以为整体成形结构,也可以由几个单波元件组焊而成。平板焊接式膨胀节结构简单,制造方便,但它们的刚性较大,补偿能力小,不常用。Ω形膨胀节适用于直径大、压力高的换热器。

图2-4 膨胀节的结构形式
由于需要膨胀节的壁厚比较薄,厚了变形能力差,因而膨胀节不能承受较大压力。当壳程介质压力较大,或换热管与壳体温差过大时,则可以改用其他结构形式的列管式换热器来消除温差应力。例如,可采用浮头式、U形管式、填料函式换热器代替固定管板式换热器。
2.1.2.2 浮头式换热器
固定管板式换热器存在轴向温差应力的原因是圆筒和管束在两端都用管板固定连接起来了,要变形必须同时变形,管束不能自由浮动,而图2-5所示的浮头式换热器就改变了这种状况。这种换热器的一端管板通过法兰用螺栓固定,另一端可在壳体内自由移动,即所谓的“浮头”。这种结构使得管子和壳体在热膨胀时可自由伸长,相互不受影响,所以不会产生温差应力。浮头式换热器的管束可以从一端自由抽出,便于管外清洗。但是,它又产生了新的缺点,主要是结构较复杂,造价高,浮头处的密封要求较严,密封不严时会造成管内、外的流体相互混合,流体会从压力高的一边泄漏到压力低的一边,且泄漏量不大时不易觉察。

图2-5 浮头式换热器
2.1.2.3 填料函式换热器
填料函式换热器的结构如图2-6所示。“填料函”是一种专门用来密封的结构物,依靠塞进像绳子一样的柔软物并压紧来密封流体。这种换热器的结构与浮头式换热器的结构相似,只是浮头伸到了壳外,且浮头与壳体之间采用了填料函式密封,所以又可称为外浮头式换热器。这种换热器结构简单,加工制造方便,管束容易抽出进行检修、清洗。因而,这种换热器适用于管壳温差较大、介质不清洁或腐蚀严重、需经常清洗或更换管束的场合。但是,由于受到填料密封条件的限制,不宜用在直径较大、压力较高的场合,这是它的缺点。

图2-6 填料函式换热器
2.1.2.4 U形管式换热器
U形管式换热器的结构如图2-7所示。这种换热器只有一块管板,换热管被弯成U形,管子两端固定在同一块管板上。因此,管子在受热时可以自由膨胀,消除了温差应力。而且管束可以抽出来,因而管外清洗方便。由于省掉了一个管板和管箱,所以当管内压力较高时,可以节省许多材料。在这种情况下,U形管换热器的优点就比较突出。但由于管子被弯成U形,管内清洗困难,管子拆修更换不便。此外,管子弯曲时有一定的弯曲半径,使得管间距离较大,管板上布管数较少,结构不紧凑,管束中心部分存在空隙,减小了换热面积,而且管外流体容易走短路,影响传热效率。

图2-7 U形管式换热器
综上所述,固定管板式换热器适用于壳程介质清洁,不易结垢,管、壳温差比较小的场合;浮头式换热器适用于管、壳温差较大,介质不清洁,需经常清洗的场合;填料函式换热器适用于管、壳温差较大,介质不清洁或腐蚀严重,需经常清洗或更换管束的场合,由于受到填料密封条件的限制,不宜用在直径较大、壳程压力较高的场合;U形管式换热器适用于管、壳温差较大,管内走清洁介质且管内压力较高的场合。填料函式换热器的管程是单数管程,浮头式、U形管式换热器的管程是双数管程。
2.1.3 列管式换热器的组成元件及其连接
2.1.3.1 换热管
换热管是换热器的主要换热元件,主要通过管壁的内、外表面来进行传热。管子的直径、长度、数量和材料是影响换热管传热的几个因素。管子的直径、长度和数量是由换热器的换热面积决定的,采用小直径管子,换热器单位体积内的换热面积要大一些,设备紧凑,传热系数高,但制造麻烦,管内容易结垢,清洗不便,流体压力降大,多用于清洁的流体。大直径管子的管内清洗较方便,多用于黏性大或较污浊的流体。
换热管在管板上的排列有正六角形(或称正三角形)、正方形和同心圆三种,如图2-8所示。正六角形排列使用最多,其优点是在同样的管板面积上,排管数最多,但不易清洗管子的外表面。对于需要经常清洗管外的换热器可采用正方形排列,其优点是清刷管外方便,但排管数量比正六角形排列要少得多。同心圆排列在靠近壳体的地方布管均匀,在小直径的换热器中排管数较多,但制造中管板钻孔前划线麻烦。

图2-8 换热管在管板上的排列方式
2.1.3.2 管子与管板的连接
管子与管板的连接部位如果结合不紧密,往往会在此处引起泄漏。泄漏量小时,不易被发现,会造成一定的危害。因而,管子在管板上的连接是列管式换热器制造中的关键。常用的连接方法有胀接、焊接和胀焊结合等。
(1)胀接
胀接是利用胀管器挤压伸入管板孔中的管子的端部,使管端产生“塑性变形”,同时使管板产生“弹性变形”(解除外力以后,能够恢复原来形状和长度的变形是弹性变形,不能恢复原来状态的是塑性变形),这时管端直径增大而紧贴在管板孔壁上。取出胀管器,管板孔弹性收缩,使管板与管子间产生一定的挤压力而紧紧贴合在一起。这种方法劳动量较大,效率较低。用液压胀管和爆破胀管的方法使管子与管板连接牢固,是较新的制造技术。它具有生产效率高、劳动强度低、密封性能好等优点,现已得到广泛应用。
采用胀接时,换热管材料的硬度值一般需低于管板的硬度值。为提高连接强度和密封性,可在孔壁上开槽,以便胀管后管子发生塑性变形,管壁被嵌入小槽中,如图2-9所示。

图2-9 换热管的胀接结构
由于胀接主要是靠挤压来实现连接的,为防止温度过高产生“高温蠕变”(指在高温下随着时间的延长,材料缓慢地增加塑性变形的现象),使得胀接部位松脱,故其使用范围应限制在设计压力p≤4MPa,设计温度t≤300℃。
(2)焊接
管子与管板之间采用焊接,应用较为广泛。它连接可靠,具有良好的“气密性”(指密封住气体使其不漏的性能),承受压力的能力高,且在高温、高压下也能保证连接的紧密性和抗拉脱能力。为了保证焊接质量,管板孔边上应开斜口,称为焊接坡口。由于制造和检验技术的进步,近年来焊接连接使用得越来越多。焊接连接的主要缺点是管子与管板孔之间往往存在微小间隙,当壳程存在液体时易形成“缝隙腐蚀”(指因为缝隙中液体缺少流动使浓度逐步增加而造成的腐蚀);当管壁和管板厚度相差很大时,由于焊接后冷却速度不同会产生热应力。
(3)胀焊结合
单独采用胀接或焊接都有一定的局限性,当胀、焊结构不能满足要求时,可采用胀焊结合。胀焊结合有两种形式:一种是强度胀加密封焊,另一种是强度焊加密封胀。前者是胀接承受作用力,而密封则由焊接保证(焊接高度一般为1~2mm,不影响胀接强度);后者是焊接承受作用力,而胀接只消除间隙,防止发生泄漏和缝隙腐蚀。胀焊结合适用于密封要求高、承受振动、有缝隙腐蚀及采用复合钢板的场合。
2.1.3.3 管板与壳体的连接
管板与换热器壳体的连接方式与换热器的结构形式有关,固定管板式换热器的管板与壳体的连接采用不可拆连接,而浮头式、填料函式及U形管式换热器的管板与壳体的连接则采用可拆连接。
(1)不可拆连接结构
固定管板式换热器两端管板通常直接焊在壳体上,并兼作“法兰”(法兰是用于管道或化工设备上可以多次拆卸且起密封作用的连接构件,详见2.6.3),如图2-10所示。其中结构(a)采用的是角焊缝,壳体对中容易,施焊方便,但不易焊透,适用于壳程设计压力ps≤1MPa、物料危害不大的场合;结构(b)采用单面对接焊缝,焊接质量提高,但焊接时难以调整,适用于1MPa<ps≤4MPa的场合;结构(c)采用带衬环的单面对接焊缝,焊接质量高,适用于1MPa<ps≤4MPa的场合。

图2-10 兼作法兰的管板与壳体的连接
管板也可不兼作法兰,如图2-11所示。

图2-11 不兼作法兰的管板与壳体的连接
(2)可拆连接结构
浮头式、填料函式及U形管式换热器有一块管板是与壳体固定连接在一起的。为了能使管束从壳体中抽出进行清洗,将固定端管板做成可拆连接,即将管板夹于壳体法兰与管箱法兰之间,如图2-12所示。图2-12(a)所示为卸下管箱后就可把管板连同管束从壳体中抽出的结构。如使用中只需经常卸下管箱,不必抽出管束,则可采用图2-12(b)所示结构。

图2-12 管板与壳体的可拆连接结构
2.1.3.4 管箱、折流板、支持板及拉杆
管箱位于换热器的两端,其作用是使进入换热器中的管程流体均匀分布到各换热管中,或把管内的流体汇集一起送出。在多管程换热器中,管箱还起到分隔管程、改变流向的作用。
垂直于轴线方向安装的挡板称为横向折流板,它可以提高壳程内流体的流速,增加介质的湍流程度,提高传热效率;另外它还起到支承管束的作用。
常用的弓形折流板有单弓形、双弓形和三弓形三种,各种折流板的结构形式及流体的走向如图2-13所示。单弓形折流板[图2-13(a)]流体只经折流板的圆缺部分而垂直流过管束,结构简单,加工方便,应用较广泛。单弓形折流板一般应按等距离布置,其最小间距应不小于圆筒内径的1/5,且不小于50mm;其最大间距应不大于圆筒内径,且管束两端折流板尽可能靠近进、出口接管。
单弓形折流板在板间距较大时,液体绕到折流板后会在这里滞流,形成滞流死区,影响传热效果。为了消除滞流死区通常可采用双弓形和三弓形折流板[图2-13(b)、(c)]。

图2-13 折流板的结构形式及流体走向
折流板既起折流作用,又起支承作用。当工艺要求无折流板而管子又比较细长时,应考虑设置一定数量的支持板,防止管子产生较大变形。支持板的形状有弓形、双弓形和三弓形,其形状与弓形折流板相同。
在列管式换热器中,折流板和支持板的固定是通过拉杆和定距管来实现的。图2-14(a)所示结构适用于换热管外径大于或等于19mm的管束,此拉杆两端都带有螺纹,一端用螺纹拧入管板,折流板用定距管定位,最后一块折流板用两螺母固定。对于换热管外径小于或等于14mm的管束,可采用焊接结构,如图2-14(b)所示。拉杆一端插入管板中焊接,每块折流板均与拉杆点焊固定。

图2-14 拉杆在管板上的固定
2.1.3.5 壳程接管
壳程流体进、出口,对换热器的传热效率和换热管的使用寿命都有很大影响。尤其是流体进、出口速度较高或流体内夹杂有固体颗粒时,会对换热管产生剧烈冲刷。为了克服这一现象,可在进口处装有缓冲挡板和缓冲接管等。
(1)缓冲挡板
图2-15所示为平板形缓冲挡板。为了减小流体阻力,挡板与换热器内壁的距离h一般为接管直径的0.25~0.3,若距离太大会阻碍管子的排列。

图2-15 平板形缓冲挡板
(2)缓冲接管
图2-16所示为缓冲接管。它将接管在入口处加以扩大,做成喇叭口,以降低入口处的流速,起到缓冲作用。

图2-16 缓冲接管
(3)导流筒
图2-17所示为导流筒。在流体进管处加上一个圆筒,目的是将流体导至靠近管板处才进入管束间,消除了接管至管板段的滞流死区,更充分地利用了换热面积。

图2-17 导流筒
2.1.4 其他类型的换热器
在化工厂内遇到的换热问题是错综复杂的,为了适合各种换热要求,出现了多种形式的换热器。
(1)套管式换热器
套管式换热器由两种大小不同的管子组成同心圆套筒,内管与外管之间采用填料函式连接或焊接。根据换热的要求,可适当增减套筒的数目来组成换热器。每一段套筒称为一程,每程的内管依次与下一程的内管用U形短接管连接,而外管之间也用管子连接,如图2-18所示。这种换热器的程数可以根据所需传热面积来确定,一般都是上下排列固定于管架上。若所需的传热面积较大,可用数排并列,每排与总管相连。进行热量交换时,一种介质在管内流动,另一种介质在套管的环隙中流动,冷、热流体一般呈逆流流动。这种设备均由管子构成,所以能耐较高的压力,制造也方便,传热面易于增减;其主要缺点是金属消耗量大,占地面积大。所以,套管式换热器适用于高压、中或小流量、传热面积要求不大的场合。

图2-18 套管式换热器
(2)翅片管式换热器
翅片管式换热器的结构如图2-19所示。翅片管式换热器特点是换热管内、外有许多金属翅片,常见的翅片如图2-20所示。翅片的使用既增加了传热面积,又增强了介质流动时的湍流程度,增强了传热效率。国内对于翅片管的应用主要在空气冷却器(简称空冷器)中。

图2-19 翅片管式换热器

图2-20 常见的几种翅片形式
(3)螺旋板式换热器
螺旋板式换热器是由两块薄金属板位于中心的一块挡板上,并卷成螺旋形而构成的,因而在换热器内构成两条螺旋形通道,分别走冷、热两股流体,其结构如图2-21所示。这种换热器传热面是螺旋板面,因而传热面积较大,传热效率高,有自清洗作用,不易结垢。但由于板面承压性能差,因而它适用于压力不高的场合。

图2-21 螺旋板式换热器
阅读材料
高效性能换热管的开发
换热器的换热管结构一般为光滑管。为了强化传热过程,提高传热效率,一些科技工作者将光滑管进行了适当的改进。最初的改进主要是在管外,如在管外轧制各种形状的外翅片、车制螺纹或者在管外设置螺旋线等,这些措施不仅增大了冷、热流体的传热面积,增加了介质的湍流程度,而且可以减轻换热管的振动。随着换热器设计技术的发展,又先后研制出了内螺纹管、内翅片管以及带有内插件(如麻花片、螺旋线、螺旋片等)的换热管等;还有对管内外同时进行改进,研制出了横槽纹管(即在与管子轴线呈90°的方向上轧制槽纹,则在管内形成一圈圈突出圆环)、缩放管(它是由依次交替的收缩段和扩张段组成的波形管道)或者将上述改进管内外的方法进行组合而制成的各种异形管。这些高效换热管的运用,使传热系数提高到原来的1.25~10倍,因而可以减少传热过程中的换热器的尺寸或台数,降低投资。