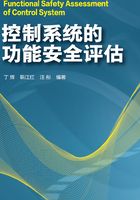
2.2 事故后果分析与评估
事故后果分析就是估计受控系统发生事故所造成的损失。一个完善的事故后果分析应考虑人员伤亡、财产损失、环境破坏以及第三方责任。虽然危险化学品火灾爆炸和泄漏事故的分析结果是其区域和影响(如致伤半径),但是后果分析的结果应该用人员或财产损失的形式来表达。另外,在分析危险事件可能造成的事故后果时,应该以正常的工况和操作背景作为基准,并基于特定危险事件可信的最严重情节进行评估。
事故后果分析所采用的方法取决于若干因素,包括公司与过程和危险相关的经验水平、工程人员估计后果的能力水平、以往事故后果的有效数据等。下面将后果分析方法分为定性、半定量、统计分析和定量等方法,并针对常用的方法给出较为详细的介绍。
2.2.1 定性方法
定性风险分析方法通常都不给出危险事件发生的频率(或概率),而多以危险事件导致的事故后果来定性分级,如预先危险性分析、危险与可操作性分析、失效模式及影响分析。以下将一一给出这些方法较为详细的介绍及其应用示例。虽然安全检查表和假设分析(What-if Analysis)方法也是常用的定性风险分析方法,但它们的分析结果不能明确给出危险事件的后果、防止危险的安全措施以及改进的措施建议,即根据该种分析结果难以确定SIS的SIF以及选择每个SIF的SIL。因此,本书不介绍安全检查表和假设分析(What-if Analysis)方法。
2.2.1.1 预先危险性分析
(1)定义
预先危险性分析(Preliminary Hazard Analysis,PHA)也称初始危险分析,是安全评估常用的一种方法。是在每项生产活动之前,特别是在设计的开始阶段,对系统存在危险类别、出现条件、事故后果等进行概略地分析,尽可能评价出潜在的危险性。
(2)预先危险性分析的主要目的
1)识别危险,确定安全性关键部位;
2)评价各种危险的程度;
3)确定安全性设计准则,提出消除或控制危险的措施。
(3)进行预先危险性分析需要的资料
1)各种设计方案的系统和子系统、部件的设计图纸和资料;
2)在系统预期的寿命期内,系统各组成部分的活动、功能和工作顺序的功能流程图及有关资料;
3)在预期的试验、制造、储存、修理、使用等活动中与安全要求有关的背景材料。
(4)分析步骤
1)危害辨识。通过经验判断、技术诊断等方法,查找系统中存在的危险、有害因素。
2)确定可能事故类型。根据过去的经验教训,分析危险、有害因素对系统的影响,分析事故的可能类型。
3)针对已确定的危险、有害因素,制定预先危险性分析表。
4)确定危险、有害因素的危害等级,按危害等级排定次序,以便按计划处理。
5)制定预防事故发生的安全对策措施。
(5)预先危险性分析的等级划分
为了评判危险、有害因素的危害等级以及它们对系统破坏性的影响大小,预先危险性分析法给出了各类危险性的划分标准。该法将危险性的划分4个等级:
1)安全的。不会造成人员伤亡及系统损坏。
2)临界的。处于事故的边缘状态,暂时还不至于造成人员伤亡。
3)危险的。会造成人员伤亡和系统损坏,要立即采取防范措施。
4)灾难性的。造成人员重大伤亡及系统严重破坏的灾难性事故,必须予以果断排除并进行重点防范。
(6)预先危险分析注意事项
在进行PHA分析时,应注意的几个要点。
1)应考虑生产工艺的特点,列出其危险性和状态:①原料、中间产品、衍生产品和成品的危害特性;②作业环境;③设备、设施和装置;④操作过程;⑤各系统之间的联系;⑥各单元之间的联系;⑦消防和其他安全设施。
2)PHA分析过程中应考虑的因素:①危险设备和物料,如燃料、高反应活性物质、有毒物质、爆炸高压系统、其他储运系统;②设备与物料之间与安全有关的隔离装置,如物料的相互作用、火灾和爆炸的产生和发展、控制和停车系统;③影响设备与物料的环境因素,如地震、洪水、振动、静电、湿度等;④操作、测试、维修以及紧急处置规定;⑤辅助设施,如储槽、测试设备等;⑥与安全有关的设施设备,如调节系统、备用设备等。
(7)预先危险分析的优、缺点及使用范围
1)预先危险性分析是进一步进行危险分析的先导,是一种宏观概略定性分析方法。其特点是把分析工作做在行动之前,避免由于考虑不周而造成损失。在项目发展初期使用PHA有以下优点:①方法简单易行、经济、有效;②能为项目开发组分析和设计提供指南;③能识别可能的危险,用很少的费用、时间就可以实现改进。
2)适用范围:预先危险性分析适用于固有系统中采取新的工艺方法,采用新的物料、设备和设施检修后开车,制定操作规程、技术改造之后的危险性评价。该法一般在项目的发展初期使用。当只希望进行粗略的危险和潜在事故情况分析时,也可以用PHA对已建成的装置进行分析。
(8)应用示例
热水器用煤气加热,装有温度、煤气开关联装锁置。当水温超过规定温度时,联锁装置将调节煤气阀的开度。热水器结构示意图如图2.1所示。

图2.1 热水器结构示意图
如果发生失效,导致压力过高时,则由泄压安全阀放出热水,防止发生事故。预先危险分析结果如表2.1所示。
表2.1 燃气热水器预先危险性分析

2.2.1.2 危险与可操作性分析
(1)起源
危险与可操作性分析(Hazardand Operability Studies)又称为HAZOP。是英国帝国化学工业公司(ICI)蒙德分部于20世纪60年代发展起来的以引导词(Guide Words)为核心的系统危险分析方法,已经有50年应用历史。
(2)概述
危险与可操作性分析是过程工业最常用的过程危险(安全)分析(Process Hazard Analysis,PHA)方法,是一种形式结构化的方法。该方法全面、系统地研究系统中每一个设备或装置的重要参数偏离了指定的设计条件所导致的危险和可操作性问题。主要通过研究工艺管线和仪表图(P&ID)、带控制点的工艺流程图或工厂的仿真模型来确定,应重点分析由管路和每一个设备操作所引发潜在事故的影响,应选择相关的参数,例如:流量、温度、压力和时间,然后检查每一个参数偏离设计条件的影响。采用经过挑选的关键词表,例如“大于”、“小于”、“部分”等,来描述每一个潜在的偏离。最终应识别出所有的失效原因,得出当前的安全保护装置和安全措施。所做的评估结论包括非正常原因、不利后果和所要求的安全措施及建议。
(3)HAZOP分析法简介
1)HAZOP分析的适用范围
①HAZOP分析即适用于设计阶段,又适用于现有的生产装置。根据全生命周期理念,过程工业应每两年进行一次HAZOP分析评价。
②HAZOP分析可以应用于连续的化工过程,也可以应用于间歇的化工过程。
2)HAZOP分析方法的特点
①从生产系统中的工艺参数出发来研究系统中的偏差,运用启发性引导词来研究因温度、压力、流量等状态参数的变动可能引起的各种失效的原因、存在的危险以及采取的对策。
②HAZOP分析所研究的状态参数正是操作人员控制的生产工艺指标,针对性强,利于提高安全操作能力。
③HAZOP分析结果既可用于设计的评价,又可用于操作评价;即可用来编制、完善安全规程,又可作为可操作的安全教育材料。
④HAZOP分析方法易于掌握,使用引导词进行分析,既可扩大思路,又可避免漫无边际地提出问题。
3)HAZOP的理论依据
工艺流程的状态参数(如温度、压力、流量等)一旦与设计规定的基准状态发生偏离,就会发生问题或出现危险。
4)术语
①节点:便于分析具有共同设计意图的部分系统。
②设计意图:工艺流程的设计思路、目的和设计运行状态。
③参数:工艺流程操作变量参数,例如温度、压力。
④引导词:用于和参数结合创造偏差的一组词,如多、少、部分。
⑤偏差:流程偏离设计意图的状态。
⑥原因:导致偏差的可能起因。
⑦后果:偏差所能引起的损失,包括人员伤亡、财产损失或其他可能的安全后果。
⑧保护措施:能减少危害事件发生概率或减轻危害事件后果危害程度的工程设计或管理程序(现有的)。
⑨建议措施:在设计或操作程序方面的改进建议,以降低危害事件发生的概率或后果的严重程度,以达到控制风险水平的目的。
5)引导词
引导词及其定义见表2.2。
表2.2 引导词及其定义

6)确定节点的原则
①节点范围不能过粗。
②节点范围不能过细。
③管线节点:物料流动通过且不发生组分和相态变化的、具有共同设计意图的一件或多件工艺设备(如过滤器、泵等)。
④容器节点:储存、反应或处理物料的容器,在其中材料可发生或不发生物理/化学变化。
7)节点分析
①确认节点的设计意图;
②列出重要参数和引导词;
③确定偏差并记录;
④确定偏差的后果;
⑤分析偏差的原因;
⑥列出现有保护措施;
⑦若现有保护措施不充分,制定改进措施建议。
(4)应用领域
HAZOP分析方法特别适合化工、石油化工等生产装置,对处于设计、运行、停用等各阶段的全过程进行危险分析,既适合连续过程也适合间歇过程。近年来,应用范围扩大至可编程电子系统;道路、铁路等运输系统;检查操作顺序和规程;评价工业管理规程;评价特殊系统,如航空、航天、核能、军事设施、火炸药生产和应用系统等;医疗设备;突发事件分析;软件和信息系统危险分析。
(5)应用示例
假设一个简单的过程工业生产过程,如图2.2所示。物料A和物料B通过泵连续地从各自的供料罐输送至反应器,在反应器中合成并生成产品C。假定为了避免爆炸危险,在反应器中A总是多于B。完整的设计描述将包括很多其他细节,如:压力影响、反应过程和反应物的温度、搅拌、反应时间、泵A和泵B的匹配性等,但为简化示例,忽略这些因素。工艺流程中的分析节点用粗线条表示。

图2.2 简化流程
节点是从物料A供料罐到反应器之间的管道,包括泵A。这个节点的设计目的是连续地把物料A从罐中输送到反应器,且物料A的流速应大于物料B。
“物料”和“活动”要素的HAZOP输出例子见表2.3。仅记录了有意义的偏离。
表2.3 某化工工艺的HAZOP工作表

2.2.1.3 失效模式及影响分析
(1)定义
失效模式及影响分析(Failure Modeand Effect Analysis,FMEA)是由可靠性工程发展起来的,主要分析系统、产品的可靠性和安全性。其基本内容是对系统或产品各个组成部分,按一定顺序进行系统分析和考察,查出系统中各子系统或元件可能发生的各种失效模式,并分析它们对系统或产品的功能造成的影响,提出可能采取的预防改进措施,以提高系统或产品的可靠性和安全性。
(2)方法特点
①失效模式及影响分析是通过原因来分析系统故障(结果)。即用系统工程方法,从元件(或组件)的失效开始,由下向上逐次分析其可能发生的问题,预测整个系统的失效,利用表格形式,找出不希望的初始原因事件。
②失效模式及影响分析除了考虑系统中各组成部分上、下级的层次概念,如物理、空间、时间关系外,还主要考虑功能关系。从可靠性角度看,则侧重于建立上级和下级的逻辑关系。因此,失效模式及影响分析是以功能为中心,以逻辑推理为重点的分析方法。
③该方法是一种定性分析方法,不需要数据作为预测依据,只要理论知识和过去失效的经验积累即可,因此便于掌握。当个人知识不够,可采用集思广益的办法进行分析。
④该方法一般用于考虑非危险性失效,费时较多,而且一般不能考虑人、环境和部件之间相互关系等因素。适用于产品设计、工艺设计、装备设计和预防维修等环节。
(3)目的和要求
①搞清楚系统或产品的所有失效模式及其对系统或产品功能以及对人、环境的影响;
②对有可能发生的失效模式,提出可行的控制方法和手段;
③在系统或产品设计审查时,找出系统或产品中薄弱环节和潜在缺陷,并提出改进设计意见,或定出应加强研究的项目,以提高设计质量,降低失效率,或减少损失;
④必要时对产品供应列入特殊要求,包括设计、性能、可靠性、安全性或质量保证的要求;
⑤对于由协作厂提供的部件以及对于应当加强试验的若干参数需要制定严格的验收标准;
⑥明确提出在何处应制定特殊的规程和安全措施,或设置保护性设备、监测装置或报警系统;
⑦为系统安全分析、预防维修提供有用的资料。
(4)分析步骤
①将系统分成子系统,以便处理。
②审查系统和各子系统的工作原理图、示意图、草图,查明它们之间及元件、组件之间的关系。这项工作可通过编制和使用可靠性框图来完成。
③编制每个待分析的子系统的全部零件表,每个零件的特有功能同时列入。确定操作和环境对系统的作用。
④分析工程图和工作原理图,查出元件发生的主要失效机理。
⑤查明每个元件的失效类型对子系统的失效影响。1个元件有1个以上的失效类型时,必须分析每一类型失效的影响并分别列出。根据失效影响大小确定危险严重度。严重度等级一般分为4个等级,见表2.4。
表2.4 严重度等级分类

⑥列出失效模式的失效率。失效率一般为常数,记为λ。失效模式的失效率一般亦分为4级,见表2.5。
表2.5 失效率等级

注:勿将失效模式的失效率误当作系统发生失效的频率或概率。
⑦列出排除或控制危险的措施。如果失效会引起受伤或死亡,要说明提供的安全装置。
元件分解到什么程度是需要注意的问题,要根据危险分析的目的加以确定。一般认为分析的对象有确定的失效率并能得到它时就可以了,不必再详细分解。例如,生产中的电动机,它的失效率是可以得到的,就没有必要再对它的零件进行分析了。如果这部机器的失效率很高,可以进一步分析各种零件的失效类型、影响及失效率,以确定哪个零件需要加以改进。
(5)适用范围
1957年,FMEA用于飞机发动机的危险分析。后来,美国国家航空和航天管理局、陆军在签订合同时都要求实施FMEA。现在FMEA在原子能工业、电气工业、仪表工业都有广泛的应用,在化学工业应用也有明显的效果,如美国杜邦公司就将其作为化工装置三阶段安全评价中的一个环节。
失效模式及影响分析还常常与故障树配合使用,来确定故障树的顶上事件。
(6)应用举例
空气压缩机储罐失效模式及影响分析。空气压缩机储罐属于压力容器,其功能是储存空气压缩机产生的压缩空气。这里仅考察储罐的罐体和安全阀两个部件,分析结果列于表2.6。
表2.6 压缩空气储罐的失效模式及影响分析

2.2.2 半定量方法
本小节仅讨论事故后果的半定量评估方法。常用的方法有美国道化学公司(Dow)的“火灾、爆炸危险指数评价法”、英国帝国化学工业公司蒙德部的“ICI/Mond火灾、爆炸、毒性指标法”、日本劳动省的“六阶段法”、“单元危险指数快速排序法”等,它们均是以物质系数为基础,采取综合评价的危险度分级方法。虽然在许多有关评价方法的书中均把它们归为定量评价方法,但是,由于这些方法并非完全基于数据定量计算得出事故后果,而是通过人工取值计算出无量纲的危险度分值或系统火灾、爆炸危险指数,因此,本书认为将这些方法归为“事故后果的半定量评价方法”更为准确。
当然还有许多其他半定量评价方法,但它们不只针对事故后果,而是针对系统的整体风险,即评价结果是系统的整体风险大小。例如基于对事物的经验、知识、观察和归纳统计的经验评价方法:LEC(格雷厄姆-金尼法)、机械工厂安全评价法等;以模糊数学和矩阵理论为基础的定量分析方法:模糊数学综合评判法、层次分析法等。本书均不给予介绍。
下面对道化学公司火灾、爆炸危险指数法给予较为详细的介绍,并在此基础上简单介绍ICI蒙德法,最后通过应用示例比较这两种方法。
2.2.2.1 道化学公司火灾、爆炸危险指数评价法
道化学公司火灾、爆炸危险指数评价法(简称道化法)是对工艺装置及所含物料的潜在火灾、爆炸和反应性危险按逐步推算的方法进行客观的评价。火灾爆炸危险指数评价法以道(Dow)氏火灾爆炸危险指数法第七版为基础,该方法用于确定工艺过程中的最大潜在危险性,并预测导致事故后果的危险程度。具体过程如下。
(1)评价单元的确定
①单元的划分 火灾爆炸危险指数法用于进行化工工艺危险性评价时,首先要选定研究对象,对整个生产区域,可将其划分成在事故中相对独立的单元。
②评价单元的确定 大多数生产单元都包括许多工艺单元,但在计算火灾、爆炸指数时,只评价那些从损失预防角度来看对工艺有影响的工艺单元,这些单元称之为恰当工艺单元,简称工艺单元。
③评价状态的确定 在分析研究生产过程的基础上并与现场人员讨论后,对每个评价单元确定其各自最危险的状态,即评价状态。
(2)单元评价内容
单元工艺的危险性由单元中的危险物质的性质、单元中的一般工艺危险性和单元中特殊工艺危险性来决定。
①确定物质系数 物质系数(Material Factor,简称MF)是在火灾、爆炸指数的计算和其他危险性评价时的最基础数据,是表述物质在由燃烧或其他化学反应引起的火灾、爆炸中所释放能量大小的内在特性,其值越大表示火灾危险性越大。物质越不稳定,潜在的能量越大。
物质系数MF是由NF和NR决定的。NF和NR是由美国消防协会规定的参数值,分别代表物质的燃烧性和化学活性(或不稳定性)。
②一般工艺危险性 一般工艺危险性是确定事故损害大小的主要因素,包括6项内容:
a.放热化学反应;
b.吸热反应;
c.物料处理与输送;
d.封闭单元或密闭单元;
e.通道;
f.排放与泄漏控制。
③特殊工艺危险性 特殊工艺危险性是影响事故发生概率的主要因素,特定的工艺条件是导致火灾、爆炸事故的主要原因,特殊工艺危险有以下12项:
a.毒性物质;
b.负压操作;
c.燃烧范围或附近的操作;
d.粉尘爆炸;
e.低温;
f.释放压力;
g.易燃和不稳定物质的数量;
h.腐蚀;
i.泄漏;
j.明火设备的使用;
k.热油交换系统;
l.转动设备。
④确定火灾、爆炸指数(F&EI) 某单元的火灾、爆炸危险程度由单元中火灾、爆炸危险物质,单元中所采用的一般工艺,特殊工艺三方面决定,综合这三者可得到此单元的火灾、爆炸指数,见表2.7。
表2.7 危险程度等级

⑤计算火灾、爆炸指数(F&EI) 火灾、爆炸指数用来估计生产过程中事故可能造成的破坏程度,该指数是单元工艺危险系数(F3)和物质系数的乘积,即F&EI=F3×MF。
⑥确定安全措施的补偿系数
a.工艺控制安全补偿系数(C1);
b.物质隔离安全补偿系数(C2);
c.防火措施补偿系数(C3);
d.安全措施补偿系数C。
安全措施补偿系数由工艺控制安全补偿系数C1、物质隔离安全补偿系数C2和防火措施补偿系数C3的乘积给出,即:
C=C1×C2×C3 (2.1)
⑦确定补偿后火灾、爆炸指数 采取安全补偿措施后,评价单元的火灾、爆炸指数为:F&EI×C。
⑧暴露区域 暴露区域是指当单元内发生火灾、爆炸事故时,可能影响的区域。按照道化学公司给出的计算模型,暴露区域半径R为:
R=0.256F&EI(m) (2.2)
暴露区域的面积S为:
S=πR2(m2) (2.3)
即为:
S=0.20588(F&EI)2 (2.4)
⑨财产损失
基本可能最大财产损失(Base MPPD)=暴露区域内财产损失×DF(由单元工艺危险系数F3和物质系数MF查“单元危害系统计算图”得到) (2.5)
实际最大可能财产损失(Actual MPPD)=基本可能最大财产损失(Base MPPD)×C(安全措施补偿系数) (2.6)
最大可能工作日损失(MPDO):根据实际最大可能财产损失(Actual MPPD)查“最大可能停工天数计算图”得到。
式中,VPM为每月产值;0.7代表固定成本和利润。
2.2.2.2 ICI蒙德法
石油化工等过程工业的生产操作物料不仅易燃易爆,还往往具有毒性,因此,事故后果应包括火灾爆炸和毒物危害。ICI公司蒙德法是在美国道化学公司(Dow)火灾、爆炸危险指数评价法的基础上,发展了某些补偿系数,引进了毒性指标,使评价结果更加切合实际。这里不再详细介绍ICI公司蒙德法。
2.2.2.3 道化法和ICI蒙德法应用比较
以下将通过示例探讨道化法(七版)和蒙德法对评价结果的影响,并得出合理选取两种评价方法的依据。
(1)评价单元的主要参数
①评价单元:煤气车间的煤气发生系统(煤气发生炉、集气罐)。
②评价单元主要物质:CO。
③煤气发生炉内煤气量:492kg。
④煤气发生炉内压力:700~800Pa。
⑤煤气发生炉内温度:800℃。
⑥评价单元高度:15m。
⑦评价单元作业区域:1200m3。
(2)两种安全评价方法的计算结果
运用道化法(七版)和蒙德法的有关规定、计算图表、公式和方法、对煤气发生系统(主要物料为CO)进行安全评价计算,具体结果见表2.8~表2.10。
表2.8 道化法(七版)和蒙德法的计算结果一览表

注:道化法(七版)评价的A1表示影响区域内的总价值。
表2.9 安全措施补偿前后危险等级对照(道化七版)

表2.10 安全措施补偿前后各项安全指标对照(蒙德法)

(3)结果分析
从表2.8~表2.10的计算结果可以看出:
①对同一评价单元,道化法的评价结论是:未补偿前F&EI为155.61,危险程度属“很大”的级别。而蒙德法的结果是:火灾负荷F为17.8,属“轻”的范畴,爆炸指标E为6.3,属“非常高”范畴,气体爆炸指标A为155.2,属“高”范畴。显然,这两种评价方法在反映评价单元的火灾爆炸危险方面的情况是基本接近的,都反映出该评价单元的火灾爆炸危险级别属于一个较高的水平。
当进行了补偿之后,道化法的结论是:F&EI下降为“较轻”危险级别;而蒙德法的结论,也降至F为“轻”,E为“中等”,A为“中等”的范畴。
由此可见,道化法与蒙德法在对某一具体的评价单元进行火灾、爆炸方面的危险程度评价时,其结果基本上是接近的。
②在评价指标参数方面,蒙德法反映的指标包括了单元毒性指标U和主毒性事故指标C的影响,并且作为主要的评价指标单独列出,突出了毒性对评价单元的影响。
③道化法考虑了评价单元发生火灾爆炸时的影响区域和最大可能财产损失、最大可能工作日损失和停产损失,侧重于评估评价单元一旦发生火灾爆炸事故时可能产生的危害、范围和造成的后果。
④根据评价单元的各种各样的情况,道化法从物质系数、一般工艺危险系数和特殊工艺危险系数3个方面考虑对评价单元可能造成的影响,涉及范围达19种情况;而蒙德法却从物质系数、特殊物质危险性、一般工艺危险性、特殊工艺危险性、布置上的危险性、毒性的危险性6个方面进行考虑,涉及的范围达42种情况。
在补偿措施方面,道化法考虑了工艺控制、物质隔离、防火措施3个方面,涉及的内容有22种情况;而蒙德法则从容器危险性、工程管理、安全态度、防火、物质隔离、灭火活动6个方面进行考虑,涉及的内容有32种情况。
显然,蒙德法在考虑火灾、爆炸、毒性危险方面的影响范围以及在考虑安全补偿措施方面都较道化法(七版)更为全面。
⑤在安全措施补偿方面,蒙德法强调了工程管理和安全态度,突出了企业管理的重要性。
(4)两种方法选择建议
①评价单元的主要物料具有毒物质,且对毒物危害要求有具体的评价指标时,应考虑选用蒙德法进行评价。
②如评价要求对火灾、爆炸危险发生后的影响范围、最大可能财产损失、最大可能工作日损失和停产损失等有具体的反映时,可考虑选用道化法进行评价。
③如要求对评价单元的火灾、爆炸、毒性危险因素指标有更全面的反映时,宜采用蒙德法。
④在进行项目预评价时,由于整个项目仍处于初步设计阶段,很多的参数处于待定的状态,此时采用道化法进行安全评价会更合适。
2.2.3 重大事故后果分析与定量预测
由于设备损坏或操作失误引起泄漏从而大量释放易燃易爆、有毒有害物质。可能会导致火灾、爆炸、中毒等重大事故发生。事故后果分析与定量预测是安全风险分析与评估的一个重要组成部分,其目的在于定量地描述一个可能发生的重大事故对工厂、厂内职工、厂外居民,甚至对环境造成危害的严重程度,为企业决策者和设计者采取何种防护措施提供决策依据,如压力保护安全仪表系统等,以达到减轻事故影响的目的。
需要指出的是,重大事故后果定量预测的数学模型通常是在系列的假设前提下按理想的情况建立的,有些模型经过小型试验的验证,有的则可能与实际情况有较大出入,但对事故后果定量评估来说是可以参考的。
2.2.3.1 物质泄漏后果分析与定量预测
根据各种设备泄漏情况分析,可将工厂(特别是化工厂)中易发生泄漏的设备分类,通常归纳为:管道、挠性连接器、过滤器、阀门、压力容器或反应器、泵、压缩机、储罐、加压或冷冻气体容器及火炬燃烧装置或放散管等。
一旦泄漏,后果不但与物质的数量、易燃性、毒性有关,而且与泄漏物质的相态、压力、温度等状态有关。这些状态可有多种不同的组合,在后果分析中,常见的可能组合有4种:常压液体;加压液化气体;低温液化气体;加压气体。泄漏物质的物性不同,其泄漏后果也不同。
(1)可燃气体泄漏
可燃气体泄漏后与空气混合达到燃烧极限时,遇到引火源就会发生燃烧或爆炸。泄漏后起火的时间不同,泄漏后果也不相同。
①立即起火。可燃气体从容器中往外泄出时立即被点燃,发生扩散燃烧,产生喷射状火焰或形成火球,它能迅速地危及泄漏现场,但很少会影响到厂区的外部。
②滞后起火。可燃气体泄出后与空气混合形成可燃蒸气云团,并随风飘移,遇火源发生爆燃或爆炸,能引起较大范围的破坏。
(2)有毒气体泄漏
有毒气体泄漏后形成云团在空气中扩散,有毒气体的浓密云团将笼罩很大的空间,影响范围大。
(3)液体泄漏
一般情况下,泄漏的液体在空气中蒸发而生成气体,泄漏后果与液体的性质和储存条件(温度、压力)有关。
①常温常压下液体泄漏。这种液体泄漏后聚集在防液堤内或地势低洼处形成液池,液体由于地表面风的对流而缓慢蒸发,若遇引火源就会发生火灾。
②加压液化气体泄漏。一些液体泄漏时将瞬时蒸发,剩下的液体将形成一个液池,吸收周围的热量继续蒸发。液体瞬时蒸发的比例决定于物质的性质及环境温度。有些泄漏物可能在泄漏过程中全部蒸发。
③低温液体泄漏。这种液体泄漏时将形成液池,吸收周围热量蒸发,蒸发量低于加压液化气体的泄漏量,高于常温常压下液体泄漏量。
无论是气体泄漏还是液体泄漏、泄漏量都是决定泄漏后果严重程度的主要因素,而泄漏量又与泄漏时间的长短有关。泄漏量的定量计算参见附录1。
易燃、易爆的气体、液体泄漏后遇到引火源就会被点燃,火灾模型有池火、喷射火、火球和固体火灾四种,附录2将分别讲述它们的事故后果定量计算过程。
爆炸事故模型主要有3种:物理爆炸;凝聚相含能材料爆炸伤害模型;蒸气云爆炸模型,详见附录3。
毒物泄漏后果数学描述有三种:有毒液化气体容器破裂时的毒害区、有毒介质喷射泄漏时的毒害区以及有毒气体泄漏扩散模型,详见附录4。
2.2.3.2 典型重大事故后果定量预测实例
本小节分别给出了化学性火灾爆炸和物理性爆炸的重大事故后果定量预测的典型应用实例。
(1)苯泄漏后扩散速度以及扩散范围、毒害影响
某项目的苯储罐直径为17m,高度为15.4m,容积为3000m3。假设裂口为圆形且发生在储罐底部,泄漏面积为0.001m2。
1)泄漏速度及泄漏量的计算由附表1.1,液体泄漏系数取0.65,苯的密度为880kg/m3,储罐为内浮顶式,压力为常压,液体泄漏速度可用流体力学的伯努利方程计算,其泄漏速度为:
假设泄漏时间为10min,则泄漏的苯的质量为9.95×60×10=5970(kg)。
2)挥发后的总体积苯类物质是挥发性物质,其挥发后的总体积为:
V=22.4ρV液/M
式中 V——挥发后的总体积,m3;
ρ——液体密度,kg/m3;
V液——液体体积,在此V液=m/ρ=5970/880=6.78(m3);
M——泄漏物质的相对分子质量,kg/mol。
将各项数据代入式中,泄漏后的苯全部汽化后的总体积为1714.5m3。
3)最大中毒扩散体积根据我国《工作场所有害因素职业接触限值》(GBZ2.1—2007)得知苯在空气中时间加权平均容许浓度C为6mg/m3;慢性中毒浓度为80mg/m3;血液低中毒浓度为200mg/m3。
苯泄漏后达到时间加权平均容许浓度6mg/m3的中毒区域体积为:
V1=ρV/C=106×880×6.78/6=9.94×108(m3)
苯泄漏后最大可造成的慢性中毒浓度为80mg/m3的中毒区域体积为:
V2=ρV/C=106×880×6.78/80=0.75×108(m3)
苯泄漏后最大可造成的血液低中毒浓度为200mg/m3的中毒区域体积为:
V3=ρV/C=106×880×6.78/200=0.3×108(m3)
4)液态气体扩散半径模拟计算苯挥发后迅速扩散,其气体重于空气,沿地面能扩散到相当远的地方,可模拟为高h=100m的圆形球冠。其体积与球体半径的关系为:
V=πr2h/3+2πrh2/3-πh3/3
分别将V1=9.94×108m3、V2=0.75×108m3、V3=0.3×108m3、h=100m代入上式,可以得到球体半径r分别为:
r1=2965m,r2=768m,r3=461m
扩散半径为:
Rk=[r2-(r-h)2]1/2
由上式可得在三种不同浓度下苯的扩散半径分别为:
Rk1=765m,Rk2=380m,Rk3=288m
从计算结果可知,当6.78m3的苯泄漏后,扩散高度为100m时,达到时间加权平均容许浓度6mg/m3的中毒区域最大半径为765m;可造成的慢性中毒浓度为80mg/m3的中毒区域最大半径为380m;可造成的血液低中毒浓度为200mg/m3的中毒区域最大半径为288m。
根据事故后果模拟计算结果,在极端事故状态下,苯大量泄漏后扩散可造成半径为380m的区域范围内人员发生慢性中毒事故;可造成半径为288m的区域范围内人员发生低浓度中毒事故。在380m的范围内,不应有居民区及村庄。
(2)粗苯罐池火灾事故后果预测
某项目的可燃液体粗苯泄漏后流到地面形成液池,遇到火源燃烧而形成池火。本书以罐区的粗苯为对象,计算可能发生的池火灾事故后果的影响范围与程度。
1)查得粗苯的燃烧速度
2)防火堤长161m、宽70m,防火堤面积S=161×70=11270(m2),液池直径,则液池半径为:
3)液池火焰高度
其中,ρ0=1.29kg/m3,g=9.8m/s2。
4)计算总辐射通量
其中,h=82m,r=60m;查表得,苯的燃烧热Hc=41846kJ/kg,效率因子取η=0.2。
5)计算目标点到液池中心距离x:根据附表2.3中所列各种伤害情况下对应的热通量,利用公式反算出目标点到液池中心距离x(单位m)。tc为热传导系数,一般可取值为1,则
,详见表2.11。
表2.11 粗苯储罐区池火灾破坏半径

根据表2.11中的计算结果,距离粗苯储罐区161m处的人员、建(构)筑物基本不受影响。
(3)物理爆炸事故分析与定量计算实例
1)锅炉爆炸机理分析 对于整台锅炉而言,最大的潜在危险是锅炉汽包爆炸,即属于物理性爆炸的“水蒸气爆炸”。锅炉内的主要承压容器为汽包,其内是带压的饱和蒸汽与同压力饱和水并存的状态。一旦汽包超压破裂,则几乎同时发生两个过程:原饱和蒸汽膨胀降压的过程;原饱和水因压力骤降而使其一部分突然汽化的过程。经过这两个过程,将形成大气压力下的汽水混合物。该过程体积瞬时剧烈膨胀,来不及与周围进行热量交换,可看作绝热膨胀过程,并近似按照定熵过程——可逆绝热过程进行分析。
锅炉爆炸可对人体造成伤害,并可对周围设施、设备、建筑物等造成立体性的破坏,伤害或破坏的介质和主要方式是湿热水蒸气和冲击波。锅炉爆炸湿热蒸汽波及范围指的是当锅炉发生爆炸时,温度为100℃的湿热蒸汽所充满的半球形空间的半径,在此半径范围内的人员会受到热伤害。
锅炉爆炸时高速释放出内在的能量,该爆炸能量引起的冲击波对周围的人体和建筑物将造成伤害和破坏,超压越大,伤害和破坏作用就越大。锅炉爆炸时所释放的能量除了很少一部分(约3%~5%)消耗在撕裂钢板,将部分碎片以及与锅炉相连的汽水管道、阀门和本体抛离原地外,其余大部分能量将以冲击波的形式作用于周围环境,造成建筑物的破坏及人员伤亡。
锅炉爆炸引起的冲击波超压是评价锅炉设备事故后果大小的重要指标。因此,首先应定量地计算锅炉爆炸所能释放的能量,再评估锅炉爆炸的破坏能力。通常用TNT当量法来评估锅炉爆炸释放的能量对周围人体和建筑造成破坏的能力。蒸汽锅炉的水汽爆炸能量系数可以查表得出,再已知锅炉汽包的工作压力及其内的饱和蒸汽和饱和水体积(通常认为锅炉汽包内汽水各半),就可计算出锅炉爆炸能量。求出锅炉的爆炸能量后,再根据TNT的热爆值,将锅炉爆炸的能量折合成用TNT当量表示的爆炸能力。
2)锅炉物理性爆炸后果预测 某热电分厂自备电站2台锅炉的型号均为HG1025/17.5-MQ20-13,为亚临界、单汽包锅炉,其物理性爆炸后果的主要计算参数有:
出口额定蒸汽压力:p=17.5MPa
汽包水容积:V=48m3
以下对锅炉汽包水蒸气爆炸所释放的能量以及用TNT当量衡量的爆炸能力进行计算。
锅炉额定工作压力(表压):p=17.5MPa
锅炉汽包工作压力:pw=p=17.5MPa
锅炉汽包工作压力绝对值:pata=pw+0.1=17.6(MPa)
通常认为汽包内汽水各半,因此
锅炉汽包内饱和水容积:
锅炉汽包内饱和蒸汽容积:
饱和水爆炸能量系数:
饱和蒸汽爆炸能量系数:
锅炉内饱和水总爆炸能量:
锅炉内饱和蒸汽总爆炸能量:
锅炉总爆炸能量:U=U'+U″=7.46×106kJ
TNT热爆值:QTNT=4.23×103kJ/kg
锅炉爆炸能量的TNT当量:
即1台自备电站锅炉发生爆炸,相当于1764kg左右的TNT炸药爆炸。
3)锅炉爆炸危险区域评价
①锅炉爆炸热蒸汽波及范围估算锅炉爆炸热蒸汽波及范围指的是当锅炉发生爆炸时,温度为100℃的湿热蒸汽所充满的半球形空间的半径。在此范围之内的人员将会受到热伤害。锅炉爆炸热蒸汽波及范围的估算如下所示。
饱和水爆炸体积膨胀倍数:n'=391.28
饱和蒸汽爆炸体积膨胀倍数:n″=138.15
饱和水爆炸后汽水混合物总体积:Vw=V'n'=24×391.28=9390.72(m3)
饱和蒸汽爆炸后汽水混合物总体积:Vs=V″n″=24×138.15=3315.64(m3)
爆炸介质总体积:V=Vw+Vs=12706.36m3
爆炸介质半球的半径:
当锅炉爆炸时,半径为18.24m的半球范围内均充满100℃的湿热蒸汽,这些热蒸汽与冲击波伤害一起对人员构成很大的危险。
②冲击波超压致人员伤害区估算根据前面的分析,按冲击波超压致人员死亡和受伤分别估算危害半径。
标准TNT量:q0=1000kg
锅炉爆炸相当TNT量:q=1764kg
爆炸模拟比:
致人死亡的最小冲击波超压:Δpd=0.05MPa
与此超压相应的标准距离:R0d=32.5m
此超压距爆炸中心的距离:Rd=αR0d=1.21×32.5=39.33(m)
即以锅炉为中心,在半径39.33m的范围之内,所有未受到防护的人员都将可能因冲击波超压的作用而死亡。
致人重伤的最小冲击波超压:Δph=0.03MPa
与此超压相应的标准距离:R0h=42.5m
此超压距爆炸中心(锅炉)的距离:Rh=αR0h=1.21×42.5=51.43(m)
即以锅炉为中心,在半径从39.33~51.43m的环形范围之内,所有未受到防护的人员都将因冲击波超压的作用而受重伤。
致人轻伤的最小冲击波超压:Δph=0.02MPa
与此超压相应的标准距离:R0h=56m
此超压距爆炸中心(锅炉)的距离:Rh=αR0h=1.21×56=67.76(m)
即以锅炉为中心,在半径从51.43~67.76m的环形范围之内,所有未受到防护的人员都将因冲击波超压的作用而受轻伤。
③冲击波超压致建筑物及设施破坏区的估算根据前面的分析,按冲击波超压对钢架结构和砖墙结构的建筑物的破坏区进行估算。
可致钢架结构破坏的冲击波超压:Δps=0.20MPa
与此超压相应的标准距离:R0s=17.1m
此超压距爆炸中心的距离:Rs=αR0s=1.21×17.1=20.69(m)
即以锅炉为中心,在半径20.69m的范围之内,钢架结构的构筑物将倒塌。
可致砖墙倒塌的冲击波超压:Δpb=0.07MPa
与此超压相应的标准距离:R0b=27.00m
此超压距爆炸中心的距离:Rb=αR0b=1.21×27.00=32.67(m)
即以锅炉为中心,在半径从20.69~32.67m的环形范围之内,砖墙结构的建筑物将倒塌。