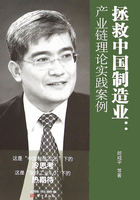
第三节 高效建模
当具备了稳定的材料来源时,我们是不是就能做出一道色香味俱全的生炒肉排呢?明显不是。我们只有在经过无数次的试验后才得出最优的原料组合:肉排切小块,打入鸡蛋后加粟粉拌匀,然后加姜汁1/2茶匙,最后加入葱节、料酒、精盐和胡椒粉腌制15分钟。这个最优组合,我们可以称为最优的肉排原料模型!因此,若把配菜的过程应用到汽车工业里,也就是一个高效的研发优化过程,那么如何将零配件组合成最佳的汽车模型呢?在虚拟制造的基础上采用仿真建模是一个不错的方法,目前已被国外大型的汽车生产商所采用,而虚拟制造本身也成了高效数据积累的良好平台。
一、高效的虚拟制造
首先,我们来了解一下:什么是虚拟制造?虚拟制造是在实际制造前,汽车制造商为了获取最佳的汽车模型数据,运用高性能计算机,模拟开发过程中的设计、测试和改进等环节。具体的实施步骤是:
·首先,研发工程师输入汽车各总成图纸设计参数;
·其次,构建三维模型和整车数据集成;
·然后,各总成三维数据进入超级计算机,超级计算机即时演算虚拟环境,并投影至特殊功能的玻璃墙,其投影精度可以达到毫米以下;
·接下去通过数据线,将投影模型传送至世界各地的研发人员;
·最后,各地研发人员只要戴上特殊眼镜,立即进入虚拟的开发环境。

图5-5 大众虚拟制造的现场示意图
这样一来,不同颜色的喷漆和设备的规格,都可以在短短几秒钟之内呈现出来,并且只要点一下鼠标,就能转换汽车角度,让人们从任何一个可能的视角进行观察。而且,研发团队可以用三维立体的方式模拟任何的内容,包括车内部件、车身强度、动力系统性能、碰撞性能等。
以奥迪Q7车头一个碰撞试验为例,为了模拟汽车碰撞分析,需要100万个数据来支持,计算机可以在150毫秒内计算出结果,为了计算一个车头碰撞的结果,超级计算机需要动用它的8个处理器工作22小时,工作人员以毫米为单位修正,修正后继续重复这个试验。当奥迪Q7的开发已经完成的时候,已经经历了大约2000次准确率达到了90%以上的车头碰撞虚拟试验;相同时间下,如果用真车的话,大概只能做40次。毋庸置疑,虚拟制造和仿真建模大大提高了研发和制造的效率。
二、虚拟制造与传统模式间的差距
为了进一步比较虚拟仿真与传统模式在研发制造中的差距,我们用虚拟仿真系统——DELMIA系统在白车身制造中的应用来说明两者间存在的效率上的差距。在研究过程中,我们留意到,德国大众2007年3月在全球范围内实施虚拟制造商达索(Dassault Systè mes)的虚拟流程管理系统(DELMIA Process Engineer)。这个系统是通过虚拟仿真设计出最优的工艺流程方案,大大提高制造效率。
白车身制造的基本过程就是采用机器人(或者手动加机械手辅助)的手段,传输、抓取、夹持离散的钣金和冲压件并将其焊接成复杂的白车身结构。白车身焊装过程的操作工序繁多,工艺内容复杂,是汽车制造企业最为关心的工艺领域之一,据统计,一个轿车的白车身在焊装过程中要经历3000~5000个点焊步骤,用到100多个大型夹具,500~800个定位器,许多工艺信息都和零部件的三维几何特性密切相关,这给车身焊装工艺参数选择、工艺流程规划、车身焊装的质量控制甚至车身设计都带来很多挑战。如何管理好数以千计的焊点,保证无漏焊、重焊,是白车身工艺规划的难点。
DELMIA的虚拟仿真技术就是通过在白车身制造过程中的八大工序仿真(工位仿真、工装布局仿真、工序分析、焊装仿真、人机仿真、机器人仿真、机构运动仿真和立位工厂仿真)来实现高效率制造的前提。首先,在虚拟系统中建立白车身制造各步骤所需的模型,各模型参数可由实际供应商直接提供,例如焊装线上可供选择的机器人品种多达800种,主要由Fanuc和ABB等一线大厂提供,不同机器人需要的运行参数就由供应厂商提供,然后各工位设计人员通过共享的虚拟开发环境,输入各工位参数在DELMIA系统中仿真运行。假如白车身结果出现偏差,各工位要根据偏差调整参数,然后DELMIA系统重新仿真计算,直至稳定输出为止。最后,每次调整的数据都记录至数据库中,数据库最终给出了最佳的白车身模型。这样一来,只要把最佳模型中参数应用到实际生产中,所有的工艺难题都能迎刃而解。
然而多年以来,在白车身焊装线领域,国内绝大多数整车厂还处在一个很低的技术水平上,相关数据多数还停留在二维的图纸状态,焊装工艺工程师最为主要的工作内容就是Excel填表和截图,工程师难有时间去考虑制造工艺本身的问题,如节拍平衡、生产线布置以及工位仿真等。正因为工艺设计数据和手段依然停留在二维年代,国内制造商难以实现焊点的有效管理,所以为了保证白车身的质量投入大量的人力物力,耗费了大量的时间和资源。同时,因为缺乏统一的管理平台,难以进行精确的焊接过程分析,更不可能打造精确的工厂布局。特别是新车型的生产初期,白车身制造要经过漫长的生产磨合期,这直接影响到新车型的产量和质量稳定性。
当然,白车身制造只是汽车生产的一个环节,假如我们把虚拟制造贯穿到从研发到生产的整个环节,它能给我们带来多大的价值?以新车的设计、制造和测试为例,虚拟仿真只需要两年半就可以实现车身的研发和生产,而传统的二维模式却需要五年之久,这样看来,虚拟制造能大大缩短研发周期。而且它是一个很好的工具,可以直接缩短本土汽车厂和国外汽车厂的差距。事实真的如此吗?
三、无法跨越的虚拟世界
在参观过国外优秀的环境后,本土的汽车制造商们引进了高效的仿真系统,真正的自主品牌似乎离我们不远了。然而,真正高效的仿真还没有我们想得那么简单!超级计算机、华丽的墙体屏幕加上强大的网络虽然可以组建虚拟世界,但是却无法保证完美的汽车模型,因为这并不是仿真研发的核心。真正的研发核心是必须通过不断的重复模拟流程,持续地进行改进来积累汽车模型参数,从而获取最优制造模型参数。
因此,虚拟仿真软件运行的首要前提是要有运行参数,仿真软件的公司并不会提供运行参数,国内汽车生产商由于缺乏参数的积累,根本无法直接运用软件进行开发。因此,虽然奇瑞和吉利等自主品牌企业自2000年来,不断努力向数字化制造靠拢,然而在昂贵的仿真软件面前,却发现没有适合的参数作为自主研发的输入,所以无奈之下他们只能采用逆向研发来实现。
什么是逆向研发?逆向研发是相对于正向研发而言的研发模式,正向研发是先从事基础研究和应用研究取得参数,后进行市场测试和产品推广。而逆向研发正好相反,它通过先购买其他厂商的成熟车型,后通过拆解测量来获得参数。如果我们仍用炒菜的例子作比喻的话,就像身处甲乙两个饭店的厨师A和厨师B,甲饭店厨师A做了一道很好的招牌菜,乙饭店应市场需要,也要提供这样的菜。可是厨师B不会,怎么办?乙饭店派人去甲饭店买其现成的招牌菜,拿给厨师B做研究,得出其原料的构成,估算其配方比例,然后做出类似的招牌菜。通过比较两种研发模式(参见表5-2),逆向研发不但耗时少、投入低而且对市场的反应也快,似乎非常适合国内的汽车生产商。
表5-2 正向研发和逆向研发的比较

事实上,国内生产商早已经采取购买——分解——仿制的逆向研发模式。例如,长城汽车开发精灵轿车时就模仿了菲亚特熊猫,他们在委托上海同济同捷做新的同等定位设计的同时,用熊猫原型车做配套商各部件匹配测试。另外,北京现代开发伊兰特时,也模仿了起亚千里马的外观和参数,他们通过扫描仪把一些零件的形状扫成数据,并且通过三维软件画出数模原型,然后开出模具才实现车型开发(参见表5-3)。
表5-3 新款现代伊兰特和起亚千里马参数对比

而最著名的当属2003年奇瑞QQ和通用Spark之间的故事,所有见过这两款车型的人都承认两者极其相似,因此,更是闹出了一场沸沸扬扬的奇瑞QQ外观抄袭通用五菱Spark的侵权案件。姑且不论是否侵犯知识产权,但从两款车的外观及基本参数对比,我们不难发现逆向工程的痕迹。
表5-4 新款奇瑞QQ和通用Spark参数对比

从历史的角度来看,大小自主品牌的崛起都经历了逆向研发的过程,而且逆向研发的获得数据可以直接输入仿真系统,从而大大节省开发时间,对于在夹缝中生存的新生制造商而言无疑是一条捷径。回顾40年前的日本,20年前的韩国,他们同样是靠逆向研发的过程获得了今天的成就,模仿也罢,抄袭也罢,问题是我们能否像日本韩国一样,通过逆向研发积累大量的模型数据,为今后更高效的正向研发作准备呢?
四、小结
通过以上的论述,我们看到世界汽车的研发已经走进了虚拟的世界。然而虚拟仿真平台容易购买,高效的研发却依然需要依靠自身所积累的扎实的数据经验。逆向工程是一个良好的开端,它可以让本土汽车制造商一步一步地进行积累,但是我们不应永远沉溺于逆向之梦,汽车强国之路的最终目的还是需要一个从无到有的创造,那才是真正属于我们的核心技术。