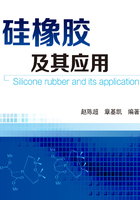
1.4 硅橡胶技术发展趋势
当前,世界有机硅材料技术发展的方向是高性能、多功能和复合化。通过配合技术的进步和添加新的添加剂,以及改变交联方式、共聚、共混等改性技术实现有机聚合物与有机硅材料复合,是当前有机硅技术发展的重要方向。科技工作者们根据需要通过下列几种途径设计出各种不同分子结构的有机硅产品,满足不同场合特别是高科技发展的需要。
近几年来,尽管有机硅产品越来越多,然而归结起来,新型有机硅材料应用开发所采用的新技术主要有3个方面。
1.4.1 交联方式
室温硫化硅橡胶其传统方式是利用硅醇基和烷氧基的缩合反应,而利用乙烯基和氢的加成反应的开发带来了很大的技术进步。加成反应可控制固化速率且无副产物生成,所以提高了制品的电性能和耐热性等物性。如日本东丽有机硅公司由含Si—H键的有机硅氧烷与乙烯基有机硅氧烷制得聚硅氧烷;美国GE公司采用新型零价镍配合物催化剂研制的加成型硅橡胶;美国3M公司研制的Si—H键化合物与烯键化合物的加成制品。这些新产品的某些物理性能得到了明显提高。在缩合反应方面,也开发出用于单组分室温硫化硅橡胶的各种交联剂。在原有醋酸型、酮肟型和醇型交联剂的基础上,开发了能使硅橡胶模量低、伸长率大的氨氧型和酰胺型交联剂;进而又开发了毒性小、固化快、在高温下不分解的丙酮型交联剂。例如日本公布的TSE39X系列产品就是改进后得到的一种无腐蚀快干密封剂。近年来,以硅氢加成交联发展起来的液体硅橡胶特别引起人们重视。它是由分子量大小不等,从数千至一二十万的乙烯基生胶和含Si—H键百分之十几摩尔的硅氢油以及催化剂及填料所组成。这种混料的黏度较小,生胶有一部分为乙烯基封端,硅氢油也有Si—H键封头。在末端的SiVi和SiH活性比较大,反应快,因此在交联时还有链增长反应,使分子量又有提高,强度加大,所要填料须反复处理,充分除去表面羟基。根据成品要求,黏度可控制在100~300Pa·s,送入泵式螺杆机,注射压力在10~200kgf/cm2,胶料通过螺杆混合加热硫化成型挤出,螺杆受热反应很快,有单组分和双组分,目前用得最多的是双组分。液体硅橡胶拉伸强度可达8~9MPa,伸长率500%~600%,撕裂强度30~40kgf/cm,它生产效率高,每台机器一年可生产106个部件,对小零件的制作可降低1/4成本,所以液体硅橡胶近几年发展很快。
以快述固化、节约能源为目的,国外正在加速研究通过电子束(EB)和紫外线(UV)固化的交联方式。电子束交联不会带来任何杂质,并可在室温下进行深层次的反应。国外用电子束交联方式已制备性能较佳的高强度硅橡胶,其拉伸强度为10MPa,伸长率500%,撕裂强度25kN/m,最高选43kN/m。但电子束需要电子加速器等大型设备,非一般单位有能力购置。近年来活跃起来的是光交联,光交联以紫外线为能源,设备简单,操作费用低,每摩尔光子(365nm)只需10多美分,就可以获得面积0.5m2、厚100μm的高分子交联。更有意义的是光交联速度快,在室温下可以让带状、线状样品迅速固化,如光缆和胶带纸等,它还可以定域反应,使在掩膜下1μm宽的线带固化。可用于复印和半导体电路的光刻,是非常有前景的交联方法。聚硅氧烷的光交联,一种是在它的分子中引入光敏基团,借这些光敏基团的互助结合而形成交联;另一种是本身没有光敏基团,只有乙烯基之类的官能团,借光敏引发剂(如Benzoin之类),它见光分解生成自由基,引起交联。
1.4.2 聚合物的化学改性
在硅氧烷的主链上引入长链烷基以及氨基、羟基、巯基、氰基、环氧基、聚醚基等有机官能团,形成的改性硅油被赋予特殊的界面活性。例如引入氨基的硅氧烷用作发型定型,引入聚酰亚胺的有机涂料可用作大规模集成电路结点涂料和纯化膜。近年来,硅烷化技术在有机合成中极为活跃。它使原来难以实现的有机合成得以进行,因而引起了人们合成含有不同键的有机硅化合物的兴趣。最近又出现了称为共混聚合物的制品,有机硅和乙丙橡胶的改性橡胶就是一例,它作为弥补两者不足的材料引起人们的重视。特别值得指出的是,把聚硅氧烷和有机高分子以化学键或其他稳定的方式结合起来。可把聚二甲基硅氧烷(PDMS)的某些特征引入有机高分子得到新的聚合物,用于高分子的改性,同时也可以促进有机硅工业的发展。由于PDMS的链很柔软,它上面的官能基团活性又比较大,容易和各类高分子反应。因此,近几年来。聚硅氧烷与有机高分子相结合的研究蓬勃发展,文献很多,可看成发展的一个主要趋势。
(1)增强塑料 引进少量PDMS,改进工程塑料(如尼龙、聚碳酸酯等)的韧性,提高冲击强度,同时也能改进机械加工的精密度。
(2)增强橡胶 在硅橡胶中引入少部分(<20%)热塑性高分子代替二氧化硅等无机填料,可制成热塑性弹性体(TPE),可用塑料方法加工成型,强度也可以提高很多。
(3)改进表面性能 在某些高分子(如环氧树脂、天然橡胶、聚酰亚胺等)中引入PDMS,即使数量仅为1%~3%,也可使其表面性能改观,从亲水变为疏水,加工时容易脱模,还可以改进润滑性能,使摩擦系数降低,在摩擦时不容易氧化破坏。
(4)制备分离膜 PDMS的透气率比其他高分子高一两个数量级,但它的强度差,不能单独作膜,和其他高分子结合解决了支撑问题,其选择系数也可提高。
(5)制备液晶骨骼 在聚氢甲基硅氧烷上,通过硅氢加成反应接上各种液晶基团以制备高分子化的液晶,使相变温度加宽,晶态比较稳定,某些液晶的化学效应也明显起来。
(6)降低加工温度 有些高分子如聚酰亚胺、聚芳酯等熔点很高,加工时有热分解,引入PDMS可降低其加工成型温度。
(7)医用材料 有机硅在医用材料方面应用广泛多样。
1.4.3 配合技术和新型添加剂
开发配合技术、加工技术和添加新的添加剂。配合技术的进步和添加新的添加剂赋予功能性的实例越来越多。例如添加炭黑开发了导电硅橡胶,从而开发了电子计算机键盘、数字钟表控制器、电视接触电路开关、电磁干扰屏蔽、汽车点火电缆、玻璃纤维等具有多种用途的产品。特殊加工技术进而开发了各种导向部件和负压元件等散热板和润滑脂。液体注射成型(LIMS)和就地成型(FIPG)加工技术的最新发展,它们分别在双组分和单组分的室温硫化硅橡胶的加工中体现出更大的优越性。同时,真空浇注成型和超高频连续挤出成型(UHF)等先进的加工技术已得到开发和应用。
通过添加新的添加剂改变或提高某些有机硅产品性能近年来也取得十分有实用价值的成果。如抑制侧甲基氧化反应发生和进一步清除硅羟基引起的主链降解是提高高温硫化硅橡胶和室温硫化硅橡胶在热空气中稳定性的两个重要方面。目前国内外都采用添加不同类型添加剂的方法提高硅橡胶热稳定性方面,都取得比较好的效果。如美国DC、GE公司采用添加两种或两种以上复合金属化合物,使硅橡胶在275℃左右也能长期使用;中国科学院北京化学研究所采用添加硅氮环体或聚合体,以消除硅橡胶端羟基和水引发的主链降解,能有效提高硅橡胶在封闭体系内的热稳定性;上海高分子材料研究开发中心和上海爱世博有机硅材料有限公司采取添加自行创新合成的特殊高分子化合物,在高温场合下(250℃以上),能产生离子,多次阻止自由基氧化和再氧化,最终形成热稳定的产物.有效阻止硅橡胶侧链的热高温降解,使硅橡胶的耐热时间(在250~350℃下)提高2~5倍,经北京航空材料研究院应用,将它加入二甲基室温硫化硅橡胶中,在特定硫化体系中,经300℃、600h长时间热空气考核,仍未失去弹性,已投入实际应用。另外,还通过在高温硫化硅橡胶中添加极少量的有机硅抗黄变剂和在环氧树脂中加入不超过1%特殊有机硅聚合物,分别达到抗黄变和改变环氧树脂表面性能(不黏其他材料以及光滑等)、达到内脱模等目的。
特别值得指出的是。有机硅工业不同于通用合成材料,通用合成材料是以原料制造工艺、大型生产技术及产品加工为中心发展的,而有机硅工业则是以产品开发为中心发展的。以日本为例,三十多年来一直采用直接法合成硅单体。据称生产工艺变化不大,而有机硅技术重点主要在于产品应用、有机基团引入聚合物结构、交联技术和配合技术等方面。
总体上来说,有机硅材料技术的发展趋势主要体现在有机硅化合物以及有机硅高分子功能化的实现,具体主要包括以下诸方面的微观技术手段。
①变换硅氧烷分子结构,例如变换分子的大小、形状(线状,分枝状)、交联密度等。
②改变结合在硅原子上的有机基团,例如烷基(甲基、乙基多碳基)、苯基、乙烯基、氢基、聚醚基等。
③选择不同的固化方法,例如过氧化物固化,脱氢反应、脱水反应、加成反应,脱醇反应、脱酮肟反应、紫外线固化、电子束固化等。
④采用有机树脂改性(共聚、混合),例如环氧、醇酸、聚醚、丙烯酸等。
⑤选择不同填料,例如金属皂、二氧化硅、炭黑、氧化钛等。
⑥选择各种不同二次加工技术,例如乳液、溶液脂、炼胶、胶黏带等。
⑦采用各种共聚技术,如本体聚合、嵌段聚合、乳液聚合等。