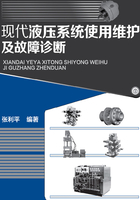
2.7 液压油液的污染及其控制
2.7.1 油液污染及其危害
(1)污染物种类、来源
在液压工作介质中,凡是油液成分以外的任何物质都认为是污染物。主要有固体颗粒物、水和空气等,微生物、各种化学物质;系统中以能量形式存在的静电、热能、放射能及磁场等。
污染物来源有三个途径:系统内部残留(如液压元件、油路块、管道加工和液压系统组装过程中未清除干净而残留的型砂、金属切屑、焊渣、尘埃、锈蚀物和清洗溶剂等);系统外界侵入(如通过液压缸活塞杆侵入的固体颗粒物和水分,以及注油和维修过程中带入的污染物等);系统内部生成(如各类元件磨损产生的磨粒和油液氧化及分解产生的有害化学物质等)。
(2)油液污染对液压系统的危害
颗粒污物会堵塞和淤积引起元件故障;加剧磨损,导致元件泄漏、性能衰退;加速油液性能劣化变质等。空气侵入会降低油液体积弹性模量,使系统刚性和响应特性变差,压缩过程消耗能量而使油温升高;导致气蚀,加剧元件损坏,引起振动噪声;加速油液氧化变质,降低油液的润滑性;气穴破坏摩擦副耦合件之间的油膜,加剧磨损。油液中侵入的水与油液中某些添加剂的金属硫化物(或氯化物)作用产生酸性物质而腐蚀元件;水与油液中某些添加剂作用产生沉淀物和胶质等有害污染物,加速油液劣化变质;水会使油液乳化而降低油液的润滑性;低温下油液中的微小水珠可能结成冰粒,堵塞元件间隙或小孔,导致元件或系统故障。
2.7.2 污染度及其测量
污染度是评定介质污染程度的一项重要指标,它是指在单位容积油液中固体颗粒物的含量,即油液中固体颗粒污染物的浓度;对于其他污染物(如水和空气),则用水含量和空气含量表述。固体颗粒污染物的浓度主要采用两种表示方法:一是质量污染度(mg/L);二是颗粒污染度,即单位体积油液中所含各种尺寸范围的固体颗粒污染物数量,颗粒尺寸范围可用区间(如5~15μm,15~25μm)表示,或用大于某一尺寸(如>5μm,>15μm等)表示,由于颗粒污染物对元件和系统的危害作用与其颗粒尺寸分布及数量密切相关,因而目前被普遍采用。
污染度测定有多种方法,应用较多的是显微镜计数法和自动颗粒计数器法。
(1)显微镜计数法
使用微孔滤膜(滤膜直径为47mm,孔径为0.8μm或1.2μm)过滤一定体积的样液,将样液中的颗粒污染物全部收集在滤膜表面,然后在显微镜下利用其测微尺测定颗粒大小,并按要求的尺寸范围计数。此法采用普通光学显微镜,设备简单,容易操作,能直接观察到污染物的形貌和大小并能大致判断污染颗粒的种类,但计数准确性受到操作者经验和主观性的影响,精度较差。
(2)自动颗粒计数器法
采用的自动颗粒计数器有遮光型、光散射型和电阻型等,遮光型应用较多,其工作原理如图2-1(a)所示,主要特点是采用遮光型传感器[图2-1(b)]。从光源发出的平行光束通过传感区的窗口射向一光电二极管。传感区部分由透明的光学材料制成,被测样液沿垂直方向从中通过,在流经窗口时被来自光源的平行光束照射。光电二极管将接收的光转换为电压信号,经前置放大器放大后传输到计数器。当流经传感区的油液中没有任何颗粒时,前置放大器的输出电压为一定值。当油液中有一个颗粒进入传感区时,一部分光被颗粒遮挡,光电二极管接收的光量减弱,于是输出电压产生一个脉冲[图2-1(c)],其幅值与颗粒的投影面积成正比,由此可确定颗粒的尺寸。传感器的输出电压信号传输到计数器的模拟比较器后,与预先设置的阈值电压相比较。当电压脉冲幅值大于阈值电压时,计数器即计数。通过累计脉冲的次数,即可得出颗粒的数目。计数器设有若干个比较电路(或通道),如6个或8个。预先将各个通道的阈值电压设置在与要测定的颗粒尺寸相对应的值上。这样,每一个通道对大于该通道阈值电压的脉冲进行计数,因而计数器就可以同时测定各种尺寸范围的颗粒数。此法测量速度快,精确度高,操作简便,但设备投资较大。目前已广泛应用于各工业部门,作为油液污染分析的主要方法。

图2-1 遮光型颗粒计数器
1—光源;2—平行光管;3—平行光束;4—传感区;5—样液;6—透明窗口;7—光电二极管;8—前置放大器;9—计数器
现已有多种油液污染度检测仪器可供选用,如XP74LJ150型遮光式颗粒计数器(北京中西泰安技术服务有限公司产品)和KLD系列污染度检测仪(北京航峰科伟装备有限公司产品)等。
2.7.3 污染度等级标准
为了便于液压油液污染度描述、评定和控制,需对油液污染度等级进行规定。常用油液污染度等级标准如下。
(1)NAS1638污染度等级标准(表2-10)
表2-10 NAS1638污染度等级(100mL中的颗粒数)

这是美国宇航学会标准,它是按照5~10μm、10~25μm、25~50μm、50~100μm和大于100μm5个尺寸范围的颗粒浓度划分等级(14个等级),适应范围更广。可以看出,相邻两个等级颗粒浓度的比为2,因此当油液污染度超过表中11级,可用外推法确定其污染度等级。当采用此标准评定样液的污染度等级时,从测得的5个颗粒尺寸范围的污染度等级中取最高的一级定为样液的污染度等级。
(2)ISO4406:1999污染度等级标准(表2-11)
表2-11 ISO4406:1999污染度等级数码

注:1.ISO 4406:1987标准选择5μm和15μm这两个特征尺寸(两个等级数码)代表油液污染度等级,是因为5μm左右微小颗粒是引起淤积和堵塞故障的主要因素,而大于15μm的颗粒对元件的污染磨损起着主导作用。因此,选择这两个尺寸的颗粒浓度作为划分等级的依据,能比较全面地反映不同尺寸的颗粒对元件的影响。
2.由于现代液压和润滑元件精密程度的提高,摩擦副间隙变小,对微细颗粒更敏感,因而对油液清洁度的要求越来越高。绝对精度1~3μm的高精度过滤器早已应用于对油液清洁度要求高的液压系统。ISO4406:1987标准已不能满足对油液高清洁度的要求,因此,ISO4406:1999提出了修改意见,增加了一个反映大于2μm颗粒污染等级的数码(即将等级标准的最小计数颗粒尺寸均规定为2μm),采用三个数码表示油液的污染度。
3.目前ISO4406标准已被世界各国普遍采用,我国制定的GB/T 14039—2002也采用这一国际标准。
这是国际标准化组织(ISO)标准。该标准按每1mL油液中的颗粒数,将颗粒污染划分为30个等级,每个等级用一个数码表示,颗粒浓度越大,代表等级的数码越大。如果采用自动颗粒计数器测量油液污染颗粒时,采用三个数码表示油液的污染度,三个数码采用一斜线分割,其中第一个数码表示每毫升油液中尺寸大于2μm的颗粒数等级,第二个数码表示尺寸大于5μm的颗粒数等级,第三个数码表示尺寸大于15μm的颗粒数等级。例如,污染度等级18/16/13表示:油液中大于2μm的颗粒数等级数码为18,每1mL油液中的颗粒数在1300~2500之间;油液中大于5μm的颗粒数等级数码为16,每1mL油液中的颗粒数在320~640之间;油液中大于15μm的颗粒数等级数码为13,每1mL油液中的颗粒数在40~80之间。如果采用显微镜测量油液污染颗粒时,仍用两个数码表示油液污染等级,为了与前述表达方式保持形式上的一致,缺少的一个数码以“—”表示,例如-/16/13。
(3)GB/T 14039—2002污染物等级标准(参见表2-11)
这是我国《液压传动-油液-固体颗粒污染等级代号》国家标准,该标准采用ISO 4406:1999对GB/T 14039—1993修订而来。GB/T 14039—2002规定,当采用自动颗粒计数器测量油液污染颗粒时,采用≥4μm、≥6μm和≥14μm三个尺寸范围的颗粒浓度数码表示油液污染度等级,每个数码间用一条斜线分割,数码共30个。例如,污染度等级18/16/13:第一个数码18表示每毫升油液中尺寸≥4μm的颗粒数等级;第二个数码16表示每毫升油液中尺寸≥6μm的颗粒数等级;第三个数码13表示每毫升油液中尺寸≥14μm的颗粒数等级。当采用显微镜测量油液颗粒时,按照ISO4406:1999进行计数:第一部分用“—”表示,第一个数码用≥5μm的颗粒数确定,第二个数码用≥15μm的颗粒数确定,例如—/16/13。在采用该标准时,在试验报告、产品样本及销售文件中应使用如下标注说明:油液的固体颗粒污染等级代号符合GB/T 14039—2002《液压传动-油液-固体颗粒污染等级代号》(ISO4406:1999,MOD)。
2.7.4 液压系统与液压元件清洁度等级(指标)及液压系统(元件)清洁度试验
典型液压系统清洁度等级见表2-12,各液压元件清洁度指标可参见JB/T 7858—2006。一个新制造的液压系统(元件)在运行前和正在运转的旧系统都需要按有关规定进行清洁度试验,试验的目的是对液压系统中的油液取样,确定油液的清洁度等级是否合格。试验时,一般先测定污染度等级,然后与典型液压系统的清洁度等级或液压元件清洁度指标进行比对,如果污染度等级在典型液压系统的清洁度等级或液压元件清洁度指标范围内,即认为合格,否则即为不合格。
表2-12 典型液压系统清洁度等级

①指NAS1638。
②相当于ISO4406。
注:采用此表确定系统目标清洁度时,需根据系统中对污染最敏感的元件进行。
2.7.5 污染控制措施
污染控制措施见表2-13。
表2-13 污染控制措施


图2-2 自清洁锥底圆筒形油箱

图2-3 带自清洁油箱和离线过滤回路的液压系统