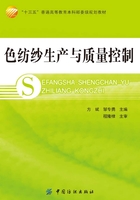
第一节 色纺纱及其色纺产业
一、色纺纱定义
色纺纱一般是指经特定工序混和加工纺制而成含有两种及两种以上不同色泽纤维的纱线,纱线具有特定的外观色彩风格。
色纺纱又称有色纤维纺纱。纺纱前所用的纤维原料中一部分或全部通过染色或原液着色,再经过混棉机组充分均匀的混和,纺制成具有独特混色效果的色纱。纤维预先经过染色纺成的纱线,在后道加工过程中一般不需再染色加工,既缩短了加工工序,又减少了对环境的污染。色纺纱生产特点是品种多、批量小、变化大、翻改频繁。对车间生产管理,尤其是分批、分色、标识等划分区域的现场管理有严格的要求,以减少杜绝混批、混色、异色飞毛、错特等质量事故的发生。因此,色纺纱在投料生产前要充分考虑品质要求,做到合理安排,严格控制各道质量,减少色偏、布面破洞、横档、阴影、异色纤维、棉结、疵点等质量问题。
色纺纱的混和工序通常有四类形式。第一类是传统混和工序,是指棉包混棉,将一种及以上不同颜色的散纤维经预混、开清棉工序进行混和,以确保本白纤维与有色纤维的充分混和,具有较均匀的混和效果,但原料混和比例控制得不够准确,且清车困难。第二类是棉条混棉,即将本白棉条与有色或含有染色散纤维的棉条,或筒子纱、长丝进行混和,该方法能较准确地控制原料混和比,但混棉的立体效果较前者稍差,混和的均匀程度不够,不利于加工高档的色纺纱,因有色混和不均匀易产生色差。第三类是选择不同混色风格的条子与粗纱或长丝或筒子纱在粗纱工序进行混和;第四类是选择不同混色风格的粗纱或条子与粗纱或长丝或筒子纱在细纱工序进行混和。不同的混和方式与工序将使色纺纱具有不同的结构与色彩风格效应。
色纺纱不同于筒子纱染色,也不是对100%的染色纤维进行加工开发,而是在纺纱过程中混入部分染色纤维。一般情况下,浅色品种中染色纤维仅占10%,约90%的纤维是不需染色的。相比较传统工艺,色纺纱更低碳、节能、绿色环保。色纺纱采用“先染色,后纺纱”的加工模式,改变了“先纺纱,后染色”的传统生产方式。其织成的织物无需再进行染整加工,既缩短了加工工序又减少了环境污染,相对而言是一种环保节能产品。由色纺纱构成的织物具有三维立体混色风格,色彩自然而又含蓄,朦胧感强,能满足现代消费者个性化、多样化、时尚化的服饰消费需求,具有较强的产品竞争力,符合主流发展趋势,市场需求量巨大。
二、色纺产业发展及其规模
(一)色纺起源与发展
色纺最早应用于毛纺,起源于19世纪的欧洲,然后慢慢在棉纺、麻纺等行业推广运用,直至20世纪中叶,转移至日本、韩国和中国台湾。中国大陆的棉纺色纺在20世纪90年代初才从韩国等地引入,起步较晚,但发展速度较快,尤其在长三角地区(浙江、江苏、上海),原因在于棉纺企业凭借充足的劳动力、快捷的交货、大批量的供货能力等优势,现已在国内迅猛扩展与壮大,逐渐占据了国际市场的主导地位。因此,可以说色纺起源于欧洲,发展于日韩,兴盛于中国。
色纺纱因为产品的时尚性、环保性和科技性,对其需求增长速度逐年呈上升趋势,随着消费结构的升级,将以高出普通纱线两倍的速度增长。未来随着人们服装品位的提升,以及对自然色的追求,色纺纱在纺织面料中的应用比例将逐步得到提高,具有广阔的发展空间。
(二)色纺产业规模
色纺纱行业尽管在我国起步较晚,但作为纺织行业中的一个新兴分支行业,目前得到了超常发展。色纺纱生产能力从初期10万锭左右增加到2009年的约500万锭,占全部纺纱产能的4.5%左右,成为世界色纺纱市场的主导者。目前,我国色纺纱生产产能已增加至600万锭,其中大量产能集中于浙江、江苏两地,如全球色纺领军企业华孚集团、百隆集团。色纺纱目前在纱线产业中还属于小品种,国际上中高档色纺纱生产规模大约为200万锭,其中,国内约170万锭,海外不到30万锭。据诺美咨询研究报告称,目前,色纺纱在服装面料领域的应用比例分别为:毛衫25%、针织面料15%、梭织面料3%左右。毛衫的应用相对成熟,外衣化是增长的主要方向;针织面料领域的发展势头较好,运动服装面料、家居服面料、户外服装面料是其主要的增长点;机织面料领域的应用尚处在起步阶段,增长潜力巨大,特别是家用纺织面料、衬衫及休闲装面料领域的应用。如果未来纱线产业形成色织、布匹染色、色纺三分天下的格局,色纺产业规模将超过2000万纱锭。
目前,色纺行业除华孚集团、百隆集团等纺织企业外,总体呈现产能规模不大的局势。其主要原因在于:色纺纱工艺复杂,进入门槛较高,对企业的经营、技术、管理水平、供给能力等综合能力要求较高;生产过程复杂,国内多数企业无法生产,供给有限,且对企业的资金实力和规模有较高的要求,因为批量小,品种多,当产量较小时单位产品的成本较高,无产品成本优势,导致市场份额扩展受限。不过,进入壁垒高则有利于现有企业的良性发展。由于普通纺纱竞争越来越激烈,一些普通纺纱企业会转型为色纺企业,走上色纺这条路的企业会越来越多。有研发能力的色纺企业将带来差别化的产品,最终会引领色纺行业向前发展。