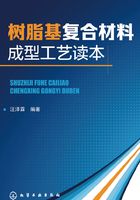
1.2 连续纤维预浸料(无纬布)制备
无纬布是纤维平行排列的浸胶片。由于其纤维单向排列,所以又称单向浸胶布。它用于压制层合板和对铺层设计有严格要求的承力结构,如飞机蒙皮和型材。
在制造预浸料之前,必须首先根据复合材料设计的要求,确定预浸料的单位面积的纤维质量和预浸料的树脂含量。对于单向纤维预浸料,其单位面积纤维质量可在一个较大的范围内设计,计算公式为:
Ws=t/d (1-2)
式中 Ws——预浸料单位面积纤维质量,g/m2;
t——丝束的纤度,tex,即g/km;
d——所制造的预浸料的纤维间距,10-3m。
纤维间距通过调节预浸料制造设备来确定。
在预浸料的单位面积纤维质量确定以后,其树脂的含量由其所制造的复合材料的纤维体积含量或复合材料单层厚度和固化树脂的密度所决定。
根据纤维类型、欲制预浸料单位面积纤维质量和宽度,按式(1-3)计算所需纱筒数。
(1-3)
式中 N——纱筒数,筒;
Gf——单位面积纤维质量,g/m2;
——单位长度纤维质量,g/m;
L——宽度,m。
1.2.1 滚筒缠绕法
首先在滚筒上平整地铺上一层脱模纸,然后将连续纤维通过基体树脂胶液的胶槽,经过几组导向辊,除去多余的树脂,平行地绕在圆柱形滚筒上,当滚筒不断转动时,浸胶之后的丝束就以固定的间距平行地缠绕在滚筒上,最后顺滚筒的一根母线切断展开,晾干后,用薄膜覆盖,便获得无纬布。布的大小由滚筒直径和长度决定。这种工艺效率低,适用于新产品研究和开发。
(1)胶液配方见表1-37和表1-38。
表1-37 胶液配方1

①胶液相对密度控制在1.0。
表1-38 胶液配方2

①胶液相对密度控制在1.0。
(2)主要设备——滚筒式排布机 滚筒式排布机主要组成部分为滚筒、机头和传动装置三大部分(如图1-23所示)。滚筒直接用来绕丝。机头上装有纱架、集束器、胶槽、导向辊和张紧辊。传动系统由电机、减速箱、传动链、调速器、丝杠、螺母、溜板等零件组成。其作用是分别带动滚筒旋转和机头平行于滚筒轴线作横向移动。电动机可实现无级变速,机头移动与滚筒转动之间的速比则采用调速装置实现。所以,可以任意选择排布速度并按纱片宽度调整机头移动的速度。

图1-23 滚筒式排布机示意图
1—纱架;2—集束器;3—导向辊;4—胶槽;5—张紧辊;6—滚筒;7—压辊;8—动力机构;9—床身;10—调速器;11—溜板(可前后移动);12—小车(可左右移动)
(3)制造方法 先在滚筒上铺满一张脱模纸,脱模纸的一面涂有隔离材料,它可以从无纬布上揭下而不至于粘连。丝束从纱架抽出,经集束器、导向辊进入胶槽浸胶,再经张紧辊由丝嘴绕到滚筒上,然后通过一系列齿轮机构来保证滚筒转动与丝嘴沿滚筒轴向移动的速比,使滚筒每转动一周,则丝嘴连续地移动一个纱片宽度。当滚筒不断转动时,纱片就一片紧接一片地按圆周方向平行地缠绕在滚筒上,直至达到要求的无纬布宽度为止。然后沿滚筒的一根母线切断纤维。
滚筒缠绕法生产无纬布应控制的工艺参数包括:纤维状态、胶液相对密度、浸胶速度、滚筒圆周线速度和纤维张力等。表1-39给出了环氧与酚醛(6∶4)胶液相对密度与无纬布含胶量的关系(试验值)。
表1-39 环氧与酚醛(6∶4)胶液相对密度与无纬布含胶量的关系(试验值)

1.2.2 溶液浸渍法
1.2.2.1 热固性树脂
(1)胶液配方及工艺参数
①环氧/酚醛胶液配方(见表1-40) 该配方制成的制品能够兼顾耐热性及机械强度,后续工艺的工艺性良好,有较长的储存和适用期。
表1-40 环氧/酚醛胶液配方

②环氧胶液配方(见表1-41) 该配方工艺性较好,制成的制品具有中等强度。
表1-41 环氧胶液配方

①MNA为甲基内亚甲基四氢化邻苯二甲酸酐。
②BDMA为苯基二甲胺。
③聚酯胶液配方(见表1-42) 配方中选用过氧化二异丙苯作引发剂,少量过氧化苯甲酰作助引发剂,以保证聚酯在较低温度下部分聚合。由于苯乙烯挥发性大,耐热性差,故此配方用DAP代替一般配方中的苯乙烯作为交联剂,从而改善了工艺性,提高了制品性能。
表1-42 聚酯胶液配方

(2)工艺过程 无纬布生产工艺过程见图1-24,纱团置于纱架上自由退解,经过梳形排纱装置集束成带状,浸胶,控制含胶量25%~30%,再进入烘炉,控制挥发物含量为(3±0.5)%,不溶性树脂含量不超过10%。

图1-24 无纬布生产工艺过程示意图
1—力矩电动机;2—卷盘;3—主动辊;4—变速箱;5—直流电动机;6—烘炉;7—电热器;8—胶槽;9—纱团
1.2.2.2 热塑性树脂
高性能热塑性树脂特别是PEEK、PPS一类结晶型高分子,没有合适的低沸点溶剂可溶,不便用溶液浸渍法制备预浸料。但也有一部分非结晶型树脂如PEI、PEK-C、PES等可溶解在部分溶剂中,不过常用的低沸点溶剂对其溶解度有限,用低浓度的溶液即便采取不同工艺措施也难以得到树脂含量在35%(质量分数)左右的预浸料,为此,常用混合溶剂增大树脂的溶解度,随之提高预浸料的树脂含量,满足对不同树脂含量预浸料的要求。
丝束从纱架上引出,经箅子分丝后,整齐地进入装有胶液的浸渍槽,经挤胶、烘干、垫铺离型纸和压实,最后收卷,即成为成卷的单向预浸料产品(如图1-25所示)。

图1-25 多用预浸机示意图
1—纤维架;2—箅子;3—浸胶槽;4,7,11—顶纸开卷;5,8,12—顶纸收卷;6,10—空气和溶剂的排出或回收;9—烘炉;13,20—压辊;14—牵引辊;15,16—切刀;17—反相涂覆辊;18—底纸开卷;19—涂覆的树脂膜;21,23—空气或惰性气体;22—压辊组;24—冷却器;25—产品
1.2.3 热熔浸渍法
1.2.3.1 熔体浸渍法(熔融直接浸渍法)
丝束从纱架上引出,经滚筒至喷气分离器,丝束舒展开来以便更多的纤维裸露出来,接着进入流出树脂熔体的挤出机头的机缝,上下层树脂熔体薄层受到压力作用浸渍纤维,浸渍后的预浸料经空气迅速冷却并收卷(如图1-26所示),单向预浸料的厚度为0.127~0.152mm,宽度为7.62~30.48cm,可供干法缠绕或层压,其流程如下:
直接纱→滚筒→喷气分离器→挤出机头→空气冷却→收卷

图1-26 熔融浸渍预浸料示意图
1—放卷装置;2—滚筒;3—喷气分离器;4—挤出机头;5—空气快冷;6—收卷辊
实用举例。环氧5228/T700和双马5428B/T700超薄预浸料制备,预浸料单位面积纤维质量为(85±5)g/m2、单层压厚为(0.085±0.01)mm。
采用美国生产的12in(1in=0.0254m)热熔预浸机。首先将纱筒固定在纱架上,引出纱束,经过箅子、展平辊、预热平台、冷却板到牵引装置。将所选用的脱模纸装于开卷机架上,将纸依次穿过各导向辊、加热平台、刮刀板、涂布头、牵引装置。参照表1-43设定工艺参数,制造预浸料。
表1-43 预浸料制备工艺参数

1.2.3.2 热熔胶膜法
热熔胶膜法制造预浸料工艺一般包括制膜和预浸两个步骤。
(1)树脂制膜工艺 用热熔法将基体树脂置于混合器中充分混合,用电动机驱动的计量泵或通过压力将基体树脂输送到涂胶辊,热态树脂按设计要求均匀地涂覆到离型纸上,冷却,使涂覆的树脂薄膜黏着在离型纸上。涂膜厚度(反应涂膜量)可通过调节涂胶辊温度或离型纸前进速度来控制,用β射线仪检测胶膜的厚度或胶膜的面密度。涂膜厚度可控制在30~70μm范围内,涂膜量约为35~80g/m2,涂胶辊的温度需根据树脂的热性能来确定(图1-27)。

图1-27 涂树脂膜工艺示意图
1—离型纸开卷;2—涂胶辊;3—β射线仪;4—冷却辊;5—聚乙烯薄膜开卷;6—收卷
(2)纤维预浸工艺 纤维筒排列在整经架上,单向排列,经过精梳机梳理,有序单向排列,彼此不交叉,彼此无空隙,排列成干态无纬布。如果是12K或24K碳纤维,还需开纤扩幅,使每根单丝都有相同概率渗浸热熔树脂。显然,有捻碳纤维不适宜制造无纬布。整经梳理好的纤维无纬布与涂有树脂膜的离型纸形成夹芯结构,依次通过几组热压辊,使基体树脂熔融,把离型纸上的树脂膜转移到无纬布上,制得单向纤维复合材料的无纬布,收卷(如图1-28所示),供使用。

图1-28 热熔胶膜法工艺示意图
1—纤维纱;2—下树脂膜;3—上树脂膜;4—收上离型纸;5—铺玻璃布或PE膜;6,7—换下离型纸;8—成品和收卷
1.2.4 粉末熔融浸渍法
1.2.4.1 静电流化床法
静电流化床法一般流程如下,其工艺示意图如图1-29所示。
纱架→张紧滚筒→空气梳状分束器→空气流化床→隧道炉→牵引辊→收卷辊

图1-29 静电流化床法工艺示意图
1—放卷辊;2—张紧控制;3—空气梳状分束器;4—稀相;5—稠相;6—空气流化床;7—电势;8—空气扩散板;9—炉子;10—牵伸辊;11—收卷辊
(1)高压静电流化床法(上海杰事杰新材料股份有限公司杨桂生专利资料) 丝束从纱架上引出,经高压静电流化床,流化床中放的是粒度为60~80目的树脂粉末,可能混合有其他组分或添加剂。玻璃纤维束在静电的作用下,玻璃纤维丝相互排斥而分散开来,粉末在气流和静电的共同作用下进入并吸附到纤维束和单丝中,从而将玻璃纤维浸渍。经过树脂粉末初步浸渍的玻璃纤维束进入多孔式预热烘箱中,在烘箱中树脂被加热到接近熔融的程度。经过预热的带有树脂的玻璃纤维进入哈夫模中,哈夫模主要是起到将树脂熔融、塑化,将纤维均匀分布的作用。带有塑化好的熔融树脂的玻璃纤维从哈夫模中出来,进入挤出机的上、下模中,在上、下两面涂覆上树脂,该挤出机主要起到对玻璃纤维进行再浸渍以及加强了对树脂含量的可调控性的作用。涂覆好的玻璃纤维进入到成型机组,经过成型机组对纤维和树脂的压迫及再分布,然后成型为片材。根据客户的要求可以将片材收成卷,也可以裁剪成需要的尺寸。
(2)玻璃纤维增强PP预浸料 将质量分数为30%的树脂粉末(组成为PP∶PP-g∶PA=60∶30∶10)、质量分数为10%的空心玻璃微珠以及质量分数为0.5%的成核剂NA-45、质量分数为0.5%的抗氧剂1010、质量分数为0.5%的抗氧剂DSTP混合均匀,并置于高压静电流化床中,将玻璃纤维连续地从流化床中通过,调节流化床的静电电压以调节玻璃纤维吸附树脂的量,使聚合物粉末的质量分数保持在40%左右。吸附有树脂的玻璃纤维连续地从烘箱和高温模头通过,再经过多辊压延机,压制成约1mm厚度的片材。
(3)碳纤维增强PEEK预浸料
①原材料 碳纤维(Hercules AS4,未上浆料,平均6000根/束)体积含量60%,PEEK体积含量为40%(ICI生产的150PF,平均粒径90μm)。
②制造工艺 静电粉末法预浸机的工作原理及其实验生产设备见图1-30。

图1-30 静电粉末法制备热塑性预浸料工艺示意(a)及实际的实验生产设备照片(b)
由图1-30可知,碳纤维首先开卷,并通过一个轮系展宽预分散。粉末预浸的关键环节是涂覆室,这里利用静电流化态床技术使碳纤维束强烈分散,吸附大量的热塑性树脂粉末,然后进入熔融炉预热固结,固定住吸附的粉末。粉末预固结的碳纤维束继续前行,并被后续的轮系微热压碾平,最后收卷,得到热塑性的“预浸带”。一个安置在轮系中的β射线控制系统负责测量预浸带的厚度,间接换算得到树脂的预浸量,即树脂的体积分数。其工艺参数见表1-44。
表1-44 碳纤维增强PEEK预浸料工艺参数

1.2.4.2 树脂槽粉末法
纤维通过导向辊进入树脂槽,在一组浸渍辊的作用下分散,吸附树脂粉末,然后通过加热装置使树脂熔融,经辅助浸渍辊及加压辊使树脂充分浸渍纤维,冷却后得到预浸纤维。该工艺设备比空气流化床法简单,具体过程如图1-31所示。

图1-31 树脂槽粉末浸渍流程
1—纱卷;2—纤维;3—导向辊;4—粉末槽;5—浸渍辊;6—加热通道;7—冷却辊;8—收卷
预浸纤维的树脂含量与树脂粉末的颗粒大小、分散辊的数量和排布方式有关。树脂粉末的颗粒越小,玻璃纤维吸附的树脂粉末越多,树脂含胶量就越高。在其他条件相同的情况下,当用粒径为40目的聚丙烯粉末浸渍玻璃纤维时,含胶量为39%;而用80目的聚丙烯粉末时,含胶量为85.7%。当分散辊数目较少时,由于纤维束未能完全分散开,纤维束中的很多纤维未能吸附到树脂粉末,而且,已分散开的纤维也有重新收紧集束的趋向,使得原已分散的纤维来不及充分吸附粉末,因此预浸带的树脂含量很低。当分散辊数目增加时,由于纤维分散程度的增加,吸附于纤维束上的树脂含量增加,所以预浸带中的树脂含量增加。分散辊数目对预浸带树脂含量的影响见表1-45。
表1-45 分散辊数目对预浸带树脂含量的影响

加热段应使吸附在纤维表面的树脂粉末充分熔融,以保证树脂能充分浸渍纤维。但是加热段的温度也不能控制过高,温度过高易引起聚合物的氧化降解。聚丙烯熔体的温度控制在210~220℃范围内较为合适。烘道内的加热气氛温度不宜超过230℃。
1.2.5 粉末悬浮浸渍法
粉末悬浮浸渍法是近几年研究得较多的一种工艺。这种工艺中,热塑性树脂粉末(直径在10μm以下并小于纤维直径)和表面活性剂(如聚环氧乙烷、甲基乙基纤维素等)在浸渍室中形成水悬浮液,导辊将连续纤维牵拉入悬浮液槽中浸渍,使粉末均匀地渗入纤维之间,然后经干燥、加热压实成型,经牵引收卷(见图1-32)。这种工艺技术新,成本低,工艺简单,设备投资少,制备周期短,可用于连续纤维增强热塑性树脂基复合材料的生产。

图1-32 粉末悬浮浸渍法制备预浸料示意图
1—纱架;2—箅子;3~6—导向辊;7—悬浮液槽;8—导向机构;9—干燥室;10—加热模;11—牵引;12—收卷
1.2.6 混纤纱浸渍法
混纤纱是将树脂纤维和增强纤维在拉丝后合股,使得树脂纤维和增强纤维达到理论上的单丝分散水平。
熔融浸渍和粉末浸渍工艺生产的预浸带在使用时都存在一个共同缺点,即带子刚硬,柔性差,而混纤纱则克服了该缺点。同时,混纤纱中树脂纤维和增强纤维达到理论上的单丝分散程度,浸渍效果更胜一筹。法国圣戈班的Vetrotex公司生产的Twintex混合纤维就是在玻璃纤维拉丝过程中与树脂纤维进行合股,浸渍效果非常好,玻璃纤维含量最高可达75%。日本东邦人造丝公司和德国BASF公司合作开发碳纤维同热塑性树脂纤维PEEK和PPS的混纤纱,成功地将直径7μm的3K碳纤维和直径20μm、0.5K的PEEK纤维均匀地混合成一组纱,将其加热熔融、碾压,使碳纤维嵌入熔融的PEEK基体中,冷却后成为预浸料。其情况如图1-33所示。

图1-33 增强纤维和热塑性树脂纤维浸渍示意图
1.2.7 XMC(连续纤维SMC)
超高强度片状模压料XMC是1976年由美国PPG公司最先开发出来的,主要用于制造汽车部件。
XMC用定向连续纤维,纤维含量达70%~80%,不含填料(XMC的典型配方见表1-46)。XMC按所用增强材料的品种可分为三类:XMC-1型使用连续无捻粗纱,XMC-2型使用连续原丝,XMC-3型使用连续原丝和短切原丝。所有纤维呈X状交叉排列,角度为82.5°。其制法为:用一般的标准缠绕设备,纤维经过浸胶槽后缠绕在芯模上,缠绕完成后,从芯模上将材料切下,用聚乙烯薄膜包裹。然后,按照SMC生产的工艺方法进行增稠、压制。其模压制品在纤维方向上的强度是普通SMC模压制品强度的5~8倍,是钢材的4倍。因此,XMC又称为超高强SMC。
表1-46 XMC的典型配方
