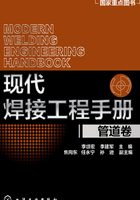
第8章 封头
8.1 概述
封头有很多类,既包括常见的普通封头如圆封头、六角封头等,还有管线上用的比较特殊的封头。封头又称为管帽。
封头是用来密封管道、容器管节等设备用的,是压力管道、压力容器中重要的结构元件,其质量直接关系到压力管道、压力容器运行的安全性。
我国现有的标准,是按结构形式和成形方式的不同来划分的。依据结构形式可以划分为碟形、锥形、平底形、半球形、椭圆形等,如图1-8-1所示;依据成形方式可以划分为冲压成形和旋压成形,有时还可采用爆炸成形制造大直径封头。

图1-8-1 常见封头
现有封头的成形方法包括冷挤压、热挤压、冷旋压、热旋压等,见表1-8-1。
表1-8-1 常用封头的成形方法

除表1-8-1成形方法外,封头还可采用爆炸成形等变形方法进行制造。
封头基本尺寸应符合GB/T 12459《钢制对焊无缝管件》、GB/T 13401《钢板制对焊管件》、SY/T 0609《优质钢制对焊管件规范》、SYT0510《钢制对焊管件规范》的要求;强度及其结构尺寸计算应遵循GB 50251《输气管道工程设计规范》、GB 50253《输油管道工程设计规范》、ASMEB31.8《输气和配气管道系统》、SY/T 0510《钢制对焊管件规范》等设计规范的要求。
8.2 冲压封头
封头的冲压是利用上、下模具配合,在压力设备的压力下一次冷或热冲压成封头形状的成形方法,是压缩类外缘翻边的一种成形方式。
冲压拉延过程中,由于下模与圆形坯料接触部位产生很大的摩擦,因此必须在下模摩擦面上涂刷适当的润滑剂,采用冷成形时可以涂刷如底盘油、植物油、动物油、鲜肥皂、石蜡等;采用热成形时应涂刷机油与石墨混合物。
冲压拉延的变形程度用冲压系数m表示
m=d/D0 (1-8-1)
式中 D0——坯料直径;
d——冲压后封头直径。
拉延冲压的极限变形程度用极限冲压系数mmin表示。极限冲压系数取决于被冲压材料的机械性能、坯料相对厚度(坯料厚度与直径比值)、冲压时的坯料温度等。
如果工件的变形程度较大,即冲压系数计算值小于上述冲压极限系数时,则采用对坯料进行加热的热冲压工艺。
图1-8-2和图1-8-3是小直径和大直径封头热压成形上下模具,该模具和分体成形异径接头所用模具相同。冲压开始时,先把加热的坯料放置在下模2上并找正中心,启动压力机,带动上模1下压,同时吹扫坯料上下面的氧化皮,圆形坯料与上模1一起向下运动,直到坯料脱离下模2,提起上模1,半成品封头与上模1分离。

图1-8-2 小直径封头热压成形上下模具

图1-8-3 大直径封头热压成形上下模具
封头冲压的坯料为圆形平板,平板坯料的直径D0可按封头外表面过中心点到两边端面的总长度+加工余量进行计算求得。冲压浅形件(如平底封头、碟形封头)时材料变薄量较小,反之变薄量较大。实际坯料直径应比计算值减少。
8.2.1 封头成形工艺流程(见图1-8-4)

图1-8-4 封头成形工艺流程图
8.2.2 冲压封头制作工序
(1)原材料检验及验收 钢板的厚度、规格根据需要直接定制,进厂后按照验收程序,检验合格后投入生产线。
(2)下料 采用等离子数控切割机将钢板按需要尺寸和形状切割,得到圆形坯料。
(3)炉内加热 用操作机将圆形坯料送进热处理炉加热至规定温度,取出放在压力机的凹模上,找正圆板中心和凹模中心,吹扫表面的氧化皮,用凸模压制坯料,直到坯料脱离凹模,就得到封头半成品。
(4)管端整形与切割 将封头半成品取出后,先对不符合尺寸要求的部位进行整形,再用切割工具对封头半成品管口按图纸要求切割,去掉毛坯余量。
(5)热处理(需要时) 为了恢复和改善材料的力学性能,将半成品件放入加热炉进行热处理,使封头达到技术条件要求的理化性能指标。
(6)检验与包装 热处理后还需要进行除锈、无损探伤、坡口磁粉探伤、防腐、尺寸及外观检验,包装标识。
8.3 拉延旋压封头
拉延旋压是指利用旋压工具将平板坯料旋制成空心回转体工件的成形方法,是普通旋压中应用最广泛且变形最复杂的成形。
拉延旋压按旋压力的来源分为手动拉旋和机动拉旋两种,由于手动拉旋是依靠人体施加压力,并凭旋压时的声音和振动等感觉进行控制旋压过程,在很大程度上受人力限制,仅限于加工一些塑性较好、厚度较薄的金属。机动拉旋是在手动拉旋的基础上发展起来的。它采用旋压设备和工具完善,旋压力由机床提供,旋压工具采用旋转轮,并进行良好的润滑和冷却,达到了提高变形效率的目的。为了实现精确的拉旋过程,采用机械仿形、液压仿形装置和数控来严格控制旋转轮的运动轨迹,保持旋转轮的运行轨迹与成品的外部形状轮廓线高度一致。
图1-8-5是球形封头拉延旋压加工示意图,首先将平板坯料1通过机床尾顶尖5和顶块4压紧在球形芯模3上,然后随同机床主轴6一起旋转,用旋压轮2加压于坯料上,反复碾压,于是由点及线、由线及面,平板坯料逐渐紧贴于芯模上而成形。

图1-8-5 球形封头拉延旋压示意图
1—平板坯料;2—旋压轮;3—球形芯模;4—顶块;5—机床尾顶尖;6—机床主轴
旋压操作时,应先从靠近芯模底部圆角处毛料开始,即由内缘向外碾压,使其逐渐变形。
旋压过程中,旋压轮施加的压力大小由实践经验控制,施加压力不能太大。尤其是在坯料外缘加力时,压力过大容易起皱。另一方面,在开始旋压时,若对坯料内缘的碾压压力过大,容易使底部圆角处的材料过度变薄和冷作硬化,造成旋压件脱底。同时旋压时,旋压轮的着力点必须逐渐转移,以保证材料均匀延伸变形。
在旋压过程中,由于旋压轮与坯料接触部位产生很大的摩擦,因此必须施加适当的润滑剂,如底盘油、植物油、动物油、鲜肥皂、石蜡以及机油与石墨混合物等。
拉延旋压的变形程度用旋压系数m表示,即
m=d/D0 (1-8-2)
式中 D0——坯料直径;
d——旋压后封头直径。
拉延旋压的极限变形程度用极限旋压系数mmin表示。极限系数取决于被旋压材料的力学性能、坯料相对厚度(坯料厚度与直径比值)、旋压工具形状以及旋压工艺参数(主要指机床主轴转动速度和旋压轮进给量)等。
根据生产经验,对于筒形件,一次成形的极限旋压系数可取mmin=0.6~0.8。当坯料相对厚度t/D×100=0.5时取大值,当t/D×100=2.5时取小值。
如果工件的变形程度较大,即旋压系数计算值小于上述旋压系数极限值时,则需进行两次或多次旋压。多次旋压由连续的几道工序在不同的芯模上进行,但旋压半成品都应以锥形过渡,且最小直径保持不变。由于加工硬化,多次旋压时一般都需进行中间退火或采用对坯料进行加热的热旋压工艺。
封头拉伸旋压的坯料为平板,平板坯料的直径D0可按冲压封头工艺中坯料直径计算求得。但由于拉旋时,材料的变薄比冲压时大,因而引起表面积增加。拉旋浅形件(如平底封头、碟形封头)时材料变薄量较小,反之变薄量较大。故而拉延旋压实际坯料直径应比计算值减少5%~7%。
在旋压过程中,为了保证旋压质量和旋压工作顺利进行,除了严格旋压操作和对坯料合理施加压力外,还必须选择合理的工艺参数。
主轴转速是主要的工艺参数。旋压时,合理的主轴转速与材料种类、厚度、旋压件尺寸大小以及机床刚度等因素有关。
平板坯料旋压时,如果转速太低,坯料边缘易失稳折皱,使旋压工件难以进行。当转速增加到一定值后,坯料可以保持稳定,转速越高,则坯料的稳定性越好,但转速过高时,由于材料与旋压轮的接触次数太多,则容易使材料过度碾压。因此,应选用合适的转速。
各种材料所要求的主轴转速经验数值见表1-8-2。当坯料直径较大、壁厚较厚时,主轴转速可取表中较小值,反之取较大值。
表1-8-2 主轴转速

旋轮进给量也是主要工艺参数。旋压过程中,旋轮进给量取决于材料的稳定性。最佳进给量的大小,通常由经验确定,一般进给量取0.25~1.0mm/r,也可增加至2~4mm/r。当操作者技术熟练、能有效地控制好被旋压材料的失稳情况时,可取大值,这有利于成形和贴模。
8.4 封头的热处理
封头成形后应按表1-8-3所列或技术规范要求进行热处理,热处理应放置在无损检测前、尺寸整形后进行。
表1-8-3 封头的热处理

热处理后的封头应进行生产中的硬度检测,硬度检测应放在热处理后,无损检测前进行,打磨测量点见金属光泽,用便携式硬度仪测量,每个点三次,取三点平均值,测量值应符合表1-8-3的规定或按技术要求进行。
8.5 封头的检测
封头在生产中和出厂前应进行形状和尺寸检测、外观检查、硬度检查、无损检测、力学性能检测等检验以及要求的静水压爆破试验。
8.5.1 形状和尺寸检测
(1)壁厚
①测量仪器:超声波测厚仪。
②测量位置:封头测量位置为变形处,每处不少于5点进行测量。
③测量前准备:用标准试块调整、校准测厚仪;用细砂纸打磨测量点见金属光泽。
④壁厚减薄率计算式为
式中 ——弯管外弧最薄处壁厚,mm
tmin——弯管前直管的壁厚最小值,mm
允许最大减薄率为12.5%。
(2)圆度
①检测用量具;卡尺、直尺。
②测量位置:各封头端口端面;从弯头、异径接头起点开始至终点等距离间隔5点(包括起始点、终点)测量。
③圆度计算式为
式中 Dmax——封头横截面上的最大外径,mm;
Dmin——封头横截面上的最小外径,mm;
D——钢管外径,mm。
圆度标准应符合表1-8-4的规定。
表1-8-4 圆度标准

(3)封头端部内径
①测量工具:盒尺、直尺、内径卡尺。
②测量位置:封头端口。
③封头圆度计算式为
式中 Dmax——封头横截面上的最大内径,mm;
Dmin——封头横截面上的最小内径,mm;
D——钢管公称内径,mm。
圆度标准如下。
DN400以下:按GB/T 12459进行;
DN400~DN600:±2.4mm;
DN650~DN900:±2.4mm;
DN950~DN1050:±3.2mm。
8.5.2 外观检查
①封头不应有裂纹、过热、过烧存在。
②封头表面应无硬点。
③封头内、外表面应光滑,无有损强度及外观的缺欠,如结疤、划痕、重皮等。检查发现的缺欠应修磨,修磨处应圆滑,直至用磁粉探伤方法确认缺欠完全消除为止,修磨后直管段剩余壁厚不得小于公称壁厚的93.5%;弯曲段的剩余壁厚不得小于封头外弧侧规定壁厚最小值。
④封头表面不允许有明显折皱。起皱高度h应不大于1.5mm,起皱波浪间距f与起皱高度h之比应大于150mm。
⑤凹痕:封头管体上深度超过3.15mm的凹坑或焊缝上深度超过1.5mm的凹坑是不可接受的缺陷,不允许采用锤击方法修理。
8.5.3 硬度检查
所有封头外表面应用便携式硬度仪进行硬度检查,检查位置:管体(包括与焊缝成90°或180°的位置)、所有纵向焊缝,每个位置应测量不少于5点。
8.5.4 其他检验
无损检测、力学性能检测、静水压爆破试验等参照本篇第4章的相关要求。