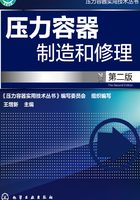
2.7 装配
2.7.1 筒节纵缝装配
筒节的制造过程中,至少有一条纵缝是在卷成形后组焊的,由于纵缝的组装没有积累误差,组装质量较易控制,但对于壁厚为20~45mm、直径为1000~6000mm的筒节,若弯卷过程控制不好,就会产生如图2-57所示的偏差,从而给组装带来麻烦。手工装配时,可以采用表2-18所列的专用工具来纠正这些偏差。

图2-57 卷板偏差
棱角度E≤(S/10+2)且不大于5mm
表2-18 常用组装工具

筒节的板料预弯质量不佳还会造成纵缝棱角度超差(图2-58),这时靠组装过程来控制是无能为力的,而只能在筒节纵缝焊后校圆工序中予以修正。

图2-58 棱角度
由于电渣焊工艺的特点,而要求筒节卷制时板头两端需留直边各不小于100~150mm。纵缝的错边也应控制在3mm以内。电渣焊纵缝的组装程序是:a.测筒节外周长,以确定焊口间隙处是否需撑大;b.二次号线,划出纵缝焊口切割线;c.装焊纵缝引弧板,引出板及Π形铁;d.按焊口间隙线切割(图2-59)。

图2-59 电渣焊纵缝装配
1—引出板;2—Π铁;3—引弧板;4—工件
近年来,国外设计制造了一些机械化纵缝组装装置。英国一家公司设计的组装设备是利用液压原理进行工作的,组装时,将筒节纵缝向下放在装置上,利用液压驱动,使装置在三个方向上运动,以纠正卷板产生的偏差。筒节纵缝组装好后,可直接在该装置上进行纵缝焊接(现在国内也有此设备),也可在纵缝定位焊后把筒节取下来。前苏联全苏化工机械制造设计工艺研究院设计的筒节纵缝组装设备,也是利用液压原理并借助液压夹钳、液缸和链条等机械传动装置来消除各种卷板偏差的。
国外还有一种悬挂在梁上的筒节纵缝组装设备,梁上左右挂着两个夹钳,夹钳插入筒节的两端,利用夹钳内各液压缸消除筒节的圆度误差、径向错边和端面错口。
2.7.2 壳体环缝的组装
环焊缝的组装比纵焊缝困难。一方面由于制造误差,每个筒节和封头的圆周长度往往不同,即直径大小有偏差;另一方面,筒节和封头往往有一定的圆度误差。此外组装时还必须控制环缝的间隙,以满足容器最终的总体尺寸要求。由于环缝组装的这种复杂性和需要大的工作量,因此,对机械化组装设备的需求是很迫切的。图2-60是国内目前常用的筒节环焊缝组装设备。小车式滚轮座可以上下、前后活动,可调节到合适的位置,以便与置于固定滚轮座上的筒节组对。然后用几块长条预焊搭板焊上,搭板数量应尽量少。组对中,可用螺栓撑圆器、间隙调节器、筒式万能夹具和单缸油压顶圆器等辅助工具和有关量具来矫正、对中、对齐(图2-61、图2-62)。

图2-60 筒节环焊缝的组对
1—滚轮座;2—辅助组对工具;3—小车式滚轮座

图2-61 螺栓撑圆器

图2-62 间隙调节器
国内曾制造一台液压外撑式筒体环焊缝组装装置。此装置适用于直径为1000~3200mm、壁厚为60mm以下的容器组装。该装置采用外撑式多油路(10个油缸)结构。每缸承受压力为21t,行程为470mm。液压系统由21.0MPa(210kgf/cm2)油泵供给,电动机为30kW,无级变速。设备结构简单,操作方便,使组装容器的劳动条件大大改善。
图2-63是一种典型的封头环焊缝组装装置。用真空吸持器3将封头5背面吸在旋转圆环2上,该环可在可摆动框架上移动。当封头调整至预定位置后,即依靠支架4用液压装置将框架旋转至垂直位置。组装时,封头可按自身的中心轴线旋转至所要求的位置,然后与筒节定位焊。

图2-63 封头环焊缝组装装置
1—框架;2—旋转圆环;3—真空吸持器;4—支架;5—封头
2.7.3 人孔、接管、支座等零部件与壳体的组装
2.7.3.1 筒体划线
在筒体总装、焊接、无损检测等工序完成后,做总体尺寸检验,并找出筒体两端的四条中心线(按筒节下料展开的样冲标记),并核查是否等分,然后检查筒体两端心线是否扭曲。检查步骤如下。
①将筒体放在滚轮架上,转动筒体,用吊垂线方法,使一端口的A心在最高位置(图2-64)。

图2-64 检查筒体心线
②在另一端的A心上吊线,与端口交点C',测得C心的偏移值b。这说明由于环缝组装后心线发生扭曲。
③将心线偏移端的A心右移b/2距离至A1心上,重新吊线,使A1C1两点与垂线重合,并重新找出B1D1心线,核查等分的正确性。
④按纠正后的心线位置重新弹好粉线,并做好标记。此时筒体心线的扭曲已纠正,按图样上各管口位置划出所有接管开孔位置线、切割线、检查线,同时划出支座安装位置线,做好标记。
对于长大塔器,尤其是分段发运的塔器,每个分段的四条中心轴线、开孔位置线、塔盘支承圈的装配位置都要分别精确划出。目前,国内的工厂已有采用光学方法进行筒体划线(图2-65),包括筒体内壁的四条心线、塔盘及其他内件的标高位置线、塔壁所有开孔的位置线、支座安装位置线等,均可采用激光准直仪配上光学划线器迅速而准确地进行划线。对于分段发运的塔器,如能在厂内对筒体进行大段预装后整体划线,其划线效率更高,效果更佳。这类划线工艺最好在可调心的辊轮架上进行。但是,此类划线的装备投资较大,辅助时间较长。另一种比较简易可行的方法是,将第一层塔盘的所在筒节立于平台上,用角尺找好垂直度,再用划针盘划出第一层塔盘支承圈的平面位置线。此后,筒体上所有焊接零部件的标高位置均可按此平面为基准。所有各层塔盘支承圈的位置线,可采用经计量的盘尺一次量出。拉盘尺需用弹簧测力器,以减少测量误差。此方法的积累误差不超过1mm。

图2-65 塔设备筒体的光学划线装置
1—立架;2—前测标;3—钢丝;4—矫圆环;5—光学划线器;6—托辊;7—后测标
人孔等大管口及壳壁上的斜插管口,还应按相贯线展开后制作开孔切割样板。人孔等开孔如采用自动开孔切割装置进行切割,则可不必制作开孔样板。
2.7.3.2 按开孔切割位置线进行切割
坡口经打磨清理后用焊口检测器检测所有管孔坡口尺寸的正确性,如有不符则必须进行认真修正。
2.7.3.3 人孔的装配
(1)人孔接管与法兰的装配
人孔法兰有两种类型,一为平焊法兰,此时只需控制接管与法兰的垂直度偏差不大于1/100且不大于3mm即可。如为锻制对焊法兰,则应控制对接环缝间隙均匀。需要特别强调的是严禁将法兰密封面直接与地面或装配平台接触,以避免弄伤密封面。国外通常的做法是法兰与接管的装配、焊接都在小型变位器上进行。法兰不会被电弧击伤,焊接过程在最佳位置下完成的,质量容易保证。
(2)人孔盲板、轴耳的组装。
人孔盲板、轴与轴耳必须在人孔法兰上先行预组装。组装过程如下:
①先按人孔盲板外圆放样,划出轴耳切割位置线,也可以按放样制作切割样板,按样板进行划线;
②切割轴耳,同时割出焊接坡口;
③在人孔法兰上放好垫片,再盖上盲板,然后再组装轴耳、销轴,手把等零件。销轴之轴线应尽量与长圆孔轴耳中心重合。焊好轴耳后再卸下盲板,以便进行人孔与壳体的装配。
(3)在壳体上组装人孔
首先要按人孔接管伸出高度及补强圈厚度在人孔接管的四条心线上点焊定位筋板,再与筒体上的开孔进行预组装。必要时用气割修正坡口处孔径,使接管顺利装入且装配环隙适当均匀。
人孔与壳体的角焊缝由于有补强圈而使得无损检测难以实施,该角焊缝的质量主要取决于坡口的清洁度及尺寸精度。而低劣的焊缝质量又会造成泄漏,甚至安全隐患。因此,对人孔的装配全过程,包括划线、气割、修磨、组装、焊接、检查等各环节必须认真做好记录,明确质量责任。
人孔组装后在焊接前,对于薄壁容器尤其是塔器,内部预先采取支撑加固,以防焊后下塌。
人孔接管的内伸余量可按图样要求待内角缝焊好后割去。也可用样板划线预先将接管内伸余量割去。
分段发运的长大容器,当人孔靠近分段处500mm范围以内时,可只将人孔装配点焊,不必焊好,以利现场环缝的组装。
2.7.3.4 接管的装配
接管法兰与壳体组装前应做好如下工作:
①接管与法兰的装配焊接,应控制法兰平面相对接管轴线垂直度偏差不大于1/100且不大于3mm。装配点焊时应防止法兰密封面碰伤,最好在焊接变位器上进行。
②按法兰螺栓孔中要求,划出接管中心线及伸出高度位置线,并点焊定位板。接管伸出高度误差不大于±5mm;
③预装接管,并对壳体所开管孔坡口进行气割修正并打磨,使之坡口完全符合技术要求,环隙均匀。
国内有些工厂采用专用工装,可快速、简便、准确地安装各种规格的接管法兰。
2.7.3.5 支座的装配
压力容器的安放或安装都要通过各种支座再与基础平面接触。支座作为部件,其本身的制造质量,及其与容器壳壁的装配、焊接质量的好坏,将直接影响到压力容器运行的平稳与操作的安全性。此外,支座与容器壳壁的装配通常都处在该容器的总装阶段,因而将直接影响到容器的管口方位、标高、轴线倾斜度等质量要素。因此,支座的制作与装配全过程必须予以足够重视。
按现行的行业标准,规定有四种类型的支座:鞍式支座、腿式支座、支承式支座及耳式支座(图2-66~图2-69)。

图2-66 鞍式支座图

图2-67 腿式支座

图2-68 支承式支座图

图2-69 耳式支座
各类支座有其不同的适用场合、制造与装配质量要求。安装过程及方法也各不相同。但有些要求却是共同的:a.支座底板应保持在同一平面内;b.底板螺栓孔距离的误差应予严格控制;c.支座底平面不允许翘曲、倾斜。
现就部分支座的制造与装配过程要点做一简单介绍。
(1)鞍式支座
在零部件装配焊接时可将两件成对称状点焊在一起,以减少焊接变形。拆开后检查底板的平面度及立板的气割口弧形,如有问题应进行火焰矫正。鞍式支座的安装过程如下:
①在筒体底部的心线上找出支座安装位置线,并以筒体两端环缝检查线为基准划出弧形垫板装配位置线。
②配垫板,用螺旋或锲铁压紧,使垫板与筒壁贴紧,其间隙不大于2mm,进行点焊。
③在垫板上划出支座立板位置线。
④试装固定鞍座,当装配间隙过大或不均时用气割进行修正,使之间隙不大于2mm,进行点焊。
⑤旋转筒体,用水平仪检测固定鞍座底板,使其保持水平位置。
⑥按相同步骤装焊滑动鞍座。在气割修正时使2个鞍座等高。当装配间隙合适、底板已找水平,螺栓孔间距满足要求后即可点焊固定。
⑦再对2个鞍座的安装尺寸做一总体检测,合格后再进行焊接。
(2)腿式支座
有角钢支腿、管子支腿2种,还有3腿、4腿之分。先将支腿上部割出缺口,并修正底部平面,使其与支腿垂直。
角钢支腿安装过程如下:
①将容器两封头环缝检查线按支腿位置等分,并弹出粉线,做出标记。在一钢质平板上划出2个同心圆,直径分别为Db及筒体外径,并将圆周进行3等分或4等分;
②在平板上按底板螺栓孔位置点焊底板,再按相对位置点焊支腿。支腿应与平板保持垂直,其内径应与筒体外径一致。然后在支腿底端及中部点焊拉筋以固定各支腿相对位置。
③组装支腿,如下封头外径偏大时,对支腿及封头做少许修磨,使之支腿顺利装在筒体上,支腿缺口应对准环缝,再以筒体下端口检查线为基准控制3支腿的H尺寸一致后点焊牢固(图2-67)。
④在筒壁的各等分心线上分别弹粉线,以检测支腿与筒体轴线的平行度,使其偏差不大于H/500并不大于2mm。同时再复核底板螺孔相对位置尺寸,当合格后再进行焊接。底部拉筋可不予卸除,设备发运时权当加固支撑。
(3)支承式支座
由于封头、垫板的成形误差及筋板或钢管与垫板连接的相贯线展开、下料的误差,使得支承式支座的安装质量难以把握。尤其是当支座数量大于3个时其安装难度更大。当工厂的装备条件许可时,建议采取如下措施。
①支座筋板应进行光电切割、数控切割或靠模切割制备。此时,支座部件的装配尺寸精度应从严控制。
②支座按螺栓孔中心线要求,预先点焊于一环形底板上,再上立车找正,按样板所划出的相贯线进行加工,此法可比较准确地控制装配间隙,从而使支座安装质量也易保证。
大多数工厂对筋板进行放样后手工切割,此时,在相贯线部位应留出余量,以便组装时再进行切割修正。其安装步骤如下:
a.下封头环缝坡口制备后置于平台上,用角尺从封头直边处对称找出封头中心部位的4~8点,再从中定出封头中心点。
b.参照下封头开孔及拼缝的相应位置划出四条心线,并核对直边部位环向等分值。对照此心线,按支座分布位置划出支座安装心线及垫板位置线。
c.装配点焊垫板,使其与封头表面贴紧,其间隙不得大于1mm,必要时予以火焰修矫。
d.按照支座底板的螺栓孔周径Db,将支座组装点焊于一环形平板上,核对各相关尺寸。也可直接在平台上按划线位置组装,再用角钢拉筋点焊固定各支座的相对位置。
e.将支座安放于倒扣在平台上的底封头上,使各支座安装高度(图2-68)保持一致,根据筋板相关间隙进行切割修正。切割修正量的大小取决于前面提到的各支座零部件制造的积累误差大小。支座施焊前,应再次核对各安装尺寸。为防止焊接变形,应点焊拉筋固定,待设备发运前,予以割除。
2.7.4 定位焊要求
在压力容器制造过程中,为控制所组装的零部件的几何形状与相关尺寸,通常采用手工(或半自动)定位焊来固定。定位焊可以在焊道外的母材上进行,如需对组装焊缝的错边进行调正定位或防变形而点焊的拉筋板、定位板等。也可以直接在焊缝坡口内定位焊。由于定位焊经常伴随着多种焊接缺陷,所以当需要在承压焊缝的坡口内实施定位焊固定,应考虑在焊缝清根时可否将此定位焊彻底清除干净,否则对此类的定位焊应严加控制。对于高强钢材质,应避免在焊道内实施定位焊。