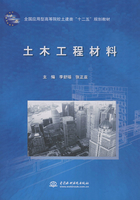
3.5 硅酸盐水泥
水泥是一种粉末状材料,当它与水或适当的盐溶液混合后,在常温下经过一定的物理化学作用,能由浆体状逐渐凝结硬化,并且具有强度,同时能将砂、石等散粒材料或砖、砌块等块状材料胶结为整体。水泥是一种良好的矿物胶凝材料,它与石灰、石膏、水玻璃等气硬性胶凝材料不同,不仅能在空气中硬化,而且在水中能更好地硬化,并保持和发展其强度。因此,水泥是一种水硬性胶凝材料。

图3.3 硅酸盐水泥系列
水泥是制造各种形式的混凝土、钢筋混凝土和预应力钢筋混凝土构筑物的最基本组成材料,也常用于配制砂浆,以及用作灌浆材料等。水泥在国民经济建设中起着十分重要的作用,不仅大量用于工业和民用建筑,还广泛用于道路、桥梁、铁路、水利和国防工程中,素有“建筑业的粮食”之称。水泥的品种很多,按其主要水硬性矿物名称可分为硅酸盐系水泥、铝酸盐系水泥、硫铝酸盐系水泥、铁铝酸盐系水泥、磷酸盐系水泥等,其中在土木工程中生产量最大、应用最广的是硅酸盐系水泥。本节主要介绍硅酸盐系水泥,并在此基础上简要介绍其他品种水泥。硅酸盐系水泥是以硅酸钙为主要成分的水泥熟料、一定量的混合材料和适量石膏共同磨细而成。按其性能和用途不同,又可分为通用水泥、专用水泥和特性水泥三大类。通用水泥是指大量用于一般土木建筑工程中的水泥,专用水泥和特性水泥是指用于各类有特殊要求的工程中的水泥。
3.5.1 硅酸盐水泥的生产和矿物组成
硅酸盐水泥(PortlandCement,故常称为波特兰水泥)分为两种类型:不掺加混合材料的称Ⅰ型硅酸盐水泥,代号P.Ⅰ;在硅酸盐水泥熟料粉磨时掺加不超过水泥熟料质量5%的石灰石或粒化高炉矿渣混合材料的称Ⅱ型硅酸盐水泥,代号P.Ⅱ。硅酸盐水泥是硅酸盐系水泥的一个基本品种。其他品种的硅酸盐类水泥,都是在此基础上加入一定量的混合材料,或者适当改变水泥熟料的成分而形成的。
1.硅酸盐水泥生产工艺
生产硅酸盐水泥的原料主要是石灰质原料(如石灰石、白垩等)和黏土质原料(如黏土、黄土和页岩等)两类,一般常配以辅助原料(如铁矿石、砂岩等)。石灰质原料主要提供CaO,黏土质原料主要提供SiO2、Al2O3及少量的Fe2O3,辅助原料常用以校正Fe2O3或SiO2的不足。
硅酸盐水泥的生产过程分为制备生料、煅烧熟料、粉磨水泥3个主要阶段,该生产工艺过程如下:石灰质原料和黏土质原料按适当的比例配合,有时为了改善烧成反应过程还加入适量的铁矿石和矿化剂,将配合好的原材料在磨机中磨成生料,然后将生料入窑煅烧成熟料。以适当成分的生料,煅烧至部分熔融得到的以硅酸钙为主要成分的物料称为硅酸盐水泥熟料。
熟料再配以适量的石膏,或根据水泥品种要求掺入混合材料,入磨机磨至适当细度,即制成水泥。整个水泥生产工艺过程可概括为“两磨一烧”,如图3.4所示。

图3.4 硅酸盐水泥主要生产流程
水泥生料的配合比例不同,将直接影响硅酸盐水泥熟料的矿物成分比例和主要技术性能,水泥生料在窑内的烧成(煅烧)过程,是保证水泥熟料质量的关键。水泥生料的烧成,在达到1000℃时各种原料完全分解出水泥中的有用成分,主要为氧化钙(CaO)、二氧化硅(SiO2)、三氧化二铝(Al2O3)、三氧化二铁(Fe2O3),其中,在800℃左右少量分解出的氧化物已开始发生固相反应,生成铝酸一钙、少量的铁酸二钙及硅酸二钙。在900~1100℃时铝酸三钙和铁铝酸四钙开始形成;1100~1200℃时大量形成铝酸三钙和铁铝酸四钙,硅酸二钙生成量最大;1300~1450℃时,铝酸三钙和铁铝酸四钙呈熔融状态,产生的液相把CaO及部分硅酸二钙溶解于其中,在此液相中,硅酸二钙吸收CaO化合成硅酸三钙。这是煅烧水泥的最关键一步,物料必须在高温下停留足够的时间,使物料中游离的氧化钙被吸收掉,以保证水泥熟料的质量。烧成的水泥熟料经过迅速冷却,即得水泥熟料颗粒。
2.硅酸盐水泥熟料的矿物组成
硅酸盐水泥熟料的主要矿物有以下4种,其矿物组成及含量的大致范围见表3.5。
表3.5 硅酸盐水泥熟料的矿物组成

表3.5中前两种矿物称为硅酸盐矿物,一般占总量的75%~82%;后两种矿物称为熔剂矿物,一般占总量的18%~25%。这4种矿物成分的主要特征如下:
(1)C3S的水化速率较快,水化热较大,且主要在早期放出;强度最高,且能不断得到增长,是决定水泥强度高低的最主要矿物。
(2)C2S的水化速率最慢,水化热最小,且主要在后期放出;早期强度不高,但后期强度增长率较高,是保证水泥后期强度的最主要矿物。
(3)C3A的水化速率极快,水化热最大,且主要在早期放出,硬化时体积减缩也最大;早期强度增长率很快,但强度不高,而且以后几乎不再增长,甚至降低。
(4)C4AF的水化热速率较快,仅次于C3A,水化热中等,强度较低;脆性较其他矿物为小,当含量增多时,有助于水泥抗拉强度的提高。

图3.5 水泥熟料的强度增长曲线
水泥熟料的抗压强度随时间的增长情况如图3.5所示。由上述可知,几种矿物成分的性质不同,它们在熟料中的相对含量改变时,水泥的技术性质也随之改变。例如,要使水泥具有快硬高强的性能,应适当提高熟料中C3S及C3A的相对含量;若要求水泥的水化放热量较低,可适当提高C2S及C4AF的含量而控制C3S及C3A的含量。因此,掌握硅酸盐水泥熟料中各矿物成分的含量及特性,就可以大致了解该水泥的性能特点。
除以上4种主要矿物成分外,硅酸盐水泥中尚有少量其他成分,常见的有氧化镁(MgO)、三氧化硫(SO3)、游离氧化钙(f-CaO)、碱等。
3.5.2 硅酸盐水泥的水化和凝结硬化
1.硅酸盐水泥熟料矿物的水化
水泥颗粒与水接触,在其表面的熟料矿物立即与水发生水解或水化作用(也称为水泥的水化)形成水化产物,同时放出一定热量。其反应式如下:
(1)3CaO·SiO2的水化。

(2)2CaO·SiO2的水化。

(3)3CaO·Al2O3的水化。
在水及Ca(OH)2饱和溶液中:

在石膏、氧化钙同时存在的条件下:

(4)4CaO·Al2O3·Fe2O3的水化。

熟料各单矿物在水化过程中表现出的特性见表3.6。
表3.6 硅酸盐水泥熟料矿物水化特性

硅酸三钙水化很快,生成的水化硅酸钙几乎不溶于水,而立即以胶体微粒析出,并逐渐凝聚称为凝胶。在电子显微镜下可以观察到,水化硅酸钙是大小与胶体相同的、结晶较差的、薄片状或纤维状颗粒,称为C-S-H凝胶。水化生成的氢氧化钙在溶液中的浓度很快达到过饱和,并呈六方晶体析出。水化铝酸三钙为立方晶体,在氢氧化钙饱和溶液中,它能与氢氧化钙进一步反应,生成六方晶体的水化铝酸四钙。
为了调节水泥的凝结时间,水泥中掺有适量石膏。水化时,铝酸三钙和石膏反应生成高硫型水化硫铝酸钙(称为钙矾石,CaO·Al2O3·3CaSO4·31H2O,以AFt表示)和单硫型水化硫铝酸钙(CaO·Al2O3·CaSO4·12H2O,以AFm表示)。生成的水化硫铝酸钙是难溶于水的针状晶体。
综上所述,如果忽略一些次要的和少量的成分,则硅酸盐水泥与水作用后,生成的主要水化产物有:水化硅酸钙和水化铁酸钙凝胶、氢氧化钙、水化铝酸钙和水化硫铝酸钙晶体。在充分水化的水泥石中以质量分数论,C-S-H凝胶约占70%, Ca(OH)2约占20%,钙矾石和单硫型水化硫铝酸钙约占70%。
2.硅酸盐水泥的凝结硬化
硅酸盐水泥用适量的水调和后,最初形成具有可塑性的浆体,随着时间的增长,失去可塑性(但尚无强度),这一过程称为初凝,开始具有强度时称为终凝。由初凝到终凝的过程称为水泥的凝结。随着水化进程的推移,水泥浆凝固成具有一定的机械强度并逐渐发展而成为坚固的人造石—水泥石,这一过程称为“硬化”。水泥的凝结和硬化是人为划分的,实际上是一个连续变化的复杂的物理化学过程。水泥的凝结硬化一般按水化反应速率和水泥浆体结构特征分为:初始反应期、潜伏期、凝结期和硬化期4个阶段,见表3.7。
表3.7 水泥凝结硬化时的几个阶段

(1)初始反应期。
水泥与水接触后立即发生水化反应,C3S水化生成的Ca(OH)2溶于水中,溶液pH值迅速增大至13左右,当溶液达到过饱和后,Ca(OH)2开始结晶析出。同时暴露在颗粒表面的C3A溶于水,并与溶于水的石膏反应,生成钙矾石结晶析出,附着在水泥颗粒表面。这一阶段大约经过10min,约有1%的水泥发生变化。
(2)潜伏期。
在初始反应期之后,有1~2h的时间,由于水泥颗粒表面形成水化硅酸钙凝胶和钙矾石晶体构成的膜层阻止了与水的接触,使水化反应速度很慢,这一阶段水化放热小,水化产物增加不多,水泥浆体仍保持塑性。
(3)凝结期。
在潜伏期中,由于水缓慢穿透水泥颗粒表面的包裹膜,与熟料矿物成分发生水化反应,而水化生成物穿透膜层的速度小于水分渗入膜层的速度,形成渗透压,导致水泥颗粒表面膜层破裂,使暴露出来的矿物进一步水化,从而结束了潜伏期。水泥水化产物体积约为水泥体积的2.2倍,生成的大量的水化产物填充在水泥颗粒之间的空间里,水的消耗与水化产物的填充使水泥浆体逐渐变稠直至失去可塑性而凝结。
(4)硬化期。
在凝结期以后,进入硬化期,水泥水化反应继续进行使结构更加密实,但放热速度逐渐下降,水泥水化反应越来越困难。在适当的温度、湿度条件下,水泥的硬化过程可持续若干年。水泥浆体硬化后形成坚硬的水泥石,水泥石是由凝胶体、晶体、未水化完的水泥颗粒及固体颗粒的毛细孔所组成的不匀质结构体。水泥凝结硬化过程示意图如图3.6所示。

图3.6 水泥凝结硬化过程示意图
1—水泥颗粒;2—水分;3—凝胶;4—晶体;5—水泥颗粒的未水化内核;6—毛细孔
水泥硬化过程中,最初的3d强度增长幅度最大,3d到7d强度增长率有所下降,7d到28d强度增长率进一步下降,28d强度基本达到最高水平,28d以后强度虽然还会继续发展,但强度增长率却越来越小。
3.影响硅酸盐水泥凝结硬化的主要因素
(1)水泥组成成分的影响。
水泥的矿物组成成分及各组分的比例是影响水泥凝结硬化的最主要因素。如前所述,不同矿物成分单独和水起反应时所表现出来的特点是不同的。水泥中如提高C3A的含量,将使水泥的凝结硬化加快,同时水化热也大。一般来讲,若在水泥熟料中掺加混合材料,将使水泥的抗侵蚀性提高,水化热降低,早期强度降低。
(2)石膏掺量。
石膏称为水泥的缓凝剂,主要用于调节水泥的凝结时间,是水泥中不可缺少的组分。水泥熟料在不加入石膏的情况下与水拌合后会立即产生凝结,同时放出热量。其主要原因是由于熟料中的C3A很快溶于水中,生成一种促凝的铝酸钙水化物,使水泥不能正常使用。石膏起缓凝作用的机理是:水泥水化时,石膏很快与C3A作用并产生难溶于水的水化硫铝酸钙(钙矾石),它沉淀在水泥颗粒表面形成保护膜,从而阻碍了C3A的水化反应并延缓了水泥的凝结时间。
石膏的掺量太少,缓凝效果不显著,但过多地掺入石膏因其本身会生成一种促凝物质,反而使水泥快凝。适宜的石膏掺量主要取决于水泥中C3A的含量和石膏中SO3的含量,同时也与水泥细度及熟料中SO3的含量有关。石膏掺量一般为水泥质量的3%~5%。如果水泥中石膏掺量超过规定的限量,还会引起水泥强度降低,严重时会引起水泥体积安定性不良,使水泥石产生膨胀性破坏。所以国家标准规定,硅酸盐水泥中SO3总计不得超过水泥总质量的3.5%。
(3)水泥细度的影响。
水泥颗粒的粗细直接影响水泥的水化、凝结硬化、强度及水化热等。这是因为水泥颗粒越细,总表面积越大,与水的接触面积越大,因此水化迅速,凝结硬化也相应增快,早期强度也高。但水泥颗粒过细,易与空气中的水分及二氧化碳反应。致使水泥不宜久存,过细的水泥硬化时产生的收缩亦较大;水泥磨的越细,能耗越多,成本越高。因此,水泥颗粒的粒径应控制在合适的范围内。
(4)养护条件(温度、湿度)的影响。
养护环境有足够的温度和湿度,有利于水泥的水化和凝结硬化过程及早期强度发展。如果环境十分干燥,水泥中的水分蒸发导致水泥不能充分水化,同时硬化也将停止,严重时会使水泥石发生裂缝。通常情况下,养护时温度升高,水泥的水化加快,早期强度发展也快。若在较低的温度下硬化,虽强度发展较慢,但最终强度不受影响。但当温度低于0℃以下时,水泥的水化停止,强度不但不增长,甚至会因水结冰而导致水泥石结构破坏。实际工程中,常通过蒸汽养护,压蒸养护来加快水泥制品的凝结硬化过程。
(5)养护龄期的影响。
水泥的水化硬化是较长时期内不断进行的过程,随着水泥颗粒内各熟料矿物水化程度的提高,凝胶体不断增加,毛细孔不断减少,使水泥石的强度随龄期增长而增加。实践证明,水泥一般在28d内强度发展较快,28d后发展缓慢。
(6)拌合用水量的影响。
在水泥用量不变的情况下,增加拌合用水量,会增加硬化水泥石中的毛细孔,降低水泥石的强度,同时延长水泥的凝结时间。所以,在实际工程中,水泥混凝土调整流动性大小时,在不改变水灰比的情况下,常增减水和水泥的用量。为了保证混凝土的耐久性,有关标准规定了最小水泥用量。
(7)外加剂的影响。
硅酸盐水泥的水化、凝结硬化受水泥熟料中C3S、C3A含量的制约,凡对C3S和C3A的水化能产生影响的外加剂,都能改变硅酸盐水泥的水化、凝结硬化性能。如加入促凝剂(CaCl2、Na2SO4等)能促进水泥水化硬化,提高早期强度。相反,掺加缓凝剂(木钙糖类等)会延缓水泥的水化、硬化,影响水泥早期强度的发展。
(8)储存条件的影响。
储存不当,会使水泥受潮,颗粒表面发生水化而结块,严重降低强度。即使良好的储存,在空气中的水分和CO2作用下,水泥也会发生缓慢水化和碳化,经3个月,强度通常降低10%~20%、6个月降低15%~30%、1年后将降低25%~40%,所以水泥的有效储存期为3个月,不宜久存。

图3.7 水泥石的结构
A—未水化水泥颗粒;B—胶体粒子;C—晶体粒子;D—毛细孔(毛细孔水); E—凝胶孔
3.5.3 水泥石的结构及其影响因素
如图3.7所示,水泥浆硬化后的水泥石是由未水化的水泥颗粒A,凝胶体的水化产物B,结晶体的水化产物C,以及未被水泥颗粒和水化产物所填满的原充水空间D(毛细孔或毛细孔水)及凝胶体中的孔E(凝胶孔)所组成。因此,水泥石是多相(固相、液相、气相)多孔体系。水泥石的工程性质取决于水泥石的结构组成,即取决于水化物的类型和相对含量,以及孔的大小、形状和分布状态等。例如,当水泥的品种一定时,则水化产物的类型也是确定的,这时,水泥石的强度主要取决于水化产物的相对含量(可用水化程度表示)和孔隙的数量、大小、形状及分布状态。后者与拌合时用水量的多少(可用水胶比—即拌合时的用水量与水泥用量之比表示)密切相关。图3.8为两种不同水胶比的水泥净浆 [图3.8(a)的水胶比为0.4,图3.8(b)的水胶比为0.7],处于不同水化程度时水泥石结构的组成示意图。由图3.8可知:同一水胶比的水泥浆,水化程度越高,则水泥石结构中水化物越多,而毛细孔和未水化水泥的量相对减少 [图3.8(a)中A线和B线],因而水泥石结构密实、强度高、耐久性好(水化程度高的B线);对水化程度相同而水胶比不同的水泥石结构而言 [图3.8(b)中B和B1],则水胶比大的浆体(B1)毛细孔所占的比例相对增加,因此,该水泥石的强度和耐久性下降。为了提高水泥石的强度和耐久性,应尽可能减少水泥石中的孔隙含量。因此,降低水胶比,提高水泥浆或混凝土成型时的密实度,以及加强养护等是非常重要的。

图3.8 不同水化程度水泥石结构的组成
由于水泥石的强度与水化产物的数量有关,在相同水泥品种及水胶比下,水化物质数量是随水化时间(龄期)延长而增加的,一般在28d内增长较快,以后渐慢,3个月以后则更缓慢。此外,水化过程还与水化时环境的温度和湿度有关,若水泥处于干燥环境,浆体中水分蒸发完毕后,则水泥无法继续水化,因而强度也不再增长。因此,混凝土工程在浇灌后2~3周内必须加强洒水养护,以保证水化时所必需的水分,使水泥得到充分的水化。温度对水泥凝结硬化的影响也很大,温度越高,凝结硬化的速度越快。因此,采用蒸汽养护是加速凝结硬化的方法之一。当温度较低时,凝结速度比较缓慢,当温度为0℃以下时,硬化将完全停止,并可能遭受冰冻破坏。因此,冬季施工时需要采取保温等措施。
综上所述,在水泥品种一定时,影响水泥石结构强度的主要因素有水胶比、水化时间(龄期)、水化环境的温度和湿度以及施工方法(成型时的振实程度)等。
3.5.4 硅酸盐水泥的技术要求
《通用硅酸盐水泥》(GB 175—2007)对硅酸盐水泥的主要技术性质要求如下。
1.细度
细度是指水泥颗粒粗细的程度,它是影响水泥需水量、凝结时间、强度和安定性能的重要指标。颗粒愈细,与水反应的表面积愈大,因而水化反应的速度愈快,水泥石的早期强度愈高,但硬化体的收缩也愈大,且水泥在储运过程中易受潮而降低活性。因此,水泥细度应适当,根据《通用硅酸盐水泥》(GB 175—2007)规定,硅酸盐水泥和普通硅酸盐水泥的细度用透气式比表面仪测定,要求其比表面积应大于300m2/kg。
2.凝结时间
《通用硅酸盐水泥》(GB 175—2007)规定:硅酸盐水泥初凝时间不得早于45min,终凝时间不大于390min。
凝结时间是指水泥从加水开始到失去流动性,即从可塑状态发展到开始形成固体状态所需的时间,分为初凝和终凝。初凝时间为水泥从开始加水拌合起至水泥浆开始失去可塑性所需的时间;终凝时间是从水泥开始加水拌合起至水泥浆完全失去可塑性,并开始产生强度所需的时间。根据国家标准《水泥标准稠度用水量、凝结时间、安定性检验方法》(GB/T 1346—2011)规定,凝结时间用维卡仪进行测定。在研究水泥凝结过程时,还可以采用测电导率或水化放热速率等方法。
水泥浆体的凝结时间对工程施工具有重要意义。一般要求混凝土搅拌、运输、浇捣在初凝之前完成。因此水泥初凝时间不宜过短;当施工完毕则要求尽快硬化并具有强度,故终凝时间不宜太长。水泥的凝结时间与水泥品种有关。一般来说,掺混合材料的水泥凝结时间较缓慢;凝结时间随水灰比增加而延长,因此混凝土和砂浆的实际凝结时间,往往比用标准稠度水泥净浆所测得的要长得多;此外环境温度升高,水化反应加速,凝结时间缩短,所以在炎热季节或高温条件下施工时,须注意凝结时间的变化。
3.强度
水泥强度是表明水泥力学性能的重要指标,它与水泥的矿物组成、水泥细度、水胶比大小、水化龄期和环境温度等密切相关。国家标准《水泥胶砂强度检验方法(ISO)》(GB/T 17671—1999)规定,采用胶砂法测定水泥强度,又根据3d强度分为普通型和早强型。该法是由按质量计的一份水泥、三份ISO标准砂,用0.5的水灰比拌制的一组塑性胶砂,制成40mm×40mm×160mm的试件,试件连模一起在湿气中养护24h后,再脱模放在标准温度(20±3)℃的水中养护,分别测定3d和28d抗压强度和抗折强度。硅酸盐水泥强度等级分为42.5、42.5R、52.5、52.5R、62.5、62.5R共6个等级。水泥强度等级按规定龄期的抗压强度和抗折强度来划分,各强度等级水泥的各龄期强度不得低于表3.8的数值。
表3.8 硅酸盐水泥的强度等级要求(GB 175—2007)

注R—早强型。
4.体积安定性
体积安定性不良是指已硬化的水泥石产生不均匀的体积变化现象。它会使构件产生膨胀裂缝,降低建筑物质量。
引起体积安定性不良的原因有以下几个方面:
(1)f-CaO过量。
由于熟料烧成工艺上的原因,使熟料中含有较多的过烧f-CaO,其水化活性低,在水泥硬化后才进行下述反应:
CaO+H2O—→Ca(OH)2
该反应固相体积膨胀97%,引起不均匀的体积变化会导致水泥石开裂。国家标准规定用沸煮法检验水泥体积安定性。其方法是将水泥净浆试饼或雷氏夹试件煮沸3h,用肉眼观察试饼未发现裂纹,用直尺检查没有弯曲,或测得雷氏夹试件膨胀量在规定值内,则该水泥体积安定性合格,反之为不合格。沸煮法的原理是通过沸煮加速f-CaO水化,检验其体积变化现象。当试饼法与雷氏夹法结果有争议时,以雷氏夹法为准。
(2)f-MgO过量。
水泥中的f-MgO形成结晶方镁石时,其晶体结构致密,水化比f-CaO更为缓慢,要几个月甚至几年才明显水化,形成氢氧化镁时体积膨胀将导致水泥石安定性不良。由于MgO的水化作用比游离石灰更为缓慢,所以必须采用压蒸法才能检验它的危害程度。由于国家标准中对MgO的含量已有限制,所以一般可不做这项检验。
(3)石膏掺量过多。
水泥中掺有石膏作为调凝剂或作为混合材的活性激发剂,当石膏掺量过多时,在水泥硬化后还会继续与固态水化铝酸钙反应生成高硫型水化硫铝酸钙,体积约增大1.5倍,也会引起体积安定性不良。检验SO3的危害作用用浸水法,由于国家标准中对SO3的含量已有限制,所以一般可不做这项检验。
5.氧化镁、三氧化硫、碱及不溶物含量
熟料中氧化镁含量偏高是导致水泥长期安定性不良的因素之一。熟料中部分氧化镁固溶于各种熟料矿物和玻璃体中,这部分氧化镁并不引起安定性不良,真正造成安定性不良的是熟料中粗大的方镁石晶体。同理,矿渣等混合材料中的氧化镁若不以方镁石结晶形式存在,对安定性也是无害的。因此,国际上有的国家水泥标准规定用压蒸安定性试验合格来限制氧化镁的危害作用是合理的。但我国目前尚不普遍具备做压蒸安定性的试验条件,故用规定氧化镁含量作为技术要求。国家标准规定硅酸盐水泥、普通硅酸盐水泥的MgO质量分数必须小于5.0%,若水泥压蒸安定性合格允许MgO质量分数小于6.0%,其他品种水泥国家标准另有规定。
水泥中的SO3主要来自石膏,SO3过量将造成水泥体积安定性不良。国家标准是通过限定水泥SO3含量控制石膏掺量,国家标准规定矿渣水泥中SO3质量分数不得超过4.0%,其他种类水泥中SO3质量分数不得超过3.5%。
若水泥中碱含量过高,当选用含有活性SiO2的集料配制混凝土时,会产生碱集料反应,严重时会导致混凝土不均匀膨胀破坏。由此而造成的危害,越来越引起人们的重视,因此国家标准将碱含量亦列入技术要求。根据我国的实际情况,国家标准规定:水泥中碱含量按Na2O+0.658K2O计算值来表示,若使用活性集料,用户要求提供低碱水泥时,水泥中的碱质量分数应不大于0.6%或由双方商定。
水泥中的不溶物来自熟料中未参与矿物形成反应的黏土和结晶SiO2,是熟料煅烧不均匀、化学反应不完全的标志。一般回转窑熟料不溶物小于0.5%、立窑熟料小于1.0%,国家标准规定Ⅰ型硅酸盐水泥中不溶物不得超过0.75%、Ⅱ型不得超过1.5%。
6.水化热
水泥的水化反应是放热反应,其水化过程放出的热称为水泥的水化热。水泥的水化热对混凝土工艺有多方面意义。水化热对大体积混凝土为有害的因素,由于水化热积蓄在内部,造成内外温差,形成不均匀应力导致开裂,但水化热对冬季混凝土施工是有益的,可促进水泥水化进程。
水泥的水化放热量及放热速率与水泥的矿物组成有关,根据熟料单矿物水化热测定结果,可测算得硅酸盐熟料中4种主要矿物的水化放热速率。由于水泥的水化热具加和性,所以可根据水泥熟料矿物组成含量,估算水泥水化热。对于硅酸盐水泥,在水化3d龄期内水化放热量大致为总放热量的50%,7d龄期为75%,而3个月可达90%。由此可见,水泥的水化放热量大部分在3~7d内放出,以后逐渐减少。各水泥矿物的水化热及放热速率比较见表3.9。
C3A>C3S>C4AF>C2S
表3.9 硅酸盐熟料矿物的水化热

水泥水化放热量和放热速率还与水泥细度、混合材种类和数量有关。水泥细度愈细,水化反应加速,水化放热速率亦增大。掺混合材可降低水泥水化热和放热速率,因此大体积混凝土应选用掺混合材量较大的水泥。
7.标准稠度及其用水量
在测定水泥凝结时间、体积安定性等性能时,为使所测结果有准确的可比性,规定在试验时所使用的水泥净浆必须以标准方法(按GB 1346规定)测试,并达到统一规定的浆体可塑性稠度,即标准稠度。水泥净浆标准稠度需水量,是指拌制水泥净浆时为达到标准稠度所需的加水量。它以水与水泥质量之比的百分数表示。
8.烧失量
水泥中烧失量的大小,一定程度上反映熟料烧成质量,同时也反映了混合材掺量是否适当,以及水泥风化的情况。国家标准对烧失量规定如下:Ⅰ型硅酸盐水泥烧失量不得大于3.0%, Ⅱ型硅酸盐水泥不得大于3.5%,普通水泥应小于5.0%。由于矿渣水泥中的烧失量不能反映上述情况,因此不予规定。
3.5.5 硬化水泥石的化学腐蚀与防护
水泥制品在一般使用条件下,具有较好的耐久性,但在某些侵蚀介质(软水、含酸或盐的水等)作用下,强度降低甚至造成建筑物结构破坏,这种现象称为水泥石的腐蚀。
水泥石就其本身而言,由于硅酸盐水泥熟料水化后生成氢氧化钙、水化硅酸钙、水化铝酸钙、水化铁酸钙等水化产物。在一般情况下,这些水化产物是稳定的,但在某些条件下也可能不稳定,会发生化学变化,从而引起水泥石结构破坏。水泥石被环境水侵蚀的原因有以下几点:
(1)氢氧化钙及其他成分,能一定程度地溶解于水,特别是软水。
(2)氢氧化钙、水化铝酸钙等都是碱性物质,若环境水中有酸类或某些盐类时,能与其发生化学反应,若新生成的化合物易溶于水或无胶结力,或因结晶膨胀而引起内应力,都将导致水泥石结构的破坏。
3.5.5.1 常见的化学腐蚀及其作用
1.软水侵蚀
不含或仅含少量重碳酸盐(含HCO-3的盐)的水称为软水,如雨水、蒸馏水、冷凝水及部分江水、湖水等。当水泥石长期与软水接触时,水化产物将按其稳定存在所必需的平衡氢氧化钙(钙离子)浓度的大小,依次逐渐溶解或分解,从而造成水泥石的破坏,这就是溶出性侵蚀。
在各种水化产物中,Ca(OH)2的溶解度最大,因此首先溶出,这样不仅增加了水泥石的孔隙率,使水更容易渗入,而且由于Ca(OH)2浓度降低,还会使水化产物依次发生分解,如高碱性的水化硅酸钙、水化铝酸钙等分解成为低碱性的水化产物,并最终变成胶凝能力很差的产物。在静水及无压力水的情况下,由于周围的软水易为溶出的氢氧化钙所饱和,使溶出作用停止,所以对水泥石的影响不大;但在流水及压力水的作用下,水化产物的溶出将会不断地进行下去,水泥石结构的破坏将由表及里地持续发生。当水泥石与环境中的硬水接触时,水泥石中的氢氧化钙与重碳盐酸发生反应:
Ca(OH)2+Ca(HCO3)2—→2CaCO3+2H2O
生成的几乎不溶于水的碳酸钙积聚在水泥石的孔隙内,形成致密的保护层,可阻止外界水的继续侵入,从而阻止水化产物的溶出。
2.盐类侵蚀
某些溶解于水中的盐类会与水泥石相互作用发生置换反应,生成一些易溶或无胶结能力或产生膨胀的物质,从而使水泥石结构破坏。最常见的盐类侵蚀是硫酸盐侵蚀与镁盐侵蚀。硫酸盐侵蚀是由于水中溶有一些易溶的硫酸盐,它们与水泥石中的氢氧化钙反应生成硫酸钙,硫酸钙再与水泥石中的固态铝酸钙反应生成钙矾石,体积膨胀约1.5倍,使水泥石结构破坏,其反应式是:
3CaO·Al2O3·6H2O+3(CaSO4·2H2O)+20H2O—→3CaO·Al2O3·3CaSO4·32H2O
钙矾石呈针状晶体,常称其为“水泥杆菌”。若硫酸钙浓度过高,也可能直接在孔隙中生成二水石膏结晶,产生体积膨胀而导致水泥石结构破坏。
镁盐侵蚀主要是氯化镁或硫酸镁与水泥石中氢氧化钙起复分解反应,生成无胶结能力的氢氧化镁及易溶于水的氯化钙或生成石膏导致水泥石结构破坏,其反应式为
MgCl2+Ca(OH)2—→Mg(OH)2+CaCl2
MgSO4+Ca(OH)2+2H2O—→CaSO4·2H2O+Mg(OH)2
可见,硫酸镁对水泥石的侵蚀包含镁盐与硫酸盐的双重作用。
在海水、湖水、盐沼水、地下水、某些工业污水及流经高炉矿渣或煤渣的水中常含钾、钠、铵等硫酸盐;在海水及地下水中常含有大量的镁盐,主要是硫酸镁和氯化镁。
3.酸类侵蚀
(1)碳酸侵蚀。
在某些工业污水和地下水中常溶解有较多的二氧化碳,这种水对水泥石的侵蚀作用称为碳酸侵蚀。首先,水泥石中的Ca(OH)2与溶有CO2的水反应,生成不溶于水的碳酸钙;接着碳酸钙又继续与碳酸水反应生成易溶于水的碳酸氢钙。反应式为
Ca(OH)2+CO2+H2O—→CaCO3+2H2O
CaCO3+CO2+H2O—→Ca(HCO3)2
当水中含有较多的碳酸,上述反应向右进行,从而导致水泥石中的Ca(OH)2不断地转变为易溶的Ca(HCO3)2而流失,进一步导致其他水化产物的分解,使水泥石结构遭到破坏。
(2)一般酸侵蚀。
水泥的水化产物呈碱性,因此酸类对水泥石一般都会有不同程度的侵蚀作用,其中侵蚀作用最强的是无机酸中的盐酸、氢氟酸、硝酸、硫酸及有机酸中的醋酸、蚁酸和乳酸等,它们与水泥石中的Ca(OH)2反应后的生成物,或者易溶于水,或者体积膨胀,都对水泥石结构产生破坏作用。例如:盐酸和硫酸分别于水泥石中的Ca(OH)2作用:
2HCl+Ca(OH)2—→CaCl2+2H2O
H2SO4+Ca(OH)2—→CaSO4+2H2O
反应生成的氯化钙易溶于水,生成的石膏继而又产生硫酸盐侵蚀作用。
4.强碱侵蚀
水泥石本身具有相当高的碱度,因此弱碱溶液一般不会侵蚀水泥石,但是,当铝酸盐含有较高的水泥石遇到强碱(如氢氧化钠)作用后会被腐蚀破坏。氢氧化钠与水泥熟料中未水化的铝酸三钙作用,生成易溶的铝酸钠:
3CaO·Al2O3+6Na(OH)—→3Na2O·Al2O3+3Ca(OH)2
当水泥石被氢氧化钠浸润后又在空气中干燥,与空气中的二氧化碳作用生成碳酸钠,它在水泥石毛细孔中结晶沉积,会使水泥石胀裂。
除了上述4种典型的侵蚀类型外,糖、氨、盐、动物脂肪、纯酒精、含环烷酸的石油产品等对水泥石也有一定的侵蚀作用。在实际工程中,水泥石的腐蚀常常是几种侵蚀介质同时存在、共同作用所产生的;但固体化合物不会对水泥石产生侵蚀,侵蚀性介质必须呈溶液状且浓度大于某一临界值。水泥的耐蚀性可用耐蚀系数定量表示。耐蚀系数是指同一龄期下,水泥试体在侵蚀性溶液中养护的强度与在淡水中养护的强度之比,比值越大,水泥耐蚀性越好。
3.5.5.2 硬化水泥石的防腐措施
从以上对侵蚀作用的分析可以看出,水泥石被腐蚀的基本内因包括两方面:一是水泥石中存在易被腐蚀的组分,如Ca(OH)2与3CaO·Al2O3;二是水泥石本身不致密,有很多毛细孔通道,侵蚀性介质易于进入其内部。因此,针对具体情况可采取下列措施防止水泥石的腐蚀。
(1)根据侵蚀介质的类型,合理选用水泥品种。
如采用水化产物中Ca(OH)2含量较少的水泥,可提高对多种侵蚀作用的抵抗能力;采用铝酸三钙含量低于5%的水泥,可有效抵抗硫酸盐的侵蚀;掺入活性混合材料,可提高硅酸盐水泥抵抗多种介质的侵蚀作用。
(2)提高水泥石的密实度。
水泥石或混凝土的孔隙率越小,抗渗透能力越强,侵蚀介质越难进入,侵蚀作用越小。在实际工程中,可采用多种措施提高混凝土与砂浆的密实度。
(3)设置隔离层或保护层。
当侵蚀作用较强或上述措施不能满足要求时,可在水泥制品(混凝土、砂浆等)表面设置耐腐蚀性高且不透水的隔离层或保护层。
3.5.6 硅酸盐水泥的特性与应用
1.凝结硬化快,强度高
硅酸盐水泥中含有较多的熟料,硅酸三钙多,水泥的早期强度和后期强度均较高。适用于早期强度要求较高的工程及冬期施工的工程,地上、地下重要结构物及高强混凝土和预应力混凝土工程。
2.抗冻性好
硅酸盐水泥采用较低的水胶比并经充分养护,可获得较低孔隙率的水泥石,具有较高的密实度。因此,适用于严寒地区遭受反复冻融的混凝土工程。
3.耐腐蚀性差
硅酸盐水泥石的氢氧化钙及水化铝酸钙较多,耐软水及耐化学腐蚀能力差,故不适用于经常与流动的淡水接触及有水压作用的工程;也不适用于受海水、矿物水、硫酸盐等作用的工程。
4.耐热性差
水泥石中的一些重要组成部分在高温下会发生脱水和分解,使水泥石的强度下降以至破坏。当受热温度为100~200℃时,由于尚存的游离水能继续发生水化,混凝土的密实度进一步增加,能使水泥石的强度有所提高,且混凝土的导热系数相对较小,故短时间内受热混凝土不会破坏。但当温度较高且受热时间较长时,水泥中的水化产物Ca(OH)2分解为CaO,如再遇到潮湿的环境时,CaO熟化体积膨胀,使混凝土遭到破坏。因此,硅酸盐水泥不宜应用于有耐热性要求的混凝土工程中。
5.耐磨性好
硅酸盐水泥强度高,耐磨性好,适用于道路、地面等对耐磨性要求高的工程。
6.碱度高、抗碳化能力强
碳化是指水泥石中的氢氧化钙与空气中的二氧化碳反应生成碳酸钙的过程。碳化会使水泥石内部碱度降低,从而使其中的钢筋发生锈蚀。其机理可解释为:钢筋混凝土中的钢筋如处于碱性环境中,在其表面会形成一层灰色的钝化膜,保护其中的钢筋不被锈蚀。碳化会使水泥石逐渐由碱性变为中性,当中性深度到达钢筋表面时,钢筋失去碱性保护而锈蚀,导致结构承载能力下降,甚至破坏。硅酸盐水泥由于密实度高且碱度高,故抗碳化能力强,所以适合于重要的钢筋混凝土结构、预应力混凝土工程以及二氧化碳含量高的环境。
7.水化热大
硅酸盐水泥石中含有大量的硅酸三钙和铝酸三钙,水化时放热速度快且放热量大,用于冬期施工可避免冻害,但高水化热对大体积混凝土工程不利,所以,它不适用于大体积混凝土工程。
8.干缩小
硅酸盐水泥在硬化过程中,形成大量的水化硅酸钙凝胶体,使水泥石密实,游离水分少,不易产生干缩裂纹,可用于干燥环境中的混凝土工程。