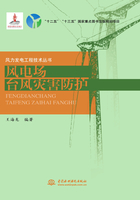
3.1 概述
3.1.1 发展趋势
目前,风电设备明显出现了大型化、变速运行、变桨距、无齿轮箱等发展趋势。
1.大型化
风电机组单机容量持续增大。世界上的主流机型已经从单机容量0.1~1MW增加到3~6MW。
目前,5MW或6MW风电机组已商业化量产,7MW或8MW风电机组也已经过认证并于近期投入市场,并开始研发更大功率的风电机组。图3-1给出了过去30年间,风电机组风轮直径的发展以及单机容量的变化趋势。

图3-1 国际风电机组单机容量变化趋势
2.变速运行
与恒速运行的风电机组相比,变速运行的风电机组具有发电量大、对风速变化的适应性好、生产成本低、效率高等优点。
3.变桨距
国内新安装的风电机组多采用变桨距功率调节方式。其优点是启动性能好、输出功率稳定、结构受力小、停机方便安全;其缺点是增加了变桨装置、控制程序比较复杂、故障率增高。
4.变速恒频
随着电力电子技术的进步,大型变流器在大型双馈风电机组及直驱式风电机组中得到了广泛应用,使得机组在低于额定风速下具有较高的效率,结合变桨距技术的应用,在高于额定风速下使发电机功率更加平稳,但机组造价较高。
5.水平轴
由于水平轴风电机组的技术特点突出且性能稳定,经过多年的发展和运行,现已成为风电装备产业发展的主流机型,占到95%以上的市场份额。而同期发展的垂直轴风电机组因风能利用率较低以及启动、停机和功率调节等问题,尚难以得到市场全面的认可和推广应用,但国内外对垂直轴机组的相关研究和开发并没有停止。
6.无齿轮箱直驱
无齿轮箱的直驱式风电机组能有效地减少由于齿轮箱故障造成的停机,提高系统的运行可靠性和寿命,减少维护成本,因而得到了市场的青睐,且在市场上占有了一定比例。
7.新技术和新机型
鉴于风电装备产业在未来能源生产中的重要性,发达国家十分重视相关的技术研发,并陆续推出了一些新颖的设计方案。如采用新型材料制成的柔性叶片可改善桨叶受力,根据空气动力学理论设计的新型叶片还可更好地实现低风速的风能利用。另外,对风电机组的创新设计也在不断进行着,如混合式风电机组、半直驱式风电机组等。
8.发电机并网及低电压穿越
为了使风电能够得到大规模的应用,当电网发生的电压跌落故障在一定范围内时,要求风电机组不能脱离电网并且能向电网提供有功功率和无功功率支撑。为此对风电场及风电机组并网提出了严格的技术要求,包括低电压穿越能力、无功控制能力、有功功率变化率控制和频率控制等。
3.1.2 基本结构
按照功率传递的机械连接方式的不同,大型并网型水平轴风电机组可分为有增速齿轮箱型和无齿轮箱的直驱型两种,其基本结构如图3-2所示。其中:有齿轮箱型风电机组的叶轮通过齿轮箱及其高速轴及万能弹性联轴节将转矩传递到发电机的传动轴联轴节,具有很好地吸收阻尼和振动的特性,可吸收适量的径向、轴向和一定角度的偏移,并且联轴器可阻止机械装置的过载;直驱型风电机组,直接将叶轮的转矩传递到发电机的传动轴,使风电机组发出的电能同样能并网输出。这样设计的优点是简化了装置的结构,减少了故障的概率,多用于大型风电机组。

图3-2 风电机组的机舱内部结构
大型并网型风电机组有以下组成机构:
(1)叶片。吸收风能的单元,用于将空气的动能转换为叶轮转动的机械能。风以一定速度和攻角作用于叶片上,使叶片产生旋转力矩,驱动风轮主轴旋转,将风能转换成旋转机械能。
(2)轮毂。将叶片固定在一起,并且承受叶片上传递的各种荷载,然后传递到发电机转动轴上。
(3)变桨距机构。通过改变叶片的桨距角,使叶片在不同风速时处于最佳的吸收风能状态,当风速超过切出风速时,使叶片顺桨刹车。
(4)主轴。也指低速轴,将转子轴心与齿轮箱连接在一起。
(5)齿轮箱。齿轮箱是将风轮在风力作用下所产生的动力传递给发电机,并使其得到相应的转速。
(6)发电机。发电机是将叶轮转动的机械动能转换为电能的部件。分为异步发电机、同步发电机、双馈异步发电机和永磁发电机等。
(7)偏航机构。与控制系统相配合,使叶轮始终处于迎风状态,充分利用风能,提高发电效率。同时提供必要的锁紧力矩,以保障机组安全运行。一般由风向传感器、偏航电动机、偏航轴承和齿轮等组成。
(8)机舱。由底盘和机舱罩组成。机舱包容着风力发电机的关键设备,包括齿轮箱、发电机。
(9)塔架。是机舱及叶轮系统的支撑结构。
(10)底座总成。主要由底座、下平台总成、内平台总成、机舱梯子等组成。通过偏航轴承与塔架相连,并通过偏航系统带动机舱总成、发电机总成、变桨系统总成。
(11)测风仪。主要用于测量实时风速、风向等。
此外,风轮和机舱置于塔架顶端,机舱内有风轮主轴、传动系统、发电机等部件。机舱内的所有部件均安装在主机架上,主机架通过轴承与塔架顶端相连接,可以在偏航系统的驱动下,相对于塔架轴线旋转,使风轮和机舱随着风向的变化调整方向。塔架固定在基础上,将作用于风轮上的各种荷载传递到基础上。
3.1.3 主要机组类型
1.上风向机组和下风向机组
水平轴风电机组根据在运行中风轮与塔架的相对位置,分为上风向风电机组和下风向风电机组,如图3-3所示。

图3-3 上风向和下风向的风电机组
上风向机组的风轮位于塔架和机舱前端,工作时,来风首先吹向风轮,因而塔架和机舱对来风的扰动较小,但需要有偏航驱动装置,保证风轮始终朝向来风方向。下风向机组的风轮位于塔架和机舱后端,工作时,来风先经过塔架和机舱再吹向风轮,因此塔架和机舱对来风扰动较大,影响风轮的风能吸收量,但下风向机组可以实现自动对风,因此不需要偏航驱动装置。
目前实际应用的风电机组以上风向机组为主,下风向机组较少。
2.失速机组与变桨机组
当风速超过额定风速时,为了保证发电机的输出功率维持在额定功率附近,需要对风轮叶片吸收的气动功率进行控制。对于确定的叶片翼型,在风作用下产生的升力和阻力主要取决于风速和攻角i,在风速发生变化时,通过调整攻角,可以改变叶片的升力和阻力比例,实现功率控制。
按照功率调节方式不同,风电机组分为失速调节式和变桨距调节式,相应的结构也不相同。
(1)失速调节式风电机组主要利用叶片的气动失速特性实现功率调节,即当入流风速超过一定值时,在叶片后端将形成湍流状态,使升力系数下降,而阻力系数增加,从而限制了机组功率的进一步增加。失速调节又分为被动失速和主动失速两种类型。
1)被动失速风电机组叶片与轮毂采用固定连接,叶片的桨距角不能发生变化,因此也被称为定桨距风电机组。其主要优点是结构简单;缺点是超过额定风速区段的输出功率不能保证恒定,并且由于阻力增大,导致叶片和塔架等部件承受的荷载相应增大。此外,由于被动失速风电机组的叶片桨距角不能调整,没有气动制动功能,因此定桨距叶片在叶尖部位需要设计专门的制动刹车机构。
2)主动失速风电机组同样利用叶片的气动失速特性实现功率调节,但其叶片与轮毂不是固定连接,叶片可以相对轮毂转动,实现变桨距角调节。当机组达到额定功率后,使叶片向桨距角β减小的方向转过一个角度,增大来风的攻角i,使叶片主动进入失速状态,从而限制功率。主动失速风电机组改善了被动失速风电机组功率调节的不稳定性,但是增加了桨距调节机构的调节式,使设备变得复杂。
(2)变桨距风电机组的叶片和轮毂与主动失速风电机组的同样,不是固定连接,叶片桨距角可调;所不同的是变桨距风电机组在超过额定风速范围时,通过增大叶片桨距角β,使攻角i减小,以改变叶片升力FL与阻力FD的比例,达到限制风轮功率的目的,使风电机组能够在额定功率附近输出电能。变桨距风电机组在高于额定风速区域可以获得稳定的功率输出,但调节设备的结构复杂,可靠性降低。
3.带增速齿轮箱、直驱式和半直驱式风电机组
风电机组通过传动系统连接风轮和发电机,把风轮产生的旋转机械能传输到发电机,并使发电机转子达到所需要的转速。由于风轮转速一般较低,约10~20r/min,而发电机要输出50Hz的交流电功率,这就要求发电机转子转速根据发电机的磁极对数的不同而调整。例如当磁极对数为2时,要求发电机其转子转速在1500r/min左右,这时需要在风轮与发电机组之间用齿轮箱进行增速。如果发电机的磁极对数足够大,使得发电机转速与风轮转速接近,就不需要增速齿轮箱。风电机组按照是否有增速齿轮箱可以分为带增速齿轮箱的风电机组、直驱式风电机组和半直驱式风电机组。
带增速齿轮箱风电机组的发电机,由于磁极对数小,因而结构比较简单,体积小。但是由于需要齿轮增速箱,因此传动系统结构比较复杂,齿轮箱设计、运行维护复杂,容易发生故障。
直驱式风电机组的风轮直接驱动发电机转子旋转,不需要齿轮箱增速,从而提高了传动效率和可靠性,减少了故障点。但是直驱式机组的发电机磁极对数高,体积比较大,结构也复杂得多。
半直驱式风电机组是一种折中方案,其发电机的磁极对数少于直驱式发电机,利用增速比相对较小的齿轮箱进行增速,这样既可以降低齿轮箱的设计、运行维护难度,也使发电机结构相对简单。
4.陆地风电机组和海上风电机组
安装在内陆地区和沿海地区的风电机组在基本结构上并无太大差别,但是由于沿海风电场的风况和环境条件与陆地风电场存在差别,因此海上风电机组具有一些特殊性,主要表现在以下方面:
(1)目前建成的海上风电场一般处于离海岸较近的中浅海域,海水深度小于30m。海上风速通常比沿岸陆地高,而且由于海面平坦,没有障碍物,因此风速比较稳定,不受地形影响,风湍流强度和风切变都比较小,并且具有稳定的主导风向,因此海上风况条件优于陆地。适合选用大容量风电机组,而且在相同容量下,海上风电机组的塔架高度比陆地机组低。
(2)海上风电场遭遇极端气象条件的可能性大,强阵风、台风和巨浪等极端恶劣天气条件都会对机组造成严重破坏,因此对于风电机组安全可靠性要求更高。海上风场与海浪、潮汐具有较强的耦合作用,使得风电机组运行在随机海浪干扰下的风场中,荷载条件比较复杂。此外,海上风电机组长期处在含盐湿热雾腐蚀环境中,加之海上风电机组安装、运行、操作和维护等方面都比陆地风场困难,因此,海上风电机组结构,尤其是叶片材料的耐久性问题极为重要。
(3)海上风电机组与陆地风电机组的最主要区别在于基础型式。由于不同海域的水下情况复杂,基础建造需要综合考虑海床地质结构、离岸距离、风浪等级、海流情况等多方面影响,因此海上风电机组的基础比陆地风电机组要复杂得多,用于基础建设的费用也相对较大。随着海上风电的发展,风电场将逐渐向较深海域扩展,风电机组的基础问题将更加突出。
除了机组设备的特殊性以外,海上风电在风资源评估、机组安装、运行维护、设备监控、电力输送等许多方面都与陆地风电存在差异,技术难度大、建设成本高。
3.1.4 主要参数
风电机组的性能和技术规格可以通过风轮直径与扫掠面积,轮毂高度,叶片数,额定风速、切入风速和切出风速,风轮转速和叶尖速比,风轮锥度和风轮仰角以及偏航角等一些主要参数反映。
1.风轮直径与扫掠面积
风轮直径是风轮旋转时的外圆直径。风轮直径大小决定了风轮扫掠面积的大小,是影响风电机组容量大小和机组性价比的主要因素之一。
风轮直径增加,则其扫掠面积成平方增加,根据贝茨理论,获取的风功率也成平方增加。图3-1示出了过去30年来风电机组风轮直径和相应功率的发展变化情况。早期的风电机组直径很小,额定功率也相对较低。目前大型兆瓦机组的风轮直径在70~80m范围,目前已有风轮直径接近180m,额定功率超过若干兆瓦的风电机组已投入商业运行。
2.轮毂高度
轮毂高度是指风轮轮毂中心离地面的高度,也是风电机组设计时要考虑的一个重要参数,由于风剪切特性,离地面越高,风速越大,具有的风能也越大,因此大型风电机组的发展趋势是轮毂高度越来越高。但是轮毂高度增加,所需要的塔架高度也相应增加,当塔架高度达到一定水平时,设计、制造、运输和安装等方面都将产生新的问题,也导致风电机组成本的相应增加。
3.叶片数
风电机组的基本性能主要指其吸收和转化风能的性能,即风轮的气动性能。功率特性是反映风电机组基本性能的重要指标,用风电机组输出功率随风速的变化曲线(P-V)来表示,也称作风电机组的功率曲线。功率曲线直接影响风电机组的年发电量。理论风功率与风速的三次方成正比,而根据贝茨定理,理想风轮只能吸收部分风功率(极限状态下,只能吸收理论风功率的0.593倍),实际风电机组的风轮不满足理想风轮条件,并且存在各种损失,其风能吸收量低于贝茨极限。风电机组的发展过程,一直是追求使机组的风能吸收量接近贝茨极限的过程。
选择风轮叶片数时要考虑风电机组的性能和荷载、风轮和传动系统的成本、风力机气动噪声及景观效果等因素。
采用不同的叶片数,对风电机组的气动性能和结构设计都将产生不同的影响。风轮的风能转换效率取决于风轮的功率系数。图3-4示出了不同类型风轮的功率系数CPR随叶尖速比λ的变化曲线,其中:现代水平轴风电机组风轮的功率系数比垂直轴风轮高,其中三叶片风轮的功率系数最高,其最大功率系数CPR≈0.47,对应叶尖速比λ≈7;双叶片和单叶片风轮的风能转换效率略低,其最大功率系数对应的叶尖速比也高于三叶片风轮,即在相同风速条件下,叶片数越少,风轮最佳输出功率对应的转速越高。因此,有时也将单叶片和双叶片风轮称为高速风轮。相比之下,多叶片风轮的最佳叶尖速比比较低,风轮转速可以很慢,因此也称为慢速风轮。多叶片风轮由于功率系数低很多,因而很少用于现代风电机组。

图3-4 不同叶片数风轮的功率系数随叶尖速比的变化曲线
风轮的作用是将风能转换成推动风轮旋转的机械转矩。因此用于衡量风轮转矩性能的另一个重要参数是转矩系数CQR,它定义为功率系数除以叶尖速比。转矩系数决定了传动系统中主轴及齿轮箱的设计。现代并网风电机组希望转矩系数小,以降低传动系统的设计费用。图3-5示出了几种具有不同叶片数的水平轴风轮的转矩系数CQR随叶尖速比λ的变化曲线。可以看出,叶片数越多,最大转矩系数值也越大,对应的叶尖速比也越小,启动转矩就越大。

图3-5 不同叶片数风轮的转矩系数随叶尖速比的变化曲线
综上分析,三叶片风轮的性能比较好,目前,水平轴风电机组一般采用双叶片或三叶片风轮,其中以三叶片风轮为主。国内安装投运的大型并网风电机组几乎全部采用三叶片风轮。
叶片数量减少,将使风轮制造成本降低,但也会带来很多不利的因素,在选择风轮叶片数时要综合考虑。例如双叶片风轮上的脉动荷载要大于三叶片风轮,因此双叶片风轮采用跷跷板式柔性轮毂。另外,由于双叶片风轮转速高,在旋转时将产生较大的空气动力噪声,对环境产生不利影响,而且风轮转速快,视觉效果也不佳。
风轮实度也常用于反映风轮的风能转换性能,风轮实度定义为风轮叶片总面积与风轮扫掠面积的比值。风轮的叶片数多,风轮实度大,功率系数比较大,但功率曲线较窄,对叶尖速比的变化敏感。叶片数减少,风轮实度下降,其最大功率系数相应降低,但功率曲线也越平坦,对叶尖速比变化越不敏感。
4.额定风速、切入风速和切出风速
风电机组输出功率与机组设计风速密切相关,所谓设计风速一般包括额定风速、切入风速和切出风速,具体如下:
(1)额定风速指风电机组达到额定功率对应的风速时,额定风速的大小直接影响到机组的总体构成和成本。额定风速应匹配风电机组所在区域的风能资源分布,需要事先掌握平均风速及其出现的频率。可以参照风速条件,按一定的原则评估额定风速。
(2)切入风速和切出风速也是反映机组性能的重要设计参数:切入风速指风电机组开始并网发电的最低风速,决定了机组在低风速条件下的性能;切出风速则主要用于在极端风速条件下,对机组进行停机保护。当风速达到切出风速时,机组将实施制动停机。
5.风轮转速和叶尖速比
叶尖速比λ是描述风电机组风轮特性的一个重要的无量纲量,定义为风轮叶片尖端线速度与风速之比。
对于特定的风轮型式,其功率系数与尖速比λ的关系由图3-4中曲线确定。在某一叶尖速比值处,功率系数达到最大值,此时,风轮吸收的风能最多,对应的叶尖速比值称为最佳叶尖速比。风电机组风轮的一个主要设计目标是尽可能多地吸收风能,因此在低于额定风速的区域,希望使风轮尽可能工作在最大功率系数附近,即风轮转速与风速的比值尽可能保持在最佳叶尖速比附近。由于风速是连续不断变化的,因此需要对风轮的转速进行控制,使之与风速变化匹配。对于风轮转速的控制有恒速、双速和变速控制等多种方式。
实际风电机组的风轮转速范围的确定,还要考虑其他多种因素。风轮转速除了影响风能吸收特性以外,还对风轮的机械转矩产生影响。当风电机组的额定功率和风轮直径确定后,风轮转速增加,则风轮转矩减小,因而作用在传动系统上的荷载也相应减小,并使齿轮箱的增速比降低。
6.风轮锥角和风轮仰角
风轮锥角是叶片与风轮主轴相垂直的旋转平面的夹角,风轮仰角是风轮主轴与水平面的夹角。由于叶片为细长柔性体结构,在其旋转过程中,受风荷载和离心荷载的作用,叶片将发生弯曲变形,风轮锥角和仰角的作用是防止叶片在发生弯曲变形的状态下,其叶尖部分与塔架发生碰撞。
7.偏航角
偏航角是通过风轮主轴的铅垂面与风矢量在水平面上的分量的夹角。风电机组在运行过程中,根据测量的风矢量方向,通过偏航系统对风轮的方向进行调整,使其始终保持正面迎向来风方向,以获得最大风能吸收率。