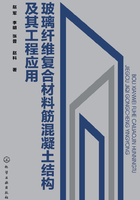
3.3 基本力学性能
GFRP筋的基本力学性能主要包括:抗拉强度、抗压强度、弯曲强度、剪切强度和抗扭刚度等指标。
3.3.1 抗拉强度
可参考《拉挤玻璃纤维增强塑料杆力学性能试验方法》(GB/T 13096—2008),采用1000kN电伺服万能试验机。如图3-3所示,对GFRP筋进行拉伸性能测试,采用试验机配置的小变形计测量GFRP筋的拉伸变形,得到延伸率、弹性模量和极限抗拉强度。

图3-3 锚具试样示意图
1—试样;2—钢管;3—锚具填充物;d—试样直径;l0——测试部分长度;l1——锚具部分长度锚具填充物可用环氧树脂或者1∶1的树脂和净砂浆混合物,或者水泥灌浆。填充材料应与纤维固化树脂等相容,确保试样在拉伸试验中不会发生与锚具的拔出滑移
试验主要参数如下。
①试件尺寸及形状:如图3-3所示。
②测量试件直径和标距,测量精确到1mm。
③试验环境:温度25℃±2℃。
④加载速度应控制在100~500MPa/min范围内,保持均匀加载,若试验采用应变控制方法,应变增长速率应和前述应力加载速度换算后一致。
⑤试件数量:每组试样不少于5个。
⑥安装测量变形的小变形计于试件中部,对试件进行预加载至试验机夹具将试件牢牢夹死;为了避免引伸计破换,继续加载至60kN时将引伸计取下,然后继续加载至试样破坏,记录最大荷载值及试样破坏形式,测量抗拉强度、拉伸弹性模量、延伸率及应力-应变曲线等材料性能指标。
⑦在锚固段内破坏、锚具附近处破坏以及筋材从锚具中滑出的试样应予作废。同批有效试样不足5个时,应从同一批筋材中补做相应数量的试样。
强度计算如下。
荷载(应力)-应变曲线由数据采集系统采集的数据得到。
拉伸强度按式(3-1)计算,取三位有效数字。
(3-1)
式中 σb——拉伸强度,MPa;
Pb——极限荷载,N;
A——试样的横截面面积,mm2。
弹性模量按式(3-2)计算,取三位有效数字。
(3-2)
式中 EL——弹性模量,MPa;
P1——达到试样极限拉伸强度的60%时的荷载,N;
ε1——达到试样极限拉伸强度的60%时的应变,无量纲;
P2——达到试样极限拉伸强度的20%时的荷载,N;
ε2——达到试样极限拉伸强度的20%时的应变,无量纲;
A——同式(3-1)。
极限应变按式(3-3)计算,取三位有效数字。
(3-3)
式中 εu——极限应变,无量纲;
Pb——同式(3-1);
EL——同式(3-2);
A——同式(3-1)。
3.3.2 拉伸性能测试
本小节参考《拉挤玻璃纤维增强塑料杆力学性能试验方法》(GB/T 13096—2008),1000kN电伺服万能试验机,如图3-4(a)所示,对GFRP筋进行拉伸性能测试,采用试验机配置的大变形计测量GFRP筋的拉伸变形,得到极限延伸率、弹性模量和极限抗拉强度。
根据参考文献的试验方法,制成用环氧树脂和固化剂作为填充物的黏结式锚具试样,如图3-4(b)所示。本实验采用的GFRP筋材直径为12mm,肋间距分别为10mm、20mm、30mm,缠绕物分别为尼龙绳、一层玻璃纤维束和两层玻璃纤维束。

图3-4 拉伸性能测试仪器及试件
根据ACI规范规定,对纤维塑料增强聚合物筋进行拉伸性能测试时,要保证两端锚具间有效长度不小于筋材直径的40倍,本试验设计GFRP拉伸试件总长L=1240mm,标距L0=640mm,两端采用套管锚固,锚固长度均为L=300mm。套管采用的镀锌钢管,为外径32mm、壁厚3mm的国标管。将生产的不同表面缠绕方式的GFRP筋在切割机上截取所需要的试件长度,然后将灌注用的环氧树脂灌入下端密封的钢套管中,将筋材缓缓插入套筒内,使其充分固结,经一段时间待完全固化后,将试件的另一端以同样的方法灌注,完全固化后可进行试验。本试验所做的试样尺寸如图3-4(b)所示。
制作试验试件时应注意:
①进行灌注时保证钢套筒的下端是完全密封的,避免灌注胶流出;
②插入筋材时要尽量保证对中,最好采取一定的措施,如套筒的两端用中孔的垫片,以保证试验数据的真实有效;
③环氧树脂一定要达到固化时间,以保证试验的成功率;
④特别注意补胶,因为灌注所用的环氧树脂经固化反应后体积会减小,如果不及时补胶就会造成钢管中胶不满,容易造成拉伸测试时筋材拔出,测试失败。
3.3.2.1 试验现象
试验过程中,测得的典型GFRP筋应力-应变曲线如图3-5和图3-6所示。对于浅肋的GFRP筋材,从开始受荷至完全破坏的受力过程中,应力-应变关系在达到极限强度前近似为一条斜直线。当荷载强度达到极限抗拉强的40%左右时,开始出现细微的断裂声,疑似基底树脂断裂的声响,随着荷载的增加断裂声响逐渐加剧,当达到极限荷载前,出现急促而又绵密的响声,此时增强纤维开始断裂,当达到极限强度后,荷载曲线突然下降,不会出现明显的区服阶段,在GFRP即将达到极限荷载时,明显可以观察到筋材表面纤维出现断裂,并伴随剧烈爆炸声,整个筋材发生炸裂是破坏,如图3-7(a)所示。

图3-5 浅肋GFRP筋典型的应力-应变曲线

图3-6 深肋GFRP筋典型的应力-应变曲线

图3-7 浅肋GFRP筋和深肋GFRP筋破坏形式
对于深肋的GFRP筋材,开始加载时明显出现筋材表面的纤维迅速变形,反映在应力-应变曲线上则是加载前期不是一条直线,会有一段较为平滑的曲线,并伴随有“噼啪”声,为纤维与树脂的剥离声,因为筋材表面的肋较深,表层纤维的弯曲程度较大,加载前期表层纤维有一个先被拉直的过程,整个筋材截面纤维没有共同受力,随着荷载继续增大,当荷载增加到极限荷载的30%~50%时,应力-应变曲线开始呈现一条直线,达到极限荷载时,筋材一般会在中部断裂,整个筋材会瞬间散开,如图3-7(b)所示。
由于GFRP筋强度较高,在测试拉伸强度时部分试件出现破坏而不能测出有效的拉伸强度,主要的破坏形式有以下两种:①试件从GFRP筋中部位置破坏,为有效试件;②GFRP筋从黏结套筒中滑出或直接将套筒两端堵头拉断,为无效试件,如图3-8和图3-9所示。

图3-8 拉伸试样破坏形式(一)

图3-9 拉伸试样破坏形式(二)
3.3.2.2 试验数据处理
(1)试验原始数据处理 对不同表面缠绕方式的GFRP筋进行拉伸性能测试,得到筋材的极限抗拉强度,根据ACI规范规定,将应力-应变曲线中应力值20%~50%的数据取出,得到这一段的斜率即为拉伸弹性模量,试验结果见表3-7。
表3-7 GFRP筋拉伸试验结果

注:试样编号中18、27代表筋材肋间距18mm、27mm;-1、-2代表筋材为深肋、浅肋;-01、-02、-03、-04、-05等代表一组试验试件的编号。
(2)试验数据进一步处理 数理统计中对数据的处理方法主要有以下几种。
①平均数
(3-4)
平均数表示一组数据中所有数据之和再除以数据的个数,它是反映数据集中趋势的一项指标。
②方差
(3-5)
D(x)是表示x取值分散程度的一个量,它是衡量x取值分散程度的一个尺度。若x的取值比较集中,则方差D(x)较小;若x的取值比较分散,则方差D(x)较大。
③协方差 协方差表示的是两个变量总体误差的方差。
④相关系数
(3-6)
相关系数用来度量两个变量间的线性关系和相关程度。
根据以上数据处理的方法对数据求平均值、方差,见表3-8和表3-9。
表3-8 数据平均值

注:试样编号中18、27代表筋材肋间距18mm、27mm;-1、-2代表筋材为深肋、浅肋。
表3-9 数据方差

注:试样编号中18、27代表筋材肋间距18mm、27mm;-1、-2代表筋材为深肋、浅肋。
3.3.2.3 试验数据及结果分析
(1)肋深对抗拉性能的影响 通过表3-8中数据分析得图3-10。根据试验数据和对比图可知,在肋间距相同时肋深对拉伸性能产生很大的影响。对于肋间距为18mm的筋材,由深肋GFRP筋到浅肋GFRP筋,极限抗拉强度增加83.9%,弹性模量增加61.1%;对于肋间距为27mm的筋材,由深肋GFRP筋到浅肋GFRP筋,极限抗拉强度增加103%,弹性模量增加71.3%,在工程实际应用中,浅肋GFRP筋材可以大大减小使用量,并且减小梁、板等受力混凝土结构的变形和裂缝宽度。

图3-10 不同表面缠绕方式对拉伸性能的影响
图示中1~4分别代表表3-8中的18-1、27-1、18-2、27-2 GFRP筋材
通过表3-9中数据分析得图3-11。根据试验数据和对比图可知,S27-1的GFRP筋材不管是抗拉强度还是弹性模量都的方差比其他类型的筋材大很多,说明这种筋材本身的离散程度远远大于其他类型的GFRP筋;对于深肋的筋材,肋间距对抗拉强度离散性的影响较大,造成这种结果的原因可能是由材料自身各向异性和生产工艺决定的。

图3-11 不同表面缠绕方式对拉伸性能离散程度的影响
图示中1~4分别代表表3-9中的18-1、27-1、18-2、27-2 GFRP筋材
如图3-12~图3-15所示为肋间距为18mm和27mm肋深不同的GFRP筋材的应力-应变曲线。
从图3-12~图3-15应力-应变曲线可以明显看出,浅肋的GFRP筋材弹性阶段为一条斜率基本没有变化的直线,这与材料本身为线弹性材料有关;深肋的GFRP筋材弹性阶段均存在一个直线斜率变化的过程,这与材料的线弹性不相符,因为深肋的GFRP筋表层很厚的一层材料呈现很大的弯曲,在受到拉伸时同一截面内的纤维没有同时受力,表面纤维有一个先拉直后承受荷载的过程。

图3-12 S18应力应变曲线
图示中S、D分别表示浅肋、深肋;18、27表示肋间距为18mm、27mm,下同

图3-13 S27应力应变曲线

图3-14 D18应力应变曲线

图3-15 D27应力应变曲线

图3-16 新鲜的树脂
(2)肋间距对拉伸性能的影响 从图3-10和图3-11可知,肋间距对抗拉强度和弹性模量几乎没有影响,不管是深肋还是浅肋,随着肋间距的增大,极限延伸率有略微增加;而对于抗拉强度和弹性模量的方差,即抗拉强度和弹性模量的离散程度有较大影响。
3.3.2.4 树脂黏度对拉伸性能的影响
在研究GFRP筋材生产过程中发现,随着时间的增长,浸胶槽里面的树脂会发生细微的变化,新鲜的树脂如图3-16所示,为透明色且黏度较小,在生产过程中玻璃纤维表面的硅烷偶联剂和其他浸润剂会逐渐溶解到树脂中,同时也会有一定量的空气以微小气泡的形式进入到树脂内,使树脂由透明色逐渐地变浑浊,黏度也逐渐增大,如图3-17所示。

图3-17 使用过程中变浑浊的树脂
本试验用如图3-18所示的黏度计在生产过程中测试不同时间段浸胶槽中树脂的黏度,并对此时间段内经浸胶槽玻璃纤维生产的筋材进行标记,以便测试树脂黏度对于筋材拉伸性能的影响。如图3-19所示为实测的树脂黏度随时间的变化曲线;如图3-20所示为与实测黏度相应的GFRP筋抗拉强度。

图3-18 黏度测试图

图3-19 实测的树脂黏度随时间的变化曲线
由于测试黏度时在浸胶槽中取胶位置以及不同批次环境等的差别,会造成测试树脂黏度有部分差异,但总体上树脂黏度在前期变化不大,中后期会有显著增大。随着树脂黏度的增加,玻璃纤维的挂胶能力会下降,从图3-20中抗拉强度变化曲线中可知,虽然强度有差异,但这些差异是由于筋材本身的离散性所决定的,与树脂黏度无关。因此,只要浸胶槽中树脂足够量,能够完全浸没纤维,则基底树脂的黏度对于筋材本身的抗拉性能不会产生大的影响。

图3-20 与测试黏度相应的GFRP筋抗拉强度
通过上述研究,得出如下结论。
①对于肋间距为18mm的筋材,由深肋GFRP筋到浅肋GFRP筋,极限抗拉强度增加83.9%,弹性模量增加61.1%。
②对于肋间距为27mm的筋材,由深肋GFRP筋到浅肋GFRP筋,极限抗拉强度增加103%,弹性模量增加71.3%。
③肋间距对抗拉强度和弹性模量几乎没有影响,不管是深肋还是浅肋,随着肋间距的增大,极限延伸率有略微增加;而对于抗拉强度和弹性模量的方差,即抗拉强度和弹性模量的离散程度有较大影响,深肋的GFRP筋抗拉强度随肋间距的不同,离散程度很大。
④只要浸胶槽中树脂足够量,能够完全浸没纤维,则基底树脂的黏度对于筋材本身的抗拉性能不会产生大的影响,树脂黏度对于GFRP筋拉伸性能几乎没什么影响。
3.3.3 抗压强度
参考《纤维增强塑料压缩性能试验方法》(GB/T 1448—2005)有关要求,采用的GFRP筋材直径分别为10mm、12mm、14mm、16mm,缠绕物为尼龙绳、一层玻璃纤维束和一层玻璃纤维束,制作试样如图3-21所示,试样的基本尺寸是H/d=3(H为试样高,d为试样直径),如图3-22所示。

图3-21 压缩测试试件

图3-22 FRP筋抗压试件示意图
3.3.3.1 试验现象
如图3-23(a)所示为压缩试验典型的应力-应变曲线,试验加载前期,曲线较为平滑,随后试件承受压力不断增大,当试件中树脂和玻璃纤维间的横向拉应力过大时,树脂与玻璃纤维黏结较差的薄弱点附近首先出现树脂与纤维剥离的现象,随着荷载的继续增加,树脂与纤维的剥离区也不断增大,直至最后产生纵向劈裂裂缝而破坏,如图3-23(b)所示。
GFRP筋的破坏较为突然,破坏前基本上无明显预兆,破坏时伴有很大的响声。试样主要有两种破坏形式:①由于压力过大使压缩试件两端的玻璃纤维束散掉,此时端部呈圆台状;②试样沿纵向产生劈裂裂缝而破坏。
3.3.3.2 结果分析
对不同表面缠绕方式的GFRP筋进行压缩性能测试,试验数据见表3-10,通过理论分析得图3-23。由图3-23可知表面采用玻璃纤维束缠绕与表面缠绕尼龙绳的GFRP筋相比,可以明显提高小直径GFRP筋的抗压强度,提高幅度分别为59%(d=10mm)和41.6%(d=12mm),但是对大直径GFRP筋提高不明显。这是因为当压缩试样承受压力时,玻璃纤维束缠绕在筋表面,对试样有一定约束作用,相当于箍筋的作用,抑制了压缩试样的横向变形,从而提高了抗压强度。直径较大时,由于成型工艺不完善,约束效果较差,提高效果不明显。另外,缠绕层数对抗压强度的影响不明显。
表3-10 GFRP筋压缩试验结果


图3-23 压缩性能破坏及分析图
3.3.4 弯曲强度
采用CMT系列电伺服50kN万能试验机并配以三点受弯测试夹具(图3-24)进行抗弯试验。

图3-24 三点弯曲测试图
本次试验采用的GFRP筋材直径为16mm,肋间距为18mm、27mm,肋深为深肋和浅肋,表面缠绕物为尼龙绳,试件长度为130mm,试验参数主要如下。
①试件尺寸及形状:如图3-25所示。

图3-25 弯曲试件试样
②测量试件直径和标距,测量精确到1mm。
③试验环境:温度25℃±2℃。
④加载速度:2mm/min。
⑤试件数量:每组试样不少于5个。
⑥安装三点受弯测试夹具时要将下半部夹具两端点牢牢固定在底座上,避免下部两端点由于受到很大的力而向两侧滑移,设置预加载为300N,测量抗弯强度与应力-应变曲线。
⑦有效试样不足5个时,应重做试验。
3.3.4.1 试验现象
试件刚开始加载便听见细微的声响,疑似GFRP筋材底部树脂断裂,然后出现一段较为平静的阶段,当荷载增大到极限荷载附近时,出现较为密集的噼啪声响,此时纤维与树脂剥离,并伴随有碎屑迸出,随后会出现玻璃纤维断裂的声响,荷载急剧下降破坏。
3.3.4.2 试验数据处理
(1)原始试验数据处理 对不同表面缠绕方式的GFRP筋进行弯曲性能测试,得到筋材的极限抗弯强度,试验数据见表3-11。
表3-11 GFRP筋弯曲试验结果

注:试样编号中18、27代表筋材肋间距18mm、27mm;-1、-2代表筋材为深肋、浅肋;-01、-02、-03、-04、-05、-06代表一组试验试件的编号。
(2)试验数据的优化处理 对表3-11中的数据进行优化处理得表3-12,方差和标准差见表3-13。
表3-12 优化处理结果

注:试样编号中18、27代表筋材肋间距18mm、27mm;-1、-2代表筋材为深肋、浅肋。
表3-13 方差和标准差

注:试样编号中18、27代表筋材肋间距18mm、27mm;-1、-2代表筋材为深肋、浅肋。
3.3.4.3 试验数据及结果分析
通过表3-12中数据分析得图3-26。根据试验数据和对比图可知,在肋间距相同时肋深对抗弯性能产生很大的影响。对于肋间距为18mm的筋材,由深肋GFRP筋到浅肋GFRP筋,极限抗拉强度增加74.9%;对于肋间距为27mm的筋材,由深肋GFRP筋到浅肋GFRP筋,极限抗弯强度增加48.2%,因此,肋间距相同时浅肋的GFRP筋比深肋的GFRP筋抗弯强度有较大幅度增加。

图3-26 缠绕方式对平均抗弯强度的影响
1~4对应应表3-12中的试件号
通过表3-13中数据分析得图3-27。根据试验数据和对比图可知,S18型号的GFRP筋抗弯强度的方差是最大的,这说明此种筋材抗弯性能比较离散,其他几种筋材抗弯性能的离散程度都可以接受,造成这种结果的原因可能有:①GFRP筋材本身的离散性;②由于肋间距比较小,相同长度内肋比较多,生产时容易出现差异;③试件个数较少出现偶然现象。

图3-27 缠绕方式对抗弯强度方差的影响
1~4对应应表3-13中的试件号
如图3-28和图3-31所示为肋间距为18mm和27mm、肋深不同的GFRP筋材的荷载-位移曲线。

图3-28 S18荷载位移曲线

图3-29 S27荷载位移曲线

图3-30 D18荷载位移曲线

图3-31 D27荷载-位移关系曲线
应力与荷载的关系为
(3-7)
应变与位移的关系为
(3-8)
式中 σ——应力;
ε——应变;
N——荷载;
ω——位移;
S——筋材的截面积;
l——试件的长度;
l1——计算应变时标距的长度;
n——试件长度相对于标距的倍数;
由式(3-7)和式(3-8)可以看出,应力与荷载、应变与位移都是线性关系,因此荷载-位移曲线可以代表应力-应变曲线的趋势,荷载位移曲线的斜率与应力-应变曲线的斜率也是线性相关的,而荷载位移曲线斜率可以代替弯曲弹性模量进行比较。
从图3-28~图3-31荷载位移曲线可知,浅肋GFRP筋的弹性模量稍小于深肋GFRP筋的弹性模量,但差别不大;浅肋GFRP筋材的抗弯强度基本上就是在加载前期,强度逐渐增大,当达到极限荷载时突然发生劈裂,如图3-32所示。在此过程中一直伴随有细微的断裂声,随后随着应变的增加,强度逐渐将小,直至破坏,深肋GFRP筋加载前期与浅肋GFRP筋基本一样,但在加载到强度出现第一次峰值后开始下降,但随后还会有一个强度随应变增强的过程。对于肋间距为18mm的GFRP筋材,强度增长不会超过第一次荷载的最大值,而对于肋间距为27mm的GFRP筋材,第二次强度极限值会大于第一次强度极限值,然后随应变的增加强度开始下降,造成这种现象的原因是浅肋的GFRP筋在受弯时,底部纤维同时受力并随荷载的增加由表面向中心逐渐破坏,而深肋的GFRP筋材,在受力时中心平直纤维先受力,表面纤维逐渐由弯曲变平直再受力,此时中心部分纤维可能已经破坏,所以出现强度随应变有两次增加的过程,并且筋材一般出现上部被挤压破坏,整体更加容易弯曲,如图3-33所示。

图3-32 浅肋筋劈裂破坏

图3-33 深肋筋弯曲破坏
另外,肋间距为27mm深肋的GFRP筋出现抗弯荷载第二次增大时,基本上其荷载值都要大于第一次的最大荷载值,而肋间距为18mm深肋的GFRP筋第二次荷载最大值一般不大于第一次的最大荷载值。主要是因为肋间距为27mm与肋间距为18mm的GFRP筋相比单位长度的纤维弯曲率要小很多,且表面弯曲纤维厚度也稍小一些,因此要使肋间距为18mm的GFRP筋表面纤维由于弯曲而拉直所需要的挠度变形稍大一些,在加载速率相同的条件下,需要的加载时间也相对长一些,荷载值也相对大一些,这就表现在图3-33中肋间距为18mm的GFRP筋第一次荷载最大值较大,大于第二次荷载最大值的现象。
通过上述试验研究,可以得到如下结论。
①对于肋间距为18mm的筋材,由深肋GFRP筋到浅肋GFRP筋,极限抗拉强度增加74.9%;对于肋间距为27mm的筋材,由深肋GFRP筋到浅肋GFRP筋,极限抗弯强度增加48.2%,因此,肋间距相同时浅肋的GFRP筋比深肋的GFRP筋抗弯强度有较大幅度增加。
②浅肋GFRP筋材的抗弯强度基本上就是在加载前期,强度逐渐增大,当达到极限荷载时突然发生劈裂,深肋GFRP筋会出现二次抗弯强度增加的过程。
3.3.5 剪切强度
参考《纤维增强塑料冲压式剪切强度试验方法》(GB/T 1450.2—2005),采用CMT系列电伺服50kN万能试验机并配以压式剪切器(图3-34)进行剪切试验。

图3-34 剪切试样示意图
试验方案及参数如下。
采用GFRP筋材,直径为18mm,肋间距为18mm、27mm,肋深为浅肋,表面缠绕物为尼龙绳,试验试样尺寸与剪切模具相当,长度为140mm。
试验参数主要如下。
①试件尺寸及形状:如图3-34所示。
②试验环境:温度25℃±2℃。
③试件数量:每组试样不少于5个。
④测量试件直径和标距,测量精确到1mm。
⑤加载速度为0.1kN/s。
⑥将试样安放于剪切夹具的中部,使夹具完全插入底座中,以避免出现弯剪形式的破坏,设置预加载为300N,保证试样与夹具完全接触后再加载,测量剪切强度、剪切模量及应力-应变曲线等材料性能指标。
⑦设置合理的破坏准则,即瞬时荷载下降幅度超过20%时停机以保证试件的有效,有效试样不足5个时,应重做试验。
3.3.5.1 试验方案
采用不同表面缠绕方式的GFRP筋进行各项力学性能测试,试验方案如下。
参考《纤维增强塑料冲压式剪切强度试验方法》(GB/T 1450.2—2005),采用CMT系列电伺服50kN万能试验机并配以压式剪切器[图3-35(a)]进行剪切试验。采用GFRP筋材直径为6mm、8mm、10mm、12mm、14mm、16mm,表面缠绕物为尼龙绳、一层玻璃纤维束、两层玻璃纤维束,试验试样尺寸与剪切模具相当,长度为140mm,试样如图3-35(b)所示。

图3-35 剪切性能测试验仪器及测试试样
3.3.5.2 试验现象
试验加载初期,呈现较平滑的曲线,主要是由于GFRP筋材表面的树脂在力很小时就会发生断裂,随着荷载的增大而发出纤维断裂的“噼啪”声,声音逐渐增大且越加密集,当试件破坏时,伴随着很大的响声。GFRP筋试件的破坏均为整体缓慢切断,断口较整齐,且都有不同程度的挤压变形,没有发生脆性剪断,这说明GFRP筋中的树脂性能较好,纵向纤维对横向剪切有一定的作用。
3.3.5.3 结果分析
对不同缠绕方式的GFRP筋[图3-36(a)]进行剪切性能测试,试验数据见表3-14,通过理论分析得图3-36(b)。由图可知,表面缠绕玻璃纤维束对剪切强度有明显的提高,玻璃纤维束的缠绕使GFRP筋成型时纤维更加紧密,与树脂充分结合,两者的协同工作性更强,从而使GFRP筋的剪切强度得到提高,同时,玻璃纤维束本身对剪切强度也有所贡献。在GFRP筋直径较小时,缠绕两层纤维束的GFRP筋剪切强度明显高于缠绕一层的GFRP筋,但是当直径较大时,两者的差别则不是很明显。

图3-36 剪切性能破坏及分析图
表3-14 GFRP筋剪切试验结果单位:MPa

3.3.6 抗扭强度
玻璃纤维筋在一定工况下会涉及扭矩这个力学指标,这里简单介绍一下玻璃纤维筋进行扭转测试的方法。
本试验采用玻璃纤维带缠绕的GFRP筋和尼龙绳缠绕的GFRP筋进行抗扭性能测试,测试其扭矩是否符合规范规定的用于煤矿支护的GFRP锚杆的要求。
3.3.6.1 试验设备和试验试样
使用计算机控制扭转试验机,型号是NDW31000(图3-37)。计算机控制电子式扭转试验机主要用于非金属材料扭转性能试验,能够自动测量抗扭强度、屈服点,配备扭转计可测量切变模量、规定非比例扭转应力,而且能够自动记录扭矩与转角的曲线。试验机配有全数字测量控制系统,性能稳定,精度高。

图3-37 抗扭试验机
所用抗扭试件如图3-38所示,使用的是肋间距为27mm,缠绕物分别为尼龙绳和玻璃纤维带的两种GFRP筋。

图3-38 抗扭测试试件
3.3.6.2 试验现象
对于尼龙绳缠绕的GFRP筋进行测试时,当抗扭试验机逐步增加扭矩的过程中,筋材表面会逐渐出现一些细小的裂痕,当扭矩达到一定程度时,试件会突然破坏并出现严重的扭曲,甚至变成“麻花状”,如图3-39所示;对于玻璃纤维袋缠绕的GFRP筋,刚开始加载时与一般GFRP筋材相差无几,在达到规定的扭矩时玻璃纤维带缠绕的GFRP筋在破坏前会保持相当长的一段时间,即将破坏时,先发生缠绕带的断裂剥落,紧接着整个筋材发生破坏,形成以近似的“屈服平台”,这将有利于锚杆支护中锚杆的嵌入与防损坏,破坏形式如图3-40所示。

图3-39 尼龙绳缠绕GFRP筋抗扭破坏

图3-40 玻璃纤维带缠绕GFRP筋抗扭破坏
3.3.6.3 数据处理与分析
根据试验数据得出时间-扭矩图3-41和图3-42所示。

图3-41 缠绕尼龙绳的GFRP筋扭矩-时间曲线

图3-42 缠绕玻璃纤维带的GFRP筋扭矩-时间曲线
从图3-41和图3-42可以看出,表面缠绕尼龙绳的GFRP筋不能达到行业标准规定的GFRP筋材的抗扭力矩应达到的40N·m,用玻璃纤维带缠绕的GFRP筋则都能达到40N·m;缠尼龙绳的GFRP筋几乎都是在达到最大扭矩时发生脆性破坏,没有一个近似“屈服平台”,这对于锚杆支护的应用不利。
从图3-43中可以看出,缠绕玻璃纤维束的GFRP筋能够在40N·m扭矩作用下坚持更长的时间而不发生破坏,这对于GFRP锚杆在边坡、煤矿支护过程中更加有利。但由于用玻璃纤维束作为缠绕物生产时,纤维束为松散状,容易搅在一起而影响生产的稳定性与连续性,用玻璃纤维带缠绕时不会出现此问题,并且抗扭性能与用玻璃纤维束差不多,均比尼龙绳缠绕的强,综合考虑用玻璃纤维带缠绕的GFRP筋材更适合作为锚杆。

图3-43 缠绕玻璃纤维束的GFRP筋扭矩-时间曲线