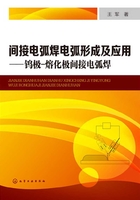
第二节 国内外研究现状
一、铜在钢表面堆焊研究现状
国内外研究学者对在钢表面堆焊铜合金进行了大量的研究[10,11],发现在熔覆过程中控制熔覆金属的铁含量是重要的研究目标,对堆焊中母材熔化进行控制,可以避免Fe-Cu液态分离而产生的偏析现象。
王克鸿等人[7-9]采用感应熔覆、炉中熔覆和熔铸熔覆的方法实现了在钢基体表面熔覆铜层。熔覆铜层与钢基体实现了冶金结合,界面结合良好,平整光洁,无夹渣、气孔、未熔合等缺陷,钢基体表面平直未发生熔化,获得了良好的界面结合性能,界面结合强度大于铜熔覆层强度,检测表明含铁扩散层在铜熔覆层一侧,其宽度仅为20~30μm。
任振安等人[12]采用激光加工方法在45钢基体表面熔覆铜合金,试验研究了激光加工工艺参数(激光功率、扫描速度)对铜基合金熔覆层的成分和组织、熔覆层摩擦磨损性能的影响规律。研究发现,随着激光功率的增加或扫描速度的下降,母材吸收能量增多,使得母材大量熔化,较多的Fe元素进入堆焊熔池中,与熔池中的Cu呈液相分离状态,Fe在上浮过程中与熔池中的Si元素发生反应生成Fe3Si,而反应剩余的Fe将继续上浮,生成球形ε-Fe颗粒。
单际国等人[13]利用Cu与Fe具有液相分离特性,以及母材与堆焊材料的冶金反应,采用聚焦光束堆焊获得了α-Cu基体上弥散分布Fe3Si花形树枝晶的铜基合金复合堆焊层,研究了堆焊层的物相组成和微观组织特征。试验结果表明,聚焦光束输入能量使预涂于试样表面的堆焊粉末迅速熔化,同时部分热能传递至母材,与预涂粉末接触的母材只发生少量熔化。
吕世雄等人提出了冷体热丝TIG微熔堆焊工艺[14-16],有效地提高了熔敷率,降低了稀释率。建立了电弧热丝模型,系统分析了热丝电流、送丝速度对预热温度的影响,分析结果与试验数值吻合良好。研究了堆焊工艺对堆焊层硬度、摩擦磨损性能的影响规律。考察了堆焊工艺对堆焊层剪切、拉伸及冲击韧性的影响,确定了获得良好综合性能堆焊层的最佳堆焊工艺。
当前在钢表面熔覆铜研究中,研究人员所采用的方法,使得在熔覆过程中,铜合金熔敷率大,而铁基体金属熔化量小,从而抑制偏析现象的发生。
二、堆焊方法研究现状
堆焊是指利用热源把金属熔化,堆在工具或机器零件上的焊接方法。堆焊通常用来修复磨损的工件。国内外学者对堆焊进行了大量的研究。堆焊主要包括氧乙炔火焰堆焊、电弧堆焊、电渣堆焊、等离子堆焊和激光堆焊等。堆焊重要的评价指标是如何控制稀释率。
1.氧乙炔火焰堆焊
氧乙炔火焰堆焊是指采用氧乙炔火焰作为热源,加热堆焊母材及熔覆合金,在工件表面进行堆焊的方法。该方法成本低,设备简单,适应性广。如碳化钨条火焰堆焊[17]就是依靠氧乙炔焰加热和熔化被堆焊金属表面及碳化钨条钢质套管,并在母材表面形成复合陶瓷堆焊层,显著提高了基体的耐磨性能。刘朔峰等人[18]在16Mn钢表面氧乙炔火焰堆焊自熔性铁基及镍基合金粉末得到铁基合金堆焊层和镍基合金堆焊层,并对两种堆焊层进行了显微组织、组成相、硬度和耐磨性以及抗热疲劳性能的比较研究。结果表明,两种堆焊层组织都具有枝晶生长特征,枝晶间存在着共晶组织,两种涂层均由γ-Ni固溶体和多种共晶化合物相组成,但镍基合金堆焊层的枝晶比较细小。镍基合金堆焊层比铁基合金堆焊层具有更高的硬度和耐磨性,同时也具有较好的抗热疲劳性能。
2.电弧堆焊
董巍等人[19]为了控制直流TIG电弧粉末堆焊层的稀释率获得Ni、Al含量较高的涂层,研究了堆焊规范对堆焊层的形状、稀释率和化学成分的影响规律,并从降低母材温度的角度出发,考察了辅助冷源对堆焊层稀释率的影响。结果表明,随着堆焊规范的减弱,堆焊层的熔宽和熔深减小、堆高增加,堆焊层的稀释率由70%降低到32%,有利于获得低稀释率的堆焊层。采用辅助冷源对母材进行冷却,使堆焊层的堆高增大、熔深减小、稀释率降低到21%。
王元良等人[20]采用双丝单弧填丝焊,在单丝焊基础上同时插入另一焊丝到熔池,插入焊丝接电源的连接工件一端起分流作用,以预热焊丝和形成推弧力。这种焊接方法生产效率可提高一倍以上,节约电能一半以上,可以达到提高焊接速度、减少变形、减小过热和热影响区宽度的目的,还可通过焊丝掺合金。
3.电渣堆焊
电渣带极堆焊是一种靠熔融的焊渣产生电阻热,不断地熔化焊带和母材形成堆焊接头的过程,焊剂从单侧送进,有强烈可见光。电渣带极堆焊具有采用大电流低电弧电压、焊接速度快、生产效率高、焊剂的消耗低、焊道表面成形更美观等特点。
李晓清等人[21]在2.25Cr-1Mo-0.25V钢上进行90mm不锈钢电渣带极堆焊工艺试验研究。研究结果表明,宽带极电渣堆焊磁场对焊道成形影响很大,外加磁场的控制很重要,通过工艺试验调整,达到三种磁场的平衡,获得了平滑美观的焊道成形。堆焊层各项技术性能满足石油化工容器堆焊制造技术要求。电渣带极堆焊的焊道成形比埋弧堆焊好,生产效率比埋弧堆焊高。
4.等离子堆焊
等离子堆焊[22]是采用等离子热源熔化堆焊金属及母材形成堆焊接头的焊接方法。等离子堆焊作为材料表面强化技术之一,能堆焊各种合金粉末材料,能得到致密的低稀释率的堆焊层,具有生产效率高、合金材料消耗少、成本低等许多优点。
董丽虹等人[23]针对工程应用中常见的磨损失效,进行了粉末等离子弧堆焊枪体设计研究。该堆焊枪喷嘴下端面设计为分体式结构,通过螺纹连接一个可拆卸的配件;采用双喷嘴式结构,输送堆焊用合金粉末;枪体内设计了良好的水冷通道,保证堆焊时各部件得到充分冷却。堆焊枪工艺性能试验结果表明,该焊枪稀释率约10%,粉末沉积率>95%,焊接质量优良。
斯松华等人[24]在16Mn钢表面等离子堆焊自熔性铁基合金层(Fe55)、镍基合金层(Ni60)以及镍基WC合金(NiWC25)。结果表明,合金堆焊层的显微组织均为γ固溶体,基体上分布着多种复杂的化合物相,如Fe23(C,B)6、(Cr,Fe)7C3、Cr7C3、NiB等。NiWC25堆焊层具有最高的硬度和耐磨性;合金堆焊层在稀H2SO4溶液和稀NaOH溶液介质中的耐磨性与在中性水中相比都有所降低,在酸性介质中降低更加明显。
5.激光堆焊
激光堆焊[25,26]是以激光为热源进行堆焊的方法。激光堆焊技术的特点[27]是可以实现热输入的准确控制,焊接速度高,冷却速度快,热畸变小,厚度、成分和稀释率可控性好,可以获得组织致密、性能优越的堆焊层,可以实现在普通材料上覆盖高性能(耐磨、耐高温、耐蚀)堆焊层,达到节省高性能材料的目的。
骆芳等人[28]在45钢的基体上,选用不同的激光功率、扫描速度、送丝速度等,用专用焊丝进行堆焊处理。结果表明,当速度不变时,激光功率增加,其热影响区变大,组织由细变粗,硬度减小;当其他条件不变时,随着扫描速度的增加,堆焊层的稀释率下降,硬度增加;随着送丝速度的增加,堆焊层的组织均匀分布,硬度先增加后下降。
综上所述,控制堆焊接头的稀释率是堆焊研究领域重要的研究目标。合理控制母材的熔化量是保证堆焊合金低稀释率的先决条件。堆焊方法和工艺参数是影响稀释率的重要因素。按单层稀释率由小到大的顺序各种堆焊方法排序:氧乙炔火焰堆焊、等离子弧堆焊、钨极氩弧堆焊、手工电弧堆焊、埋弧堆焊。一般地,埋弧堆焊虽稀释率偏大,但其堆焊效率较高,其单层堆高可达3~5mm。钨极氩弧单层堆焊稀释率可控制在10%~20%,但堆高偏小,必须堆焊2~3层方能达到3mm的有效堆高。用于堆焊的等离子弧堆焊技术有两种,粉末等离子弧堆焊单层有效堆高可达2mm,稀释率5%~30%;送丝等离子弧单层堆焊稀释率可控制在5%~15%,但一般需堆焊2层以上方能保证3mm以上的有效堆高[29]。
三、控制工件热输入电弧焊方法的研究现状
当前,电弧焊因其高效、低成本等因素,仍是堆焊领域重要的焊接方法。许多学者在降低工件母材的热输入量方面作了大量的研究。
1.串联双丝埋弧焊
1954年,D.E.Knight提出工件不接电源,电弧在双焊丝之间稳定燃烧,进行埋弧焊的方法,如图1-1所示。这种工艺焊接时更多的热量用来熔化焊丝,只有很少一部分进入工件,其熔敷速度高。研究指出[30]:焊接电流越大,则熔深越大;两焊丝与工件之间的距离越大,熔深则越小;两焊丝平面垂直堆焊方向可在熔深和稀释率较小的情况下获得熔宽较大的焊缝,两焊丝平面平行堆焊方向还可用于厚度较薄的板材。

图1-1 串联双丝埋弧焊[30]
何德孚等人[30]通过改变焊丝排列方式和焊丝间距,使焊缝成形、熔深、熔宽、稀释率可得到更充分的调节。该方法既可适用于稀释率要求较低的耐磨或耐腐蚀表面的埋弧堆焊,亦可适用于各种对接、角接焊缝的单道或多道高速埋弧焊。
2.双丝间接电弧气体保护焊
双丝间接电弧气体保护焊[31]工件仍不接电源,电弧在两焊丝端部燃烧,主要利用熔滴携带热量和少量弧柱热量熔化母材形成焊缝,如图1-2所示。邹增大等人对电弧稳定燃烧的条件、焊接工艺性、电弧形态及熔滴过渡都进行了研究。

图1-2 双丝间接电弧焊[31]
结果表明,随着焊丝伸出长度的增加,焊接电流减小;双丝间接电弧气体保护焊负极焊丝的熔化速度随着焊接电流的增加而明显增大,正极焊丝的熔化速度随焊接电流的增加而缓慢增大,两者均随着电弧电压的增加而减小[32]。双丝间接电弧气体保护焊在两焊丝端部形成电弧,焊接电流、电弧电压对电弧形态产生较大的影响,随焊接电流的变化,电弧形态会发生不同程度的集中与分散的变化;电弧电压越大,电弧越明亮,电弧的形体也越大。燃烧过程中电弧电压随时间而周期性变化,相应的电弧形态也随着时间发生周期性变化[33]。双丝间接电弧焊焊接电流与电弧电压的不同匹配选择,使得熔滴具有短路过渡、大滴过渡、混合过渡、射滴过渡、射流过渡等不同过渡形式。随着焊接电流的增大,熔滴尺寸减小,熔滴细化;随电弧电压的增大,熔滴尺寸减小[34,35]。
3.双电极焊条单弧焊
双电极焊条单弧焊[36-39]是焊接时双电极焊条的两焊芯用特制的焊钳夹持,分别接电源的正、负两极,工件不接电源,如图1-3所示。电弧在双电极焊条相互绝缘的两个焊芯端部形成,电弧可在离工件不同距离的空间进行引弧和燃烧,两极性斑点分别在两焊芯上。主要利用弧柱热量和熔滴携带热量熔化母材,改变了被焊工件的热循环。

图1-3 双电极焊条单弧焊[41]
经研究发现,双电极焊条单弧焊具有上升的电弧静特性,静特性曲线随两焊芯间距的增大而上移;在两焊芯间距合适的情况下,双电极焊条阴、阳极熔化速度可以保持一致,故双电极焊条单弧焊可使用交、直流电源,其熔化速度比单芯焊条的大,并且随焊接电流的增大和两焊芯间距的减小熔化速度增大。
通过对电弧形态的研究发现[40],双电极钛钙型碳钢焊条电弧的形态与传统工件接电源的焊接电弧形态有较大差别,按电弧的集中程度可以分为集中型电弧和分散型电弧两种形态,电弧燃烧过程中两种形态的电弧又有不同程度的变化。燃烧过程中电弧形态随时间发生周期性的变化,相应的电弧电压也是周期性变化的。
研究了双电极焊条的熔滴过渡[42,43],发现电弧对药皮的加热易于使焊芯两边药皮产生滞熔,形成两边尖中间凹的套筒形状,从而有利于熔滴以渣壁过渡形式过渡。钛钙型双电极碳钢焊条和不锈钢焊条具有渣壁过渡、喷射过渡和爆炸过渡等多种过渡形式,以细熔滴渣壁过渡为主;而石墨型堆焊焊条主要以粗熔滴渣壁过渡为主。
韩彬等人还通过测量双电极焊条的动态温升等试验方法研究了双电极焊条单弧焊中双电极焊条的加热和熔化。研究结果表明[44],双电极焊条的熔化系数随焊接电流的增大、药皮重量系数和焊芯间距的减小而增大,是单芯焊条的2~3倍。加热和熔化双电极焊条的能量有焦耳效应产生的电阻热、电弧通过熔滴传给焊条端部的电弧热,焊条的熔化主要依靠电弧的热量。双电极焊条两焊芯熔化的一致性受焊条类型、焊接电流等因素的影响。双电极焊条两焊芯熔化一致的充分条件为U阳极等于U阴极,两者差值越大则焊芯熔化不一致程度越大[45]。双电极焊条单弧焊电弧对两焊芯的熔化存在自调节作用,即电弧燃烧过程中两焊芯端部在电弧中的长度不等,两焊芯仍能保持等速熔化,使电弧燃烧过程能够稳定进行。研究人员还利用双电极电弧焊进行了许多工艺试验,如奥氏体不锈钢的焊接。结果表明该工艺具有高效节能、焊缝成形好、热影响区窄的特点[46,47]。
4.MIG-IEA焊
为了合理分配焊丝和母材的热输入,2002年墨西哥的Garcia等人提出MIGIEA[48,49]焊接。该方法电弧产生于焊丝和工件表面的覆板之间,射流过渡的熔滴形成,使高温液体瞬时大量填入工件的坡口中,如图1-4所示。该方法能够有效降低母材的熔化量。

图1-4 熔化极间接电弧焊[48]
对12.5mm厚铝合金厚板进行MIG-IEA焊接时[50],只在工件的上半部分加工了单V形坡口,热分析显示因为热损耗的减少使焊接的热效率增加。MIG-IEA焊与普通MIG焊相比,其焊缝的熔深比较大。MIG-IEA焊不仅能够焊接铝合金,而且还能够焊接铝基复合材料[51]。通过与埋弧焊、MIG焊的比较,研究了不同的焊接方法在X65焊缝时的抗腐蚀性能[52],发现MIG-IEA焊缝表现最好。MIG-IEA焊缝良好的抗腐蚀性是由于其微观组织从针状形变成了更为细小的组织。Garcia等人还采用焊前预热的方法改进了MIG-IEA焊接[53]。使用ER-4043焊丝同样焊接12.7mm厚的6061-T6铝合金板材,获得了全熔透焊缝。
5.双电极-熔化极惰性气体保护焊
双电极-熔化极惰性气体保护焊工艺是将一个TIG焊枪与一个MIG焊枪相组合,TIG焊枪与MIG焊枪构成旁路,MIG焊枪与工件构成主路,作用于焊丝上的电流数值较高,有利于提高焊丝的熔化速度,从而提高熔敷效率,适合焊接厚度较大的铝合金,如图1-5所示。TIG焊枪构成的旁路,分流了一部分通过焊丝的焊接电流,在保证了熔敷效率的同时,减小了作用于母材的热输入。

图1-5 双电极-熔化极气体保护焊工作原理示意图[57]
为了使主电流值可控,K.H.Li等人[54]在旁路回路中加入了一组电阻器,通过改变电阻器的组合来改变旁路电流,从而能够改变主电流的数值。他们还对DEGMAW焊接熔滴过渡机制进行了研究[55,56],通过调节电流获得射流过渡的临界电流。试验证实其临界过渡电流与GMAW焊接相比下降了。通过对各种电弧力的比较和分析发现旁路电弧不仅能提供电流,而且能增加阳极的电弧导电区的角度,从而进一步增加电磁收缩力,使熔滴过渡更加容易。非对称的电弧电磁收缩力还能作用弧根,对熔滴产生脱离作用。
Y.M.Zhang等人采用图像处理的方法对DE-GMAW焊接过程中的熔滴过渡进行了自动监测研究[58]。研究改进了原有的GMAW熔滴过渡图像处理方法,建立了以灰度为基的几何图像处理方法来自动监测焊接过程中熔滴位置及尺寸。通过改进,引入了相邻图片的关联度,从而提高了监测精度。
C.S.Wu通过研究找出了合理匹配的工艺参数,并利用有限元对焊接温度场和应力场进行分析,对焊缝尺寸进行预测[59],如图1-6所示。结果表明该方法降低了射流过渡的临界电流值,实现小电流高速焊接;有限元计算得出焊接条件和夹持条件相同的情况下,减小了焊接工件的挠曲变形和横向收缩变形;通过对焊接温度场的数值模拟,确定了焊缝横断面尺寸。

图1-6 焊缝横截面比较
Y.M.Zhang等人[60,61]还将旁路中的TIG焊枪改为熔化极焊枪,建立了熔化极DE-GMAW焊接系统,并将其利用在焊接高强钢上。通过对焊缝热影响区的研究,得出采用该方法焊接能够降低工件母材热输入,并获得小的热影响区和浅的熔深。
6.双旁路熔化极惰性气体保护焊
Y.Shi等人[62]提出了双旁路熔化极惰性气体保护焊,如图1-7所示。通过在传统的熔化极气体保护焊中加入两支钨极焊枪,降低了进入工件基体金属的电流,从而达到增加焊缝熔敷率的目的。研究发现旁路电弧能够促进熔滴过渡,降低临界过渡电流。

图1-7 双旁路熔化极氩弧焊熔滴过渡
综上,通过改变电极数量及排布方式,能够控制工件母材热输入量,降低焊缝的稀释率。本研究试图提出一种钨极-熔化极间接电弧焊方法,其特点是工件不接电源,使电弧在钨极和熔化极之间燃烧,在保证电弧稳定燃烧、熔滴持续过渡的情况下,达到降低工件热输入量、减小焊缝稀释率和提高熔覆效率的目的。
四、电弧行为研究现状
电弧行为研究是电弧焊研究中重要研究内容,主要包括电弧电特性、电弧几何特性、熔化特性及在熔化极焊接中的熔滴过渡特性等研究。这些特性是合理解释电弧形成并稳定燃烧、熔滴持续过渡的理论基础,并可为优化焊接工艺提供理论指导。
1.电弧电特性研究现状
电弧电特性是指电弧在导电方面表现出的一些特征,其中电弧在燃烧过程中电弧电流、电弧电压随时间的变化以及在燃烧过程中电流和电压之间的关系是重要的研究方面。电弧电特性的研究与电弧几何特性、熔化特性彼此之间有着重要的联系。在钨极-熔化极间接电弧焊中,研究其电特性,可以为工艺参数的正确选择提供理论依据,并可为进一步研究间接电弧形态及熔滴过渡行为奠定试验基础,对于了解和分析电弧燃烧的稳定性具有十分重要的意义。
许多学者对电弧电特性作了大量的研究[63],工作多集中在电流和电压的变化规律方面,如高洪明等人[64]对熔化极等离子弧焊焊接电弧信号进行了分析,结论表明该焊接方法电流电压与常规熔化极气体保护焊相比波动较小,韩永全等人[65]研究了铝合金变极性等离子弧的电特性,结果表明由于电极极性发生周期性变化,其电弧电压也随之发生改变,钨极为负时的电弧电压要比钨极为正时的电弧电压低。这些都说明电弧发生变化时,电弧电特性也会发生相应的变化。每种电弧焊接方法在研究电弧行为时都会对焊接电流和电弧电压的变化进行研究[66-68],以此作为研究其他电弧特性和进行工艺优化的试验基础。
J.Wang研究了复合脉冲小电流钨极氩弧焊时的电弧电特性[69],如图1-8所示。通过对采集到的电流和电压进行滤波,采用平均值绘制U-I图的方法描述了复合电弧的动态特性。结果表明,高复合脉冲的电弧电压与电阻大于低复合脉冲,此现象在基值电流期间尤其突出。U-I动特性图也表现为一个滞后环,分析可能是由于在脉冲期间电弧的热惯性造成的。通过比较得知,低复合脉冲的滞后环大于高复合脉冲。随着脉冲频率和脉冲时间的增加,滞后环会收缩,这说明高复合脉冲电弧的热惯性更大。

图1-8 小电流钨极氩弧焊电弧电特性
Praveen等人研究了脉冲MIG焊中熔滴过渡一脉一滴时的电弧电压和焊接电流随时间的变化[70],如图1-9所示。试验发现随熔滴过渡,焊接电流与电弧电压呈现规律的脉冲结构。研究得出,可通过对电流电压波形的监测来间接控制熔滴的过渡。在熔滴过渡过程中,电弧电压波动明显,又由于有焊接电源内部的自感应效果,使得电流的波动不明显。由于颈缩,熔滴在脱离焊丝前焊接电压会出现陡升。熔滴过渡后会使电弧电压出现陡降的现象,这是因为熔滴与焊丝接触的固液界面发生了变化,致使弧长发生改变。在熔滴进入电弧空间后,电弧电压又保持稳定。

图1-9 脉冲MIG焊电弧电压与焊接电流波形
2.电弧形态研究现状
很多学者作了大量有关从磁场、脉冲电流、外部环境压力、气体成分、焊接材料的表面状态对电弧形态的试验和理论研究。陈树君等人[71]研究了不同磁场条件下,焊接电弧中带电粒子的漂移旋转运动,研究了磁场方向和磁感应强度对旋转电弧和旋转半径的影响,发现磁场强度越强其电弧旋转速度越快,并由此可以改变焊接电弧的形貌。赵家瑞[72,73]提出脉冲电流频率达到5~20kHz时,焊接电弧直径随频率的增加而减小;根据电磁学理论,解释了高频脉冲电流导致的高频压缩效应。王中辉等人[74]研究了环境压力对焊接电弧形态、稳定性、电弧电压特性、电弧电流密度、电弧温度及电弧效率的影响规律,得出了随着环境压力的增加,弧柱压降及电流密度均增加、电弧更加明亮的结论;根据对电弧行为的研究,还开发了水下高压干式焊接方法[75]。李明利等人[76]发现应用大电流TIG氩-氦混合气体保护焊,随着氦气体积、流量分数的增大,电弧逐步收缩,逐渐由典型的“钟罩”形态向“扇子”形态变化,电弧颜色逐渐由白亮向橘色过渡,同时电弧的稳定性也开始变差。于治水等人[77]通过研究发现镀锌钢板对焊接电弧形态的影响很大,由于锌的蒸发导致电弧直径增大,并根据轴对称电弧空间热流的高斯分布可知镀锌钢板表面单位面积吸收热量减少,热流密度峰值降低。这都说明电弧形态的影响因素很多且非常复杂,对焊接的稳定性和质量也至关重要。对电弧形态的研究能为继续研究熔滴的受力情况以及过渡机制奠定基础,并能深入分析电弧的稳定机制,还可为新电弧焊接方法的提出提供重要的试验依据。
对电弧形态进行研究主要包括电弧形态的研究方法、各种因素对电弧形态的影响以及各种焊接方法的电弧形态研究。
除了传统的高速摄像法[78],近年来又出现了一种热成像法来研究电弧形态,如图1-10所示。

图1-10 热成像摄像机拍摄的电弧形态
Dudek等人[79]认为采用试错法来选择工艺参数既费时,成本又高。他们提出采用高分辨率热成像照相机来检测电弧形态和温度,这样在等离子喷涂过程中就能在线监控工艺质量。其流程为:采集电弧数码图片;对图片进行初始化并滤波;标定热成像照相机;定位阳极最高稳定点,测量几何参数;显示电弧及温度的图像。Dudek等人利用这种方法在线检测了使用等离子重熔法在40Cr4钢表面熔覆TiO2过程中的电弧形态及温度。
Q.Li等人[80]对活化剂焊接中活化剂对电弧形态的影响进行了研究,如图1-11所示。通过试验发现当采用SiO2活化剂时,焊枪向前移动进行焊接,电弧发生偏移,即与工件相接触的电弧滞后于向前移动的焊枪。电流越小,偏移越大。当焊接电流低于80A时,偏离最大。在此情形下,电弧被拉得越来越长,在工件表面出现阳极斑点的跳跃。但如果采用TiO2活化剂,则电弧没有偏移现象。

图1-11 活化剂对电弧形态的影响[80]
Perry等人采用TIG焊对钛合金实施焊接,也研究了活化剂对电弧形态的影响,如图1-12所示。

图1-12 TIG和A-TIG表面与热输入的比[81]
试验发现,加入活化剂可明显增加电弧的亮度,说明活化剂的加入改善了电弧中的电子分布。分析其原因,在工件表面电弧周围,活化剂中氟化物与钛板发生反应形成TiFn,该反应物熔点极高,在阳极区能够与大量电子复合,从而对电弧起到压缩作用,即提高了电流的密度,使电弧在有活化剂的情况下亮度更高。
Hidetoshi等人在日本的微重力中心比较研究了重力和微重力情况下的电弧形态[82]。结果表明,当焊接电流大于60A时,电弧形态不发生变化;当焊接电流小于25A时,其电弧形态与弧根的初始位置有关;当焊接电流处于25~60A之间时,电弧形态偶尔发生变化,但不明显。因此研究表明,重力对电弧形态没有明显的影响。
20世纪60年代,空心阴极电弧[83]作为在低压环境中使用的等离子热源被开发和利用。因空心阴极电弧电流较高,该电弧可作为焊接热源。不仅如此,由于使用于低压环境,该电弧还可应用于空间焊接领域。由于在大气环境下,其对母材的熔化量明显高于传统的TIG焊接,因此该方法也可应用于陆地的低压环境焊接中。传统TIG焊的电弧形态为钟罩形,而空心阴极电弧是从阴极内表面一直延伸到阳极工件的细圆柱形,如图1-13所示。

图1-13 空心阴极电弧与传统TIG电弧比较[84]
试验发现,其空心阴极内径对电弧形态具有很大的影响,如图1-14所示。内径越小,其电弧收缩越大,电弧直径越小。电弧直径越小也就意味电弧能量密度越大,因此其焊缝熔深也会越大。

图1-14 空心阴极电弧中阴极内径对电弧形态的影响[84]
窄间隙电弧焊是焊接厚板工件的重要方法,其最主要的工艺目的是,在厚板间隙中获得平直且具有足够熔深的焊缝。采用外加磁场驱动电弧使电弧产生摆动来进行窄间隙焊接是一种比较新的焊接方法。根据外加磁场方向的不同,电弧可在焊丝的前后左右四个方向发生偏移,电弧方向的变化对窄间隙两侧金属的熔化具有重要的作用。图1-15为在不同的磁通密度[25Gs(1Gs=10-4T,下同),50Gs,75Gs]下的电弧形态。结果表明,电弧的摆动随磁通密度增加而增加。当磁通密度为25Gs时,其电弧的摆动不明显;当磁通密度达到75Gs时,电弧摆动剧烈,电弧已经在侧壁燃烧;当磁通密度为50Gs时,电弧指向背板与侧壁之间所构成的直角。同时发现,对接间隙越小,则电弧偏离越大。电弧的摆动引起了焊接电流、电弧电压的周期性变化,进而影响了焊缝成形,使其能够焊接窄间隙厚度板。

图1-15 外加磁场电弧窄间隙熔化焊电弧形态[85]
G.J.Zhang等人[86]对双钨极氩弧焊的电弧形态作了研究。如图1-16所示,双钨极产生的电弧彼此在洛仑兹力的作用下互相吸引最后变成了一个较大的电弧。与单弧焊相比,电弧不是轴对称的,电弧横截面为椭圆形,其短轴方向与两钨极构成的平面平行。电弧越亮,其电弧密度越高,电弧温度越高。电弧所受洛仑兹力可用式(1-1)表示,即
(1-1)

图1-16 单钨极氩弧焊与双钨极氩弧焊的电弧形态[86]
式中 F——洛仑兹力,N;
I1,I2——两钨极焊接电流,A;
L——两钨极之间距离,mm。
3.熔滴过渡研究现状
熔滴过渡过程包括在电弧的作用下焊丝端头受热熔化形成熔滴,并在各种力的综合作用下从焊丝端头脱离,最后进入到工件表面的过程。熔滴过渡是影响电弧稳定性的重要原因,与焊接质量关系紧密。因此研究熔滴过渡对电弧焊的影响,能在控制焊接质量、提高熔敷速度方面产生重要的意义。对熔滴过渡的研究[87-93]主要包括不同的熔滴过渡形式、不同因素对熔滴过渡的影响以及熔滴过渡机制。
根据国内外研究现状,熔滴过渡形式如表1-1所示。
表1-1 电弧焊中熔滴过渡分类[93]

目前,国内外学者的研究主要集中在不同焊接方法、不同工艺参数以及不同外部环境对熔滴过渡的影响,并分析其熔滴过渡的机制。
T.W.Eagar等人对比了在Ar和He保护气体下进行熔化极氩弧焊过程中不同的熔滴过渡行为[94]。在焊丝侧面产生的电子聚集会增加焊丝侧面的熔化,熔化金属在重力、电磁力以及等离子流力的作用下聚集到焊丝端头处,最后对液态的金属形成压缩作用,使焊丝端头形成圆锥形,这就是所谓的锥形效应。试验发现在Ar气体保护下,与He气体保护下相比,其锥形效应更容易发生。这是因为在Ar气体保护下,在焊丝侧面流出的电流密度更大。
Kim等人采用静态力平衡理论和收缩不稳定性理论预测熔滴的大小,讨论了熔滴过渡的机制[95]。测量了熔滴的大小和过渡频率,发现随着焊接电流的增大,熔滴半径减小,熔滴过渡频率增加。研究还发现,当采用CO2气体保护时,熔滴过渡出现排斥现象,当焊接电流增加后,这种排斥现象开始减弱。当采用He气体保护时,则随焊接电流的增大,从大滴过渡转变到射滴过渡。随着焊丝伸出长度的增加,其熔滴直径会略有下降。Rhee等人研究了电弧压力对熔滴过渡的影响,当考虑电弧压力时,不管采用静态力平衡理论还是动态收缩不稳定理论,计算获得的熔滴直径都比不考虑电弧压力时要大[96]。
对于熔滴的形成与脱离机制,Amson等人研究了洛伦兹力对熔滴过渡的影响[97],当焊丝端头熔化界面为平的或圆锥形时,洛伦兹力与界面的形状和大小无关。研究发现,在熔滴形成的最初阶段为阻力,随着熔滴逐渐长大,开始成为促使熔滴过渡的力。Choi等人在静态平衡的基础上引入惯性力来预测熔滴的过渡[98],通过计算发现当惯性力达到电磁收缩力的一半时,随焊接电流的增加,惯性力开始明显影响熔滴从焊丝表面脱离;此外,得出当熔滴处于平衡状态时为球形,而处于非平衡状态时为椭圆形。Haidar等人[99,100]还研究了电弧焊过程中熔滴的形成过程、各种力对熔滴形状的影响,发现在熔滴过渡过程中轴向电磁力的影响要大于径向电磁力。Lowke等人[101]认为熔滴形式从滴状到喷射的主要原因是焊接电流增至熔滴轴心处的径向收缩压力大于表面张力,同时也提出了熔滴过渡形式发生转变时的物理模型,如式(1-2):
(1-2)
式中 γ——表面张力系数;
Rw——焊丝直径,mm;
R——熔滴半径,mm;
ρ——熔滴密度,kg/m3;
I——焊丝电流,A;
u0——真空中的磁通率,H/m。