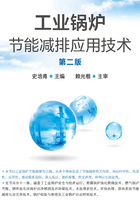
第六节 燃煤锅炉降低灰渣含碳量
一、灰渣含碳量与经济运行的关系
燃煤工业锅炉的固体不完全燃烧热损失q4包括三部分,即灰渣含碳量、漏煤含碳量和飞灰含碳量所造成的热损失。它是衡量燃料中可燃成分燃尽程度的一个重要指标,是燃煤工业锅炉的主要热损失。其中最主要的是灰渣含碳量所造成的,一般达到15%左右,较差的高达20%以上,成为中小型工业锅炉的通病。还应该指出,q4热损失大,不仅浪费了燃料,还会造成环境污染。
固体不完全燃烧热损失的大小,主要与锅炉型号、结构、燃料品种与质量、燃烧方式及其燃料管理优劣和运行操作技术等有关。该项热损失越大,燃烧效率越低,直接影响锅炉热效率。据大量锅炉热平衡与节能监测资料显示,灰渣含碳量减少2.5%,可节煤1%;灰渣含碳量降低4.5%,锅炉热效率可提高1%左右,对经济运行、节能减排效果显著。
二、加强燃煤管理工作
1.工业锅炉燃用洁净煤
目前工业锅炉燃煤很难满足设计煤种、质量要求。主要表现在燃用小煤窑煤多,煤种与成分波动大、煤质差,往往出现着火推迟、燃烧恶化、炉膛温度水平低、灰渣含碳量升高等现象,供热难以保证;特别是我国沿用历史习惯,工业锅炉一直燃用原煤,粒度级配与设计不匹配,3mm以下煤屑高达60%~70%,漏煤与飞灰多,煤层阻力大,配风难于均匀,灰渣含碳量升高;燃煤含硫量普通较高,且很难控制,环境污染严重。因此,工业锅炉应燃用洁净煤,主要包括动力洗选煤、锅炉型煤、水煤浆、小型高效煤粉以及生物质燃料等锅炉,这是我国燃煤工业锅炉可持续发展的必由之路。这将在第六章中进行详细介绍。
2.燃煤筛分破碎,保持粒度合理
市场上供应的散煤粒度为0~50mm,且小于3mm的煤屑太多,不符合链条锅炉的设计要求。为均匀布煤、合理配风和组织高温燃烧创造条件,在使用前应进行筛分、破碎。链条炉3mm以下煤屑不好烧,应通过筛分除掉,对大块煤经破碎合格,煤矸石一定要拣出。
对于筛分下来的煤面与拣出的矸石,有条件的可用于循环流化床锅炉燃用,或者再搭配几种煤面,并加入适量固硫剂,经炉前成型机压制成型煤入炉(详见第六章),可获得良好的综合经济效益。
3.燃煤适量加湿焖水
煤中混入水是有害的,因为蒸发每千克水要消耗2500kJ(600kcal)热量。若煤中含有8%的水,就要降低发热量126kJ/kg,相当于煤的0.5%左右热值。但是提前均匀适量焖水,把水分渗透到煤的内部,可补偿上述损失,是一项非常必要的燃煤准备工作,它有以下几点好处:
(1)疏松燃煤,为强化燃烧创造条件 在一个标准大气压下,水由液态变为气态,比容从0.001043m3(标准状态 )/kg膨胀为1.725m3/kg,体积增大1650倍。当煤中水分与挥发物受热逸出时,必然会产生微小空隙或裂纹,使其疏松,增大了与空气的接触面积,有利于氧气扩散进入,为强化燃烧创造了条件。
(2)促进焦炭还原反应,加速燃烧过程 煤的层燃是通过炭的氧化与还原反应进行的。链条炉排煤层中段下部为氧化带,生成大量CO2,其上为还原带,水蒸气通过赤热焦炭,发生吸热的还原反应:
C+CO2=2CO-ΔH (2-17)
C+H2O=CO+H2-ΔH (2-18)
水蒸气的存在可促进炭的气化过程,使固体炭通过气化反应转化为气态,从而加速了煤的燃烧过程。
(3)减少漏煤与飞灰热损失 煤中渗透适量水分,使煤屑与煤屑之间、煤屑与煤块之间相互黏结,可减少漏煤与飞灰,降低固体不完全燃烧热损失。
加水要点:煤中掺水要适量、均匀、焖透,一般以8%~10%为宜。可送化验室进行分析,也可以用经验法予以判定,用手攥一下,松手后煤团开裂而不散。掺水后要焖放8h以上,使水分渗透到煤粒内部。有的锅炉房在煤仓顶部设水管喷水,很不均匀,时间又短,起不到应有作用。
三、炉排横向均匀布煤,保持火床均衡
通常机械化给煤输送系统,到达顶部平台后先由水平皮带机经落煤管送入锅炉贮煤仓内。在重力分离作用下,出现沿煤仓宽度方向的粒度离析现象:中部煤屑多,大块则滚落到两侧,因而造成链排横向煤层粒度分布不均,通风阻力差异大。中部阻力大,风量严重不足,两侧阻力小,风量过剩。于是炉排横向燃烧进程不同,火床不平齐,甚至会出现火口,灰渣可燃炭与飞灰量增加,降低燃烧效率。应设法解决炉排横向布煤不均问题,视具体情况可采取如下措施。
1.设置可摆动的落煤管
燃煤由储煤仓流到煤斗时,多采用固定的落煤管。由于煤斗很宽,有时设置两个以上落煤管,仍会出现粒度离析现象。为此可改为下端沿煤斗横向摆动的落煤管,也叫摆煤管,工作原理如图2-11所示。

图2-11 摆煤管工作原理图
1—链条;2—链轮;3—煤仓;4—摆煤管;5—电机;6—直流调速电机;7—行程开关;8—减速器;9—前大轴
在锅炉链排传动主轴上装设两个行程开关触点,来控制落煤管电机的启动。当落煤管摆到一定角度时,由落煤管电机轴端设置的两个行程开关与触点相碰,控制落煤管的停止位置。在链排主轴转动与落煤管电机联动作用下,实现了落煤管的左右摆动频率与链排速度相协调。
落煤管可促进燃煤粒度沿炉排横向均匀分布,煤层阻力趋于均衡,有利于燃烧的正常进行,降低灰渣含碳量。该装置结构简单,操作方便,维修工作量小,适合于大中型工业锅炉应用。目前已有定型产品供选配,亦可自行设计改造。
2.设置皮带机移动卸煤犁
为了使燃煤粒度在链条炉排上均匀分布,首先应设法促进煤仓内的燃煤粒度沿横向分布均匀。为此,在煤仓顶部的水平皮带机上加装移动卸煤犁小车,其下铺设轨道。当皮带机启动后,卸煤犁小车可沿煤仓宽度方向往返移动,使落煤点沿煤仓宽度方向有规律地移动,可达到均匀布煤的要求。该设备已有定型产品供选配,结构简单,效果很好。
四、链条锅炉布煤方法沿革与评述
1.煤闸板布煤法
此为传统布煤法,煤斗中的燃煤因重力作用而下落,经煤闸板限定所设厚度,进到移动的正转链排上。煤层平整密实,粒度分布混杂,无规律,火床难以均匀,通风阻力大,风机电耗高,水冷煤闸板带走热量,有时被烧坏。
2.分层布煤法
1993年发明了分层布煤法。取消煤闸板,燃煤从煤仓经辊筒落下时,经向后倾斜一定角度的筛分器溜到正转链排上。最初的筛分器就是有一定间距的圆钢棍排面,后来经不断改进,研制出箅板网孔式、梳齿式、峰谷式(垄形式)和组合式等筛分器。其原理均是利用燃煤从倾斜的筛分器下溜时,与正转链条炉排向前移动的时间差,使燃煤得以分层。大块煤只能从筛分器末端滚下,落到链排表面,较小煤块随后落到大块煤层上,煤屑与粉煤最后落到煤层表面,如图2-12所示。此种布煤方法的前提条件必须是正转链排,筛分器应有恰当的倾斜角度,并设计有网孔或间距,以控制不同粒度燃煤下落的顺序。由于燃煤在下落的过程中未受到挤压,煤层较为有序疏松,通风阻力小,火床较均匀,有一定的节能效果。但后来因所供原煤粒度发生变化,煤屑与粉煤约占60%~70%,造成无层可分的现象,因而又研发出较为先进的布煤方法。

图2-12 分层布煤剖面示意图
3.分行垄形布煤法与节能机理
天津最早于1996年发明了《纵向分行垄形布煤燃烧装置》,并申报了专利,如图2-13所示。该方法也称波峰波谷式布煤法,组装结构见图2-14。利用单辊筒和特制的筛分器,达到布煤既分行,又能完成垄形状,并把燃煤中有限的煤块分布在垄沟处。由于燃煤在筛分器斜面上滚落下溜时会产生二次离析并从垄背滚动溜边现象,因而垄沟中煤块落的较多,而在垄背处煤屑与粉煤较多,突破了布煤要求“平”、“均”的传统框框。起初有些人难于理解,但该专利投入市场后,节能效果显著,很快在天津、河北、辽宁、吉林、山东等省市推广应用几千台,并向全国各地转让专利技术多家,特别是我国最大的锅炉炉排生产企业瓦房店永宁机械厂购置了该专利技术,在链条炉排出厂时整套配置,更加大了推广应用力度和范围。2010年9月经天津锅炉协会委派专家组,对多年来安装该装置的九个锅炉房共计28台锅炉进行了现场考查调研,对该专利节能机理进行了深入研究,汇总如下。

图2-13 垄形布煤筛分器原理图

图2-14 分行垄形布煤组装结构图
1—给煤设备本体;2—链条炉排;3—调煤闸板;4—煤斗;5—辊筒式给煤机;6—筛分器;7—导流板
①煤层疏松,风机节电原理。由于取消了煤闸板,燃煤自由下落,煤层较为疏松,尤其在垄沟处,煤层不但薄而且煤块居多,通风阻力小,可提前点燃,燃烧旺,有的企业曾专门做过模拟试验,垄形布煤与煤闸板挤压布煤相比,煤的堆密度约减小40%左右,风室压力由400Pa降至200Pa。因而风机电流减小,节电7.5%以上。
②煤层外表面积扩大,提高炉排热强度。分行垄形布煤后煤层表面积展开宽度增大30%~40%,相当于扩大了炉排面积,必然会提高炉排热强度。因而锅炉出力提高4.5%左右。天津金泰供热中心专门进行了热平衡测定,锅炉热效率平均提高4.0%左右。
③微型自动拨火,降低灰渣含碳量。分行垄形布煤一般在三门过后变为平火床。对此现象早已认定,但对其产生的原因曾有不同解读。归纳起来,大致有以下几种观点:
a.在100℃时燃煤中的水分开始蒸发,变为水蒸气后体积膨胀1650倍,为垄背受热燃煤向两侧垄沟倒塌提供了助推力;
b.链条运行,不断向前移动,会产生一定的振动现象,有助于垄背受热燃煤在存有位差的条件下,向两侧垄沟倾落;
c.燃煤中的挥发分在170℃时开始析出,200~300℃时着火燃烧;还有燃煤中的碳燃烧反应,生成气体,这些燃烧产物析出时,也会产生一定的膨胀作用;
d.燃煤燃烧后所剩灰分体积必然会缩小所致。
经过认真研究分析,认识到垄背两侧为垄沟呈现为一定斜度,二者存有位差,提供了垄背向两侧垄沟倒塌的客观条件。实地观察结果并参照图2-15所知,在燃烧初始阶段,垄沟内的温度远高于垄背。随着燃烧不断进行,垄沟处先行下沉,与垄背位差加大。当垄背燃烧温度提高后,不稳定因素增加,在a、b两项外力作用下,垄背必然向两侧垄沟倒塌,变为平火床,起到微形拔火作用,促使燃烧旺盛,降低灰渣残碳5%以上。

图2-15 垄形布煤着火初期
④氧化还原反应相汇合,提高火焰温度。在垄沟处煤层薄,煤块多,风量充足,全部为氧化反应,(C+O2→CO2+32760kJ/kg)不可能产生还原层,呈现出氧化性火焰。而在垄背处,煤层厚,且煤屑与粉煤较多,风量相对不足,按层燃原理,会产生一定的还原反应(C+0.5O2→CO+9954kJ/kg),生成还原性气体。上述两种气体相遇,必然会发生强烈的混合燃烧反应,因而可提高火焰温度70~80℃。同时氧化性气体与还原性气体混合燃烧,必然会消耗掉烟气中多余的残氧含量,巧现低氧燃烧技术,达到合理的空气系数。天津市金泰供热中心,经锅炉热平衡测试,尾部受热面后的空气系数为1.39,南开大学供热站锅炉尾部受热面后的空气系数为1.36~1.45。与煤闸板布煤锅炉相比低很多,由于少消耗21%的氧,必然少带进79%的氮,因而减小了烟气体积,降低了排烟热损失。
4.燃用湿煤和冻煤的技术措施与效果
我国工业锅炉房一般为露天储煤,污染环境,遇有刮风、下雨或降雪天气,锅炉必然要烧湿煤或冻煤。因而经常发生堵煤、棚煤、下煤不畅或粘结筛分器等问题,严重影响正常供热,甚至会造成事故。尤其是“三北”地区更为严重。遇此情况,首先应加设储煤厂房,然后可采用三辊式给煤装置,如图2-16所示。利用三辊给煤装置的湿煤搅动辊,将其搅动松散,再通过移煤辊与拨煤辊,使其下煤通畅均衡,保证正常运行,满足供热要求。

图2-16 三辊给煤装置示意图
1—下煤仓;2—湿煤搅动辊(Ⅲ辊);3—防漏煤板;4—移煤转辊(Ⅱ辊);5—炉排;6—倾斜式煤闸板;7—拨煤转辊(Ⅰ辊);8—可变形组合式筛分器
五、应用强化燃烧技术,促进燃煤加速燃尽
煤的燃烧速度主要与温度及配风情况有关,提高炉膛温度、提高火焰温度,即可加快燃烧进程。在一般情况下,配风合理,炉膛温度高于1200℃,炉内的辐射传热比对流传热强烈得多,此时炉膛内布置的水冷壁所吸收的辐射热量比对流热量要提高5倍以上;当炉膛温度在1100~1200℃时,辐射传热量与对流传热量基本持平;当炉膛温度低于1000℃时,辐射传热量明显减弱。链条锅炉燃煤燃烧速度还与煤的品种、质量有关。若煤的灰分高、挥发分低、热值不高,起火困难,燃烧速度趋缓,难于燃尽,灰渣含碳量升高。
链条锅炉针对以上情况,采取强化燃烧措施,加快燃烧速度,提高燃烧效率。诸如合理设计和砌造炉拱、调整前后拱角度、必要时设置中拱、恰当地布置炉拱的遍盖面、在炉膛相关部位增设高压喷射抽吸炉内高温烟气再高速喷入炉膛内进行强化燃烧等措施。当燃用劣质煤时,应加设卫燃带,适当减缓水冷壁吸热量,来提高炉膛温度,加速燃烧进程。实践证明,其效果是很明显的。另外,应设法提高空气预热温度,除能降低排烟温度外,还可提高火焰温度,有利于强化燃烧。有关强化燃烧的相关内容,将在第三章中作详细介绍,这里只概要提及。
六、漏煤回烧与灰渣返烧
漏煤的含碳量一般较高,比原煤略低,应设法降低漏煤损失。前已叙及,要加强原煤的准备与处理工作,并采取先进的布煤技术,可以减少漏煤损失,还可改进或选用鳞片式不漏煤链排结构。但还是有漏煤的,应当专门收集起来,掺混在原煤中回烧。在掺混前应适当加湿处理,以便与原煤较好混合。
灰渣的含碳量一般在15%左右,有的还高。目前多数企业经水冲后当作废物处理,造成环境污染。应通过分析化验,有反烧价值的,掺混在原煤中返烧。有条件的企业,最好送往流化床锅炉返烧,效果更好。如无返烧价值,也应当作为一种资源进行综合利用。
飞灰的含碳量一般30%左右,目前均作为废物处理,又无密闭设施,造成环境污染。应加设密闭回收,作为一种资源进行综合利用,如与原煤适当配比制造型煤,或者加湿处理后进行回烧,有条件的企业最好送往流化床锅炉回烧。