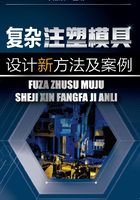
2.2 注塑件上的成型加工痕迹
注塑件在成型加工过程中,除了具有模具结构成型的痕迹之外,还具有成型加工的痕迹或称缺陷痕迹或弊病痕迹。缺陷痕迹有的是因注塑件设计不当而产生的;有的是因模具结构设计不当而产生的;有的是因浇注系统选择不当而产生的;有的是因加工工艺方法不当所产生的;有的是因加工参数选择不当而产生的;有的是因所用材料型号和质量及添加剂不当而产生的;有的是因前置处理或后处理不当而产生的;还可能因设备、加工环境等原因所产生。其中对模具影响最大的原因,是因注塑件设计、模具结构设计和浇注系统设计不当所产生的。因为在这种情况下是需要修改模具或推倒现有的模具结构方案,再重新进行模具的设计和制造才能消除这些缺陷痕迹。有时不仅要重新设计注塑模,甚至还要重新设计注塑件。如此,就要进行模具的修改或重新进行模具的设计和制造,这样必定会造成模具和产品生产时间的滞后和经济的损失,甚至失去市场的严重后果。对于非注塑件结构和模具结构及浇注系统所产生的缺陷痕迹,只要通过试模,找出缺陷产生的原因后加以改进塑料品种、质量、配方、工艺方法、加工参数、设备和加工环境等后便可消除。
2.2.1 流痕
流痕是指注塑件的表面上出现了一些大小不同突出的粗糙斑块,如图2-8 所示,流痕是料流温度和模具温度影响类型的缺陷。流痕主要是注塑件在成型过程中,塑料熔体遇冷形成的冷凝分子团在填充的过程中,散布在流程中并逐渐地增大而形成的。料流失稳流动和低温的薄膜前锋都是产生流痕的主要因素。此外塑料的流动性差;料粒不匀或料粒过大;料中混入杂质和不同品种的料;模具的温度低及喷嘴的温度低;模具无主浇道或主浇道过短;模具无冷料穴;喷嘴温度低,熔体的温度过低,塑料塑化不良;塑化不匀,注射速度低,成型时间短;注射机的容量接近注塑件的质量,注射机塑化能力不足也是产生流痕的原因。

图2-8 流痕
2.2.2 熔接痕
熔接痕也称为结合线,如图2-9所示,熔接痕属于温度影响类型的缺陷。塑料熔体分流汇合时的料温降低、树脂与附和物不相溶等原因导致在熔料分流汇合处产生不规则的熔接痕,即沿注塑件表面或内部产生了明显且细的接缝线。产生熔接痕的主要原因有物料内渗有不相溶的塑料与添加剂;使用脱模剂不当;存在不相溶的油质;使用了铝箔薄片状着色剂;脱模剂过多;熔料充气过多;塑料流动性差;纤维填料分布融合不良;模温低、模具冷却系统不当;浇口过多;模具内存在着水分和润滑剂,模具排气不良;塑料流动性差、冷却速度快;存在着冷凝料、料温低;注射速度慢、注射压力小;注塑件形状不良、壁厚太薄及壁厚不均匀; 嵌件温度低、嵌件过多、嵌件形状不良等。

图2-9 熔接痕
2.2.3 缩痕
注塑件表面上产生不规则的凹陷现象称为缩痕,也可称为塌坑、凹痕、凹陷和下陷等。缩痕如图2-10所示,是为因冷却收缩影响类型的缺陷。产生的主要原因:保压补塑不良;注塑件冷却不匀;加料不够、供料不足、余料不够;浇口位置不当、模温高或模温低、易出真空泡;流道和浇口太小、浇口数量不够;注射和保压时间短;熔料流动不良或溢料过多;料温高、冷却时间短、易出缩痕;注射压力小、注射速度慢;壁太厚或壁厚不匀引起收缩量不等及塑料收缩率过大等。

图2-10 缩痕
2.2.4 填充不足
塑料熔体填充不满型腔,使得注塑件残缺不全称为填充不足或缺料。填充不足如图2-11所示。填充不足属于缺料影响类型的缺陷。产生的主要原因是供料不足、熔料填充流动不良、充气过多及排气不良等。

图2-11 填充不足
2.2.5 银纹
银纹又可称为水迹痕或冷迹痕。由于料内的潮气或充气或挥发物过多;熔体受剪切作用过大;熔料与模具表面密合不良,或急速冷却或混入异料或分解变质,使注塑件表面沿料流方向出现银白色光泽的针状条纹或云母片状斑纹的现象称为银纹,如图2-12所示。产生银纹的原因有物料中含水分高,存在着低挥发物,物料中充有气体;配料不当、混入异料或不相溶料;浇道和浇口较小;熔料从注塑件薄壁处流入厚壁处;排气不良;模温高;模具型腔表面存在着水分,润滑油或脱模剂过多,模剂选用不当;模温低、注射压力小、注射速度低;塑料熔料温度太高;注射压力小等。

图2-12 银纹
2.2.6 裂纹
裂痕是指注塑件的表面和内部产生了细裂纹或开裂的现象,塑料件表面裂痕可以用眼睛观察到,内部裂痕可以通过气孔检测仪或X光机探测到。产生裂纹的主要原因是塑料性脆、混入异料或杂质;ABS塑料或耐冲击聚苯乙烯塑料易出现细裂痕;塑料收缩方向性过大或填料分布不均匀;脱模时顶出不良;料温太低或不均匀;浇口尺寸大及形式不当;冷却时间过长或冷却过快;嵌件未预热或预热不够或清洗不干净;成型条件不当、内应力过大;脱模剂使用不当;注塑件脱模之后或后处理之后冷却不均匀;注塑件翘曲变形、熔接不良;注塑件保管不良或与溶剂接触;注塑件壁薄、脱模斜度小、存在着尖角与缺口等。
2.2.7 喷射痕
塑料熔体高速注射时,在浇口处出现回形状的波纹称为喷射痕,如图2-13所示。产生喷射痕的主要原因有塑料熔体注射速度高;螺杆转速高;注塑机背压高;成型加工循环周期长,喷嘴有滴垂现象;塑料含有水分,模腔内渗有水或挥发物;料筒和喷嘴温度低;料温低、模温低;浇口截面小、浇口位置不当、无冷料穴或冷料穴位置不当、设置排气孔等。

图2-13 喷射痕
2.2.8 波纹
波纹是指注塑件的表面上存在着像水波纹的细线,这种波纹的细线称为波纹,如图2-14所示。主要是由于熔料沿着模具表面不是平滑地流动填充型腔,而是呈半固态的波动状态沿着型腔表面流动或熔料流动存在着滞流的现象。产生的主要原因有塑料流动性差、供料不足、料温低;冷料穴设置不当、存在着冷料;模具冷却系统不当;浇注系统流程长、截面小、浇口尺寸小及其形式和位置不当;流动曲折、狭窄和粗糙度大;模温低和喷嘴温度低;注射压力小、注射速度慢;注塑件壁薄、面积大、形状复杂等。

图2-14 波纹
2.2.9 翘曲(变形)
翘曲(变形)是指注塑件发生了形状的畸变、翘曲不平或型孔偏斜、壁厚不均匀等现象。变形如图2-15所示。

图2-15 变形
产生翘曲主要原因是塑料塑化不均匀、供料填充不足或过量、纤维填料分布不均匀;模温高;浇口部分填充作用过分、模温低;模具强度不良;模具精度不良、定位不可靠或磨损;浇口位置不当、熔料直接冲击型芯或型芯两侧受力不均匀;喷嘴孔径及浇口尺寸过小;注塑件冷却不均匀、冷却时间不够;料温低;注射压力高、注射速度高;冷却时间短;脱模时注塑件受力不均匀、脱模后冷却不当;注塑件后处理不良、保存不良;注射压力小、注射速度快;保压补塑不足;料温高;保压补塑过大、注射压力过大;料温不均匀;注塑件壁厚不均匀、强度不足;注塑件形状不良;嵌件分布不当及预热不良等。
2.2.10 变色
注塑件局部的颜色发生了变化称为变色(泛白也是变色),如图2-16所示。产生的主要原因是注塑件局部温度相差太大;塑料未充分干燥,螺杆内残留其他塑料或杂物、料温高、塑料停留在料筒的时间长;模具局部存在着气体,浇道和浇口的截面较小和模温过高;注射压力高、注射时间长、螺杆回转速高和背压高、喷嘴温度高、循环周期长等。

图2-16 泛白与变色
2.2.11 过热痕
过热痕指在注塑件成型温度产生热分解或料中存在可燃性挥发物、空气或塑料颗粒经反复预热,塑料在高温高压下分解燃烧使注塑件表面或整体呈现碳状烧伤的现象,如图2-17所示。出现过热的注塑件脆性、强度和刚度降低而无法正常使用。产生的主要原因是水敏感性塑料干燥不良;喷涂润滑剂过量、可燃性挥发物过多;含有过量的细小颗粒或粉末;再生料的比例过高;塑料粒中存在着碎屑卡入柱塞及料筒之间的间隙;喷嘴及模具的死角存有储料或料筒清洗不干净;染色不匀,存在着深色的塑料,色母变质;模具的排气不良;模具的浇注系统设计不合理;模具型腔表面不洁,存在可燃性的挥发物;熔体温度过高;注射压力过大、螺杆的转速过高;模具的锁模力太大;背压过小;加料量少;注射机的柱塞或螺杆及喷嘴磨损等。

图2-17 过热痕
2.2.12 气泡
气泡是熔体内充气过多或排气不良,导致注塑件内残留气体,形成的体积较小或成串的空穴称为气泡,如图2-18所示。产生气泡主要原因是塑料含有水分、溶剂或易挥发物;料温高、加热时间长、塑料降聚分解、料粒太细和不匀;注塑件结构不良,模具型腔内含有水分和油脂,或脱模剂使用不当;模温低、模具排气不良;流道不良有储气死角;注射压力小;注射速度太快、背压小,柱塞或螺杆退回过早;料筒近料斗端温度高、加料端混入空气或回流翻料、喷嘴直径过小和无衬垫等。

图2-18 气泡
注塑件上成型加工的痕迹,通俗讲就是注塑件上的缺陷或弊病痕迹,是不允许存留的。注塑件成型加工的工艺人员与这些缺陷痕迹的博弈,就是他们工作内容的全部,可以这么说工艺人员的工作就是与注塑件缺陷进行斗争。其艰难的程度绝不亚于注塑模结构的设计,甚至远超出了注塑模结构的设计和制造。注塑件上的缺陷若得不到有效的根治,注塑件就是不合格的,注塑模也被视为是不合格的。究其原因与注塑件上成型加工痕迹与注塑件结构设计、注塑件的材料、注塑件的工艺路线的制订、注射设备的选用、注塑工艺参数的选取、注塑模具结构的设计和注塑模温控与浇注系统的设计有关,甚至与注塑生产的环境有关。影响注塑件上的成型加工痕迹的因素有很多,导致注塑件产生缺陷的原因也很复杂,相应地整治起来也就比较麻烦了。
要想全面地整治所有注塑件上的缺陷,应该对所有的缺陷作出正确的定义,给出各种缺陷痕迹的照片,并附有各种缺陷痕迹形成的原因和根治缺陷的措施及整治效果的文件。这就是注塑件缺陷痕迹与整治技术规范文件或者是缺陷整治行业的标准。有了这种文件对注塑成型加工质量的提高会产生实际而深远的影响,还可以更进一步提高我国注塑成型加工的水平和产生重大的经济性效果。时至今日,还没有一个权威性的注塑件缺陷整治行业性标准,这是导致注塑件缺陷整治混乱的根源。随着我国注塑工艺水平的提高和注塑产量的迅速增加,制订注塑件缺陷整治行业性标准是势在必行的事情了,希望有关部门尽早出台这个行业性标准。