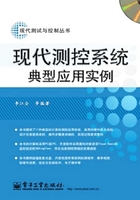
0.2 计算机测控系统的任务和工作原理
1.计算机测控系统的任务
下面以生产过程控制系统为例来说明计算机测控系统的任务,因为它比较集中地体现了计算机测控系统的各种功能。如图0-2所示,计算机测控系统借助传感器从生产过程中收集信息,对生产过程被控对象进行监视并提供控制信号。被收集的信息在不同层次上进行分析计算,得出对生产装置提供的调节量,完成自动控制,或者为生产管理人员、工程师和操作员提供所需要的信息。

图0-2 某生产过程控制系统框图
由此可以看出,计算机测控系统应当完成下列任务:
1)检测
生产过程参数的大小是由传感器进行检测的。传感器产生与被测物理量(如温度、压力、流量、液位等)成比例(一般为正比)的电信号。
传感器信号在进入计算机系统的接口之前,首先要转换成一种标准形式,通常是把传感器的0%~100% 量程转换成4~20 mA电流或1~5 V电压。
另一类测量值是关于被控过程的状态信息。例如,阀门是否关闭?容器是否注满?泵是否打开?这些信息是以开关量的形式提供给计算机的,通过继电器接点的开闭或TTL电平的变化来表示。
计算机也可通过串行或并行通信口直接接收数字量信息。目前,很多传感器都带有微处理器(如智能仪表),可以直接给出数字量信息。
2)控制
对生产装置的控制通常是通过对阀门或伺服机构等执行机构进行调节的,通过对泵和电动机进行控制来达到的。计算机可以产生一串脉冲去驱动执行机构达到所需要的位置,可以通过继电器接点闭合或产生某个电平的跳变去起动或停止某个电动机,也可通过D/A转换产生一个正比于某设定值的电压或电流去驱动执行机构。执行机构在收到控制信号之后,通常还要反馈一个测量信号给计算机,以便检查控制命令是否被执行。
在工业过程控制系统中常用的控制方案有三种类型:直接数字控制、顺序控制和监督控制。大多数生产过程的控制需要其中一种或几种控制方案的组合。
3)人机交互
计算机控制系统必须为操作员提供关于被控过程和控制系统本身运行情况的全部信息,为操作员直观地进行操作提供各种手段,例如改变设定值,手动调节各种执行机构,在发生报警的情况下进行处理等。因此,它应当能显示各种信息和画面,打印各种记录,通过专用键盘对被控过程进行操作等。
此外,计算机控制系统还必须为管理人员和工程师提供各种信息,例如,生产装置每天的工作记录以及历史情况的记录,各种分析报表等,以便掌握生产过程的状况和做出改进生产状况的各种决策。
4)通信
现今的工业过程控制系统一般都采用分级分散式结构,即由多台计算机组成计算机网络,共同完成上述的各种任务。因此,各级计算机之间必须能实时地交换信息。此外,有时生产过程控制系统还需要与其他计算机系统(例如,全厂的综合信息管理系统)进行数据通信。
2.计算机测控系统的工作原理
下面以一个计算机温度测控系统来简要地说明计算机测控系统的工作原理,图0-3为系统组成示意图。

图0-3 计算机温度测控系统
根据工艺要求,该系统要求加热炉的炉温控制在给定的范围内或者按照一定的时间曲线变化。由于存在着各种干扰,使用计算机进行控制,并在显示器上用数字或图形实时地显示温度值。
假设加热炉使用的燃料为重油,并使用调节阀作为执行机构,使用热电偶来测量加热炉炉内的温度。热电偶把检测信号(电势信号)送入温度变送器,将其转换为电压信号(1~),再将该电压信号送入输入装置。输入装置可以是一个模块也可以是一块板卡,它将检测到的信号转换为计算机可以识别的数字信号。计算机软件根据该数字信号按照一定的控制算法进行计算,计算出来的结果通过输出模块转换为可以推动调节阀动作的电流信号(4~20 mA 5V)。通过改变调节阀的阀门开度即可以改变燃料流量的大小,从而达到控制加热炉炉温的目的。与此同时,计算机中的软件还可以将与炉温相对应的数字信号以数值或图形的形式在计算机的显示器屏幕上显示出来。操作人员可以利用计算机的键盘和鼠标输入炉温的设定值,由此实现计算机监控的目的。
上述温度监控计算机系统对生产过程实现自动控制可以分解为四个过程:
(1)生产过程的被控参量(过程信号)通过测量环节转化为相应的电参量或电参数,再由变送器或放大器变换成标准的电压或电流信号;
(2)电压或电流信号经过A/D转换后变成计算机可以识别的数字信号,并将其转换为人们易于理解的工程量(测量值);
(3)计算机根据测量值与给定值的偏差,按一定的控制算法输出控制信号;
(4)控制信号作用于执行机构,通过调节物料流量或能量的大小来实现对生产过程的调节。
以上这四个过程是周期性的。