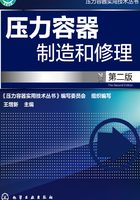
2.10 热处理
2.10.1 焊后消除应力热处理
压力容器的焊后消除应力热处理(PWHT)是保证压力容器内在质量的重要技术手段之一。其目的在于:消除焊接残余应力、冷变形应力和组装的拘束应力,软化淬硬区,改善组织,减少含氢量,尤其对合金钢,可以改善力学性能及耐蚀性,还可以稳定构件的几何尺寸。
压力容器的PWHT通常是将构件加热到Ac1以下某一确定的温度,保温一段时间,然后在炉内冷却至300~400℃出炉空冷。
以下为常用的PWHT方式。
2.10.1.1 炉内整体热处理
对于高压容器、中压反应和储存容器、盛装混合液化石油气的卧式储罐、移动式压力容器等应根据相关标准和设计图样采用炉内整体热处理。这是对压力容器进行PWHT的首选方式。热处理装置(炉)应配有自动记录曲线的测温仪表,并保证加热区内最高与最低温度之差不大于80℃。我国一些大型压力容器制造厂的大型热处理炉,对热处理过程都配备有程序控制系统,在保温期间,炉膛温差大都可控制在±15℃以内。
对于需要进行整体PWHT的压力容器而言,应安排在全部焊接工作已结束,竣工液压试验之前进行。
在PWHT中起主导作用的两个因素是加热温度和保温时间。对需要多次进行热处理的构件,为表征这两个因素重叠作用的程度,广泛采用拉松-米勒(Larson-Miller)参数(又称回火参数)P。其表示式为
P=T(C+lgt)×10-3 (2-24)
式中 T——加热温度,K;
C——常数,约等于20;
t——保温时间。
由该式可以看出,温度比时间的作用大得多。不同的钢材P值范围不同。一个容器产品在制造过程中可能会有多次热处理,且加热温度也不同,计算时可加以换算。对于1.25Cr-0.5Mo钢,推荐P值为20.2~20.6。
鉴于压力容器的最终PWHT在整个制造过程中的重要性,对PWHT全过程应进行有效控制,对热处理装置应配有自动记录曲线的测温仪表。
①装炉时炉内温度不得高于400℃。特殊情况下,如厚度大于60mm或结构复杂的容器,装炉温度可低于300℃。所有测温点应保持与容器壳壁直接接触。对于大型、厚壁容器,在炉前、炉中、炉后的三个横截面各四个方位上均需设置测温点,超厚筒体内壁尚应增加测点。加热时还应采取措施,防止火焰直接喷向容器壳壁而可能造成局部过度氧化。
②升温速度应是可控的,且不应超过5500/δ℃/h(δ为容器壁厚),且不得超过220℃/h,最小可为55℃/h。升温期间,加热区内任意长度为4600mm内温差不得大于140℃。
③保温期间,最高与最低温度之差不宜大于80℃。不同钢材的加热温度与保温时间见表2-19。
表2-19 常用钢号焊后热处理规范

①钢质母材类别按NB/T 47014规定。
②Fe-1、Fe-3类别的钢质母材,当不能按本表规定的最低保温温度进行焊后热处理时,可按NB/T 47015—2011表6规定降低保温温度,延长保温时间;Fe-9B类别的钢质母材保温温度不得超过635℃,当不能按本表规定的最低保温温度进行焊后热处理时,可按NB/T 47015—2011表6规定降低最低保温温度(最多允许降低55℃),延长保温时间。
③Fe-5A类、Fe-5B-1组的钢质母材,当不能按本表规定的最低保温温度进行焊后热处理时,最低保温温度可降低30℃,降低最低保温温度焊后热处理最短保温时间:
a.当δPWHT≤50mm时,为4h与(4δPWHT/25)h中的较大值;
b.当δPWHT>50mm时,为NB/T 47015—2011表6中最短保温时间的4倍。
④Fe-6、Fe-7中的06Cr13、06Cr13Al型不锈钢,当同时具备下列条件时,无需进行焊后热处理:
a.钢材中碳含量不大于0.08%;
b.用能产生Cr-Ni奥氏体熔敷金属或非空气淬硬的Ni-Cr-Fe熔敷金属的焊条施焊;
c.焊接接头母材厚度不大于10mm,或母材厚度为10~38mm且保持230℃预热温度;
d.焊接接头100%射线透照检测。
⑤Fe-8、Fe-10H类钢质母材焊接接头既不要求,也不禁止采用焊后热处理。
⑥焊件温度高于或等于650℃时,冷却速度不应大于55℃/h,低于650℃后迅速冷却,冷却速度应足以防止脆化。
⑦Fe-5B-2类焊后热处理保温温度与焊缝金属成分密切相关,表中所列数值尚需调整。
④降温速度不得超过7000/δ℃/h,且不得超过280℃/h,最小可为55℃/h。
⑤出炉时的炉温不得高于400℃,北方地区在冬季,可适当降低出炉温度。出炉后应在静止的空气中冷却。
对于结构复杂或封闭性好的厚壁容器,在加热与降温期间速度宜取低值,以防止过大的温差对结构造成危害。
2.10.1.2 炉内分段热处理
压力容器应尽可能进行整体焊后热处理,这对提高产品的使用性能有很大的好处。对于较长的产品,由于受炉子长度的限制,不能进行整体热处理时,也可以进行调头分段热处理。此时,重叠加热长度至少为1500mm。炉口应为隔热,容器的炉外部分应用绝热材料包覆起来,以控制纵向温度梯度。距炉口处,壳壁的温度不宜小于近炉口处壳壁温度的一半(R为壳体内半径,S为厚度,均以mm为单位)。但产品的分段热处理不一定能保证与整体工业炉处理有同等的耐应力腐蚀性能。
如更长者,可将产品分成几段制造,各段组焊完毕,分别进炉进行热处理,然后再将各段用环缝组焊起来,焊完后可对其环缝进行环带局部热处理。
2.10.1.3 焊缝局部热处理
超长容器的分段制造、分段炉内热处理后,再进行总装环缝的组装焊接。对于总装环缝只能采用环带加热局部热处理。局部热处理的加热温度和保温时间与进炉热处理相同。保温环带宽度从环缝的最大宽度边缘算起,每侧宽度应不小于筒体壁厚或50mm,取两者较小值。加热带以外的壳体延伸段应采用保温材料包覆起来,以控制纵向温度梯度。距保温温度环带边缘3倍壁厚处(外侧),壳壁的温度不宜低于环带边缘处实际温度的一半(图2-79)。

图2-79 环带局部热处理规定要求示意图
对于管道或短管的环带局部加热,加热带宽度在焊缝中心线两侧均不小于完工焊缝最大宽度的3倍。对于一个包含接管或其他焊接附件的需焊后进行环带局部热处理的容器,环形带应包围整个容器圆周,并包括接管或焊接附件,自接管或附件与容器连接的焊缝算起,环形加热带宽度至少比器壁厚度宽出6倍。为了避免温度梯度的危害,该加热环带应进行有效保温。加热温度及保温时间按要求进行。对容器上的纵、环焊缝返修后的局部热处理,也可照此办理。
焊缝局部热处理的加热元件近年来大量采用远红外电加热元件组成的履带式加热器。对于管道或接管环缝的局部热处理可采用绳状电红外加热器。大型容器现场组装环焊缝的局部热处理,国内外已普遍采用瓣式燃气(油)加热炉,热处理的效果得到较大改善。
焊缝局部热处理的全过程也应严格控制,即应设置测温点,对加热升温、保温、降温应有自动记录和显示,并可随时进行监控与调整。
2.10.2 其他焊后热处理
2.10.2.1 电渣焊焊后热处理
电渣焊作为一种高效的焊接工艺方法,被广泛使用于大型压力容器制造厂,尤其是厚壁容器的筒节纵缝、封头拼板焊缝。其优点在于:①焊接是垂直状态下进行的,所以焊缝中不易产生气孔及夹渣;②可以不开坡口而一次焊成,生产率高,焊接厚板时尤其明显;③除了采用单丝、多丝电渣焊外,对于异形断面,可以采用熔嘴电渣焊。但是,电渣焊的最大弊端是焊缝和热影响区晶粒粗大,由于焊缝和热影响区在高温停留时间长,这是电渣焊工艺特点所决定的。因此,对于电渣焊缝,焊后必须进行细化晶粒的正火处理。正火的目的是均匀组织,细化晶粒,改善焊缝的综合性能。当容器筒节与封头上的A类焊缝采用电渣焊时,对其进行正火处理的方式是多种多样的。
(1)封头电渣焊拼缝的正火
①封头拼接焊缝焊后应先正火一次,以便对焊缝先进行超声预检测。
②封头热成形可以在正火温度下进行。当加热炉无法保证正火加热要求时,必须在冲压成形后重新正火处理。
③正火加热宜采用热装炉,既可缩短加热时间,也可减少钢板表面氧化和烧损。通常装炉温度≤850℃,加热温度可参照表2-10,加热速度一般不大于200℃/h,保温时间以工件与炉壁颜色一致时算起,一般为1.5~2.5min/mm(工件厚度),升温时任意测温点间温差不应大于50℃,保温时温差不应大于25℃。
④正火处理应遵循“产品热处理工艺卡”的规定,热处理工艺应有焊接工艺评定支持。工艺卡应注明带焊接拼缝试板及母材试板。这两种试板可按模拟方式进行回火及PWHT热处理,然后对力学性能及焊缝金相组织进行检测,以评价焊缝正火处理的效果。只有当试板的性能指标满足技术要求时,封头才能转入下道工序。
⑤当正火处理空冷的冷却速度不能满足要求时,可采取正火后加速冷却工艺。加速冷却方式可以采用喷淋或水槽中冷却。封头直径不大于1600mm时可采取水槽中冷却,大于1600mm时采用专用喷淋装置进行喷淋冷却(图2-80)。

图2-80 封头、筒体喷淋淬火示意图
1—进水槽;2—内喷淋;3—外喷淋;4—封头;5—上喷淋;6—内筒
a.水槽中冷却方式:封头应焊好吊耳及十字支撑,试板可点焊于支撑上。把加热好的封头迅速吊入水槽中,上下摆动,使工件快速冷却下来,但会在工件表面产生大量蒸汽,形成一层紧密包围工件的蒸汽膜,将工件与介质隔绝,使工件冷却速度下降,加之工件入水有先后,冷却速度不一致,致使工件硬度不均,变形加大,同时水温也很快升高。为了克服上述缺点,目前广泛采用喷淋冷却方式。
b.采用喷淋方式:在我国已使用20多年。喷淋用工装比较复杂,但远较水槽淬火优越,尤其是旋转式喷淋装置,效果更好。
喷淋装置可根据工件大小形状而定。喷淋孔的大小与数量取决于进水量和水压,喷淋孔直径一般为2~3mm。装置的旋转是靠喷水的反作用力产生的。
喷淋淬火的用水量见表2-20。
表2-20 喷淋淬火的用水量

喷淋时间按t≈3S估算。其中,t为喷淋时间,s;S为工件厚度,mm。
(2)筒节电渣焊纵缝的正火
①大直径筒节如采用电渣焊拼板,当要进行冷卷或中温卷板时,应对拼缝先进行一次正火和超声预检测,以防止成形时焊缝开裂。
②筒节热成形的温度可参照表2-10,其他工艺参数要求同封头。
③筒节纵缝电渣焊后可按正火处理要求进行热校圆,为减少表面压坑,也可采取冷校或中温校圆,但也应在正火加超声检测之后。纵缝焊接试板的1/3可经模拟后序热处理后送检,另外2/3应伴随产品的热处理全过程。
④筒节直径≤1400mm时采取水罐冷却。直径>1400mm进可采用喷淋加速冷却。
经正火后加速冷却的封头、筒节电渣焊接头,σb≥540MPa及Cr-Mo钢材质,最好能在24h内进行回火处理。
除电渣焊焊缝必须经细化晶粒的正火处理外,气电立焊(简称EGW)近年也已被广泛采用。它是由普通的GMAW和电渣焊发展而形成的一种熔化极气体保护电弧焊方法。其主要优点是可不开坡口焊接厚板,生产率高,成本低。焊缝在垂直状态下一次焊成,从而也会形成热输入大,热影响区宽等弊端,对这一类焊接接头,也应进行正火处理以改善接头的金相组织与综合性能。
2.10.2.2 旋压成形封头消除应力热处理
对于冷旋压成形的各类封头(除奥氏体不锈钢封头外),都必须进行消除应力(简称SR)热处理,这不但可消除冷变形应力,还可降低硬度,使原有塑性、韧性指标得以恢复。通常可采取整体退火处理。封头应预先加焊防变形支撑,退火炉的加热、保温、冷却全过程应能控制并可自动记录。
2.10.2.3 金属垫片的热处理
压力容器的密封结构中采用的各种金属垫片,在保证密封的可靠性中担负着重要角色。金属垫片一般为经退火的软铝、软铜与黄铜、软钢、蒙耐尔或某些铬钢制成,经固熔化处理的奥氏体不锈钢也被广泛用于制作垫片。绝大部分垫片材料可选用退火状态供货的,以达到降低硬度的基本要求。也有在加工制造过程中,因冷变形致使材料硬度升高而不能满足垫片的技术要求,需要对垫片坯料进行退火处理。由于垫片材料的多样化,对垫坯料进行软化退火的工艺也各不相同。常用于制作垫片的材料退火温度见表2-21。
表2-21 常用垫片材料退火温度

2.10.2.4 螺栓、螺母的热处理
压力容器的密封结构中,螺栓和螺母是重要的承载零件,螺栓和螺母的力学性能与韧性指标是保证设备安全运行的两大因素。螺栓与螺母所用材质的选用与容器的操作压力、温度、耐蚀要求及密封垫类型等工况有关。除选用部分碳素钢如20钢、35钢外,绝大部分选用合金结构钢中的Mn-B、Mn-V-B、Cr、Cr-Mo、Cr-Mo-V、Cr-Ni-Mo等钢种系列。上述材料中,Q235A是热轧状况使用的,35钢需经正火而45钢及合金结构钢是必须经调质处理(淬火+回火)后才能使用。压力容器用螺栓的材质按GB 150.2—2011规定有40MnB、35CrMoA、25Cr2MoVA、40CrNiMoA等11种,此外,奥氏体不锈钢及部分马氏体不锈钢也可以用作螺栓、螺母材料。螺母材质的强度级别应比螺栓低一个级别。用作螺栓、螺母的材料首先需经锻制,然后按GB/T 3077《合金结构钢》中规定的热处理规范先进行淬火处理,再进行回火。在热处理前,锻坯应先进行初加工经调质处理后再精加工。经调质处理的高强钢制螺栓、螺母,在进行螺纹加工前应做磁粉检验。每个热处理炉批均应制备试样若干件,以验证零件经调质后的力学性能和冲击韧性。
2.10.2.5 封头、弯管的热处理
压力容器承压元件中的封头、弯管等承压零件,对所用材料如板材、管材的使用状态都有相关要求。如钢板GB 150.2中规定Q245R、Q345R厚度大于36mm,应在正火状态下使用。
Q370R、18MnMoNbR、13MnNiMoR、16MnDR、09MnNiDR、15CrMoR及高强钢、低温钢、Cr-Mo钢等任意厚度应在正火、正火+回火或调质状态下使用。
钢管所涉及的多项标准中对供货状态都有明确规定,其中大多数合金钢管均以正火、正火+回火、退火等热处理状态下供货,而奥氏体不锈钢管均为固溶化状态供货的。
当封头、弯管在制造过程中由于成形的方式、方法不同,致使技术条件所规定的热处理状态遭到破坏,从而必须对其重新进行热处理。
(1)封头
①如采用冷成形,当符合下列a~e中任意条件之一,且变形率超过表2-22的范围,应于成形后进行相应热处理恢复材料的性能。
表2-22 封头材料变形率

①当设计温度低于-100℃,或高于675℃时,变形率控制值为10%。
注:双向拉伸(如封头成形)变形率(%)=75δ[1-(Rf/Ro)]/Rf 式中,δ为板材厚度,mm;Rf为成形后中面半径,mm;Ro为成形前中面半径(对于平板为∞),mm。
a.盛装毒性为极度或高度危害介质的容器;
b.图样注明有应力腐蚀的容器
c.对碳钢、低合金钢,成形前厚度大于16mm者;
d.对碳钢、低合金钢,成形后减薄量大于10%者;
e.对碳钢、低合金钢,材料要求做冲击试验者。
②当封头采用热冲压成形时,如加热装置及加热过程控制能满足正火要求时,可以在正火热处理状态下冲压,否则应在成形后再进行正火处理。奥氏体不锈钢封头应在固溶化温度下冲压。封头正火热处理制度可参照电渣焊拼缝正火的规定。封头单独正火时,需对其进行支撑加固,以防止变形。封头的正火处理必须带随炉母材试板。对高强钢制的封头,正火后应及时回火处理。同样,做正火处理的封头,如有拼接焊缝时,对其拼缝应有相应的WPS支持。
(2)弯管
①常用的弯管方法见表2-15,凡符合冷弯条件者,应尽量进行冷弯。为防止应力腐蚀破坏,奥氏体不锈钢U形管冷弯后,应对U形管弯曲部位进行固溶化处理。固溶化处理的主要过程是把U形管弯曲部位当成一个电阻负载而直接通电,红热状态的弯头达到固溶化温度后保持一段时间,然后在管内吹扫氮气加速冷却。
②采用表2-17中的弯制工艺弯制的弯管,由于是环形加热后喷水急冷,对于高强钢、Cr-Mo等具有淬硬倾向的合金钢管而言是十分不利的,所以应在短时间内对其做回火处理,再对其外表做除锈处理和磁粉检测。
③如采用型模压制法制作高压厚壁弯头,与上述封头热成形一样,应对弯头进行正火或正火+回火处理。也可以在正火状态下压形,对于高强钢制弯头,正火后应及时做回火处理。
2.10.2.6 不锈钢的稳定化处理
稳定化处理:将含有强烈碳化物形成元素的奥氏体不锈钢,如06Cr18Ni11Ti,加热至840~900℃,并保温一定时间,然后较快地冷却,使各自形成稳定的碳化物而把碳固定住,以避免Cr23C6沿晶界析出而影响耐蚀性能,这样的处理方法称为稳定化处理。
对于压力容器中的奥氏体不锈钢零部件,如需进行热加工制作(含SR热处理),应尽量选用含稳定化元素(Ti、Nb等)的材料对有应力腐蚀倾向的不锈钢构件进行稳定化处理,这样不但可提高抗晶间腐蚀的能力,而且应力解除的效果也更理想[17]。对于那些需在奥氏体不锈钢危险温度(敏化温度)范围(450~850℃)内长期服役的设备,首先应选用含Ti、Nb不锈钢,如能进行一次稳定化处理,可进一步提高其使用寿命。
2.10.2.7 不锈钢的固溶化处理
固溶化处理:就是将一般奥氏体不锈钢加热至高温,使所有碳化物尽快地溶入奥氏体中并进行扩散使之均匀化,而后以适当的冷却速度使之冷却,以防止碳化物重新沉淀析出,以获得碳化物完全固溶于奥氏体基体内均匀的单相组织,从而得到高的耐蚀性和最好的延展性。
碳化物完全溶于奥氏体的温度一般高于900℃。奥氏体不锈钢的碳化物主要是铬的碳化物,它在钢中的溶解相当缓慢,欲使之在较短时间内完全溶解并均匀化,必须采用更高的温度。但温度太高,晶粒粗化,影响韧性,故生产中一般采用1000~1500℃,装炉温度≥850℃,保温时间一般按1~1.5min/mm计算。
现行标准中规定,几乎所有奥氏体不锈钢材料,其供货状态均为固溶化,对于奥氏体不锈钢构件的热加工,通常也被要求在固溶化温度下进行,所以它一种使用最广泛的热处理方法。