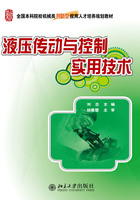
2.2 液压执行元件
2.2.1 液压缸
液压缸是液压系统中的执行元件之一,它是一种把液体的压力能转换成机械能,以实现直线往复运动或往复摆动的能量转换装置。
1.液压缸的分类、特点和职能符号
液压缸的分类、职能符号及特点见表2-2。
表2-2 液压缸的分类、职能符号及特点

2.活塞式液压缸
活塞式液压缸根据其使用要求的不同可分为双杆式和单杆式两种。
1)双杆式活塞缸
活塞两端都有一根直径相等的活塞杆伸出的液压缸称为双杆式活塞缸,它一般由缸体、缸盖、活塞、活塞杆和密封件等零件构成。根据安装方式的不同,可分为缸筒固定式和活塞杆固定式两种。
图2.17(a)所示的为缸筒固定式的双杆活塞缸。

图2.17 双杆式活塞缸
它的进、出口布置在缸筒两端,活塞通过活塞杆带动工作台移动,当活塞的有效行程为l时,整个工作台的运动范围为3l,所以机床占地面积大,一般适用于小型机床。当工作台行程要求较长时,可采用图2.17(b)所示的活塞杆固定的形式,这时缸体与工作台相连,活塞杆通过支架固定在机床上,动力由缸体传出。这种安装形式中,工作台的移动范围只等于液压缸有效行程l的两倍(2l),因此占地面积小。进出油口可以设置在固定不动的空心的活塞杆的两端,但必须使用软管连接。
由于双杆活塞缸两端的活塞杆直径通常是相等的,因此它左、右两腔的有效面积也相等。当分别向左、右腔输入相同压力和相同流量的油液时,液压缸左、右两个方向的推力和速度相等。当活塞的直径为D,活塞杆的直径为d,液压缸进、出油腔的压力为p1和p2,输入流量为q时,双杆活塞缸的推力F和速度v为

式中,A为活塞的有效工作面积。
双杆活塞缸在工作时,设计成一个活塞杆是受拉的而另一个活塞杆不受力,因此这种液压缸的活塞杆可以做得细些。
2)单杆式活塞缸
如图2.18所示,活塞只有一端带活塞杆,单杆液压缸也有缸体固定和活塞杆固定两种形式,但它们的工作台移动范围都是活塞有效行程的两倍。

图2.18 单杆式活塞缸
由于液压缸两腔的有效工作面积不等,因此它在两个方向上的输出推力和速度也不等,其值分别为

由式(2-33)至式(2-36)可知,由于A1 >A2,所以F1 >F2, v1 <v2。如把两个方向上的输出速度v2和v1的比值称为速度比,记作λV,则λV=v2/v1 =1/[1-(d/D)2]。因此,d=。在已知D和λV时,可确定d值。
3)差动液压缸
单杆活塞缸在其左右两腔都接通高压油时称为“差动连接”,如图2.19所示。

图2.19 差动液压缸
差动连接缸左右两腔的油液压力相同,但是由于左腔(无杆腔)的有效面积大于右腔(有杆腔)的有效面积,故活塞向右运动,同时使右腔中排出的油液(流量为q')也进入左腔,加大了流入左腔的流量(q+q'),从而也加快了活塞移动的速度。实际上活塞在运动时,由于差动连接时两腔间的管路中有压力损失,所以右腔中油液的压力稍大于左腔油液压力,而这个差值一般都较小,可以忽略不计,则差动连接时活塞推力F3和运动速度v3为

进入无杆腔的流量为

由式(2-36)和式(2-38)可知,差动连接时液压缸的推力比非差动连接时小,速度比非差动连接时大。利用这一点,可使在不加大油源流量的情况下得到较快的运动速度,这种连接方式被广泛应用于组合机床的液压动力系统和其他机械设备的快速运动中。如果要求机床往返快速相等时,则由式(2-36)和式(2-39)得

3.柱塞式液压缸
图2.20(a)所示为柱塞缸,它只能实现一个方向的液压传动,反向运动要靠外力。若需要实现双向运动,则必须成对使用。如图2.20(b)所示,这种液压缸中的柱塞和缸筒不接触,运动时由缸盖上的导向套来导向,因此缸筒的内壁不需精加工,它特别适用于行程较长的场合。

图2.20 柱塞式液压缸
柱塞缸输出的推力和速度各为

4.其他液压缸
1)增压液压缸
增压液压缸又称增压器,它利用活塞和柱塞有效面积的不同使液压系统中的局部区域获得高压。它有单作用和双作用两种型式,单作用增压缸的工作原理如图2.21(a)所示。当输入活塞缸的液体压力为p1、活塞直径为D、柱塞直径为d时,柱塞缸中输出的液体压力为高压,其值为

式中,K=D2d2,称为增压比,它代表其增压程度。
显然,增压能力是在降低有效能量的基础上得到的。也就是说,增压缸仅仅是增大输出的压力,并不能增大输出的能量。
单作用增压缸在柱塞运动到终点时,不能再输出高压液体,需要将活塞退回到左端位置,再向右行时才又输出高压液体。为了克服这一缺点,可采用双作用增压缸,如图2.21(b)所示,由两个高压端连续向系统供油。

图2.21 增压缸
2)伸缩缸
伸缩缸由两个或多个活塞缸套装而成,前一级活塞缸的活塞杆内孔是后一级活塞缸的缸筒,伸出时可获得很长的工作行程,缩回时可保持很小的结构尺寸,伸缩缸被广泛用于起重运输车辆上。
伸缩缸可以是如图2.22(a)所示的单作用式,也可以是如图2.22(b)所示的双作用式。前者靠外力回程,后者靠液压回程。

图2.22 伸缩缸
伸缩缸的外伸动作是逐级进行的。首先是最大直径的缸筒以最低的油液压力开始外伸,当到达行程终点后,稍小直径的缸筒开始外伸,直径最小的末级最后伸出。随着工作级数变大,外伸缸筒直径越来越小,工作油液压力随之升高,工作速度变快。其值为


式中,i指i级活塞缸。
3)齿轮传动缸
齿轮传动缸由两个柱塞缸和一套齿条传动装置组成,如图2.23所示。柱塞的移动经齿轮齿条传动装置变成齿轮的传动,用于实现工作部件的往复摆动或间歇进给运动。

图2.23 齿轮传动缸
4)摆动式液压缸
摆动式液压缸是输出扭矩并实现往复运动的执行元件,也称摆动式液压马达,有单叶片和双叶片两种形式。图2.24中定子块固定在缸体上,而叶片和转子连接在一起。根据进油方向,叶片将带动转子作往复摆动。

图2.24 摆动式液压缸工作原理
1—限位挡块;2—缸体;3—传动轴;4—叶片
5.常用液压缸的典型结构及工作原理
1)液压缸的典型结构举例
图2.25所示的是一个较常用的双作用单活塞杆液压缸。它是由缸底20、缸筒10、缸盖兼导向套9、活塞11和活塞杆18组成。缸筒一端与缸底焊接,另一端缸盖(导向套)与缸筒用卡键6、套5和弹簧挡圈4固定,以便拆装检修,两端设有油口A和B。活塞11与活塞杆18利用卡键15、卡键帽16和弹簧挡圈17连在一起。活塞与缸孔的密封采用的是一对Y型聚氨酯密封圈12,由于活塞与缸孔有一定间隙,采用由尼龙1010制成的耐磨环(又叫支承环)13定心导向。杆18和活塞11的内孔由密封圈14密封。较长的导向套9则可保证活塞杆不偏离中心,导向套外径由O型圈7密封,而其内孔则由Y型密封圈8和防尘圈3分别防止油外漏和灰尘带入缸内。缸与杆端销孔与外界连接,销孔内有尼龙衬套抗磨。

图2.25 双作用单活塞杆液压缸
1—耳环;2—螺母;3—防尘圈;4, 17—弹簧挡圈;5—套;6, 15—卡键;7, 14—O型密封圈;8, 12—Y型密封圈;9—缸盖兼导向套;10—缸筒;11—活塞;13—耐磨环;16—卡键帽;18—活塞杆;19—衬套;20—缸底
图2.26所示为一空心双活塞杆式液压缸的结构。
由图2.26可见,液压缸的左右两腔是通过油口b和d经活塞杆1和15的中心孔与左右径向孔a和c相通的。由于活塞杆固定在床身上,缸体10固定在工作台上,工作台在径向孔c接通压力油,径向孔a接通回油时向右移动;反之则向左移动。在这里,缸盖18和24通过螺钉(图中未画出)与压板11和20相连,并经钢丝环12相连,左缸盖24空套在托架3孔内,可以自由伸缩。空心活塞杆的一端用堵头2堵死,并通过锥销9和22与活塞8相连。缸筒相对于活塞运动由左右两个导向套6和19导向。活塞与缸筒之间、缸盖与活塞杆之间以及缸盖与缸筒之间分别用O型圈7、V型圈4和17和纸垫13和23进行密封,以防止油液的内、外泄漏。缸筒在接近行程的左右终端时,径向孔a和c的开口逐渐减小,对移动部件起制动缓冲作用。为了排除液压缸中剩留的空气,缸盖上设置有排气孔5和14,经导向套环槽的侧面孔道(图中未画出)引出与排气阀相连。

图2.26 空心双活塞杆式液压缸的结构
1, 15—活塞杆;2—堵头;3—托架;4, 17—V型密封圈;5, 14—排气孔;6, 19—导向套;7—O型密封圈;8—活塞;9, 22—锥销;10—缸体;11, 20—压板;12, 21—钢丝环;13, 23—纸垫;16, 25—压盖;18, 24—缸盖
2)液压缸的组成
从上面所述的液压缸典型结构中可以看到,液压缸的结构基本上可以分为缸筒和缸盖、活塞和活塞杆、密封装置、缓冲装置和排气装置5个部分,分述如下。
(1)缸筒和缸盖。

图2.27 缸筒和缸盖结构
1—缸盖;2—缸筒;3—压板;4—半环;5—防松螺帽;6—拉杆
一般来说,缸筒和缸盖的结构形式和其使用的材料有关。工作压力p<10MPa时,使用铸铁;p<20MPa时,使用无缝钢管;p>20MPa时,使用铸钢或锻钢。图2.27所示为缸筒和缸盖的常见结构形式。图2.27(a)所示为法兰连接式,结构简单,容易加工,也容易装拆,但外形尺寸和重量都较大,常用于铸铁制的缸筒上。图2.27(b)所示为半环连接式,它的缸筒壁部因开了环形槽而削弱了强度,为此有时要加厚缸壁,它容易加工和装拆,重量较轻,常用于无缝钢管或锻钢制的缸筒上。图2.27(c)所示为螺纹连接式,它的缸筒端部结构复杂,外径加工时要求保证内外径同心,装拆要使用专用工具,它的外形尺寸和重量都较小,常用于无缝钢管或铸钢制的缸筒上。图2.27(d)所示为拉杆连接式,结构的通用性大,容易加工和装拆,但外形尺寸较大且较重。图2.27(e)所示为焊接连接式,结构简单,尺寸小,但缸底处内径不易加工,且可能引起变形。
(2)活塞与活塞杆。
可以把短行程的液压缸的活塞杆与活塞做成一体,这是最简单的形式。但当行程较长时,这种整体式活塞组件的加工较费事,所以常把活塞与活塞杆分开制造,然后再连接成一体。图2.28所示为几种常见的活塞与活塞杆的连接形式。

图2.28 常见的活塞组件结构形式
图2.28(a)所示为活塞与活塞杆之间采用螺母连接,它适用于负载较小、受力无冲击的液压缸中。螺纹连接虽然结构简单,安装方便可靠,但在活塞杆上车螺纹将削弱其强度。图2.28(b)和图2.28(c)所示为卡环式连接方式。图2.28(b)中活塞杆5上开有一个环形槽,槽内装有两个半圆环3以夹紧活塞4,半环3由轴套2套住,而轴套2的轴向位置用弹簧卡圈1来固定。图2.28(c)中的活塞杆使用了两个半圆环4,它们分别由两个密封圈座2套住,半圆形的活塞3安放在密封圈座的中间。图2.28(d)所示是一种径向销式连接结构,用锥销1把活塞2固连在活塞杆3上。这种连接方式特别适用于双出杆式活塞。
(3)密封装置。
液压缸中常见的密封装置如图2.29所示。图2.29(a)所示为间隙密封,它依靠运动间的微小间隙来防止泄漏。为了提高这种装置的密封能力,常在活塞的表面上制出几条细小的环形槽,以增大油液通过间隙时的阻力。它的结构简单,摩擦阻力小,可耐高温,但泄漏大,加工要求高,磨损后无法恢复原有能力,只能在尺寸较小、压力较低、相对运动速度较高的缸筒和活塞间使用。图2.29(b)所示为摩擦环密封,它依靠套在活塞上的摩擦环(尼龙或其他高分子材料制成)在O型密封圈弹力作用下贴紧缸壁而防止泄漏。这种材料效果较好,摩擦阻力较小且稳定,可耐高温,磨损后有自动补偿能力,但加工要求高,装拆较不便,适用于缸筒和活塞之间的密封。

图2.29 密封装置
图2.29(c)、图2.29(d)所示为密封圈(O型圈、V型圈等)密封,它利用橡胶或塑料的弹性使各种截面的环形圈贴紧在静、动配合面之间来防止泄漏。它的结构简单,制造方便,磨损后有自动补偿能力,性能可靠,在缸筒和活塞、缸盖和活塞杆、活塞和活塞杆、缸筒和缸盖之间都能使用。
对于活塞杆外伸部分来说,由于它很容易把脏物带入液压缸,使油液受污染、密封件磨损,因此常需在活塞杆密封处增添防尘圈,并放在向着活塞杆外伸的一端。
(4)缓冲装置。
液压缸一般都设置缓冲装置,特别是对大型、高速或要求高的液压缸,为了防止活塞在行程终点时和缸盖相互撞击,引起噪声、冲击,则必须设置缓冲装置。
缓冲装置的工作原理是利用活塞或缸筒在其走向行程终端时封住活塞和缸盖之间的部分油液,强迫它从小孔或细缝中挤出,以产生很大的阻力,使工作部件受到制动,逐渐减慢运动速度,达到避免活塞和缸盖相互撞击的目的。
如图2.30(a)所示,当缓冲柱塞进入与其相配的缸盖上的内孔时,孔中的液压油只能通过间隙δ排出,使活塞速度降低。由于配合间隙不变,故随着活塞运动速度的降低,起缓冲作用。当缓冲柱塞进入配合孔之后,油腔中的油只能经节流阀1排出,如图2.30(b)所示。由于节流阀1是可调的,因此缓冲作用也可调节,但仍不能解决速度减低后缓冲作用减弱的缺点。如图2.30(c)所示,在缓冲柱塞上开有三角槽,随着柱塞逐渐进入配合孔中,其节流面积越来越小,解决了在行程最后阶段缓冲作用过弱的问题。
(5)排气装置。
液压缸在安装过程中或长时间停放重新工作时,液压缸里和管道系统中会渗入空气。为了防止执行元件出现爬行、噪声和发热等不正常现象,需把缸和系统中的空气排出。一般可在液压缸的最高处设置进出油口把气带走,也可在最高处设置如图2.31(a)所示的放气孔或专门的放气阀,如图2.31(b)和图2.31(c)所示。有杆腔的面积A2=80×10-4m2,缸1的输入压力p1=0.9MPa,输入流量q=12L/min。不计摩擦损失和泄漏,求:(1)两缸承受相同负载(F1=F2)时,该负载的数值及两缸的运动速度。(2)缸2的输入压力是缸1的一半(p1=p2)时,两缸各能承受多少负载?(3)缸1不承受负载(F1=0)时,缸2能承受多少负载?
【例2.4】图2.32为两个结构相同相互串联的液压缸,无杆腔的面积A1=100×10-4m2,

图2.30 液压缸的缓冲装置

图2.31 排气装置

图2.32 相互串联的液压缸
1—缸盖;2—放气小孔;3—缸体;4—活塞杆
解:
(1)P3为大气压,所以P3=0。

特别提示
在液压系统中,液压缸属于执行装置,用以将液压能转变成往复运动的机械能。由于工作机的运动速度、运动行程与负载大小、负载变化的种类繁多,液压缸的规格和种类也呈现出多样性。因此,液压缸的设计以及与设计相关的,如缸的类型、缸的组成、缸的计算、缸的结构以及与结构相关联等有关问题为本章的重点。由于液压缸种类繁多,而活塞式液压缸应用广泛,因而活塞式液压缸是诸类缸中的重点;就缸的计算而言,对3种不同连接形式的单杆液压缸的压力(p1、p2)、推力F、速度v、流量q及负载F等量的关系中,这些量之间的计算关系为重点;对与缸结构相关的问题,液压缸的排气、缓冲为重点。
液压缸的结构比较简单,便于理解和学习,但是对于直观性不强的差动液压缸、缸的背压、缸的缓冲的概念的理解可视为本节的难点。
2.2.2 液压马达
1.液压马达的分类及特点
液压马达是把液体的压力能转换为机械能的装置,从原理上讲,液压泵可以用做液压马达,液压马达也可用做液压泵。但事实上,同类型的液压泵和液压马达虽然在结构上相似,但由于两者的工作情况不同,使得两者在结构上也有某些差异。例如以下几点。
(1)液压马达一般需要正反转,所以在内部结构上应具有对称性,而液压泵一般是单方向旋转的,没有这一要求。
(2)为了减小吸油阻力和径向力,一般液压泵的吸油口比出油口的尺寸大。而液压马达低压腔的压力稍高于大气压力,所以没有上述要求。
(3)液压马达要求能在很宽的转速范围内正常工作,因此,应采用液动轴承或静压轴承。因为当马达速度很低时,若采用动压轴承,就不易形成润滑油膜。
(4)叶片泵依靠叶片跟转子一起高速旋转而产生的离心力使叶片始终贴紧定子的内表面,起封油作用,形成工作容积。若将其当马达用,必须在液压马达的叶片根部装上弹簧,以保证叶片始终贴紧定子内表面,以便马达能正常起动。
(5)液压泵在结构上需保证具有自吸能力,而液压马达就没有这一要求。
(6)液压马达必须具有较大的启动扭矩。所谓启动扭矩,就是马达由静止状态启动时,马达轴上所能输出的扭矩,该扭矩通常大于在同一工作压差时处于运行状态下的扭矩。所以,为了使启动扭矩尽可能接近工作状态下的扭矩,要求马达扭矩的脉动小,内部摩擦小。
由于液压马达与液压泵具有上述不同的特点,使得很多类型的液压马达和液压泵不能互逆使用。
液压马达按其额定转速分为高速和低速两大类,额定转速高于500r/min的属于高速液压马达,额定转速低于500r/min的属于低速液压马达。
高速液压马达的基本型式有齿轮式、螺杆式、叶片式和轴向柱塞式等。它们的主要特点是转速较高、转动惯量小,便于启动和制动,调速和换向的灵敏度高。通常高速液压马达的输出转矩不大(仅几十牛·米到几百牛·米),所以又称为高速小转矩液压马达。
高速液压马达的基本型式是径向柱塞式,例如单作用曲轴连杆式、液压平衡式和多作用内曲线式等。此外,在轴向柱塞式、叶片式和齿轮式中也有低速的结构型式。低速液压马达的主要特点是排量大、体积大、转速低(有时可达每分钟几转甚至零点几转),因此可直接与工作机构连接,不需要减速装置,使传动机构大为简化,通常低速液压马达输出转矩较大(可达几千牛顿·米到几万牛顿·米),所以又称为低速大转矩液压马达。
液压马达也可按其结构类型来分,可以分为齿轮式、叶片式、柱塞式和其他型式。
2.液压马达的性能参数
1)排量、流量和容积效率
习惯上将马达的轴每转一周,按几何尺寸计算所进入的液体容积,称为马达的排量V,有时称为几何排量、理论排量,即不考虑泄漏损失时的排量。
液压马达的排量表示出其工作容腔的大小,它是一个重要的参数。因为液压马达在工作中输出的转矩大小是由负载转矩决定的。但是,推动同样大小的负载,工作容腔大的马达的压力要低于工作容腔小的马达的压力,所以说工作容腔的大小是液压马达工作能力的主要标志。也就是说,排量的大小是液压马达工作能力的重要标志。
根据液压动力元件的工作原理可知,马达转速n、理论流量qi与排量V之间具有下列关系,即

式中,qi为理论流量,m3/s; n为转速,r/min; V为排量,m3/s。
为了满足转速要求,马达实际输入流量q大于理论输入流量,则有

式中,Δq为泄漏流量。

所以得出的实际流量为

2)液压马达输出的理论转矩
根据排量的大小,可以计算在给定压力下液压马达所能输出的转矩的大小,也可以计算在给定的负载转矩下马达的工作压力的大小。当液压马达进、出油口之间的压力差为ΔP,输入液压马达的流量为q,液压马达输出的理论转矩为Tt,角速度为ω时,如果不计损失,液压马达输入的液压功率应当全部转化为液压马达输出的机械功率,即

又因为ω=2πn,所以液压马达的理论转矩为

式中,ΔP为马达进出口之间的压力差。
3)液压马达的机械效率
由于液压马达内部不可避免地存在各种摩擦,实际输出的转矩T总要比理论转矩Tt小些,即

式中,ηm为液压马达的机械效率,%。
4)液压马达的启动机械效率ηm。
液压马达的启动机械效率是指液压马达由静止状态启动时,马达实际输出的转矩T0与它在同一工作压差时的理论转矩Tt之比,即

液压马达的启动机械效率表示出其启动性能的指标。因为在同样的压力下,液压马达由静止到开始转动的启动状态的输出转矩要比运转中的转矩大,这给液压马达带载启动造成了困难,所以启动性能对液压马达是非常重要的,启动机械效率正好能反映其启动性能的高低。启动转矩降低的原因,一方面是在静止状态下的摩擦因数最大,在摩擦表面出现相对滑动后摩擦因数明显减小,另一方面也是最主要的方面是因为液压马达静止状态润滑油膜被挤掉,基本上变成了干摩擦。一旦马达开始运动,随着润滑油膜的建立,摩擦阻力立即下降,并随滑动速度增大和油膜变厚而减小。
实际工作中都希望启动性能好一些,即希望启动转矩和启动机械效率大一些。现将不同结构形式的液压马达的启动机械效率ηm0的大致数值列入表2-3中。
表2-3 液压马达的启动机械效率

由表2-3可知,多作用内曲线马达的启动性能最好,轴向柱塞马达、曲轴连杆马达和静压平衡马达居中,叶片马达较差,而齿轮马达最差。
5)液压马达的转速
液压马达的转速取决于供液的流量和液压马达本身的排量V,可用式(2-53)计算,即

式中,nt为理论转速,r/min。
由于液压马达内部有泄漏,并不是所有进入马达的液体都推动液压马达做功,一小部分因泄漏损失掉了。所以液压马达的实际转速要比理论转速低一些。

式中,n为液压马达的实际转速,r/min; ηV为液压马达的容积效率,%。
3.各类液压马达的工作原理
常用的液压马达的结构与同类型的液压泵很相似,下面对齿轮马达、叶片马达、轴向柱塞马达和摆动马达的工作原理作一介绍。
1)齿轮马达的工作原理
图2.33为外啮合齿轮马达的工作原理图。

图2.33 外啮合齿轮马达的工作原理图
图中I为输出扭矩的齿轮,B为空转齿轮,当高压油输入马达高压腔时,处于高压腔的所有齿轮均受到压力油的作用(如图中箭头所示,凡是齿轮两侧面受力平衡的部分均未画出),其中互相啮合的两个齿的齿面,只有一部分处于高压腔。设啮合点c到两个齿轮齿根的距离分别为a和b,由于a和b均小于齿高h,因此两个齿轮上就各作用一个使它们产生转矩的作用力pB(h-a)和pB(h-b)。这里p代表输入油压力,B代表齿宽。在这两个力的作用下,两个齿轮按图示方向旋转,由扭矩输出轴输出扭矩。随着齿轮的旋转,油液被带到低压腔排出。
齿轮马达的结构与齿轮泵相似,但是内于马达的使用要求与泵不同,二者是有区别的。例如:为适应正反转要求,马达内部结构以及进出油道都具有对称性,并且有单独的泄漏油管,将轴承部分泄漏的油液引到壳体外面去,而不能向泵那样由内部引入低压腔。这是因为马达低压腔油液是由齿轮挤出来的,所以低压腔压力稍高于大气压。若将泄漏油液由马达内部引到低压腔,则所有与泄漏油道相连部分均承受回油压力,而使轴端密封容易损坏。
2)叶片马达的工作原理
图2.34为叶片马达的工作原理图。
当压力为p的油液从进油口进入叶片1和叶片3之间时,叶片2因两面均受液压油的作用,所以不产生转矩。叶片1和叶片3的一侧作用于高压油,另一侧作用于低压油,并且叶片3伸出的面积大于叶片1伸出的面积,因此使转子产生顺时针方向的转矩。同样,当压力油进入叶片5和叶片7之间时,叶片7伸出面积大于叶片5伸出的面积,也产生顺时针方向的转矩,从而把油液的压力能转换成机械能,这就是叶片马达的工作原理。为保证叶片在转子转动前就要紧密地与定子内表面接触,通常是在叶片根部加装弹簧,弹簧的作用力使叶片压紧在定子内表面上。叶片马达一般均设置单向阀为叶片根部配油。为适应正反转的要求,叶片沿转子径向安置。

图2.34 叶片马达的工作原理图
叶片马达的体积小,转动惯量小,因此动作灵敏,可适应的换向频率较高。但泄漏较大,不能在很低的转速下工作,因此,叶片马达一般用于转速高、转矩小和动作灵敏的场合。
3)轴向柱塞马达的工作原理

图2.35 轴向柱塞马达的工作原理
1—斜盘;2—缸体;3—柱塞;4—配油盘;5—马达轴
轴向柱塞马达包括斜盘式和斜轴式两类。由于轴向柱塞马达和轴向柱塞泵的结构基本相同,工作原理是可逆的,所以大部分产品都可作为泵使用。图2.35所示为轴向柱塞式液压马达的工作原理。斜盘1和配油盘4固定不动,缸体2和马达轴5相连接,并可一起旋转。当压刀油经配油窗口进入缸体孔作用到柱塞端面上时,压力油将柱塞顶出,对斜盘产生推力,斜盘则对处于压油区一侧的每个柱塞都要产生一个法向反力F。这个力的水平分力Fx与柱塞上的液压力平衡,而垂直分力Fy则使每个柱塞都对转子中心产生一个转矩,使缸体和马达轴作逆时针方向旋转。如果改变液压马达压力油的输入方向,马达轴就可作顺时针方向旋转。
一般来说,轴向柱塞马达都是高速马达,输出扭矩小,因此,必须通过减速器来带动工作机构。如果能使液压马达的排量显著增大,也就可以使轴向柱塞马达做成低速大扭矩马达。
4)摆动马达
摆动液压马达的工作原理如图2.36所示。
图2.36(a)是单叶片摆动马达。若从油口Ⅰ通入高压油,叶片2作逆时针摆动,低压力从油口Ⅱ排出。因叶片与输出轴连在一起,帮输出轴摆动,同时输出转矩、克服负载。
此类摆动马达的工作压力小于10MPa,摆动角度小于280°。由于径向力不平衡,叶片和壳体、叶片和挡块之间密封困难,限制了其工作压力的进一步提高,从而也限制了输出转矩的进一步提高。

图2.36 摆动缸摆动液压马达的工作原理图
图2.36(b)是双叶片式摆动马达。在径向尺寸和工作压力相同的条件下,分别是单叶片式摆动马达输出转矩的2倍,但回转角度要相应减少,双叶片式摆动马达的回转角度一般小于120°。
叶片摆动马达的总效率η=70%~95%,对单叶片摆动马达来说,设其机械效率为1,出口背压为零,则它的输出转矩为

式中,P为单叶片摆动马达的进口压力;B为叶片宽度;R1为叶片轴外半径,叶片内半径;R2为叶片外半径。
【例2.5】有一液压泵,当负载p1=9MPa时,输出流量q1=85L/min,而负载p2=11MPa时,输出流量为q2=82L/min。用此泵带动一排量VM=0.07L/r的液压马达,当负载转矩TM=110N·m时,液压马达的机械效率ηMm=0.9,转速nM=1000r/min,求此时液压马达的总效率。
解:马达的机械效率
则

泵在负载p2=11MPa的情况下工作,此时输出流量为q2=82L/min。
马达的容积效率为
