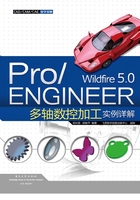
1.4 数控线切割加工基本理论
1.4.1 线切割机床的加工原理
电火花切割加工简称“线切割”,它是利用移动着的细金属丝(铜丝或钼丝)做工具电极,并在金属丝与工件之间通以脉冲电流,利用脉冲放电的电腐蚀作用对工件进行切割加工的。其加工原理见图1-18,电极丝4穿过工件5上预先钻好的小孔,经导轮3由贮丝桶2带动做往复交替移动。工件通过绝缘板7安装在工作台上,由数控装置1按加工程序发出指令,控制两台步进电机11,以驱动工作台在水平面上沿X、Y两个坐标方向移动而合成任意平面曲线轨迹。由高频脉冲发生器8对电极丝与工件施加脉冲电压,喷嘴6将工作液以一定的压力喷向加工区,当脉冲电压击穿电极丝和工件之间的间隙时,两者之间随即产生电火花放电而切割工件,图中9、10分别为液压泵和油箱。

图1-18 线切割机床加工原理
线切割有许多无可比拟的优点,如:线切割具有加工余量小、加工精度高、生产周期短、制造成本低等突出优点,线切割已在生产中获得广泛的应用。电火花线切割加工能正常运行,必须具备下列条件:
(1)钼丝与工件的被加工表面之间必须保持一定间隙,间隙的宽度由工作电压、加工量等加工条件而定。
(2)电火花线切割机床加工时,必须在有一定绝缘性能的液体介质中进行,如煤油、皂化油、去离子水等,要求较高绝缘性是为了利于产生脉冲性的火花放电,液体介质还有排除间隙内电蚀产物和冷却电极作用。钼丝和工件被加工表面之间保持一定间隙,如果间隙过大,极间电压不能击穿极间介质,则不能产生电火花放电;如果间隙过小,则容易形成短路连接,也不能产生电火花放电。
(3)必须采用脉冲电源,即火花放电必须是脉冲性、间歇性的,在脉冲间隔内,使间隙介质消除电离,使下一个脉冲能在两极间击穿放电。
1.4.2 线切割加工特点与应用范围
1.线切割加工特点
线切割加工具有很多优点,发展速度很快,得到广泛的应用,其优点如下。
1)加工精度高
线切割是通过高温熔化或气化局部金属而达到材料的切除,因此,工件和电极之间没有切削力,工件不存在力学变形。线切割采用移动的电极丝进行加工,因此,电极丝在单位长度上的损耗较少,对加工精度的影响也小。线切割加工自动化程度高,可以对影响加工精度的加工参数(脉冲宽度、脉冲间隙、加工电流)进行调节和控制,提高切割精度。
2)加工形状复杂的零件
线切割可以加工其他方法难以加工或根本无法加工的零件,如凸轮、异形槽、冲模等外形复杂的精密零件和狭缝,尺寸精度可达到±0.01mm,表面粗糙度Ra为1.25~2.5μm。
3)材料的利用率高
线切割加工的切缝很窄,只对工件进行轮廓切割加工,实际的金属的腐蚀量很小,材料的利用率高,适合于贵重金属的加工。
2.线切割加工应用
线切割广泛应用于加工各种硬质合金和淬火钢格冲模、样板、各种外形复杂的精细小零件、窄缝等,并可多件叠加起来加工,能获得一致的尺寸。因此,线切割工艺为新产品试制、精密零件和模具的制造开辟了一条新的途径。具体应用如下。
(1)加工各种模具,如凸凹模、粉末冶金。
(2)加工成形工具,如加工带锥度型腔的电极板、微细复杂形状的电极和各种形状的样板、成形刀具。
(3)加工微细孔、槽、窄缝、激光器件等。
(4)各种稀有金属和贵重金属的加工。
(5)加工各种由直线组成的直纹面,如圆锥面、螺旋面及各种二维曲面等。
(6)同时切割凹凸模。利用线切割机的锥度切割功能,可一次加工出达到所需配合间隙的一副冲裁模具。
1.4.3 四轴数控线切割加工原理
图1-19为四轴线切割加工原理图,在NC控制装置的作用下,工作台做X-Y方向的移动,上、下导向器做U-V方向移动,构成四轴联动控制,使电极丝倾斜一定的角度,从而实现锥度切割和上下异形截面形状的加工。

图1-19 四轴数控线切割加工原理
1.4.4 线切割加工工艺内容
利用线切割机床进行加工时,经常会遇到如何解决加工速度与表面粗糙度的矛盾、加工速度的提高与减少电极丝损耗的矛盾及如何避免断丝等。要正确解决这些问题,就必须制定出合理的线切割加工工艺。线切割加工工艺的制定包括以下内容。
1)电极丝
电极丝的粗细影响切割缝隙的宽窄,电极丝直径越细,切缝越小。电极丝直径最小的可达φ0.05mm,但太小时,电极丝强度太低容易折断。一般采用直径为0.1~0.3mm的电极丝。
2)电极丝移动速度
根据电极丝移动速度的大小分为高速走丝线切割和低速走丝线切割。低速走丝线切割的加工质量高,但设备费用、加工成本也高。高速走丝时,线电极采用高强度钼丝,钼丝以8~10m/s的速度做往复运动,加工过程中钼丝可重复使用。低速走丝时,多采用铜丝,电极丝以小于0.2m/s的速度做单方向低速移动,电极丝只能一次性使用。
3)切割起点与切割路线的选择
切割起点是起始切割点,往往也是几何图形的终止点。起点选择不当会使工件切割表面留下痕迹。起始点应尽量选在几何图形的拐角处;起始点应尽量选在工件表面粗糙度值要求高的一侧,且尽可能选在工件切割后容易修磨的表面上。
切割路线的选择主要以防止或减少工件变形为原则,一般应考虑使靠近装夹这一边图形为最后切割为宜。一般情况下,最好将工件与夹持部分分割的线段安排在切割路线的末端。
4)穿丝孔的选择
穿丝孔是工件上为穿过电极丝而预先钻出的小孔。穿丝孔的大小应便于钻孔或镗孔加工,不宜过大或过小,一般在3~10mm范围内取整数值。穿丝孔常用做加工基准,因此,穿丝孔一般在较高精度的机床上进行,或采用电火花穿孔,以保证穿丝孔的位置、尺寸精度。
5)电参数的选择
脉冲宽度越宽加工效率越高,加工越稳定,但表面粗糙度值会增大。反之亦然。因此,根据不同工件的加工要求选择合适的脉冲宽度。
脉冲间隔小,使切割速度提高,但会给排屑带来困难,加工不稳定。脉冲间隔大,使排屑有充裕的时间,使切割速度下降。
放电峰值的选择会影响切割速度和断丝。低速走丝机床峰值电流一般为100~150A,最大达1000A。工件较厚、粗切削时采用较大的放电峰值电流。
空载电压的大小会直接影响到放电间隙的大小,进而引起切割速度和加工精度的变化,对断丝影响也较大。当电极丝直径较小(0.1mm)、切缝较窄,或要减小加工面腰鼓形时,应选较低的空载电压。当要改善拐角的塌角时,应尽量选择较高的空载电压,一般低速走丝机床选150V。