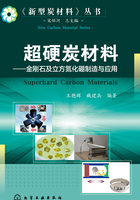
4.3 爆炸法合成金刚石
4.3.1 爆炸法合成的主要装置
用冲击波合成超硬材料的重要问题之一是如何保存爆炸后的产物,为此研究了不同的方法和不同结构的装置。大体可分为三种类型:平面型(飞片冲击反应材料)、圆筒型(聚合圆筒波冲击反应材料)和聚能流能量冲击型。
①平面型 这是很多研究者都采用的一种产生高压的方法,也用于合成金刚石。产生高压的方法是爆炸物使飞片产生冲击波,冲击反应材料(如图4-7所示)。
②圆筒型 为了用这种方法制造超硬材料,设计了不同结构的圆筒,借助于它们可以保存爆炸后的物质。目前用得最广的是管状和共轴状的圆筒,被研究材料或直接受爆炸圆筒波的压力或受爆炸物质外面金属筒的冲击。
③聚能流能量冲击型 利用带有锥形凹槽的装药引爆后的聚能效应,在凹槽附近的爆轰产物将形成一股高速、高温、高密度的射流,冲击反应材料。这种方式仅在聚能流作用的区域发现了金刚石,而且主要是围绕在凹坑周围。因为在聚能流的高速和高温下,反应材料在经受撞击时,大部分材料是不能保存下来的,其金刚石的产量大大低于平面法和圆筒法。
平面型冲击波合成金刚石的原理是利用烈性炸药爆炸时所产生的冲击波驱动一块金属板,以高速撞击产生高压高温,如图4-7(a)所示[51]。当起焊电雷管1起爆传药条2爆炸,作用于药板3,药板3爆炸,产生平面波作用于主爆药柱4,主爆药柱4爆炸,以极高的速度驱动飞片5,以极高的速度撞击石墨板7,产生高温高压,使部分石墨转变为金刚石。爆炸后收集含金刚石的石墨合成块。经过化学提纯处理,即可得到金刚石微粉。张路青等人设计了可提高飞片速度的平板爆炸装置[52]。
金刚石微粉再经爆炸冲击波的高温高压处理,可以得到不同粒度的大颗粒金刚石聚晶[51],如图4-7(b)所示。经过整形处理的金刚石可用来做石油钻头、地质岩心钻头、砂轮和修正笔等。

图4-7 平面型爆炸装置示意图
图4-8是一种改进型爆炸合成金刚石装置示意图[53]。这个装置的基本工艺过程如下。当起爆雷管1爆发后,隔爆板上的传爆炸药层2被引爆,其爆轰波向四周传播。爆轰波到达隔爆板边缘,由于隔爆板的作用,引爆传爆炸药层2的爆轰波击发主药包外层传爆药15,然后击发主药包外缘同时起爆。这样,在药柱上的爆轰波,一方面向下传播,一方面向中心传播,形成一个向中心收缩的斜击波——“准柱面收缩爆炸”。在钢管5内的石墨试样获得了比爆轰压力更高的高压,从而使石墨试样产生高温高压转变成金刚石。主药包斗在爆轰收缩的同时,由于爆轰波还向下传播,最后驱动飞片10,使之获得3~4km/s的飞行速度,飞片打击石墨板11,使石墨板内产生高温高压,使石墨转化成金刚石。这样的装置同时包含了两种产生高温高压的方式,一种是通过“准柱面收缩爆炸”产生高温高压;另一种是利用“飞片”打击石墨,形成高温高压。这种综合装置显然提高了炸药的利用率。
为了使普通低碳钢管在爆炸时不断裂,在试样中心加一个铁芯并和堵头焊成一体;在管外加四根加强筋16,如图4-8(b)所示。

图4-8 一种爆炸合成金刚石装置
1—起爆雷管;2—传爆炸药层(TNT∶黑索金=1∶1浇注在隔爆板上,厚15mm);3—隔爆板(混凝土制,厚50~60mm);4—主药柱(注装TNT,Φ280mm );5—钢管(低碳无缝钢管Φ57mm×7mm×195mm);6—铁芯(低碳钢棒,Φ12mm);7—石墨试样(由50%石墨+50%铜粉混合压装,装量500~600g);8—堵头(由低碳钢车制);9—卸载块(低碳钢柱,Φ57mm×25mm);10—飞片(薄钢板,厚22mm);11—石墨板(SD-1石墨,Φ250mm×15mm);12—垫板(薄钢板,厚2~3mm);13—支柱(高50mm);14—沙坑;15—主药包外层传爆药(由TNT∶黑索金=1∶1浇注在主药包外,厚10mm,能提高柱面收缩效应);16—加强筋(普通钢筋,Φ12mm)
提高单次冲击的作用时间很有限,多次冲击可以收到间接增加作用时间的效果。陈德元等人曾做过金属-石墨成形体的三次冲击压缩实验,得到金刚石的生成率和粒度随冲击次数的增加而提高的定性规律[54]。
图4-9是李世英等研发的爆炸铸铁合成金刚石装置[55],用它可制造优质微米级金刚石单晶。

图4-9 爆炸铸铁合成金刚石装置
1—井体护圈;2—井体防护网;3—导线;4—井体[Φ(1~4m)×(1~5m)深];5—框体(金属板、石板或砼板制成);6—侧铸铁板(5~16mm厚);7—飞片模(1~6mm有底无盖金属圆筒或多棱柱桶);8—河沙;9—防护板(有利于回收爆炸物);10—回收板;11—底铸铁板(10~40mm厚);12—主药柱(形状同飞片模);13—起爆柱;14—雷管
4.3.2 爆炸法合成的工艺
以图4-8的装置为例。试验结果表明[53],当主药柱4的直径为装试样钢管5的直径的5倍,钢管材料是含镍不锈钢时,金刚石的转化率达到10%~15%。若用普通钢管,则转化率为6%~8%。当药柱直径减小时,转化率显著下降。爆炸后试样回收率可达到90%以上。向下传播的爆轰波驱动飞片10,使之获得3~4km/s的飞行速度,飞片打击石墨板11,使石墨板内产生高温高压,使石墨转化成金刚石,转化率为3%~4.5%。爆炸时如果试样放在沙土地上,爆炸后回收的石墨板约为35%~45%(即飞片拍打部分的回收率);若在沙坑中则回收率会较高。
勘探技术研究所[56]曾借鉴粉末冶金的办法,用铁粉加石墨粉事先制成碳源块以提高转化率。据了解日本以含碳量为5%、含铁量为95%的粉末冶金块作合成原料,炸药质量用5kg,样品外形直径100mm,厚40mm。采用这一方案所得到的回收率达87.3%,单产量达115克拉/炮,转化率达35%。这就初步证实了这一方案具有回收率高、转化率高等优点。有人使用铜粉-石墨粉混合(92%铜,8%石墨),1kg炸药金刚石产出可达石墨质量的80%,金刚石尺寸为1~100μm。类似方法可合成CBN,但金刚石中有残留铜(纯化处理后)。
王保国等[57]通过控制装药结构、起爆方式来控制压力场以及温度场,进而提高爆轰和爆炸冲击复合合成金刚石微粉的得率,比用单一的爆轰法和冲击法的金刚石得率高。所使用的爆轰和爆炸冲击复合合成金刚石微粉是在体积为0.11m3的球形密闭容器中,用TNT/RDX混合装药(100g)在水套中爆炸来完成。根据理论计算,混合炸药中两种炸药的质量比为TNT∶RDX=60∶40时适合爆炸冲击合成金刚石,此时爆轰法合成的金刚石微粉的得率比较高。石墨采用压装方式,然后加工成所需的形状、大小和质量,在浇注前放置于炸药混合装药的中心。装药方式采用注装,装药结构采用柱状结构和球形结构两种方式。起爆方式对质量相同的球形结构,分别采用两点和四点起爆来进行起爆方式的比较。水介质体积均为8.8L。
4.3.3 金刚石的提纯
收集的爆炸产物中有未转化的石墨、金刚石、塑料碎末、大的铁屑、水等。所以,首先用60目标准检验筛除去塑料碎末和大的铁屑,然后静置4h以上,完全沉淀,除去多余的水,在烘箱中烘干。接着,将烘干物研磨破碎并用磁铁进行磁选,磁选的目的是清除爆炸产物中的细小铁杂质。磁选除铁是提纯过程中一个质的飞跃,它不但避免了盐酸加热除铁对环境的污染,而且大大缩短了提纯周期,节约了成本。然后,采用硝酸硫酸法除去石墨。为了防止此过程中反应产物以及酸蒸气对环境的污染,采用回流装置,且在通风橱中操作。反应完毕后,将反应后的产物中和至中性,然后洗涤干燥,即可得到金刚石微粉。
4.3.4 爆炸法合成的金刚石晶体结构及性能
(1)爆炸纳米多晶金刚石
纳米材料是指物质结构在三维空间中至少有一维处于纳米尺度,或由纳米结构单元构成的且具有特殊性质的材料(GB/T 19619—2004)。而爆炸法合成的多晶金刚石晶体是符合这一定义的,它是由纳米金刚石单晶颗粒聚集而成的,故应称之为多(聚)晶纳米金刚石或纳米多晶金刚石,外商常称之为PCD。
多(聚)晶纳米金刚石是碳素体在爆炸强冲击波的作用下合成的。Carbonado型聚晶金刚石微粉是由直径为3~10nm的纳米晶粒,通过不饱和键结合而成的微米和亚微米聚晶微粉,因而各向同性无解理面,具有很高的韧性。它的结构特点是晶体各向同性,无解理面。它不仅具有金刚石的无与伦比的硬度,还具有很高的韧性和强度。它不会产生整体断裂的现象。在磨削和抛光过程中会适时自动剥落而显现出新的微观切削刃口。这种“自锐性”保证了加工的高精度、高效率,把对加工面的损伤降至最低。它的应用前景广阔[58]。
(2)爆炸合成大颗粒金刚石聚晶
以爆炸金刚石微粉作原料,再利用第2次爆炸形成的高温高压制造大颗粒金刚石聚晶。
勘探技术研究所[49]曾对爆炸多晶金刚石的某些特性进行测试:抗压强度为(Φ0.4mm)15000~18000kgf/cm2;磨耗比为39400。用这样的聚晶制成钻头的钻进时效:6级灰岩,6.0m/h,最高12m/h(电镀表镶钻头)。6~7级灰岩,时效为钢粒钻进的6倍,为单晶孕镶钻头的3倍(1.21~1.5mm表镶钻头)。
爆炸法制造的聚晶金刚石与静压法制造的聚晶金刚石比较,有两个显著的优点:①聚晶大颗粒呈不规则形状,有许多锋利的刃角,做成钻头后,时效较高;②由于爆炸法的合成压力和温度都远远超过静压法,所以其耐热性能高于静压法合成聚晶,这对钻头加工和钻进情况都极为有利。
爆炸法聚晶的缺点:性脆,韧性不及静压法合成的好。
李世英等人[59]以爆炸金刚石微粉为原料,装填在特殊模具中,内部不添加任何粘接剂,经二次爆炸合成大颗粒金刚石聚晶,粒度约为1.7mm。对于0.4mm×0.3mm×0.2mm(长×宽×高)的聚晶,抗压强度可达18.8kN,硬度(HV)为1260。
陈德元等人[54]利用高能炸药爆轰产物驱动金属飞片,碰撞“硬”回收包套以输入平面冲击波,在24~37GPa的压力范围内,对纯石墨进行1~4次的冲击压缩实验,合成出了纯度很高、形貌良好的立方形聚晶金刚石。随着冲击次数的增加,金刚石的转化率和粒度有增大的趋势。但是,当金刚石粒度较大时(约100μm以上),如果冲击温度较低(约1000K 以下),同时冲击压力又较高(约20GPa以上),金刚石颗粒就容易被冲击波破碎。多次冲击石墨合成聚晶金刚石的粒度为8~145μm。由于合成中石墨不与金属直接接触,因而制造的金刚石纯度远高于静压法所制造的金刚石。
(3)爆炸合成单晶金刚石
利用炸药的冲击波作用于铸铁也可以制造出微米级的单晶爆炸金刚石。
李世英等人[55]以高能炸药为能源,以铸铁内的石墨为碳源,使爆炸瞬间产生的超高压高温作用在铸铁载体上,其中的部分碳转变成金刚石。这种金刚石属面心立方单晶,(111)的面间距增大到0.2069nm,有时含有少量六方金刚石。经岩矿鉴定,金刚石全部为单晶,未见到集合体。晶体形态为八面体歪晶(板状-多面体、沿三次对称轴压扁、沿二次对称轴拉长),淡黄色约占20%,黑色约占80%。它的单颗粒粒度可达到36μm,经粒度分级后可制成高研磨效率的金刚石微粉。