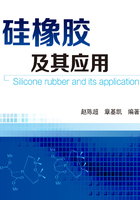
2.3 硅橡胶生胶合成
2.3.1 硅橡胶生胶合成原理
根据硅橡胶的品种要求:将一种或几种有机硅氯烷,先经水解缩合,制成硅氧烷低聚物,用作制备生胶主链的原料;再将(CH3)3SiCl或(CH3)2(CH2=CH)SiCl水解缩合制成(CH3)3SiOSi(CH3)3或(CH3)2(CH2=CH)SiOSi(CH2=CH)(CH3)2等中间体、封端剂;将这些原料经酸、碱催化平衡聚合或共聚合制成相应的硅橡胶。最后再将催化剂中和或分解得到规定的硅橡胶。
以合成甲基乙烯基生胶为例,合成过程的基本化学反应表示如下:
①氯硅烷水解
②裂解重排,精制环体
③催化平衡制备生胶
2.3.2 合成硅橡胶的主要工序
2.3.2.1 水解缩合工序
水解缩合是合成有机硅聚合的最重要工序。通常,水解缩合过程是将甲基氯硅烷、甲基苯基氯硅烷按规定比例与甲苯、二甲苯等溶剂均匀混合,在搅拌下缓慢加入到过量的水中(或水与其他溶剂中)进行水解。水解时保持一定温度,水解完成后静置至硅醇和酸水分层,然后放出下层酸水,再用水将硅醇洗至中性。水解工艺流程示意图,见图2-1。

图2-1 水解工艺流程示意图
1—碱贮罐;2—泵;3—二甲基二氯硅烷贮槽;4—水解釜;5—酸分层器;6—中和器;7—碱分层器;8—水解物贮罐;9—过滤器;F—流量计
硅烷水解后,生成硅醇,除继续缩聚成线型或支化低聚物外,分子本身也可自行缩聚成环体。环体的形成消耗了组分中的官能团(羟基),减少了各组分分子间共缩聚的机会,故不利于均匀共缩聚体的生成。水解后组分中环体众多,分子结构的不均匀性越大,最后产品的性能相差越大。
水解后各组分分子间的共缩聚和分子本身自缩聚反应是一种彼此竞争的关系,若在单位体积内各组分分子浓度大,分子间距离小,彼此碰撞的机会多,各组分分子及其官能基团彼此碰撞而反应机会也多,共缩聚就占优势;若单位体积内分子浓度低,各组分分子间距离大,彼此碰撞机会少,分子本身含有的官能基团反应的机会相对地增多,分子本身自缩聚的反应就占优势。
有机硅环体的生成,是一定链长的硅醇内羟基基团彼此反应、本身自缩聚的结果。如环体中分子链间内应力愈小,环体就愈稳定,生成量也愈多。如二甲基二氯硅烷水解时,有三环体、四环体、五环体等生成,其中四环体量较多。
二甲基二氯硅烷水解物是制取纯D3、D4、D5的基础原料。一般条件下,该水解物的黏度越高,其中所含的线型体含量就越多,所以根据不同的需要,二甲水解过程中水解物的黏度是一个控制指标,如直接就用水解物作为原料来制取高摩尔质量的端羟基聚二甲基硅氧烷,此时水解物的黏度要求就要高些,因为黏度高线型体的含量就高。而作为制取纯D3、D4、D5的水解物原料,该水解物的黏度就要求低许多,这样在后道工序中就会节约很多能耗。
各种单体共水解时,虽然配方一样,往往由于控制的水解条件不同,水解产物的组分和环体生成量相差很大。
影响水解反应的主要因素有单体结构、水的用量、介质的pH值和水解温度等。
2.3.2.2 裂解重排的精制环体工序
裂解重排过程就是将二甲水解物在碱性催化剂条件下进行裂解重排反应,以制得含D480%左右和D35%、D515%左右的裂解物(此裂解物如果未知组分含量在控制范围内,可以作为直接用于配制缩合型室温硫化硅橡胶),裂解反应过程中含(CH3)3SiO1.5或Si—H键的硅氧烷成为硅醇钾盐留于釜底。裂解工艺流程示意图,见图2-2。

图2-2 裂解工艺流程示意图
1—裂解釜;2—裂解柱;3,6—冷凝器;4—分水器;5—蒸馏柱;7,8—八甲基环四硅氧烷计量罐;9—八甲基环四硅氧烷贮罐;F—流量计
裂解常用的碱性催化剂是氢氧化钾,由于反应条件和设备的特殊性,连续往裂解釜内直接加固体氢氧化钾不能实现,所以一般都是将氢氧化钾配制成一定浓度的溶液,然后再按一定的进料比连续加入到裂解釜内。
反应机理如下:水解物在碱性氢氧化钾的催化作用下,在线型体存在以下反应,即缩合、成环与开环平衡反应。
①水解物与KOH发生端羟基置换反应,使二羟基封端的线状硅氧烷形成硅醇钾:
②在硅醇钾作用下发生缩合反应,形成长链高分子聚合物。
③硅醇钾又是环硅氧烷开环聚合的引发剂,高聚物发生解聚反应,生成环硅氧烷,解聚反应和聚合反应是可逆反应。
成环与开环平衡反应,线型体裂解重排成环体,是由于在聚硅氧烷分子链中,氧原子的孤电子对与邻近硅原子的3d空轨道配位,在催化剂和热作用下使O—Si—O键断裂所致。
④在温度较高的情况下,发生歧化反应,形成交联聚合物,使环体收率下降。
因此,裂解重排反应过程中同时存在上述反应,在反应中对裂解物组分影响最大的主要是③反应、是成环与开环的平衡反应、是裂解反应过程的主反应。由于反应的不断进行,要使反应向反应式的右边移动形成更多的环体,由平衡反应的规律可知就需破坏反应式的平衡,使反应向有利的方向移动;②反应是制取硅橡胶的主反应,但在裂解重排反应中属于副反应,应当尽量控制这类反应的发生,否则裂解釜就会出现挂胶严重、釜内反应较差等问题,这样不但增加能耗,而且裂解物质也没保证,抑制②反应的发生程度跟催化剂的使用量有直接的关系;由上面反应机理可知,①反应是基础反应,因此可以认为它是整个裂解重排反应过程的引发阶段。
由于裂解反应是二甲基硅氧烷的聚合与降解环化的可逆反应,所以只有将环硅氧烷不断移出反应体系,才能使反应不断向生成环硅氧烷方向移动。
目前,国内已采用溶剂法裂解氯硅烷水解物制备环硅氧烷的新工艺,解决了传统裂解工艺存在的问题。
将溶剂油作为热载体加入到裂解釜内,使反应体系黏度下降,传热均匀,没有局部过热现象,控制了歧化反应的发生。交联物明显减少,产品收率提高了4%~6%。碱催化剂活性寿命延长,碱耗量仅为原来的十分之一。生产排渣周期提高5~8倍,另外由于体系黏度的减小,使分子扩散速度加快、环体蒸发速度加快,提高了单位设备产出率。
其工艺路线如下:
经过脱氯处理,除去其中微量氯。脱氯后的水解物进行裂解反应,在反应体系内加入溶剂油(作为热载体),它可起到稀释反应物浓度、降低反应体系黏度、使传热均匀、消除局部过热现象的作用。裂解后产出的混合环硅氧烷,可直接作为产品,亦可进一步进行分离。经分离后获得纯D4≥98%(质量分数)产品,其他成分可作为产品,也可返回裂解釜进行重排反应。
该技术解决了水解物裂解工业化问题。由于反应体系黏度的减小,解决了传热问题,可将裂解釜任意放大。同时可将老工艺中蒸发、裂解、蒸干3步合并为由1步裂解完成,使工艺简化。
新工艺中引入环体精馏部分,使裂解出来的环体清澈透明,不含机械杂质、线状物及碱胶等;可获得98%D4,替代进口产品;避免了老工艺中由水洗环体而带来的损失。
2.3.2.3 催化平衡的聚合工序
环硅氧烷开环聚合反应,按催化剂性质可分为阳离子聚合反应的酸性催化剂和阴离子聚合反应的碱性催化剂两大类。
酸性催化剂主要是硫酸,其缺点是洗涤聚合物、除去催化剂的过程很困难,工艺设备复杂。碱性催化剂主要优点是用量少,可以钝化或中和以终止反应。目前工业生产上,普遍采用四甲基氢氧化铵、氢氧化钾作催化剂,D4(或DMC)与乙烯基环硅氧烷低聚物,经开环聚合制取硅橡胶生胶。
(1)化学反应方程式
①甲基封端型
②甲基乙烯基封端型
反应机理:乙烯基硅橡胶的合成反应属阴离子催化开环聚合反应。聚合过程由4个阶段组成:a.引发阶段(形成活性中心);b.链增长阶段;c.链终止阶段(活性中心消失);d.链转移形成新的活性点。反应开始时,在碱催化剂使用和加热下,环硅氧烷Si-O-Si链产生断裂(开环),生成链端含阴离子的线状聚硅氧烷低聚体,后进一步与环体反应,产生快速链增长,逐步成为高摩尔质量的线型聚硅氧烷。在链增长中形成的更大活性中心可以在遇到封端剂(或H2O)而终止反应,也可以继续与已形成的大分子链发生反应,使分子进行重排或重新变成环体。这一过程称为聚硅氧烷调聚反应平衡过程。在链增长和链转移中形成的活性中心,如通过加热使催化剂分解或被中和,活性中心消失,反应体系趋于稳定。
聚合过程的几个阶段可用反应式表述如下(以KOH催化为例):
a.引发阶段(形成活性中心)
b.链增长阶段(形成更大活性中心)
c.链终止阶段(活性中心消失)
d.链的转移(形成更大活性中心)
或者大分子链也可以重排成环
(2)主要原材料品种及要求
①甲基环硅氧烷(D4、DMC)。甲基乙烯基硅橡胶分子主链由环硅氧烷开环聚合而成,因此,环硅氧烷(D4和DMC)是合成它的主要原料。D4的化学名称为八甲基环四硅氧烷,它的主要性能要符合国家标准GB/T 20435—2006规定的技术要求:
DMC是以D4为主的二甲基硅氧烷混合环体,它的主要性能要符合国家标准GB/T 20436—2006规定的技术要求:
甲基环硅氧烷是有机硅的主要中间体,它的制造方法是以高效精馏得到的高纯二甲基二氯硅烷为原料,采用水解或恒沸酸水解制成水解料,然后进行中和,再在专用的裂解装置中在加热和抽真空的条件下,加入KOH溶液,使水解料进行重排(裂解),制成混合环体,再进行精馏而得到精单体(D4或DMC)。
制备高摩尔质量(40×104~80×104g/mol)的线型聚硅氧烷橡胶生胶,必须要有高纯度的原料,即甲基环体纯度必须符合橡胶级要求,达到:
a.外观无色透明,无铁锈等机械杂质,原料呈中性;
b.环体总含量≥99%,其中D4含量≥85%,D6尽量少一些;
c.三官能团链节MeSiO1.5(T)低于0.02%,单官能团链节Me3SiO(M)低于0.01%,而Si—H键及Si—OH键的含量也越低越好。
生产中,一般通过色谱法来检验原料的纯度,并用小样聚合来检查环硅氧烷的纯度和聚合活性。实践证明:D4的纯度较高,色谱分析纯度可达99.9%,小样聚合分子量可达150万以上;DMC的环体总纯度可达99%,但小样聚合分子量只能达到80万~120万。这表明,目前DMC和D4的质量还存在一定差距。D4、DMC的聚合活性测试方法如下:用精度为1g的天称称取(150±1)gD4(DMC)样品置于带加热的三口烧瓶中,搭好装置后,将系统升温,开启氮气阀门通氮气鼓泡,打开真空泵,抽真空脱水2h,控制温度为(105±3)℃,真空度为-0.07MPa。停真空,升温至110℃,用针管加入0.4g碱胶催化剂,用秒表测出加碱胶到物料开始变稠的时间即为反应活性时间(以s计算)。接着升温至(120±10)℃,保温2h,进行聚合反应,结束后按标准方法测试分子量。D4的活性一般为5~10s,而DMC要达8~15s。这很可能是因为DMC中存在着微量杂质或其他含酸物质所致。例如,在裂解二甲基二氯硅烷水介物和精馏裂解物时,因真空度不够而氧化产生的甲醛,就能与催化剂四甲基氢氧化铵发生反应而降低体系聚合活性。
从表2-1中原料纯度的分析结果可见,DMC的纯度比D4低,而含水量和硅羟基含量比较高。
表2-1 DMC纯度分析结果

②甲基乙烯基环硅氧烷(VMC)。甲基乙烯基硅橡胶合成中通过加入不同量的四甲基四乙烯基环四硅氧烷(简称乙烯基环体)而生产不同型号的生胶产品。甲基乙烯基四环体是一种由四环体、五环体、三环体和六环体组成的混合物。
分子式为[(CH2=CH)(CH3)SiO]4
物化常数为:
熔点/℃ -44
闪点/℃ 98
沸点/℃ 111~112
相对密度(d20) 0.990~1.000
a.乙烯基环体的技术指标:
外观 无色透明液体
四环体含量 ≥95%
三环体含量 ≤0.3%
五环体含量 ≤5%
乙烯基含量 ≥29.5%
b.乙烯基环体的特性:带有乙烯基活性基团的环体或化学链节可和硅氢化合物在催化剂作用下发生加成反应;在甲基硅橡胶中引入乙烯基基团后,增加了反应基团和硫化交联点,使胶料提高了硫化反应活性,提高了胶料的物理机械性能;乙烯基四环体在催化剂作用下开环,并与其他有机硅中间体起镶嵌作用,形成高分子化学物。
c.乙烯基环体的制法:工业上,乙烯基环体的合成是用乙炔与含氢单体在铂配合物催化下进行加成反应生成甲基乙烯基二氯硅烷,然后经水解,热裂解得混合环体,再经精馏制得精单体。
催化加成
→水解,热裂解→(CH3CH2=CHSiO)4
→精馏→甲基乙烯基四环体精单体。
d.乙烯基环体中三官能团检验方法:称取(150±1)g纯D4和(9±0.2)g乙烯基环体,加入到250mL三口烧瓶中,升温至(85±5)℃,在-0.07~-0.065MPa真空和通氮气鼓泡条件下,脱水2h,再升温至(115+5)℃,加入0.4g碱胶催化剂,保温聚合2h,冷却后,取出胶料称取2~3g放入锥形瓶中,加入100~150g甲苯,在振动下溶解3~5h,用4#砂芯漏斗或纱网过滤,观察是否有苯中不溶的果冻状交联物存在。
乙烯基环体的加入量虽然很少(0.05%~5%),但纯度必须很高,否则将对合成反应和VMQ质量产生影响。对VMC的要求不仅外观应该无色透明无机械杂质,乙烯基含量≥29.3%,而且三官能团的组分通过小试验证要达到要求。国内生产VMC的企业较多,生产所用原料和工艺路线有所不同,因而产品质量有一些差异。
甲基乙烯基环硅氧烷的用量可按下列公式进行计算(以摩尔分数表示):
式中 ——甲基乙烯基环体质量;
——二甲基环硅氧烷(D4或DMC)质量;
W低——脱水时蒸出的低沸物质量;
Vi——生胶中乙烯基物质的量;
Si——生胶中Si的物质的量;
MVi——100个Si有若干个乙烯基基团;
86——甲基乙烯基硅氧烷链节分子量;
74——二甲基硅氧烷链节分子量。
③生胶封端剂。生胶封端剂(分子量调节剂)又称为终止剂。在阴离子聚合反应过程中,为了控制聚合物的分子量,有时需要加入生胶封端剂。在聚合反应系统中,生胶封端剂是一类比较活泼的物质,它很容易和正在增长的大分子进行反应,将活性链终止,同时生胶封端剂分子本身又生成了新的阴离子基团,这种阴离子基团的活性和大分子相同或相近,因而可以继续引发聚合。加入生胶封端剂以后可降低聚合物的分子量,对聚合反应速率则没有太大的影响。
甲基乙烯基硅橡胶合成中用碱性催化剂进行环硅氧烷的开环聚合,必须注意聚合反应生成物的分子量调节,任何单官能化合物,其中包括水都是硅氧链的载体。但是,为了获得预定分子量的生胶,最适合的分子量调节剂是易于在环硅氧烷中均匀分散的六有机基二硅氧烷,常用的是下列结构的低黏度硅油:
采用低黏度甲基硅油(5~10mPa·s)和低黏度乙烯基硅油(18~22mPa·s)作生胶链封端剂。封端剂加入量的多少是调节硅生胶分子量的主要手段,要经过生产实践不断调节,并熟练掌握。以乙烯基硅油为封端剂生产的生胶,在分子键端含有乙烯基,使硅橡胶在交联过程中减少悬挂链,这对硅橡胶性能改进有一定好处。乙烯基生胶生产中要求封端剂无杂质、黏度等指标要稳定,才能确保产品的质量。
分子量调节的准确度,还取决于外来的链载体存在。聚合用的环硅氧烷、分子量调节剂、催化剂都必须绝对无水,尽量控制在30×10-6以下。工业上,一般都采取聚合前先将反应混合物共沸干燥(脱水)的方法。
生胶封端剂用量公式:
式中 Ww——生胶封端剂用量;
M1——不加生胶封端剂时,所得生胶的分子量;
M2——要求控制的分子量;
M3——生胶封端剂的分子量;
W——环硅氧烷的用量。
④催化剂及中和剂。生胶合成中可以使用的碱性催化剂有碱金属氢氧化物、碱金属硅醇盐、四甲基氢氧化铵、四丁基氢氧化磷等。国外工业生产普遍使用KOH,我国目前多采用四甲基氢氧化铵,应用最广的催化剂是硅氧烷醇钾和硅氧烷醇四甲基铵。前者用KOH与环硅氧烷在加热条件下制备,后者用四甲基氢氧化铵与环硅氧烷在加热和抽真空条件下制备,制成的硅氧烷醇四甲基铵被称为“碱胶”。其中,硅氧烷醇钾便宜易得,工业应用也最成熟,但它的催化活性较低,一般要在140~160℃下反应数小时才能完成平衡,反应后要将KOH中和掉装置也较复杂,而且用CO2中和时产生的K2CO3结晶析出还可能影响生胶的透明度。
硅氧烷醇四甲基铵的活性要高得多,在D4开环聚合反应中的催化活性是KOH的150倍。在90~110℃具有很好的聚合催化作用,反应1~2h就可以基本平衡。四甲基氢氧化铵虽然较贵,但加入量只需3×10-5~5×10-5,对成本影响不大。反应完成后,只要提高温度到130℃以上,Me4NOH就能很快分解为三甲胺和甲醇,失去催化作用,通过脱低分子时排除。
因此,这种催化剂也被称为“暂时性催化剂”,无需中和工序。这种暂时性催化剂十分适合于连续聚合工艺,并在聚合过程中较易控制生胶的分子量。但四甲基氢氧化铵分解后,在脱低分子工艺必须严格,将Me3N尽量抽除干净,否则生胶中残留的Me3N使是10μL/L以下也可能使胶出现鱼腥臭味或致使橡胶制品发黄,并有毒性,使应用受到一定限制。而且由于四甲基氢氧化铵一般先由氯甲烷与三甲胺反应制得(CH3)4NCl,残存在生胶中的氯离子和碱金属还将使硅橡胶生胶解聚并影响透明度。四甲基氢氧化铵的制法最好采用碘甲烷法或(CH3)4NCl电解法及离子交换法,以控制氯离子含量小于50×10-6,碱金属含量小于5×10-6。
我国硅橡胶的工业化生产中主要采用Me4NOH作催化剂。而国外公司多数采用硅醇钾盐或其他化合物为催化剂,如表2-2所示。
表2-2 各公司生胶合成使用催化剂情况表

碱胶制法:四甲基氢氧化铵一般是含有约50%结晶水的固体。少量水分的存在会影响它的催化活性,并降低所合成聚硅氧烷的摩尔质量,因此使用时必须除去。为了使用方便,计量准确,常先将其与D4或DMC反应制成四甲基氢氧化铵硅醇盐(简称碱胶),以四甲基氢氧化铵硅醇盐作为环硅氧烷聚合的催化剂使用。其反应示意图如下:
根据已有的文献和专利报道,制备Me4NOH碱胶的过程如下:含50%结晶水的四甲基氢氧化铵与D4或DMC按(CH3)4NOH含量2%~10%的比例投入带有搅拌或氮气鼓泡的反应器中,在40~50℃,抽真空、搅拌下反应半小时,而后再升温至80~90℃,真空度控制在-0.07~-0.06MPa,不断蒸出水分,脱除体系中水分,反应物黏度逐渐增大至黏稠状,经4~5h反应,反应物黏度开始下降并成透明黏稠,就可以冷却出料,即得四甲基氢氧化铵硅醇盐(碱胶),分析其含量后,密封贮存备用。注意密闭贮存,避免接触空气,因空气中的CO2会使催化剂失效。
为了得到高活性碱胶,在制备过程中温度的控制尤为重要,在刚开始脱水的过程中温度不要超过60℃,以防Me4NOH的缓慢分解。另外,由于碱胶中残余的水分会降低所合成硅橡胶生胶的分子量,因而在四甲基氢氧化铵除水过程中可以适当延长真空脱水的时间,以尽可能地降低体系内水分的含量。
用(CH3)4NOH碱胶作催化剂合成硅橡胶,催化剂用量一般为环硅氧烷及止链剂总量的0.08‰~0.1‰。碱胶催化剂用量计算公式:
式中 X——碱胶用量;
C——催化剂用量;
A%——碱胶中催化剂含量;
——聚合时环硅氧烷及封端剂用量;
W低——脱水时蒸出的低分子质量。
另一种暂时性催化剂为四丁基氢氧化磷,它在聚合后升温至130℃以上也被迅速分解成完全中性的三丁基氧磷(C4H9)3PO及正丁烷C4H10得到聚合物无臭味,无色透明非常稳定,残留在生胶中的(C4H9)3PO是热稳定剂,又无毒性,对产品应用有利。
⑤主要原材料的消耗定额,见下表: