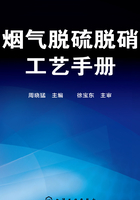
2.7 钠碱法脱硫
2.7.1 技术方法
2.7.1.1 方法概述
随着我国对火力发电厂SOx排放的控制越加严格,采用各种烟气脱硫装置越来越普遍,为了统一和规范火力发电厂烟气脱硫装置的设计和建设标准,贯彻“安全可靠、经济适用、符合国情”的基本方针,做到有章可循,结合近几年来火力发电厂烟气脱硫装置的设计和建设过程中遇到的工程实际问题和经验总结,编制DL/T 5196—2004《火力发电厂烟气脱硫设计技术规程》。
本规程适用于安装400t/h及以上锅炉的新、扩建电厂同期建设的烟气脱硫装置和已建电厂加装的烟气脱硫装置。安装400t/h以下锅炉的电厂烟气脱硫装置设计可以参照执行。
2.7.1.2 系统构成
典型的钠碱湿法烟气脱硫工艺流程如图2-13所示。

图2-13 钠碱湿法烟气脱硫工艺流程
2.7.2 反应原理
2.7.2.1 吸收原理
吸收液通过喷嘴雾化喷入吸收塔,分散成细小的液滴并覆盖吸收塔的整个断面。这些液滴中的碱液与塔内烟气逆流接触,发生传质与吸收反应,烟气中的SO2、SO3及HCl、HF被吸收进入循环池,在循环池中进行强制氧化和中和反应。
碱液处理含硫烟气,由于烟气中还含有大量的CO2,用NaOH溶液洗涤气体时,首先发生的CO2与NaOH的反应,导致了吸收液pH的降低,且脱硫效率很低。随时间的延长,pH降至7.6以下时,发生吸收SO2的反应。随主要吸收剂Na2SO3的不断生成,SO2的脱除效率也不断升高。当吸收液中的Na2SO3全部转变成NaHSO3时,吸收反应将不再发生,此时pH值降至4.4。但随SO2通入pH值仍继续下降,此时pH值的下降原因仅仅是由于SO2在溶液中进行了物理溶解所致。因此,吸收液有效吸收SO2的pH范围为4.4~7.6。在实际用吸收液进行处理时,吸收液的pH值应控制在此范围内。
2.7.2.2 吸收反应
烟气与喷嘴喷出的循环碱液在吸收塔内有效接触,循环碱液吸收大部分SO2,反应如下:
2.7.2.3 中和反应
吸收剂碱液保持一定的pH值,在吸收塔内发生中和反应,中和后的碱液在吸收塔内再循环,中和反应如下:
中和反应本身并不困难,吸收开始时主要生成Na2SO3,而Na2SO3具有脱硫能力,能继续从气体中吸收SO2转变成NaHSO3时,吸收反应将不再发生,因为NaHSO3不再具有吸收SO2的能力,而实际的吸收剂为Na2SO3。
2.7.2.4 氧化反应
部分在吸收塔喷淋区被烟气中的氧所氧化,其他的
在反应池中被氧化空气完全氧化,反应如下:
2.7.2.5 其他副反应
烟气中的其他污染物如SO3、HCl、HF和尘都被循环浆液吸收和捕集。SO3、HCl和HF与悬浮液中的石灰石按以下反应式发生反应:
脱硫反应是一个比较复杂的反应过程,其中有些副反应有利于反应的进程,有些会阻碍反应的发生,在设计中予以重视。
Al主要来源于烟气中的飞灰,可溶解的Al在F-浓度达到一定条件下,会形成氟化铝络合物(胶状絮凝物)。
在一个接近封闭的系统状态下,FGD工艺会把吸收液从烟气中吸收溶解的氯化物增加到非常高的浓度,控制氯离子的浓度在12000~20000mg/L是保证反应正常进行的重要因素。
2.7.3 系统描述
2.7.3.1 FGD系统构成
锅炉烟气经进口挡板门进入脱硫增压风机,通过烟气换热器后进入吸收塔,洗涤脱硫后的烟气经除雾器除去带出的小液滴,再通过烟气换热器从烟囱排放。钠碱湿法烟气脱硫装置应由下列系统组成:①吸收碱液制备系统;②烟气系统;③吸收及氧化系统;④废水处理系统;⑤自控和在线监测系统;⑥其他系统。
新建脱硫装置的烟气设计参数宜采用锅炉最大连续工况(BMCR)、燃用设计燃料时的烟气参数,校核值宜采用锅炉经济运行工况(ECR)、燃用最大含硫量燃料时的烟气参数。已建电厂加装烟气脱硫装置时,其设计工况和校核工况宜根据脱硫装置入口处实测烟气参数确定,并充分考虑燃料的变化趋势。烟气脱硫装置的脱硫效率一般应不小于95%,主体设备设计使用寿命不低于30年,装置的可用率应保证在95%以上。
2.7.3.2 吸收碱液制备系统
制备系统的出力应按设计工况下消耗量的150%选择,且不小于100%校核工况下的消耗量。
由汽车运来的固体碱或液体碱经配制系统,配制到合适的浓度由碱液泵送入吸收塔。脱硫所需要的碱液量由锅炉负荷、烟气的SO2浓度和Na/S来联合控制;而需要制备的碱液量由碱液箱的液位来控制,浆液的浓度由密度计控制。
2.7.3.3 烟气系统
(1)脱硫增压风机
脱硫增压风机宜装设在脱硫装置进口处,其参数应按下列要求考虑。
①吸收塔的脱硫增压风机宜选用静叶可调轴流式风机,当机组容量为300MW及以下容量时,也可采用高效离心风机。当风机进口烟气含尘量能满足要求时,可采用动叶可调轴流式风机。
②当机组容量为300MW及以下时,宜设置一台脱硫增压风机,不设备用。对于800~1000MW机组,宜设置两台动叶可调轴流式风机。对于600~700MW机组,也可设置两台增压风机;当设置一台增压风机时应采用动叶可调轴流式风机。
③增压风机的风量应为锅炉满负荷工况下的烟气量的110%,另加不低于10℃的温度裕量;增压风机的压头应为脱硫装置在锅炉满负荷工况下并考虑10℃温度裕量下阻力的120%。
(2)烟气换热器
烟气系统宜装设烟气换热器,脱硫后烟气温度一般应达到80℃以上排放。烟气换热器下部烟道应装设疏水系统。可以选择管式换热器或回转式换热器,当原烟气侧设置降温换热器有困难时,也可采用在净烟气侧装设蒸汽换热器。
(3)挡板门
烟气脱硫装置宜设置旁路烟道。旁路挡板门的开启时间,应能满足脱硫装置故障,不引起锅炉跳闸的要求。烟道挡板宜采用带密封风的挡板,旁路挡板门也可采用压差控制不设密封风的单挡板门。
(4)工作过程
从锅炉来的热烟气经增压风机增压后,进入烟气换热器(GGH)降温侧冷却后进入吸收塔,向上流动穿过喷淋层,在此烟气被冷却到饱和温度,烟气中的SO2被碱液吸收。除去SOx及其他污染物的烟气经GGH加热至80℃以上,通过烟囱排放。
GGH是利用热烟气所带的热量,加热吸收塔出来的冷的净烟气;设计条件下没有补充热源时,可将净烟气的温度提高到80℃以上。GGH正常运行时,清洗系统每天需使用蒸汽吹灰三次;系统还配有一套在线高压水洗装置,约一个月使用一次。自动吹灰系统可保证GGH的受热面不受堵塞,保持净烟气的出口温度。
烟道上设有挡板系统,包括一台FGD进口原烟气挡板,一台FGD出口净烟气挡板和一台旁路烟气挡板。在正常运行时,FGD进口/出口挡板开启,旁路挡板关闭。在故障情况下,开启烟气旁路挡板门,关闭FGD进口/出口挡板,烟气通过旁路烟道绕过FGD系统直接排到烟囱。在BMCR工况下,烟道内任意位置的烟气流速不大于15m/s。
2.7.3.4 吸收氧化系统
(1)脱硫吸收塔
脱硫装置设计温度采用锅炉设计煤种BMCR工况下,从主机烟道进入脱硫装置接口处的运行烟气温度。新建机组同期建设的运行温度,一般为锅炉额定工况下,脱硫装置进口处运行烟气温度加50℃。300MW以上机组宜一炉一塔,200MW以下机组宜两炉一塔。
吸收塔宜采用钢结构,内壁采用衬胶或衬树脂鳞片或衬高镍合金板。塔外应设置供检修维护的平台和扶梯,设计荷载不应小于4000N/m2,平台宽度不小于1.2m,塔内不应设置固定式的检修平台。塔内与喷嘴相连的浆液管道应考虑检修维护措施,应考虑不小于500N/m2的检修荷载。
(2)烟气除雾器
吸收塔应装设除雾器,除雾器出口的雾滴浓度应不大于75mg/m3(标态)。除雾器应考虑检修维护措施,支撑梁的设计荷载应不小于1000N/m2。除雾器应设置水冲洗装置。
(3)循环碱液泵
循环碱液泵入口应装设滤网等防止固体物吸入的措施。当采用喷淋吸收塔时,吸收塔碱液循环泵宜按单元制设置;按照单元制设置时,应设仓库备用泵叶轮一套;按照母管制设置时,宜现场安装一台备用泵。
(4)氧化风机
氧化风机宜采用罗茨风机,也可采用离心风机。当氧化风机计算容量小于6000m3/h时,每座吸收塔应设置2台全容量或3台半容量的氧化风机;或每两座吸收塔设置3台全容量的氧化风机。当氧化风机计算容量大于6000m3/h时,宜配3台氧化风机。
(5)事故浆池
脱硫装置应设置一套事故碱池或事故碱液箱,容量宜不小于一座吸收塔最低运行液位时的碱池容量。
(6)工作过程
烟气由进气口(入口段为耐腐蚀、耐高温合金)进入吸收塔的吸收区,在上升(流速为3.2~4m/s)过程中与碱液逆流接触,烟气中所含的污染气体因此被清洗入碱液,与碱液发生化学反应而被脱除,处理后的净烟气经过除雾器除去水滴后进入烟道。
吸收塔内配有喷淋层,吸收了SO2的循环碱液落入反应池。反应池装有搅拌,氧化风机将氧化空气鼓入反应池,氧化空气被搅拌分散为细小的气泡并均布于浆液中。部分在喷淋区被氧化,其余部分的
在反应池中被氧化空气完全氧化。
吸收碱液被引入吸收塔内循环,使吸收液保持一定的pH值。在入口烟道装有事故冷却系统,事故冷却水由工艺水泵提供。
2.7.3.5 相关技术系统
(1)供水系统
从电厂供水系统引接至脱硫岛的水源进入岛内工艺水箱,通过泵提供脱硫岛和工艺水的需要。主要用于碱液制备用水、烟气换热器的冲洗水、除雾器冲洗水及所有碱液输送设备、输送管路、储存箱的冲洗水。冷却水使用后排至吸收塔排水坑回收利用。
(2)排放系统
脱硫岛内设置一个事故碱液箱,满足吸收塔检修和碱液排空的要求。事故碱液箱设返回泵,停运时需要进行冲洗,其冲洗水就近收集在集水坑内。
(3)压缩空气系统
脱硫岛仪表用气和杂用气由岛内设置的压缩空气系统提供,压力为0.85MPa左右,最低压力不应低于0.6MPa,仪用稳压罐和杂用储气罐应分开设置。
(4)自动控制系统
脱硫系统采用PLC或DCS控制系统,对烟气的压力、温度、流量、pH值等主要运行、控制参数,进行测量和实施监控,各主要设备运行状态、供水系统流程进行监控,把各个数据采集至操作站和控制室,确保整个工艺流程安全稳定运行,当设备和流程出现问题时,能进行故障报警,PLC或DCS系统能顺序控制,连锁保护,烟气负荷波动时能自动调节,确保除尘脱硫效果,使运行维护人员减至最少,自动产生当班运行日志,并记录储存历史数据,保证脱硫完全稳定,运行费用最低,达到最佳经济效益。
2.7.4 W-L工艺介绍
钠碱法用碱液(NaOH或Na2CO3)吸收了SO2后,不用石灰(石灰石)再生,而是直接将吸收液处理成副产品。吸收液钠碱液有循环使用和不循环使用两种。循环钠碱法典型的工艺是韦尔曼-洛德法(Wellman-Lord,W-L)。
该法采用的NaOH或Na2CO3只作开始时的吸收剂,在低温下吸收SO2后生成Na2SO3。在循环过程中起吸收作用的主要是Na2SO3,它吸收SO2后生成NaHSO3(主要)和Na2S2O5(次要)。将含Na2SO3、NaHSO3的吸收液进行加热再生,得到的亚硫酸钠结晶经固液分离,并用水溶解后返回吸收系统。因此W-L法分为吸收和解吸两个工序。
由于NaHSO3不稳定,受热即可分解,因此NaHSO3清液被送至再生器(结晶器)中,加热到约96℃使其分解,释放出SO2生成Na2SO3:
所产生的SO2气体被送入下一工段进行处理。亚硫酸钠则结晶析出,再经溶解后送回吸收塔循环使用。
亚硫酸钠-亚硫酸氢钠系统独特的性质,有可能使加热再生时热能耗量较大的情况得以改善。这是因为在亚硫酸钠-亚硫酸氢钠系统中,Na2SO3要比NaHSO3的溶解度小得多,若进入脱吸系统的溶液中NaHSO3的浓度比较高,当其NaHSO3转化为Na2SO3时,则有可能使Na2SO3在再生器内结晶出来,结果使溶液组成保持在较稳定的水平上,不至于出现液面上SO2分压的下降,从而可以降低热能耗量和保证较高的脱吸效率,因此,W-L法脱吸系统采用蒸发结晶工艺,使再生的亚硫酸钠从溶液中结晶出来。
脱吸过程是在强制循环蒸发结晶系统中进行的。为防止系统结垢和提高热交换器的效率,采用轴流泵作大流量循环。为了有效利用热能,采用双效蒸发系统。经过蒸发器浓缩的含亚硫酸钠结晶的溶液送至离心机,将Na2SO3结晶分离出来。返回蒸发结晶系统,Na2SO3结晶用水溶解后送入吸收系统。
由于氧化副反应而生成的Na2SO4的增加,会使吸收液面上SO2平衡分压升高,从而降低吸收率。因此当Na2SO4的浓度达到5%时,必须排出一部分母液,同时补充部分新鲜碱液。为降低碱耗,应尽力减少氧化,这是降低操作费用的关键之一。可用石灰法、冷冻法除去排出母液中的Na2SO4。
废水处理主要是向废水中加石灰以调节废水的pH值,使其中硫酸根沉淀下来,同时将废水中的铵离子转变成NH3再加以利用。处理后的废水可以作为锅炉的冲灰水。
该工艺的特点如下:
①系统设备较多,投资比一般的石灰石/石膏工艺要高,运行费用也较高,但该工艺在处理废渣上技术合理,能够回收元素硫、液体SO2或浓硫酸,是回收工艺中较成熟的一种;
②由于回收的副产品有一定的市场,当回收产品价格合适时,该工艺仍有一定的经济效益;
③工艺系统采用全封闭回路运行,吸收剂Na2SO3溶液可循环使用,故化学试剂消耗少;
④由于用Na2SO3溶液作吸收液,故吸收塔内不会产生结垢、堵塞问题;但吸收塔中有Na2SO4存在,故需要一个冲洗系统来除掉它;
⑤本工艺是目前能大规模处理烟气的一种回收工艺,适于处理高硫煤,脱硫率可达80%以上。