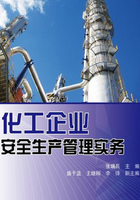
第三节 安全管理主要方法
一、工艺安全管理(PSM)
工艺安全管理又称过程安全管理,是指按《化工企业工艺安全管理实施导则》(AQ/T 3034—2010),通过工艺安全信息、工艺危害分析、操作规程、培训、承包商管理、试生产前安全审查、机械完整性、作业许可、变更管理、应急管理、工艺事故/事件管理、符合性审核工作,确保工艺安全。
二、HAZOP(危险与可操作性)分析
HAZOP分析是一种用于辨识设计缺陷、工艺过程危害及操作性问题的方法。主要是通过分析生产运行过程中工艺状态参数的变动或操作偏差,预见生产过程中存在的主要危险、危害因素,提出应采取的措施。
设计阶段要进行HAZOP分析,在役化工装置每5年必须进行1次HAZOP分析。
三、重大危险源
通过重大危险源辨识、分级、评估、建档、备案、检测、隐患排查和监督管理等工作,建立相对独立的重大危险源安全监督预警系统,确保重大危险源可控、在控。
四、两重点一重大
“两重点一重大”指重点危险工艺、重点监管危险化学品和重大危险源,是化工监管的重点,加强“两重点一重大”的监管能起到事半功倍的作用。
五、特殊危险作业
做好吊装、动火、动土、高处、设备检修、盲板抽堵、受限空间、断路作业、带压(作业)堵漏、现场临时用电等特殊危险作业的各项安全措施,确保检维修作业安全。
六、三查四定
“三查四定”:项目建设中交前的一个过程,是确保单机试车、联动试车、投料试车安全的有效手段。也适用于大检修后的装置交接。
“三查”:查设计漏项、查工程质量及隐患、查未完工程量。
“四定”:定任务、定人员、定时间、定措施。
七、九完五交
“九完五交”是化工工程建设中,在工程中间交接和竣工验收时,必须坚持的原则。
“九完”:①工程按设计文件规定的内容施工完;②工程质量初评合格;③工艺管道、动力管道的耐压试验合格,系统清洗、吹扫、气密合格,保温基本完;④静设备强度试验、无损检测、清扫合格;⑤动设备单机试车合格(需实物料或特殊介质而未试车者除外);⑥大型机组用空气、氮气或其他介质负荷试车合格,机组保护性联锁和报警等自控系统调试联校合格;⑦装置电气、仪表、计算机、防毒、防火防爆等系统调试联校合格;⑧装置区施工临时设施已拆除,工完、料尽、场地清,竖向工程施工完;⑨对联动试车有影响的“三查四定”项目及设计变更处理完,其他未完尾项责任明确,完成时间明确。
“五交”:①按设计内容对工程实物量的核实交接;②工程质量初评资料及有关调试记录的审核验证与交接;③安装专用工具、仪器和剩余随机备件、材料的交接;④工程尾项清理及完成时间的确认;⑤随机技术资料的交接。
八、四不开车
条件不具备不开车,程序不清楚不开车,指挥不在场不开车,出现问题不解决不开车。
九、五想五不干
现场作业要做到:想安全风险,不清楚不干;想安全措施,不完善不干;想安全环境,不合格不干;想安全用品,不配齐不干;想安全确认,不落实不干。
十、五懂五会五能
指企业作业人员应当具备的基本知识、技能和素质。
(1)五懂:懂生产工艺,懂技术原理,懂设备结构,懂危险特性,懂岗位应急。
(2)五会:会生产操作,会异常分析,会设备点检,会风险辨别,会处置险情。
(3)五能:能遵守劳动纪律,能遵守安全纪律,能遵守工艺纪律,能制止他人违章,能抵制违章指挥。
十一、隐患排查治理
按《安全生产事故隐患排查治理暂行规定》和《危险化学品企业事故隐患排查治理实施导则》要求,建立健全企业隐患排查治理制度和管理体系。要全面覆盖、责任到人,采取定期排查与日常管理相结合,专业排查与综合排查相结合,一般排查与重点排查相结合的方式,及时发现、消除各类事故隐患。
十二、安全性评价
安全性评价也称为风险评价,是指对系统存在的危险进行定性或定量分析,提出控制措施。可使宏观管理抓住重点、分类指导,也可为微观管理提供可靠的基础数据。
十三、一证两票三制
(1)一证 作业许可证。
(2)两票 工作票、操作票。
(3)三制 交接班制、巡回检查制、设备定期试验轮换制。
十四、安全生产标准化
是指通过建立安全生产责任制,制定安全管理制度和操作规程,排查治理隐患和监控重大危险源,建立预防机制,规范生产行为,使各生产环节符合有关安全生产法律法规和标准规范的要求,人、机、物、环处于良好的生产状态,并持续改进,不断加强企业安全生产规范化建设。
安全生产标准化达标创建要以创建本质安全型企业为目标,把规范安全生产作为促进安全生产的重要保障。安全生产标准化达标创建要与QHSE体系建设工作有机结合。
十五、技术监控
企业应建立技术监控体系,加强技术监督,确保设备安全可靠。
十六、四个凡事
(1)凡事有章可循。各项工作要有实实在在的制度文件,在工作中都能够找到相关的文件进行指导。
(2)凡事有人负责。安全生产责任要落实到每个环节、每个岗位、每个人,确保每项工作都能够找到明确的负责人。
(3)凡事有人监督。要建立起完善的监督、检查和内控机制,确保各项要求被有效和正确地执行。
(4)凡事有据可查。所做的各项工作和操作都要留下痕迹,可以追溯。
十七、四不放过
事故原因未查清不放过、责任人员未处理不放过、整改措施未落实不放过、有关人员未受到教育不放过。
十八、“8S”管理
推广“8S”管理,现场有序,环境整洁,提高效率,保证安全。其中整理、整顿、清扫、清洁是核心和基础。
(1)整理(SEIRI)。将必要的物品留下来,其他的都清除掉。
目的:防止误用。
(2)整顿(SEITON)。把留下来的必要物品定置摆放并加以标识。
目的:消除寻找物品的时间。
(3)清扫(SEISO)。保持工作场所干净。
目的:稳定品质,减少工业伤害。
(4)清洁(SEIKETSU)。经常保持环境处在美观的状态。
目的:创造明朗现场,维持上面3S成果。
(5)素养(SHITSUKE)。每位成员养成良好的习惯。
目的:培养有好习惯、遵守规则的员工,营造团队精神。
(6)安全(SECURITY)。重视安全教育,遵守安全规程。
目的:建立起安全生产的环境,所有的工作应建立在安全的前提下。
(7)节约(SAVE)。减少企业的人力、成本、空间、时间、库存、物料消耗等因素。
目的:养成降低成本习惯。
(8)学习(STUDY)。营造学习气氛、形成学习风气、养成学习习惯。
目的:使企业得到持续改善,培养学习性组织。
十九、QHSE体系
QHSE体系是指在质量(Quality)、健康(Health)、安全(Safety)和环境(Environment)方面指挥和控制组织的管理体系。通过不断提高员工QHSE意识,纠正不安全行为,从而有效控制过程风险,预防事故发生。