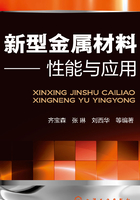
1.3 第三代汽车先进高强度钢的开发
1.3.1 汽车轻量化与先进高强度钢的发展
现代汽车发展的方向是轻量化、节能降耗、减少排放和提高安全性,从而对占汽车质量70%左右的汽车用钢也提出更高的要求,带动了汽车钢(特指汽车薄板钢)的发展。研究表明,汽车自重的25%在车身,车身材料的轻量化举足轻重;汽车的燃油消耗与汽车自身总质量呈正比,汽车每降低10%的自重就可节约燃料3%~7%。节能环保,必须在确保安全性前提下尽量减轻汽车自身质量,从而推动了先进高强度钢(Advanced High Strength Steel,即AHSS)的发展。据推测,到2015年,在世界轻型车车身及其封闭件中,AHSS将增加到35%。例如,汽车用普通钢板的厚度通常为0.70~0.75mm,而AHSS板厚度仅0.65mm甚至更薄,新款欧宝赛飞利的发动机盖钢板只有0.6mm厚。这只需在每辆车上增加212欧元(约合人民币2200元)的成本以购买AHSS板减轻车身质量就能节省约5%的燃油。因此,近年来各国一直致力于第3代汽车AHSS的研发。
美国科学家Krupitzer和Heimbuch首先提出了第3代AHSS的概念,美国汽车/钢铁联盟在美国能源部和美国国家卫生基金会的支持下于2007年10月启动了为期3年的强塑积与成本介于第1与第2代AHSS之间的第3代AHSS的研发工作。同时,我国与韩国也相继启动了提高强塑积的高强高塑钢的研发工作。至今,各国第3代AHSS的研发仍在积极探索之中。2010年10月,中国钢铁研究总院与太钢集团合作,成功地在工业生产流程上开发出第3代AHSS热轧板卷和冷轧板,强塑积均超过30GPa·%,并研发出我国第3代AHSS及其工业化生产技术。
1.3.2 第三代汽车钢的概念及其在我国的开发
针对汽车轻量化和高安全性能要求,未来汽车用钢铁材料应是一个具有强度和塑性良好结合的新一代钢铁材料。这要求新型汽车用钢不但可通过高强化来达到汽车的轻量化,而且需较高塑性来提高钢的成形能力和汽车的碰撞安全性能。
(1)汽车用钢的综合性能指标——“强塑积”
为了直观而准确地描述这种高强高塑性钢材,提出了具有高强塑积性能(即抗拉强度Rm与塑性A的乘积)的第3代汽车钢的概念,作为未来新型汽车钢的研发方向。
强塑积作为汽车用钢的一个综合性能指标,它直观地表达了汽车用钢成形能力和碰撞中吸收形变能大小的一个参数,因而越来越受到材料研究人员和汽车设计人员的重视。由于汽车用钢量大而且质量较高,高性能汽车用钢的发展水平也代表了一个国家整个钢铁研究和生产水平的重要标志。
(2)三代汽车用钢的划分
根据强塑积Rm×A的大小,将强塑积为10~20GPa·%的IF钢、DP钢、TRIP钢和热成性MART(马氏体)钢等汽车用钢称为第1代汽车用钢;将强塑积为50~70GPa·%的奥氏体钢和TWIP钢等称为第2代汽车用钢;而将第1代汽车用钢和第2代汽车用钢之间(性能与成本)的新型汽车用钢则称为第3代汽车用钢,即性能和成本均介于两者之间的新型汽车用钢。低成本和高强塑是对未来汽车用钢发展的一个基本定位。
(3)我国第三代汽车用钢的发展
2007年,中国钢研的科研人员注意到国际上的汽车钢研发动向。中国钢研董事长干勇认为,第三代汽车钢的研发意义重大,于是决定立即投入力量开展相关研究。2008年,在国家第3期“973”计划的资助下,钢铁研究总院相关研究人员在归纳分析第1代汽车钢与第2代汽车钢的组织与性能的基础上提出要获得30~40GPa·%的强塑积,钢中的亚稳奥氏体体积分数需要达到30%左右。为了同时获得高强度和高塑性,必须通过合理的组织调控获得硬基体与亚稳奥氏体相复合的组织结构。
钢研院研究人员经过深入实验研究,认为组织含30%左右亚稳奥氏体与超细晶基体,性能为强塑积不低于30GPa·%的低成本高强高塑钢将是一种非常具有前景的第3代汽车钢。中国钢研与太原钢铁公司合作,成功地在工业生产流程上开发出第3代汽车钢热轧板卷和冷轧板,强塑积均超过30GPa·%(抗拉强度为900MPa级时,伸长率35%),率先在国际上研发出第3代汽车钢产品工业生产技术。中国率先在世界上完成第3代汽车用钢的工业化试制。首先会应用在北京现代和一汽的汽车上,2012年制造出实验产品,2014年实现商业应用。
1.3.3 高强度钢的强化机理、分类与发展
(1)高强度钢的强化机理
高强度钢的强化机理主要有固溶强化、析出强化、组织强化和细晶强化等,如表1-7所示。
表1-7 高强度钢的强化机理

(2)高强度钢的分类
根据国际上对高强度汽车用钢板的研究,将抗拉强度<270MPa、屈服强度<210MPa的钢称为低强度钢;抗拉强度在270~770MPa、屈服强度在210~550MPa范围内的钢称为高强度钢(HSS);而抗拉强度>770MPa、屈服强度>550MPa的钢称为超高强度钢(DHSS)。AHSS(先进的高强度钢)的屈服强度则包含了高强度钢板(HSS)和超高强度钢板(DHSS)的范围。
按照强化机理又可把高强度钢板分为传统(普通)高强度钢板和AHSS板。传统(普通)高强度钢板多是以固溶、析出和细化晶粒等为主要强化手段,常见的主要有碳-锰(C-M)钢、高强度低合金(HSLA)钢、各向同性(IS)钢、含磷(P)钢、高强度无间隙原子(IF)钢和烘烤硬化(BH)钢等。AHSS则是指主要通过相变进行强化的钢种,组织中含有马氏体、贝氏体和残余奥氏体,如双相(DP)钢、马氏体(M)钢、相变诱发塑性(TRIP)钢、孪生诱发塑性(TWIP)钢以及淬火和再分配(Q&P)钢等。
AHSS(先进的高强度钢)的强度和塑性配合与传统高强度钢相比更加优越,且具高强度和良好的成形性,特别是加工硬化指数高,利于提高碰撞过程中对能量的吸收,对于实现车身减重的同时保证安全性十分有利。
(3)高强度钢的发展趋势
表1-8给出了北美学者的一个研究报告,它认为20世纪80年代汽车厂家主要考虑汽车钢的成本、成形性能和耐腐蚀性能,这对应着当时的IF钢和镀锌钢板;20世纪90年代主要考虑汽车钢的成本和碰撞安全性,当时汽车钢的代表主要是HSLA钢、C-Mn钢和BH钢;21世纪初的前10年主要考虑汽车钢的成本、节能和碰撞安全性,当时的汽车钢代表是DP钢、TRIP钢和热成形钢;未来人们主要考虑如何提高汽车钢的碰撞安全性、节能效果与成本,现代汽车钢将是同时具有高强度和高塑性的新一代汽车钢即第3代汽车钢。
表1-8 汽车主要设计目标、关键性能与研发的相应汽车钢类别

图1-9示出了各种钢的应力-应变曲线及抗拉强度Rm与伸长率A之间的关系。可以看出,第1代汽车钢包括DP钢、CP钢、TRIP钢、马氏体钢、贝氏体钢都可看作是以铁素体为基的高强度钢,其强塑积一般在15GPa·%的水平,其抗拉强度可从IF钢的300MPa提高至马氏体钢的2000MPa,甚至更高;但其塑性基本上随抗拉强度的提高而下降,即伸长率由IF钢的45%左右下降至马氏体钢的小于10%。可以说,具有较低强塑积的第1代汽车钢已不能满足汽车工业未来发展对轻量化和高安全的双重要求。对第2代汽车钢,其抗拉强度在800~1000MPa水平、塑性可达50%~90%的优良塑性,这表明其具有非常高的碰撞吸收能力与良好的成形能力,但相对于合金含量<5%的第1代汽车钢,第2代汽车钢如TWIP钢、L-IP(具有诱发塑性的轻量化)钢、奥氏体不锈钢等在常温下都是奥氏体单相组织,可以看作是奥氏体为基的AHSS,其强塑积虽达到较高的50GPa·%的水平,但因添加了大量的Cr、Ni、Mn、Si和Al等合金元素且其总合金含量高达25%以上,导致其成本较高、工艺性能较差及冶金生产困难较大。为适应节能、降低成本、汽车轻量化和提高安全性要求,迫切需要研发具有成本接近第1代汽车钢而性能接近第2代汽车钢的低成本高强塑积的第3代汽车钢。低成本和高强塑积是汽车钢发展的一个基本定位。

图1-9 各种汽车钢的力学性能
由图1-9可见,在第1代和第2代AHSS之间的区域,即第3代AHSS区域,现有的研究主要是通过改进或创新的工艺路线来致力于填补这些空白区域,并特别关注于工业化生产可行性和成本因素。其研发策略主要有:研发性能良好的DP钢;改进传统TRIP钢;研发超细晶贝氏体高强钢;开发新的生产工艺路线,包括淬火-碳分配(Q&P)和超快加热和冷却工艺等。
1.3.4 第3代先进高强度钢的研究进展
性价比良好的第3代先进高强度钢(AHSS)已成为世界各国研发的热点,本文将在以下7个方面,对这些方案和研究进行说明。
(1)性能良好的DP钢
DP钢是指双相钢,其软相是铁素体,硬相是马氏体。DP钢是既有高的抗拉强度又有相当高的伸长率的钢种,同时其又有较高的疲劳性能。DP钢因其具有高的伸长率和疲劳性能而常被应用于轮毂上。采用优化碳含量和/或临界退火温度来增加马氏体含量来稳定获得强度更大的DP钢。以这种方式开发出来的DP780、DP980和DP1180已经工业化生产。采用特殊的热轧工艺获得的显微组织细化也可达到强度增加的目的,主要有两种工艺。
①应用变形诱导铁素体相变(DIFT) DIFT包括由奥氏体到铁素体的应变诱导相变,该相变是在低于Ac3的Ar3之上25~50℃区域进行轧制。该方案已成功生产出晶粒尺寸在1μm级的超细晶粒铁素体。采用轧后特殊的冷却工艺以传统的DP钢成分,如0.06C-1.9Mo,生产出了超细晶DP钢。值得关注的一个现象是,超细晶DP钢可通过更低的合金成分而不添加昂贵的Mo来获得。
②在珠光体精轧温度之下进行大应变(真应变最大为1.6)温轧 由此而获得带有均匀弥散的、球化渗碳体颗粒的超细晶粒铁素体基体。在随后进行临界退火处理时,所获得的1~2μm晶粒基本处于稳定状态。以该方式获得的抗拉强度893MPa、伸长率为21%的超细晶DP钢已见报道。然而,这些钢的性能仍处于第1代AHSS的区域内,这种组织细化的DP钢还不能够达到第3代AHSS的性能。
在一些情况下,强度增加还不是主要关注点,现已开发的多种DP组织结构目的是满足专用要求,像高的扩孔率或抗弯性,而不是单纯地追求抗拉强度的增加。如浦项光阳厂的6号热镀锌生产线在世界上首次成功地生产了490MPa级深冲型DP钢汽车面板。2010年,浦项制铁又成功开发了590MPa级DP钢汽车面板。表1-9为典型DP钢工业化生产概况。
表1-9 典型DP钢工业化生产概况

注:表中DP钢均为冷轧。
(2)改进型TRIP钢
TRIP钢是指含有残余奥氏体的微合金化钢,直译是相变诱导塑性钢。它也是既有高的抗拉强度同时又有相当高的伸长率的钢种,同时它又有较高的疲劳强度。TRIP钢由于其具有相变诱导塑性的特点,在增加强度的同时不至于损害其塑性。对于TRIP钢应考虑其焊接性能、表面质量等方面问题,因此其C、Mn含量不宜过高,一般碳含量(质量分数)<0.2%,Mn、Si、Al含量(质量分数)均<2%。为获得热轧态的TRIP钢,需添加Nb、Mo等微合金元素。固溶Nb在热轧和奥氏体转变为铁素体的过程中延迟了静态和动态再结晶。少量的碳氮化物也推迟了再结晶并导致一定量的强度的增加。添加Nb、Mo可有效地改善强度和伸长率。该钢板在400℃卷曲时,抗拉强度为780MPa级的钢板的强塑积达26000MPa·%。另外,细小弥散的残余奥氏体也有助于改善钢的延展性。
相对于现今已工业化的TRIP钢,早期的研究钢种碳含量更高,研究者研究了0.4CMnSi钢种,其性能指标处于第3代AHSS优先考虑的目标区域内。此外,通过合金化对TRIP钢进行晶粒细化,已获得了标准强度达1GPa,总伸长率达20%的钢。其他的TRIP钢开发包括改进热处理,即在350~475℃温度区间内进行等温处理,而某些情况下是在Ms温度之下(计算值为417℃)。当降低保温温度时,导致强度值增加而延展性下降,同时应变硬化显著变小。
鞍钢已批量供货的低碳低硅无铝(低铝)TRIP590和TRIP780钢突破了TRIP钢传统的合金设计理念,如TRIP780采用0.22C-0.6Si-1.65Mn-0.05P-0.02Al-0.1V合金设计,以P或P+V代Si、Al,使成分、工艺设计更加科学合理,这类TRIP钢成本低、可镀、可焊,低温韧性好,工业生产方便,钢板的性能达到及优于国外同类产品实物水平。目前,980MPa级高强度冷轧TRIP钢在鞍钢也已研制成功。表1-10为典型TRIP钢工业化生产概况。
表1-10 典型TRIP钢工业化生产概况

①Si+Al=2.00。
注:表中TRIP钢均为冷轧。
(3)超细晶贝氏体钢
近来的研究工作一直致力于开发出超细贝氏体组织的高强度钢(见表1-11)。通过采用125~625℃较低的相变温度,研发出0.98C-1.89Mn-1.46Si-1.26Cr-0.26Mo-0.090V合金,其硬度为600(HV),而强度超过2.5GPa。该显微组织是经15天热处理之后获得的,该时间对于工业化生产来说,时间太长,为此正在做进一步的研究。通过采用Al和/或Co进行合金化,将加热温度降低,争取将热处理时间大幅度缩短,以便进行工业化生产。该钢具有高强度和高韧性,使该材料成为装甲用钢的一个良好备选材料,它比类似性能的马氏体时效钢的成本低很多。可以获得具有良好伸长率和韧性且抗拉强度在1700~2300MPa的钢种,但由于采用相对高的合金和碳含量,该方法进行大规模的应用可能会更加困难。
表1-11 典型超细晶贝氏体钢研发概况

西班牙国家冶金研究中心和新西兰代尔夫特大学的研究人员成功试制出了碳含量为0.3%同时不含碳化物的贝氏体钢,其显微组织由贝氏体铁素体和残余奥氏体组成。该钢显示出良好的强韧性组合,抗拉强度在1500~1800MPa,总伸长率超过了15%。经过改进的含碳量为0.2%的贝氏体钢达到了更好的强韧性组合,而且其焊接性得到改善。
(4)淬火-碳分配(Q&P)钢与淬火-碳分配-回火(Q-P-T)钢
①Q&P钢 新型钢种的开发逐步向兼顾强度和塑性的方向发展,为进一步改善材料的综合性能,2003年,美国Speer等开发研究了一种新的热处理工艺(Quenching and Partitioning Process,即Q&P工艺,淬火-分配工艺),该工艺是将含一定量Si和(或)Al的合金钢经淬火至Ms-Mf间一定的温度QT(Quenching Temperature)后,再在一定温度PT(Partitioning Temperature)等于或者高于Ms停留,使碳由马氏体扩散至残留奥氏体,使其稳定化,增加最后淬至室温的残留奥氏体含量,最终主要得到马氏体和一定可控量的富碳残留奥氏体,如图1-10所示。图中Ci、Cγ和Cm分别表示原始合金、奥氏体和马氏体中的碳含量,QT和PT分别表示初始淬火温度和碳分配温度。

图1-10 均匀奥氏体经淬火-碳分配(Q&P)处理示意
因此,Q&P钢是一种新型的高强度和高塑(韧)性的马氏体钢,室温条件下为马氏体和残留奥氏体两相组织。但它区别于传统的回火马氏体钢,同等强度下与回火马氏体钢相比,塑性有大幅度提高。这是由于Q&P钢的室温组织中除马氏体以外,还存在7%~15%的残留奥氏体,奥氏体变形时发生TRIP效应,转移颈缩时的应力集中,延缓裂纹产生,提高塑性。
我国宝钢进行了Q&P钢工业化试制,其研究的0.2C-1.5Si-1.8Mn系TRIP780钢经Q&P处理,成功生产出Q&P1000钢,其抗拉强度为981~1223MPa,伸长率为9.3%~21.2%,并成功用于国内轿车B柱的冲压成形。另外,科罗拉多矿业大学与浦项公司合作研究了不同C、Mn含量对Q&P钢组织与性能的影响。经过实验,其完全奥氏体化后的0.2C-3Mn-1.6Si及0.3C-3Mn-1.6Si系钢展示出了较佳的强韧性组合。但有关Q&P钢的组织结构与性能的关系,特别是少量残余奥氏体对于应变硬化的贡献还有待于进一步研究。表1-12为典型淬火-碳分配(Q&P)钢研发概况。
表1-12 典型淬火-碳分配(Q&P)钢研发概况

②Q-P-T钢 为了改善环保、节约能源和原材料,需要进一步提高钢的强度,我国材料科学家徐祖耀在Q&P工艺基础上,提出淬火-碳分配-回火(Q-P-T)工艺,即引入碳化物沉淀强化机制,在含有一定Si和(或)Al量的钢中有意识地加入少量复杂碳化物形成元素(如Nb、V或Mo等),使经过碳分配处理外,再在一定温度保温使析出共格、弥散的复杂碳化物(非渗碳体),呈现沉淀强化,如图1-11所示。因此,此类钢即称Q-P-T(淬火-碳分配-回火)钢。Q-P-T钢的研究与开发,不仅对Q-P-T钢组织和性能的设计和控制有重要实际意义,而且对开发具有自主知识产权的低碳硅锰高强度Q-P-T钢、进一步推动我国的汽车工业发展具有重要的实用价值。

图1-11 淬火-碳分配-回火(Q-P-T)工艺示意
(AT、QT、PT、TT和RT分别表示奥氏体化温度、淬火温度、碳分配温度、回火温度和室温)
③Q-P-T钢的成分、组织和热处理设计原则
a.成分设计 碳含量应<015%(质量);为避免Fe3C的形成造成脆性及改善焊接性,Si(及Al)能抑制Fe3C的形成,稳定ε(η)碳化物,并使钢能进行碳分配处理,宜含1%~2% Si(或约1% Al);含Mn、Ni等稳定奥氏体元素,使Ms下降;含复杂碳化物形成元素如Nb或(和)Mo,使Ms下降,呈沉淀硬化并细化奥氏体晶粒。建议的成分(质量分数)为:<015%C、1%~2% Si、1%~2% Mn、约0.02%Nb或(和)0.2%Mo。
b.显微组织 具高位错密度的细条状马氏体,条厚最好为数十纳米;马氏体上析出细小共格复杂碳化物以进一步增加强度;避免析出Fe3C;马氏体条间含适当数量(厚度)和一定碳含量的残留奥氏体,以提高钢的韧性和塑性;原始奥氏体应具细晶组织。
c.热处理工艺。较低温度奥氏体化,可以得到细晶奥氏体组织;淬火至一定温度(QT)以获得适量的马氏体。淬火温度或马氏体量为决定钢最终强度的主要因素之一。在淬火温度,也可能自马氏体沉淀出ε(η)过渡碳化物。为使更多残留奥氏体富碳,并稳定至室温,常在Ms以上温度停留,进行碳分配。复杂碳化物的沉淀可在分配温度(PT)进行,也可在PT较高或略低温度下进行,最后水淬至室温(RT),上述工艺即为Q-P-T热处理。其中,淬火温度(QT)、分配温度(PT)和在分配温度下的停留的时间,以及回火(沉淀)温度(TT)和时间,决定马氏体量及其碳含量,以及残留奥氏体量及其碳含量,从而决定钢的强度、伸长率和韧性。
④Q-P-T钢应用实例 研究者对比新型淬火-分配-回火(Q-P-T)和传统淬火-回火(Q-T)处理对中、低碳钢力学性能的影响发现,在提高材料的强塑积方面Q-P-T处理远胜于Q-T处理,特别是对中碳钢的效果更为显著。如Fe-0.42C-1.46Mn-1.58Si-0.028Nb合金的强塑积经Q-P-T处理后高达31627 MPa·%,且延伸率达20.3%,不仅远高于传统Q-T处理的试样,而且已满足新一代AHSS钢预测的性能。显微组织分析表明,Q-T和Q-P-T处理的差异在于:残留奥氏体的量和尺寸分布以及马氏体板条的均匀程度。前者含少量(<3%)较薄的“薄膜状”残留奥氏体,且马氏体板条尺寸范围较宽;而后者含较多较厚的“薄片状”残留奥氏体,且马氏体板条尺寸分布较窄。因此Q-P-T处理的AHSS具有承受较强的塑性变形和阻止微裂纹扩展的能力。
又如,研究者对Q235钢经新型淬火-分配-回火(Q-P-T)工艺处理后,进行了力学性能试验。试验结果表明,经Q-P-T处理后的Q235钢,其强度得到了大幅度的提升:屈服强度和抗拉强度分别达435MPa和615MPa。显微组织观察,揭示了Q235钢性能改善的原因:Q235钢经淬火-分配-回火(Q-P-T)工艺处理后为硬相马氏体、贝氏体和软相残余奥氏体的复合组织,取代了原铁素体+珠光体组织。
(5)超快加热和冷却工艺
一种超快加热和冷却工艺(Flash Process)现已用于钢板生产。采用该工艺生产的一种AISI8620钢种呈现出非常细的显微组织,它由贝氏体铁素体和马氏体组织构成,其上均匀分布着大的和小的被认为是富Cr的渗碳体。由于奥氏体化时间非常短,这些碳化物被认为是遗传于先前显微组织中的难溶碳化物。在最终的显微组织中也观察到非常细的先前的奥氏体晶粒。可以假设,在Ac3温度之上的很短时间内能产生不完全的碳扩散并在整个奥氏体组织上重新分配,它将导致复合的奥氏体分解产生不同的相变组织,如贝氏体和马氏体。
美国研究人员对低合金AISI1020钢进行了实验,305mm宽薄钢板在5s之内进行快速加热与冷却,获得了1560~1600MPa抗拉强度和8.0%~8.7%伸长率。由于获得了贝氏体组织,具有优良的耐回火能力,在500℃回火300s后,仍有1225MPa的抗拉强度。该钢经温轧成型,可通过一次和二次冲压将钢板加工成复杂几何形状的零件。表1-13为美国超快加热和冷却工艺钢的成分及性能。
表1-13 美国超快加热和冷却工艺钢的成分及性能

(6)高锰钢
由Merwin基于Grange和Miller早期研究成果而研发的较低锰(5%~7%)、低碳(0.1%)成分的双相铁素体-奥氏体显微组织的钢。其锰含量高于常规钢种,但比TWIP钢低很多,可以采用常规的热轧、冷轧和罩式退火工艺。在退火温度的最高点延长保温导致了双相区退火,此时产生了锰分配现象。在室温条件下获得了由铁素体和高锰奥氏体构成的超细晶显微组织。在0.10C-5.2Mn钢中,检测的奥氏体比例达17%,而在0.10C-5.8Mn和0.10C-7.1Mn钢中所获得的奥氏体比例分别达28%和38%。除了降低TWIP钢相关的合金成本之外,该工艺路线也可使那些不具备连续退火或先进冷却能力的生产线生产出高强钢。
关于第2代奥氏体钢种已提出各种成分系列,现今的研究主要集中在如何降低合金含量上。Frommeyer等研究了更低锰(15% Mn)的Fe-Mn-3Si-3Al系钢。高锰钢中Mn、C、Al等合金元素含量较高,对冶炼、连铸以及热轧工艺提出了非常苛刻的要求。主要表现在以下几点。
①冶炼过程中,Fe-Mn-Al-Si系高锰中Al元素烧损严重,成分难以精确控制;另外,Mn、C与覆盖剂容易发生反应。
②连铸过程中,Mn元素的微观偏析导致弯月面处的凝固坯壳强度偏低,容易漏钢;随着温度下降,高锰钢强度快速上升,导致拉矫过程困难。
③热轧过程中,在隧道炉加热时晶界非常容易氧化,并且钢中K相碳化物也带来热轧的困难,高Mn、C含量容易使热轧板表面形成凹坑缺陷。
可见,利用连铸-热轧传统流程生产高锰钢存在许多技术瓶颈。薄带连铸技术快速凝固,可以有效降低高合金钢中元素的偏析,提高材料的成型性能。各大钢铁集团在尝试利用该技术生产高锰钢。蒂森-克虏伯钢铁公司采用带式的薄带连铸技术,尝试生产出Fe-Mn-Al-Si系高锰钢薄带。韩国浦项科技大学也在尝试用薄带连铸流程进行Fe-Mn-C系高锰钢的生产。表1-14为典型TWIP(孪晶诱发塑性)钢研发概况。
表1-14 典型TWIP(孪晶诱发塑性)钢研发概况

(7)中锰碳亚稳奥氏体-超细晶基体钢
目前,通过中锰碳钢的合金化设计及奥氏体逆相变等措施,中钢研已在实验室内制备出30%左右的亚稳奥氏体与超细晶基体的双相复合组织钢。该钢的室温抗拉强度在0.8~1.6GPa级,断后伸长率为30%~45%的水平,而其强塑积在30~48GPa·%。目前实验室内已完成了对不同碳含量和不同锰含量的C-Mn钢的系列化基础研究。基本工艺是对设计的原型钢先进行淬火处理,获得马氏体组织,然后对这些淬火钢双相区(Ac1~Ac3)进行不同时间的退火,进行奥氏体逆转变,获得包括奥氏体、超细晶铁素体及沉淀析出相的多相组织,此种退火工艺被称为奥氏体逆转变退火。
从以上对中锰钢实验室研究结果来看,通过逆转变处理和相应的形变处理,可获得含有大量奥氏体相的基体为超细晶组织的奥氏体、铁素体双相钢。当钢中含有30%左右的亚稳奥氏体时,可获得强塑积30~40GPa·%的高强高塑汽车钢。拉伸形变过程中,亚稳奥氏体又逐步转变为马氏体,形成了亚稳、多相和多尺度的称为M3的组织。2011年11月中钢研与太钢合作研发的第3代汽车钢在太钢进行了工业试制,初步试制的0.1C-5Mn钢热轧卷和冷轧板均达到第3代汽车钢的基本目标。表1-15为中钢研第3代汽车钢工业试制数据概况。
表1-15 中锰亚稳奥氏体-超细晶基体钢的主要成分和性能

在汽车制造领域,钢与铝及镁合金等的竞争已进入一新的阶段。同时,汽车制造商也对钢铁材料的性能和成本提出了更高要求,AHSS,特别是性价比优良的第3代AHSS汽车钢的开发就显得特别迫切。目前,世界各国都在致力于AHSS特别是第3代AHSS的研究和开发,同时也对新的用户加工技术与工艺加大了研究力度,使钢的强韧性能得到进一步提升。中钢研已获初步成功的第3代AHSS研发,同时以Q&P钢和先进贝氏体钢为代表的AHSS的研发,是目前比较接近于第3代AHSS目标的研发方向,其他的工艺路线和新钢种也正在探索之中。中钢研与太原钢铁集团率先在国际上联合成功开发了第3代AHSS汽车钢的工业试制工艺路线,标志着我国AHSS的研发达到了世界先进水平。