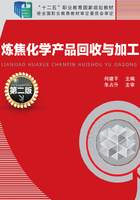
第二节 煤气在初冷器的冷却
出炭化室的荒煤气在桥管、集气管用循环氨水喷洒冷却后的温度仍高达80~85℃,且包含有大量煤焦油气和水蒸气及其他物质。由于煤焦油气和水蒸气很容易用冷却法使其冷凝下来,而且将它们先从煤气中除去,对回收其他化学产品,减少煤气体积,节省输送煤气所需动力,都是有利的,所以让煤气由集气管沿吸煤气主管流向煤气初冷器进一步冷却,煤气在沿吸煤气主管流向初冷器过程中,吸煤气主管还起着空气冷却器的作用,煤气可降温1~3℃。
煤气冷却和煤焦油气、水蒸气的冷凝,可以采用不同形式的冷却器。被冷却的煤气与冷却介质直接接触的冷却器,称为直接混合式冷却器,简称为直接冷却器或直接冷却(直冷);被冷却的煤气与冷却介质分别从固体壁面的两侧流过,煤气将热量传给壁面,再由壁面传给冷却介质的冷却器,称为间壁式冷却器,简称为间接冷却器或间接冷却(间冷)。由于冷却器的形式不同,煤气冷却所采取的流程也不同。
煤气冷却的流程可分为间接冷却、直接冷却和间冷-直冷混合冷却三种。上述三种流程各有优缺点,可根据生产规模、工艺要求及其他条件因地制宜地选择采用。中国目前广泛采用的是间接冷却。
一、煤气的间接冷却
1.立管式冷却器间接冷却工艺流程
如图2-3所示为立管式煤气初冷工艺流程。焦炉煤气与循环氨水、冷凝煤焦油等沿吸煤气主管先进入气液分离器,煤气与煤焦油、氨水、煤焦油渣等在此分离。分离下来的氨水和煤焦油一起进入机械化(煤)焦油氨水澄清槽(习惯称机械化焦油氨水澄清槽,下同),利用密度不同经过静置澄清分成三层:上层为氨水(密度为1.01~1.02kg/L),中层为煤焦油(密度为1.17~1.20kg/L),下层为煤焦油渣(密度为1.25kg/L)。沉淀下来的煤焦油渣由刮板输送机连续刮送至漏斗处排出槽外。煤焦油则通过液面调节器流至煤焦油中间槽,由此泵往煤焦油储槽,经初步脱水后泵往煤焦油车间。氨水由澄清槽上部满流至氨水中间槽,再用循环氨水泵送回焦炉集气管以冷却荒煤气。这部分氨水称为循环氨水。

图2-3 立管式煤气初冷工艺流程
1—气液分离器;2—煤气初冷器;3—煤气鼓风机;4—电捕焦油器;5—冷凝液槽;6—冷凝液液下泵;7—鼓风机水封槽;8—电捕焦油器水封槽;9—机械化焦油氨水澄清槽;10—氨水中间槽;11—事故氨水槽;12—循环氨水泵;13—煤焦油泵;14—煤焦油储槽;15—煤焦油中间槽;16—初冷冷凝液中间槽;17—冷凝液泵
经气液分离后的煤气进入数台并联立管式间接冷却器(初冷器),用水间接冷却,煤气走管间,冷却水走管内。从各台初冷器出来的煤气温度是有差别的,汇集在一起后的煤气温度称为集合温度,这个温度依生产工艺的不同而有不同的要求:在生产硫酸铵系统中,要求集合温度低于35℃,在水洗氨生产系统中,则要求集合温度低于25℃。随着煤气的冷却,煤气中绝大部分煤焦油气、大部分水汽和萘在初冷器中被冷凝下来,萘溶解于煤焦油中。煤气中一定数量的氨、二氧化碳、硫化氢、氰化氢和其他组分溶解于冷凝水中,形成了冷凝氨水。
煤焦油和冷凝氨水的混合液称为冷凝液。冷凝氨水中含有较多的挥发铵盐[NH3与H2S、HCN、H2CO3形成的铵盐,如NH4HS、NH4CN、NH4HCO3等],固定铵盐[如NH4Cl、NH4SCN、(NH4)2SO4和(NH4)2S2O3等]的含量较少。当其溶液加热至100℃即分解的铵盐为挥发铵盐,需加热到220~250℃或有碱存在的情况下才能分解的铵盐叫固定铵盐。循环氨水中主要含有固定铵盐,在其单独循环时,固定铵盐含量可高达30~40g/L。为降低循环氨水中固定铵盐的含量,以减轻对煤焦油蒸馏设备的腐蚀和改善煤焦油的脱水、脱盐操作,大多采用两种氨水混合的分离流程,混合氨水固定铵盐含量可降至1.3~3.5g/L。如图2-3所示,冷凝液自流入冷凝液槽,再用泵送入机械化焦油氨水澄清槽,与循环氨水混合澄清分离。分离后所得剩余氨水送去蒸氨,蒸氨废水还应经生化处理后才能外排。
由管式初冷器出来的煤气尚含有1.5~2g/m3的雾状煤焦油,被鼓风机抽送至电捕焦油器除去其中绝大部分煤焦油雾后,送往下一道工序。
当冷却煤气用的冷却水为直流水时(水源充足的地区),初冷器后的热水直接排放(或用作余热水供热)。如为循环水时,则将热水送到凉水架冷却后循环使用,冷却后的温度随地区、季节不同而异,在冬季自然冷却,在夏季靠轴流风机强制冷却,一般至25~33℃,再送回初冷器。
上述煤气间接初冷流程适用于生产硫酸铵工艺系统,当水洗氨生产时,为使初冷后煤气集合温度达到20℃左右,宜采用两段初冷。
两段初冷可采用具有两段初冷功能的初冷器,将其中前四个煤气通道作为第一段,后两个煤气通道作为第二段。在第一段用32℃循环冷却水将煤气冷却到约45℃,第二段用18℃低温水将煤气冷却到25℃以下。
也可采用初冷器并串联实现煤气两段初冷。例如用“二串一”。即煤气先通过作为第一段的两台并联的初冷器,再汇合通过作为第二段的一台初冷器,简称为“二串一”,第一段用循环水冷却,第二段用低温水冷却,可将煤气冷却到25℃以下。或用“三串一”工艺。
2.横管式初冷器间接初冷工艺流程
横管式煤气初冷器冷却,煤气走管间,冷却水走管内。水通道分上下两段(或三段:热水段、循环水段、低温水段),上段用循环水冷却,下段用制冷水冷却,将煤气温度冷却到22℃以下。横管式初冷器煤气通道,一般分上、中、下三段,上段用循环氨水喷洒,中段和下段用冷凝液喷洒,根据上、中、下段冷凝液量和热负荷的计算可知:上段和中段冷凝液量约占总量的95%,而下段冷凝液量仅占总量的5%;从上段和中段流至下段的冷凝液由45℃降至30℃的显热及喷洒的冷凝液冷却显热,约占总热负荷的60%;下段冷凝液的冷凝潜热及冷却至30℃的显热,约占总热负荷的20%;下段喷洒冷凝液的冷却显热,约占总热负荷的20%。由此可见,上段和中段喷洒的氨水和冷凝液全部从下段排出,显著地增加了下段负荷。为此推荐如图2-4所示的横管式煤气初冷工艺流程。

图2-4 横管式煤气初冷工艺流程
该流程上段和中段冷凝液从隔断板经水封自流至氨水分离器,下段冷凝液经水封自流至冷凝液槽。下段冷凝液主要是轻质煤焦油,作为中段和下段喷洒液有利于洗萘。喷洒液不足时,可补充煤焦油或上段和中段的冷凝液。该流程最突出的优点是横管式初冷器下段的热负荷显著降低,低温冷却水用量大为减少。
目前焦化厂广泛采用半负压回收系统横管式初冷器间接冷却煤气工艺流程,如图2-5所示。从焦炉来的煤焦油氨水与煤气的混合物约80℃入气液分离器,煤气与煤焦油氨水等在此分离。分离出的粗煤气并联进入三台横管式初冷器,当其中任一台检修或吹扫时,其余两台基本满足正常生产时的工艺要求。初冷器分上、下两段,在上段用循环水将煤气冷却到45℃,然后煤气入初冷器下段与制冷水换热,煤气被冷却到22℃,冷却后的煤气并联进入两台电捕焦油器,当一台电捕焦油器检修或冲洗时,另一台电捕焦油器基本满足正常生产时的工艺要求。捕集煤焦油雾滴后的煤气送煤气鼓风机进行加压,煤气鼓风机一开一备,加压后煤气送往脱硫及硫回收工段。

图2-5 半负压横管式煤气初冷工艺流程
1—气液分离器;2—横管初冷器;3—电捕焦油器;4—鼓风机;5—机械化焦油氨水澄清槽;6—机械化焦油澄清槽; 7—煤气水封槽;8—上段冷凝液液封槽;9—上段冷凝液循环泵;10—下段冷凝液循环泵;11—下段冷凝液液封槽; 12—电捕水封槽;13—液下泵;14—地下放空槽;15—煤焦油泵;16—循环氨水泵;17—循环氨水中间槽; 18—循环氨水事故槽;19—剩余氨水槽;20—剩余氨水泵;21—剩余氨水中间槽;22—剩余氨水 中间槽泵;23—除煤焦油器;24—高压氨水;25—氮气加热器;26—鼓风机水封槽
为了保证初冷器的冷却效果,在上、下段连续喷洒煤焦油氨水混合液。此外,在其顶部用热氨水不定期冲洗,以清除管壁上的煤焦油、萘等杂质。
初冷器的煤气冷凝液由初冷器上段和下段分别流出,并分别进入各自的初冷器水封槽,初冷器水封槽的煤气冷凝液分别溢流至上、下段冷凝液循环槽,再分别由上、下段冷凝液循环泵送至初冷器上、下段喷淋洗涤除萘及煤焦油,如此循环使用。下段冷凝液循环槽多余的冷凝液溢流至上段冷凝液循环槽,上段冷凝液循环槽多余部分由泵抽送至机械化焦油氨水澄清槽。
从气液分离器分离的煤焦油氨水与煤焦油渣并联进入三台机械化焦油氨水澄清槽。澄清后分离成三层,上层为氨水,中层为煤焦油,下层为煤焦油渣。分离的氨水并联进入两台循环氨水槽,然后用循环氨水泵送至焦炉冷却荒煤气及初冷器上段和电捕焦油器间断吹扫喷淋使用。多余的氨水去剩余氨水槽,用剩余氨水泵送至脱硫工段进行蒸氨。分离的煤焦油靠静压流入机械化焦油澄清槽,进一步进行煤焦油与煤焦油渣的沉降分离,煤焦油用煤焦油泵送至酸碱油品库区煤焦油槽。分离的煤焦油渣定期送往煤场掺入煤中炼焦。
半负压横管式间接初冷工艺与上述间接初冷工艺流程的主要区别之一,是将电捕焦油器置于鼓风机之前。这样配置的优点是:煤气初冷器冷却过程中生成的煤焦油雾,可在电捕焦油器中彻底清除,为鼓风机对煤气加压以及其后的化学产品回收创造良好的条件。若将鼓风机放在初冷器与电捕焦油器之间,本来已经液化成雾滴的煤焦油,则因煤气被压缩而又升温过程中,又汽化为蒸气,在管道和以后工序中遇到冷却则又会冷凝,造成堵塞。一般新建焦化厂均采用如图2-5所示的配置工艺。
3.剩余氨水量的计算
在氨水循环系统中,由于加入配煤水分和炼焦时产生的化合水,使氨水量增多而形成所谓的剩余氨水。这部分氨水从循环氨水泵出口管路上引出,送去蒸氨。其数量可由下列估算确定。
(1)原始数据
装入煤量/(t湿煤/h) 150 配煤水分/% 8.5
干煤气产量/(m3/t干煤) 340 化合水(干煤)/% 2
初冷器后煤气温度/℃ 30
(2)计算 如图2-6所示,为循环氨水量,设于集气管喷洒冷却煤气时蒸发了2.6%,剩余部分即为由气液分离器分离出来的氨水量
。离开气液分离器的煤气中所含的水汽量
,即煤气带入集气管的水量
和循环氨水蒸发部分之和。初冷器后煤气带走的水量为
,
即为冷凝水量
。从冷凝水量
中减去需补充的循环氨水量
(相当于蒸发部分),即得剩余氨水量
。

图2-6 煤气初冷系统的水平衡
1—集气管;2—气液分离器;3—初冷器;4—机械化焦油氨水澄清槽
从以上分析可见,如图2-6所示虚线围成的范围,作水的物料衡算有:
则送去加工的剩余氨水量,即为
与
之差。
式中 35.2——每m3煤气在30℃时经水蒸气饱和后的水汽含量,g(为简化计算,由附表1查得)。
则剩余氨水量为
显然,剩余氨水量取决于配煤水分和化合水的数量以及煤气初冷后集合温度和压力的高低。
煤气初冷的集合温度和负压不宜偏高,否则会带来下列问题。
①煤气中水汽含量增多,体积变大,致使鼓风机能力不足,影响煤气正常输送。
②煤焦油气冷凝率降低,初冷后煤气中煤焦油含量增多,影响后续工序生产操作。
③在初冷器内,煤气冷却到一定程度(一般认为55℃)以下,萘蒸气凝结呈细小薄片晶体析出,可溶入煤焦油中,温度越低,煤气中萘蒸气含量也越少,当集合温度高时,煤气中含萘量将显著增大。根据现场资料,甚至煤气中萘含量比同温下萘蒸气饱和含量高1~2倍。这些未分离除去的萘会造成煤气管道和后续设备的堵塞,增加洗萘系统负荷,给洗氨、洗苯带来困难。
由上述可见,在煤气初冷操作中,必须保证初冷器后集合温度不高于规定值,并尽可能地脱除煤气中的萘。
焦炉煤气是多组分混合物。其中的H2、CH4、CO、CO2、N2、CnHm(按乙烯计)、O2等,在常温条件下始终保持气态,而且在其后的冷却、加压及回收化学产品过程中,其总物质的量的流量不变,故这部分气体称为干煤气。又因在标准状态下1kmol理想气体的体积为22.4m3,故以m3/h作为干煤气的流量的计量单位时,干煤气的体积流量也是不变的。与干煤气不同的是水蒸气、粗苯气、煤焦油气以及NH3、H2S、HCN等,在煤气冷却过程中,有的会冷凝成液体溶于水,或在化学产品回收中采用吸收的方法将其从煤气中分离出去,这些成分是可变的,都不属于干煤气的成分,在煤气中的含量,常以g/m3为单位计量。
二、煤气的直接冷却
煤气的直接冷却,是在直接式煤气初冷塔内由煤气和冷却水直接接触传热完成的。中国在20世纪80年代前有些小型焦化厂大都用直接初冷却流程,如图2-7所示。

图2-7 煤气直接初冷工艺流程
1—气液分离器;2—煤焦油盒;3,4—直接式煤气初冷塔;5—罗茨鼓风机;6—电捕焦油器;7—水封槽;8—煤焦油泵;9—循环氨水泵;10—焦油氨水澄清池;11—煤焦油槽;12—煤焦油池;13—煤焦油泵;14—初冷循环氨水澄清池;15—初冷循环氨水冷却器;16—初冷循环氨水泵;17—剩余氨水泵
由图2-7可见,由焦炉来的80~85℃的煤气,经过气液分离器进入并联的直接式煤气初冷塔,用氨水喷洒冷却到25~28℃,然后由鼓风机送至电捕焦油器,电捕除焦油雾后,将煤气送往回收氨工段。
由气液分离器分离出的氨水、煤焦油和煤焦油渣,经煤焦油盒分出煤焦油渣后流入焦油氨水澄清池,从澄清池出来的氨水用泵送回集气管喷洒冷却煤气。澄清池底部的煤焦油流入煤焦油池,然后用泵抽送到煤焦油槽,再送往煤焦油车间加工处理。煤焦油盒底部的煤焦油渣由人工捞出。
初冷塔底部流出的氨水和冷凝液经水封槽进入初冷循环氨水澄清池,与洗氨塔来的氨水混合并在澄清池与煤焦油进行分离。分离出来的煤焦油与上述煤焦油混合。澄清后的氨水则用泵送入冷却器冷却后,送至初冷塔循环使用。剩余氨水则送去蒸氨或脱酚。
从初冷塔流出的氨水,由氨水管路上引出支管至煤焦油氨水澄清池,以补充焦炉用循环氨水的蒸发损失。
煤气直接冷却,不但冷却了煤气,而且具有净化煤气的良好效果。据某厂实测生产数据表明,在直接式煤气初冷塔内,可以洗去90%以上的煤焦油,80%左右的氨,60%以上的萘,以及约50%的硫化氢和氰化氢。这对后面洗氨洗苯过程及减少设备腐蚀都有好处。
同煤气间接冷却相比,直接冷却还具有冷却效率较高,煤气压力损失小,基建投资较少等优点。但也具有工艺流程较复杂,动力消耗较大,循环氨水冷却器易腐蚀、易堵塞,各澄清池污染严重,大气环境恶劣等缺点,因此目前大型焦化厂还很少单独采用这种煤气直接冷却流程。在以人为本,建设和谐社会的今天,这类严重污染环境的工艺已不允许使用。
国外一些大型焦化厂也有采用煤气直接冷却流程的,空喷塔和冷却器等采取防腐措施,各澄清池皆配有顶盖,排放气体集中洗涤。空喷塔用经过冷却的氨水煤焦油混合液喷洒。在冷却煤气的同时,还将煤气中夹带的部分萘除去。由初冷塔流出来的冷凝液进入专用的焦油氨水澄清槽进行分离,澄清后的氨水供循环使用,并将多余部分送去蒸氨加工。
三、间接冷却和直接冷却结合的煤气初冷
煤气的直接冷却是在直接冷却塔内,由煤气和冷却水(经冷却后的氨水焦油混合液)直接接触传热而完成的。此法不仅冷却了煤气,且具有净化煤气效果良好、设备结构简单、造价低及煤气阻力小等优点。间冷、直冷结合的煤气初冷工艺即是将两者优点结合的方法,在国内外大型焦化厂已得到采用。
自集气管来的荒煤气几乎为水蒸气所饱和,水蒸气热焓约占煤气总热焓的94%,所以煤气在高温阶段冷却所放出的热量绝大部分为水蒸气冷凝热,因而传热系数较高;而且在温度较高时(高于52℃),萘不会凝结造成设备堵塞。所以,煤气高温冷却阶段宜采用间接冷却。而在低温冷却阶段,由于煤气中水汽含量已大为减少,气体对壁面间的对流传热系数低,同时萘的凝结也易于造成堵塞。所以,此阶段宜采用直接冷却。
间冷和直冷结合的煤气初冷流程如图2-8所示,由集气管来的82℃左右的荒煤气经气液分离器分离出煤焦油氨水后,进入横管式间接冷却器被冷却到50~55℃,再进入直冷空喷塔冷却到25~35℃。在直冷空喷塔内,煤气由下向上流动,与分两段喷淋下来的氨水煤焦油混合液逆流密切接触而得到冷却。

图2-8 间冷和直冷结合的煤气初冷工艺流程
1—气液分离器;2—横管式间接冷却器;3—直冷空喷塔;4—液封槽;5—螺旋换热器;6—机械化焦油氨水澄清槽;7—氨水槽;8—氨水储槽;9—煤焦油分离器;10—煤焦油中间槽;11—煤焦油储槽
聚集在塔底的喷洒液及冷凝液沉淀出其中的固体杂质后,其中用于循环喷洒的部分经液封槽用泵送入螺旋板换热器,在此冷却到25℃左右,再压送至直冷空喷塔上、中两段喷洒。相当于塔内生成的冷凝液量的部分混合液,由塔底导入机械化焦油氨水澄清槽,与气液分离器下来的氨水、煤焦油以及横管初冷器下来的冷凝液等一起混合后进行分离。澄清的氨水进入氨水槽后,泵往焦炉喷洒,剩余氨水经氨水储槽泵送脱酚及蒸氨装置。初步澄清的煤焦油送至煤焦油分离槽除去煤焦油渣及进一步脱除水分,然后经煤焦油中间槽泵入煤焦油储槽。
直冷空喷塔内喷洒用的洗涤液在冷却煤气的同时,还吸收硫化氢、氨及萘等,并逐渐为萘饱和。采用螺旋板换热器来冷却闭路循环的洗涤液,可以减轻由于萘的沉积而造成的堵塞。
在采用氨水混合分离系统时,循环氨水中挥发氨的浓度相对增加,而循环氨水的温度又高,因而氨的挥发损失将增大。为防止氨的挥发损失及减少污染,澄清槽和液体槽均应采用封闭系统,并设置排气洗净塔,以净化由槽内排出的气体。