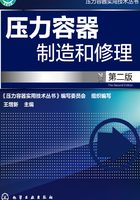
2.5 机械加工与坡口制备
2.5.1 焊接坡口加工
压力容器承压壳体上的所有A、B类焊缝均为全焊透焊缝,都要进行无损检测。为保证焊缝质量,坡口的制备显得十分重要。坡口形式由焊接工艺确定,而坡口的尺寸精度、表面粗糙度及清洁度取决于加工方法。筒体纵缝通常可采取刨边、铣边,车削加工、火焰切割等工艺手段来制备。壳壁开孔可采用气割(包括行健机器人气割开孔机)、车削、镗、钻等方法。对于筒体上较大的开孔、加工原有的设备已无法满足,现已采用行健机器人进行开孔、坡口的制备。
2.5.1.1 刨边机加工坡口
压力容器壳体焊缝坡口在下列情况下可选择刨边。
①允许冷卷成形的纵环缝、封头坯料拼接;
②不锈钢、有色金属及复合板的纵环缝;
③坡口形式不允许用气割方法制备的或坡口尺寸较精确的,如U形坡口、窄间隙坡口。
④其他不适宜采用热切割方法制备的坡口,如低合金高强度材料等。
采用刨边(或铣边)加工坡口的方式,在我国压力容器行业十分普遍。刨边机加工坡口与金属切削加工一样。刨边机长度一般为3~16m,加工厚度60~160mm。工件可采用气动、液压、螺旋压紧及电动压紧等方式夹持固定。刨边机切削在前进与回程中均可进行,这类刨边机生产率较高。将刨边机刀架改成铣削刀盘就成铣边机了。国外中小型压力容器制造厂已很少采用刨边机加工坡口。绝大部分材料的坡口制备都由火焰切割来完成。
2.5.1.2 立式车床加工坡口
对于大型厚壁、合金钢容器,大多采用热卷、温卷成形,其环缝坡口则可在立车上加工完成。其优点是对各类坡口形式都适宜,钝边直径尺寸精度高;钝边加工直径容易控制,又能保证环缝装配组对准确。封头环缝及顶部中心开孔的坡口也可在立车上加工。国内一些大型锅炉、压力容器厂都配备有5m立车,可加工筒节高度达5m。国外一些大型容器厂一般都配备机械加工中心[18],如德国Schiess工厂的VKE800/1200镗铣机床,可车削高度为7.5m,用动力头进行车削,还可进行镗、铣、钻加工。美国C·E公司的Chattanooga工厂的立式机械加工中心,其车削直径可达11.7m,现在国内立车加工能力已超过之前国外的加工能力。
2.5.1.3 切割坡口
采用火焰切割方法制备坡口,是目前压力容器行业广泛使用的最为经济的手段。切割坡口时,通常是将分离切割与坡口制备合并一步完成的。当在半自动或自动切割机上做双嘴或三嘴切割时,生产率成倍提高。采用双嘴切割V形坡口、三嘴切割X形坡口可一次割成(图2-14、图2-15)。

图2-14 用两个割炬切割V形坡口
1,2—割炬

图2-15 用三个割炬切割X形坡口
1~3—割炬
为进一步提高切割坡口的生产率,除了广泛采用半自动切割并配置高速割嘴外,压力容器制造行业普遍添置自动切割设备。
(1)数控“水刀”切割机
“水刀”是将超高压水射流发生器与二维数控加工平台组合而成的一种平面切割机床。它将水流的压力提升到足够高(200MPa以上),使水流具有极大的动能(水流速度超过2倍声速),在高速水流中混合一定比例的磨料,在二维数控加工平台的引导下,在材料的任意位置开始加工或结束加工,按设定的轨迹以适当的速度移动,实现任意图形的平面切割加工。
(2)数控切割机
利用电子计算机对切割过程进行自动控制,使切割过程更趋便捷。目前国内的大型压力容器厂已广泛采用国产的或引进的数控火焰等离子切割机。数控切割机已替代了繁杂的人工划线、放样等工作,也替代了不太经济的刨边机制备切口的工艺方式。
筒体端面的切割、封头余量切割、筒体人孔等开孔切割、管子端口切割等工序,目前均已有相应的切割设备对其进行半自动切割。割出的坡口经打磨后即可进行组装、焊接。需要特别指出的是,作为压力容器的焊接坡口,当材料为σb≥540MP及Cr-Mo低合金钢,如采用火焰切割方法制备坡口时,应对坡口表面先进行打磨然后做磁粉或渗透检测,加钒钢气割开孔后,应采用机加工方法制备坡口。
2.5.1.4 其他方法加工坡口
(1)封头法向斜插孔坡口加工
此类开孔轴线垂直于封头表面,如果是球形封头,找正、加工都比较方便。通常可采用镗床加工,也可以在加工中心上镗孔,坡口深度是一致的。而椭圆形封头上的斜插孔,尤其在接近过渡区时,坡口深度略有差异,但并不影响加工、焊接。
(2)筒壁侧向开孔坡口加工
薄壁容器的开孔,如人孔等大直径孔,需制作开孔样板,按划线进行手工切割,最好能采用马鞍形切割机作开孔切割[图2-16(a)]。厚壁容器上的小孔可采用镗床钻孔、扩孔。大直径孔需在镗床或加工中心上加工,坡口钝边是一个等高圆柱面,坡口深度是变化的[图2-16(b)]。为了简化孔的加工,此类开孔通常加工成无坡口的直孔,再用手工割出坡口,经修磨后使用。这种加工与气割结合的坡口制备方法也常用于封头,筒壁斜插孔上。

图2-16 筒体侧向开孔坡口
2.5.2 典型零部件的机械加工
2.5.2.1 八角垫的加工
采用八角垫(图2-17)密封形式在加氢反应器上十分普遍,这种密封属于半自紧式密封,在高温、高压腐蚀的工况下,即使压力有波动,密封仍较可靠。垫圈材料一般选用0Cr13、0Cr18Ni9钢锻件。垫卷的加工要点如下。

图2-17 垫片的形式
①控制中径尺寸,趋于正偏差。
②锥角误差要严格把握。
③锥面粗糙度尽量使其光滑一些。
④上下锥面应同轴。加工前先准备一工艺环,将锻环点焊在上面再加工,以避免因车床装卡而变形。在立车上加工过程为:
a.找正夹紧后车上平面及内、外径[控制中径,见图2-18(a)];

图2-18 八角垫加工
b.车上锥面(用样板检查),(见图2-19);

图2-19 八角垫样板
c.切断后将半成品零件压紧于另一工艺环上[另外加工的工艺环,见图2-18(b)];
d.按垫圈高度加工并车锥面(用样板检查)。
小直径八角垫在卧车上加工,可直接用三爪卡盘找正、加工,不需要工艺板。椭圆垫的加工与上述工序相仿,只是样板为圆弧形。
2.5.2.2 梯形槽的加工
加氢反应器的梯形密封槽是在不锈钢堆焊层上加工的。其加工过程比较复杂:
①在法兰初加工坯料上加工堆焊槽(图2-20);

图2-20 梯形槽
②按图样尺寸要求堆焊E309L过渡层,堆焊厚度不小于4mm;
③热处理后加工过渡层,控制厚度3mm,检测;
④法兰、封头、筒节总装、热处理;
⑤堆焊表层E347;
⑥加工密封槽使达到图样要求,检测。
需要注意的是:
a.密封槽底r不得小于0.5mm;
b.表层堆焊、加工后不应再经受热处理;
c.槽的中径需按八角垫配置,按下偏差控制,其好处在预紧密封时使外锥面先压紧,这可提高密封的可靠性。
将顶部法兰、封头、筒节组焊成部件时,梯形槽的最终加工可在5m立车上进行,这使得加工比较方便,但与筒体大段总装后,环缝只能做局部热处理。如先行总装、热处理,表层堆焊是在全位置状态下进行的,而密封面的最终加工只能在加工中心上进行。梯形槽锥面的粗糙度数值应控制在1.6μm以下,而这在大直径梯形槽的镗削加工时是很难达到的,必要时可采取研磨的方法补救。
对加工好的梯形槽进行中径检测有如下方法:
a.用钢球进行中径测量。钢球直径应经挑选后使用。此法在立车上实施比较方便,测量时需两个人配合,将测得的直径减去两个钢球各自的半径即可。
b.采用中径样板测量。根据中径尺寸系列制作中径样板(图2-21)。直接用样板卡在直径处测量,同时对槽形进行检测。此法适用于小直径系列。

图2-21 中径测量样板
h—槽深;b—槽宽;ф—中径
c.在卡尺上装专用测量头(图2-22)。将卡尺一个腿改制后装上测量头进行单腿与外径间距间接测量中径,也可两个腿改制后直接测出中径。

图2-22 中径测量头
h—槽深;b—槽宽
根据梯形槽系列尺寸制作出系列样板,可对梯形槽形状进行检测。
2.5.3 特殊形状零件的加工
高压厚壁容器的侧向开孔通常要采取如图2-23所示的结构形式,目的是使得镶嵌式焊缝接头尽量远离应力集中区。加强接管与壳壁连接处有一马鞍形接盘,通常都是整体锻造的。接盘内弧面与筒节内表面相连接,加工方法比较简单,如采用刨、车等。而坡口及外弧面的加工比较复杂,需在卧式车床上增加一套靠模车削机构。接盘内弧面可当成靠模(图2-24)。其加工工序如下:①在卧车上先加工出接管各圆柱面;②在刨床上刨削内弧面,用圆弧样板检查;③在卧车上找正后装上靠模机构,以内弧面为依托分别加工外弧面,使接盘与筒节连接处厚度S均匀,圆角R处圆滑;④加工内外焊接坡口,用样板检查。马鞍形接管的加工质量取决于该靠模机构是否紧凑、灵活自如,以及机构的制造精度。外弧面及圆角R处虽经加工,但仍需再经修磨,使其外表面过渡圆滑。此类靠模机构目前已有厂家生产。随着数控三维镗床诞生与使用,现已代替了卧式车床加一套靠模车削机构来加工加强接管马鞍形的加工。

图2-23 马鞍形接管

图2-24 马鞍形加工靠模装置