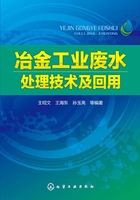
1.2 钢铁工业废水处理回用现状与节水状况分析
1.2.1 钢铁工业废水处理回用现状分析
中国钢铁工业的环境保护,从20世纪70年代,经历了近40年的发展历程,已发生了巨大的变化,污染物排放量不断减少,这是保证中国钢铁工业持续发展的前提和条件。特别是宝钢环保技术的引进与创新,为我国钢铁工业环境保护树立了榜样。就宝钢、首钢京唐、鞍钢、武钢等而言,钢铁工业环境保护已达到了世界先进水平。但是,就钢铁工业全行业而言,由于地区差异、水平高低、技术优劣、经济强弱以及其他种种原因,与国外发达国家先进水平相比,存在着不同程度的差异。所以,目前钢铁领域仍是我国工业污染的大户之一,污染还较严重,因此,钢铁工业废水处理与回用,仍是当今钢铁工业重要的任务。
(1)钢铁工业用水与重复利用情况分析
“十五”期间钢铁行业清洁生产与环境保护水平取得较大进步。经过多年努力通过建立十四个钢铁清洁生产试点企业等方式,清洁生产与环境保护理念已取得共识并取得显著效果。不少钢铁企业已制定或着手制定清洁生产环境保护与循环经济发展规划,除了原来试点外,首钢、京钢、邯钢、太钢、湘钢、通钢、安钢、宣钢、孝钢、宁波建龙、武钢、本钢、唐钢、梅钢、水钢、马钢等在“十一五”期间都制定了清洁生产、环境保护与循环经济发展规划。因此,我国钢铁企业用水逐年下降,废水处理回用循环率不断提高,见表1-2[4~7]。
表1-2 1996~2009年钢铁企业用水与重复利用率

注:1.除①外均摘自《钢铁企业环境保护统计》,1996~2010年有关数据。
2.①摘自《2008年中国钢铁年鉴》.中国钢铁工业年鉴编委会.
从表1-2可以看出,钢铁企业吨钢耗水量由1996年的231.92m3下降至2009年151.80m3,吨钢耗水量下降80.12m3,下降幅度为34.55%;吨钢新水耗量由41.73m3下降至4.50m3,吨钢新水用量下降了37.23m3,下降幅度为89.22%;废水重复利用率提高了15.06个百分点。
如以1996年钢产耗水量为基数,在同等产钢量条件下,2009年一年内要比1996年节省新水112.04亿立方米。说明近年来我国钢铁工业用水与节水成效显著。但是,由于钢产量增加,用水总量仍呈上升趋势,用水短缺问题有增无减。
(2)钢铁工业废水排放污染物与工序排污分析
2000~2009年是我国钢铁工业以科学发展观统领全行业发展,为建设和谐、节约型社会,提高钢铁企业自主技术创新能力建设,推行资源节约、资源综合利用,推进清洁生产,发展循环经济,实现和谐和环境友好型社会的关键时期。
中国钢铁工业的环境保护,从20世纪70年代中期开始,经历了近40年的发展历程,已发生了巨大的变化,污染物排放量不断减少,这是保证中国钢铁工业持续发展的前提和条件。特别是宝钢环保技术的引进与创新,为我国钢铁工业环境保护树立了榜样。就宝钢、首钢京唐、鞍钢、武钢等而言,钢铁工业环境保护已达到了世界先进水平。但是,就钢铁工业全行业而言,由于地区差异、水平高低、技术优劣、经济强弱以及其他种种原因,与国外发达国家先进水平相比,存在着不同程度的差距。所以,目前钢铁行业仍是我国工业污染的大户。
①钢铁工业废水排放与处理状况分析 近10年来中国钢铁工业外排废水量、废水处理率及外排废水达标率如图1-2~图1-4所示[4,8~10]。

图1-2 近10年中国钢铁工业外排废水量变化

图1-3 近10年中国钢铁工业废水处理率变化

图1-4 近10年中国钢铁工业外排废水达标率变化
由图1-2~图1-4可知,在2000~2010年,中国钢铁工业外排废水量在逐渐减少,从200804.81万吨下降到72495.02万吨,下降率为63.39%,废水处理率和外排废水达标率均逐年上升。
②钢铁工业废水排放主要污染物分析 近10年来钢铁工业废水主要污染物如COD、悬浮物(SS)、石油类、氨氮、酚、氰化物(以氰根计)等的排放情况见表1-3[4,9,10]。从表1-3看出,我国钢铁废水中主要污染物排放量都有明显下降,其中以悬浮物最为明显,但氨氮明显增加。是因焦化废水处理设施未能同步配套所致。
表1-3 2000~2009年钢铁工业废水中主要污染物排放情况

①“-”表示上升。
③钢铁企业各工序排污分析 根据工序排污专题调研统计分析,钢铁工业废水中主要污染物如COD、悬浮物、石油类、氨氮、酚、氰化物(按氰根计)在各工序中的分布情况,见表1-4[5,10]。
表1-4 废水中主要污染物在各工序中的分布情况

由表1-4可知,中国钢铁企业各工序排放的COD量按大小排列依次为焦化、炼铁、轧钢、炼钢和烧结;对悬浮物而言,只有烧结工序排放较少,其他工序排放量相近;各工序排放石油类污染物量以轧钢最多,其次是焦化、炼钢和炼铁,而烧结产生量最少;氨氮主要来源于焦化工序;焦化工序是废水中氰化物的主要产生源,其次是炼铁,烧结排放的氰化物很少。废水中COD、氨氮、酚、氰等有毒物,均以焦化工序最为明显,说明焦化工序是钢铁企业的污染最为严重的工序。
按各工序吨产品分析,中国钢铁工业废水主要污染物如COD、悬浮物、石油类、氨氮、酚、氰化物(按氰根计)排放情况,见表1-5[5、9、10]。
表1-5 废水中主要污染物在各工序吨产品中的分布情况

由表1-5可知,各工序吨产品排放的COD、悬浮物、石油类、氨氮、氰化物量以焦化最大,烧结最小;石油类排放量比较大的还有轧钢工序;悬浮物和COD的排放情况,除焦化工序外,炼铁、炼钢和轧钢工序排放量都比较大;氰化物和氨氮的排放除焦化工段外,其他各工序排放量都不大。
1.2.2 钢铁工业节水潜力与减排现状分析
我国钢铁工业近几年来,对节约用水重要意义的认识有较大提高,对节水设施的投入力度亦有所增加,钢铁企业在节水方面取得了显著成绩。以2000年与2009年相比,钢产量由1.17亿吨增加到3.89亿吨,增加了3.32倍 ,而用水量只增加2.64倍;吨钢平均新用水量由24.75m3/t下降到4.50m3/t,下降率达81.82%以上;废水重复利用率提高了10.03个百分点。
我国钢铁行业的节水仍有较大潜力,但从吨钢取水量和重复利用率这两个指标衡量分析,无论从国内企业之间比较,还是与国外企业之间比较,均存在着较大的差距,也反映了节水潜力所在。2002年钢铁企业吨钢取水量的多与少、重复利用率的高与低,与企业所在地的水资源条件有着密切关系,与企业的钢产量规模大小虽有关系,但是已不像过去那样突出了。
根据近年来的钢铁企业用水指标分析,年产钢量大于500万吨的企业,吨钢取水量最低值为5.31m3,上下值相差约6倍多;年产钢量在400万~500万吨之间的企业,吨钢取水量最低值为10.07m3,上下值相差2.5倍;年产钢量在200万~400万吨之间的企业,吨钢取水量最低值为4.54m3,上下值相差6.2倍;年产钢量在100万~200万吨之间的企业,吨钢取水量最低值为4.68m3,上下值相差7.2倍;年钢产量在小于100万吨的企业,吨钢取水量最低值为4.29m3,上下值相差达11倍之多。吨钢取水量接近高限的企业基本上位于丰水地区。各企业中水的重复利用率最低为65%,在缺水地区的企业基本上均大于90%,与国外一些钢铁企业比较,国内缺水地区企业比国外低1~8个百分点,在丰水地区企业比国外低8~33个百分点。这说明我国钢铁工业节水潜力还有较大空间,同时加强节水意识教育与节水统一管理是非常重要的。
为了掌握和分析节水途径,某大型钢铁公司组织了从原料、烧结到冷轧钢管开展了系统的水平衡测试分析,包括输入水量、输出水量、冷却水量、进出水量、循环率、新水补充量及排污量等进行了水量平衡测试。其各工序用水量与工序耗水量分析结果见表1-6和图1-5[11]。
表1-6 各工序用水量结果


图1-5 各工序耗水情况
根据表1-6数据分析:说明系统水的损失漏水率较高,占总用水量约8.3%;炼铁工序用水量最大,占公司总用水量的25%;炼钢工序次之,占总水量的17%;其他大部分用户的用水量占总水量的比例大致在5%~15%之间;条钢和钢管工序用水量较小,占用水量的2%。
中国钢铁工业协会从30家重点企业抽样调研结果,其吨钢耗水量见表1-7。
表1-7 30家重点企业工序吨钢耗水情况

表1-7表明,耗水程度依次按炼铁—炼钢—轧钢—焦化—烧结递减。采用干熄焦、高炉煤气、转炉煤气干式除尘的企业其相关工序的新水消耗指标有明显优势,如宝钢的焦化和转炉炼钢、莱钢的炼铁与转炉炼钢工序耗新水指标都位居调研企业的领先水平。以特钢和以板带材为主要产品的企业其轧钢工序新水耗量更多一些,节水难度更大一些,如图1-5所示。其工序耗水量(从大到小)依次为冷轧—炼铁—焦化—炼钢—烧结。这也是国外按板材和长材制定不同用水标准的原因。
图1-6是近年来我国部分钢铁企业节水潜力调研与分析结果。

图1-6 我国部分钢铁企业各工序中的用水与节水潜力分析
图1-6表明,串级供水技术在炼铁工序中的利用率最高,在烧结、焦化、炼钢工序中的利用率相差不大,而在轧钢工序中利用率最低;生产废水回用技术在炼钢、轧钢工序中利用率最高,而在焦化工序中利用率最低。同时也表明,我国钢铁工业节水潜力尚有很大空间。
串级供水技术、污水回用技术等节水技术的应用使钢铁企业水的重复利用率大幅提高。但是这些节水技术的有效运用有一个前提,那就是必须对钢铁企业各工序废水进行有效处理,以满足工序用水要求与水质标准。