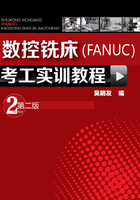
1.4 数控铣床的功能特点
1.4.1 数控铣床的结构和主要技术参数
(1)数控铣床的主要用途和特点
本书所采用的数控铣床为济南机床厂生产的J1VMC40M型立式数控铣床。机床总体结构与组成如图1-1所示。

图1-1 机床总体结构与组成
1—Z轴伺服电动机;2—立柱;3—电气箱;4—总电源开关;5—主轴头;6—鞍座;7—Y轴伺服电动机;8—底座;9—切削液泵;10—主轴电动机;11—松刀汽缸;12—控制箱;13—全护罩钣金;14—主轴;15—工作台;16—X轴伺服电动机;17—水箱
本机床具有3个可以联动的数控轴:X、Y、Z,工件在一次装夹后,可按照预先编制好的程序自动完成铣、镗、铰、攻螺纹等多种工序的加工。由于坐标可以自动精确定位,所以无需钻、镗模具,即可以直接镗孔并保证孔距的加工精度(质量)和一批工件尺寸的同一性(质量稳定),节省了工艺装备,缩短了生产准备周期,大幅降低了成本,获得了好的经济效益。利用本数控机床的3轴联动功能,还能加工出三维空间的复杂型面,这是普通铣床所无法胜任的。
本机床适用于中小型板件、盘件、壳体件、模具等复杂零件的多品种中小批量轮番生产等加工。由于加工的高质量和高效率,它可以广泛适用于一切需要机械加工的行业。
X轴行程加长至800mm,适宜对机床X轴需要大行程的需求。配置了FANUC 0i Mate-MB型数控系统,由于系统带有AI前瞻功能,因此适宜复杂轮廓零件加工的要求。机床整体刚性好。由于X、Y、Z三方向全部采用优质铸铁淬硬滑动导轨,机床具有良好的切削吸振性和使用寿命。机床高速性能好,工作稳定可靠,定位精度和重复定位精度高,不需要模具就能确保零件的加工精度,减少辅助时间,提高了劳动生产效率。
本机床的设计广泛采用了最新发展的数控技术和机械结构,具有以下特点。
① X、Y、Z三个方向全部采用高频淬硬滑动导轨支承,其中主轴箱进给方向(Z向)采用重锤平衡。
② 立柱固定、工作台十字滑台移动式布局设计大大提高了机床接触刚度。
③ 采用电、气作为动力源,由于无液压系统,减少了噪声、发热和振动,提高了可维修性,也避免了由于液压系统的渗漏而可能造成的环境污染。
④ 对X、Y、Z三个方向的丝杠进行了预拉伸,确保了长时间工作下进给精度的保持性。
⑤ 床座、立柱、十字滑台等基础大件,利用有限元法进行设计,采用密筋格箱性结构,具有非常高的刚性。
(2)数控铣床的主要组成部分
数控铣床一般由铣床主机、控制部分、驱动装置等部分组成。
① 铣床主机。它是数控铣床的机械部件,包括床身、主轴箱、工作台和进给机构等。
② 控制部分(CNC装置)。它是数控铣床的控制核心,本书所讲的CNC系统为FANUC 0i系统。
③ 驱动装置。它是数控铣床执行机构的驱动部件,包括主轴电动机和进给伺服电动机等。
④ 辅助装置。它是指数控铣床的一些配套部件,包括液压装置、气动装置、冷却系统、润滑装置和排屑装置等。
(3)机床结构简介
机床由床身、工作台、立柱、主轴部件、进给部件、冷却、润滑及电气等部分组成。
① 主轴箱。
a.主轴通过齿形带由主轴电动机直接驱动。主轴采用我国台湾产高性能数控铣床专用主轴单元,主轴由4只FAG产P4级轴承支承。主轴单元最高许用转速为8000r/min,主轴单元为四瓣爪(首选)式拉紧(或钢球式拉紧),拉刀力为800kgf±50kgf。主轴前后轴承均采用高精度组合向心推力球轴承,轴承采用油脂润滑,依靠非接触式迷宫套密封。
b.刀具自动夹紧机构。主轴内部有刀柄自动夹紧机构,它由拉杆及头部的拉爪或钢球和碟形弹簧等组成。夹紧时,碟形弹簧使拉杆处于上端,松刀时,气缸的活塞杆下移并将推拉杆下移,使头部的钢球将刀柄放开,行程开关用于发出夹紧和松动时的位置状态信号。
注意:为防止主轴旋转时,汽缸活塞杆与拉杆端面摩擦,开机前必须接通好气源,活塞杆上移,使两端部之间留有一定的间歇。
② 进给轴。本机床共有X、Y、Z三个进给轴,工作台沿十字滑台导轨的运动方向为X向,其驱动轴定义为X轴,十字滑台沿床身导轨的运动方向为Y向,其驱动轴定义为Y轴,主轴箱沿立柱导轨的运动方向为Z向,其驱动轴定义为Z轴。X、Y、Z三个进给轴的丝杠结构形式相同,均采用预拉伸的结构形式,形成高刚性的进给轴。进给电动机的驱动扭矩通过联轴器传递给丝杠,然后由螺母带动工作台、十字滑台、主轴箱沿X、Y、Z三个方向分别移动。
③ 工作台。工作台面为900mm×400mm,台面上有3个18T形槽,工作台可沿X轴及Y轴两个方向移动。
④ 润滑。X、Y、Z轴滑动导轨及滚珠丝杠的润滑方式为油润滑,由集中式润滑泵不停地把20#机械油打至每个润滑点。操作时注意以下两点。
a.及时把润滑油加至油位线,当油位低于最低限时,机床报警。
b.不能选用锭子油及含低级酮、芳香烃的润滑油。
⑤ 气动系统。在机床立柱侧面装有气动单元装置。本机床气动装置的设计工作压力为5.5bar,因此气源的压力至少应恒定在6bar。尽管在气动单元内装有过滤装置来保护整个回路,但气源仍需要除去水分和灰尘,并用5μm的过滤器进行过滤。
⑥ 冷却系统。冷却装置采用外装式,即水泵安置在水箱中,有接头将水泵出口管线引出,经过管线、阀门至主轴箱上喷水嘴。
(4)数控铣床的主要技术参数
数控机床的技术参数反映了机床的性能及加工范围,J1VMC40M型立式数控铣床的主要技术参数如下。
① 工作台面积(长×宽):900mm×400mm。
② 工作台T形槽×槽数:18H7×3。
③ 工作台T形槽间距:125mm。
④ 工作台最大承重:500kg。
⑤ 工作台面距地面高度:1000mm。
⑥ 基准T形槽:中间T形槽。
⑦ 工作台X轴行程:800mm。
⑧ 工作台Y轴行程:500mm。
⑨ 主轴箱Z轴行程:500mm。
⑩ 主轴头端面至工作台面的距离:100~600mm。
主轴锥孔:BT40。
主轴电动机功率:7.5kW。
主轴转速范围:80~8000r/min(AC伺服)。
X、Y、Z轴快速移动速度:16m/min、16m/min、12m/min。
X、Y、Z轴进给电动机功率:1.2kW、1.8kW、1.8kW。
冷却泵电动机功率:0.55kW。
刀具允许最大直径:100mm。
刀具允许最大长度:200mm。
最大端铣刀直径:100mm。
最大刀具重量:5kg。
刀柄号:MAS-BT40/LDA-40BT。
拉钉号:MAS-LDA-40BT型。
定位精度:0.01mm。
重复定位精度:0.005mm。
主机外形尺寸(长×宽×高):2768mm×2400mm×2610mm。
机床净重:5500kg。
气源压力:6bar(1bar=0.1MPa)。
电源:3相380V/50Hz。
电源容量:25kV·A。
1.4.2 数控铣削加工的特点及应用
(1)数控铣削加工的特点
数控铣床与普通铣床比较有以下特点。
① 具有高度柔性。
② 加工精度高,质量稳定。
③ 生产率高。
④ 可大大减轻工人的劳动强度。
(2)数控铣削加工的应用
数控铣床应用十分广泛,可以加工各种平面轮廓和立体轮廓的零件,如凸轮、模具和叶片等;还可以进行钻、扩、铰、攻螺纹和镗孔等。根据数控铣床的特点,从铣削加工角度来考虑,适合数控铣削的主要加工对象有以下几类。
① 平面类零件。加工面平行或垂直于水平面,或加工面与水平面的夹角为定角的零件为平面类零件(如图1-2所示)。目前在数控铣床上加工的绝大多数零件属于平面类零件。平面类零件的特点是各个加工面是平面,或可以展开成平面。例如图1-2中的曲线轮廓面M和正圆台面N,展开后均为平面。

图1-2 平面类零件
平面类零件是数控铣削加工对象中最简单的一类零件,一般只需用三坐标数控铣床的两坐标联动(即两轴半坐标联动)就可以把它们加工出来。
② 变斜角类零件。加工面与水平面的夹角呈连续变化的零件称为变斜角类零件,这类零件多为电机零件,如飞机上的整体梁、框、椽条与肋等;此外还有检验夹具与装配型架等也属于变斜角类零件。如图1-3所示为飞机上的一种变斜角梁椽条,该零件的上表面在第②肋至第⑤肋的斜角,从3°10'均匀变化为2°32',从第⑤肋至第⑨肋再均匀变化为1°20',从第⑨肋到第肋又均匀变化为0°。

图1-3 变斜角类零件
变斜角类零件的变斜角加工面不能展开为平面,但在加工中,加工面与铣刀圆周接触的瞬间为一条线。最好采用四坐标或五坐标数控铣床摆角加工,在没有上述机床时,可采用三坐标数控铣床,进行两轴半坐标近似加工。
③ 曲面类零件。加工面为空间曲面的零件称为曲面类零件,如模具、叶片、螺旋桨等,曲面类零件的加工面不能展开为平面,加工时,加工面与铣刀始终为点接触。加工曲面类零件一般采用三坐标数控铣床。当曲面较复杂、通道较狭窄、会伤及相邻表面及需刀具摆动时,要采用四坐标或五坐标铣床。
1.4.3 数控铣削加工的步骤
在数控铣床上,把被加工零件的工艺过程(如加工顺序、加工类别)、工艺参数(如主轴转速:进给速度、刀具尺寸)以及刀具与工件的相对位移,用数控语言编写成加工程序单,然后将程序输入到数控装置,数控装置便根据数控指令控制机床的各种操作和刀具与工件的相对位移,当零件加工程序结束时,机床会自动停止,加工出合格的零件。其工作原理如图1-4所示。

图1-4 数控铣床的工作原理