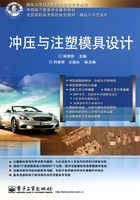
1.2 冲压成型的力学知识
1.2.1 塑性及影响塑性的因素
塑性是指固体材料在外力作用下发生永久变形而不破坏其完整性的能力。材料的塑性是冲压成型的重要依据,冲压成型时希望材料具有良好的塑性。影响金属材料塑性变形的因素主要包括两个方面,一是金属材料本身的化学成分、晶格类型和合金组织等;二是外部条件,如变形温度、变形速度和应力状态等。
1.金属的成分和组织结构
一般情况下纯金属具有最好的塑性,加入其他元素后都对塑性有不利影响。添加的元素可分为杂质元素和合金元素。杂质元素(如Pb、Sn、As、Sb、Bi、S、P)如不溶于金属而以单质或化合物存在于晶界处,使晶间联系削弱,会使塑性显著降低。合金元素的加入往往是为了提高合金的某些性能,但同时对塑性也会产生影响。当合金元素加入后,如能与基体金属形成单相固溶体,特别是面心立方结构的固溶体,一般塑性仍然很好。但当合金含量超过一定值,产生或促进产生了第二相或多相组织,就会对塑性产生不利影响。因此合金元素加入后影响塑性的途径很多,因而有时同一种元素会产生一些对塑性相反的影响。如Mn的加入会促进晶粒长大而使塑性下降,而Mn的硫化物由于熔点较高而使热脆减轻。又如强碳化物形成元素V、Ti、Nb加入后,其碳氮化合物的析出会降低塑性,而由于其又能抑制晶粒长大有利于塑性提高。所以重要的是,需结合具体的合金及变形条件做具体细致的分析。金属的组织结构如晶格类别,杂质的性质、数量及分布,晶粒大小、方向及形状等都会影响金属的塑性。
2.变形温度
金属材料的塑性与变形温度有着非常大的关系,不同的金属在不同的温度条件下所表现出的塑性状态也不一样。就一般金属而言,总的趋势是随温度升高塑性增加,其原因是温度升高会引起原子热振动加剧、位错活动性增大和回复、再结晶加快。
3.应力与应变状态
在变形物体上任意点取一个微量六面单元体,该单元体上的应力状态可取其相互垂直表面上的应力来表示,沿坐标方向可将这些应力分解为9个应力分量,其中包括3个正应力和6个切应力,如图1.2(a)所示。相互垂直平面上的切应力互等,τxy=τyx,τyz=τzy,τzx=τxz。改变坐标方位,这6个应力分量的大小也跟着改变。对任何一种应力状态,总是存在这样一组坐标系,使得单元体各表面上只有正应力而无切应力,如图1.2(b)所示。这3个坐标轴就称为应力主轴,3个坐标轴的方向称为应力主方向,作用面称为应力主平面,其面上的正应力即为主应力。

图1.2 点的应力状态
3个主方向上都有应力存在称为三向应力状态,如宽板弯曲变形。但大多数板料成型工艺,沿料厚方向的应力σt与其他两个互相垂直方向的主应力(如径向应力σr与切向应力σθ)相比较,往往很小,可以忽略不计,如拉深、翻孔和胀形变形等,这种应力状态称为平面应力状态。3个主应力中只有一个有值,称为单向应力状态,如板料的内孔边缘和外形边缘处常常是自由表面,σr、σt为零。
与应力主平面成45°截面上的切应力达到极值,称为主切应力。当σ1≥σ2≥σ3时,最大切应力为τmax=±(σ1-σ3)/2,最大切应力与材料的塑性变形关系很大。
应变也具有与应力相同的表现形式。单元体上的应变也有正应变与切应变,当采用主轴坐标时,单元体6个面上只有3个主应变分量ε1、ε2和ε3,而没有切应变分量。塑性变形时物体主要是发生形状的改变,体积变化很小,可忽略不计,即式(1.1)

为塑性变形体积不变定律。它反映了3个主应变值之间的相互关系。
1.2.2 塑性变形时应力与应变的关系
物体在弹性变形阶段,应力与应变之间的关系是线性的,与加载历史无关。而塑性变形时应力应变关系则是非线性的、不可逆的,应力应变不能简单叠加,图1.3所示为材料单向拉伸时的应力应变曲线。塑性应力与应变增量之间的关系式,即增量理论,其表达式如下:


图1.3 单向拉伸时的应力应变曲线
其中,,式(1.2)可以表达为

如果在加载过程中,所有的应力分量均按同一比例增加,这种状况称为简单加载,在简单加载情况下,应力应变关系得到简化,得出全量理论公式,其表达式为

其中,。
下面举两个简单的利用全量理论分析应力应变关系的例子。
(1)ε2 =0时,称平面应变,由式(1.3b)可得出 ,宽板弯曲属于这种情况。
(2)σ1>0,且σ2=σ3=0时,材料受单向拉应力,由式(1.3b)可得ε1>0,ε2=ε3=ε1,即单向拉伸时拉应力作用方向为伸长变形,其余两方向上的应变为压缩变形,且为拉伸变形之半,翻孔变形材料边缘属此类变形。
1.2.3 金属变形时硬化现象和硬化曲线
大部分冲压生产是在常温下进行的,材料在变形中会产生加工硬化,其结果会引起材料学性能的变化,表现为材料的强度指标(屈服强度σs与抗拉强度σb)随变形程度的增加增加;塑性指标(伸长率δ与断面收缩率ψ)随之降低。加工硬化既有不利的方面,如会进一步变形变得困难;又有有利的方面,板料硬化能够减小过大的局部变形,使变形趋于匀,增大成型极限,同时也提高了材料的强度。因此,在进行变形毛坯内各部分的应力分和各种工艺参数的确定时,必须考虑到加工硬化所产生的影响。
冷变形时材料的变形抗力随变形程度的变化情况可用硬化曲线表示。一般可用单向拉伸或压缩试验方法得到材料的硬化曲线。图1.4所示为几种常用冲压板材的硬化曲线。

图1.4 几种常用冲压板材的硬化曲线
为了使用方便,可将硬化曲线用数学函数式来表示。常用的数学函数的幂次式如下:
σ=Kεn
式中K、n均为材料常数,n称为材料的硬化指数,是表明材料冷变形硬化性能的重要参数,部分冲压板材的n值和K值如表1.2所示。
表1.2 部分冲压板材的n值和K值

1.2.4 各种冲压成型方法的力学特点与分类
正确的板料冲压成型工艺的分类方法,应该能够明确地反映出每一种类型成型工艺的共性,并在此基础上提供可能用共同的观点和方法分析、研究和解决每一类成型工艺中的各种实际问题的条件。在各种冲压成型工艺中,毛坯变形区的应力状态和变形特点是制定工艺过程、设计模具和确定极限变形参数的主要依据,所以只有能够充分地反映出变形毛坯的受力与变形特点的分类方法,才可能真正具有实用的意义。
1.变形毛坯的分区
在冲压成型时,可以把变形毛坯分成变形区和不变形区。不变形区可能是已变形区或是尚未参与变形的待变形区,也可能是在全部冲压过程中都不参与变形的不变形区。当不变形区受力的作用时,叫做传力区。图1.5中列出拉深、翻边、缩口时毛坯的变形区与不变形区的分布情况。

图1.5 冲压变形毛坯各区划分举例
A-变形区;B-传力区
2.变形区的应力与应变特点
从本质上看各种冲压成型过程就是毛坯变形区在力的作用下产生变形的过程,所以毛坯变形区的受力情况和变形特点是决定各种冲压变形性质的主要依据。大多数冲压变形都是平面应力状态。一般在板料表面上不受力或受数值不大的力,所以可以认为在板厚方向上的应力数值为零。使毛坯变形区产生塑性变形均是在板料平面内相互垂直的两个主应力。除弯曲变形外,大多数情况下都可认为这两个主应力在厚度方向上的数值是不变的。因此,可以把冲压变形力按毛坯变形区的受力情况和变形特点从变形力学理论的角度归纳为以下4种情况,并分别研究它们的变形特点。
(1)冲压毛坯受两向拉应力的作用可以分为以下两种情况:
σr>σθ>0,σt=0
σθ>σr>0,σt=0
相对应的变形是平板毛坯的局部胀形、内孔翻边、空心毛坯胀形等(图1.6Ⅰ象限)。

图1.6 冲压应力图
这时由应力应变关系的全量理论可知,最大拉应力方向上的变形一定是伸长变形,应力为零的方向(一般为料厚方向)上的变形一定是压缩变形。因此,可以判断在两向拉应力作用下的变形,会产生材料变薄。在两个拉应力相等(双向等拉应力状态)时,εθ=εr>0, εt=-2εθ=-2εr>0,厚向上的压缩变形是伸长变形的两倍,平板材料胀形时的中心部位就属于这种变形状况。
(2)冲压毛坯受两向压应力的作用分为下面两种情况:
σr<σθ<0,σt=0
σθr<σr<0,σt=0
与此相对应的变形是缩口和窄板弯曲内区(图1.6Ⅲ象限)等。由应力应变关系的全量理论可知,在最小压应力(绝对值最大)方向(缩口的径向、弯曲的周向)上的变形一定是压缩变形,而在没有应力的方向(如缩口厚向、弯曲宽向)的变形一定是伸长变形。
(3)冲压毛坯受异号应力的作用,是拉应力的绝对值大于压应力的绝对值,可以分为下面两种情况:
σr>0>σθ,σt=0,且 σr > σθ
σθ>0>σr,σt=0,且 σθ > σr
相对应的是无压边拉深凸缘的偏内位置、扩口、弯曲外区等,在冲压应力图1.6中处于Ⅱ、Ⅳ象限的AOH及COD范围内。同理可知,在拉应力(绝对值大)的方向上的变形一定是伸长变形,且为最大变形,而在压应力的方向(如拉深的周向、弯曲的径向)的变形一定是压缩变形,而无应力的方向(如拉深的厚向、弯曲的宽向)也是压缩变形。
(4)冲压毛坯变形区受异号应力的作用,且压应力的绝对值大于拉应力的绝对值,可以分为以下两种情况:
σr>0>σθ,σt=0,且 σr > σθ
σθ>0>σr,σt=0,且 σθ > σr
相对应的是无压边拉深凸缘的偏外位置等,在冲压应力图1.6中处于Ⅱ、Ⅳ象限的HOG及DOE范围内。同理,在压应力方向(如拉深外区周向,应力的绝对值大)的变形一定是压缩变形,且为最大变形,在拉应力方向上的变形为伸长变形,无应力方向(厚向)也为伸长变形(增厚)。
综上所述,可以把冲压变形概括为两大类:伸长类变形与压缩类变形。当作用于毛坯变形区内的绝对值最大应力、应变为正值时,称这种冲压变形为伸长类变形,如胀形、翻孔与弯曲外侧变形等。成型主要是靠材料的伸长和厚度的减薄来实现的。这时,拉应力的成分越多,数值越大,材料的伸长与厚度减薄越严重。当作用于毛坯变形区内的绝对值最大应力、应变为负值时,称这种冲压变形为压缩类变形,如拉深较外区和弯曲内侧变形等。成型主要是靠材料的压缩与增厚来实现的,压应力的成分越多,数值越大,板料的缩短与增厚就越严重。
由于伸长类成型和压缩类成型在变形力学上的本质差别,它们在冲压过程中出现的问题和解决的方法也是完全不同的,但是,对同一类变形中的各种冲压方法,却可以用相同的观点和方法去分析和解决冲压中的各种问题。
这两类成型方法的极限变形参数的确定、影响因素和提高的措施等都是不同的。
伸长类成型的极限变形参数主要取决于材料的塑性,并且可以用板材的塑性指标直接地或间接地表示。例如多数实验结果证实:平板毛坯的局部胀形深度、圆柱体空心毛坯的胀形系数、圆孔翻边系数、最小弯曲半径等都与伸长率有明显的正比关系。
压缩类成型的极限变形参数(如拉深系数等),通常都是受毛坯传力区的承载能力的限制,有时则受变形区或传力区的失稳起皱的限制。
由于两类成型方法的极限变形参数的确定基础不同,所以影响极限变形参数的因素和提高极限变形参数的途径和方法也不一样。
提高伸长类成型的极限变形参数的措施如下:
(1)提高材料的塑性,如变形前的退火、分段成型时的工序间退火等。
(2)减小变形不均匀程度。使变形趋向均匀,减小局部的集中变形,可以使总的均匀变形程度加大。例如,在用刚体冲模进行圆柱体空心毛坯的胀形时,均匀而有效的润滑可使变形均匀,提高总体的变形程度。另外,提高材料的硬化指数也能防止产生过分集中的局部变形,并使胀形、翻边、扩口等伸长类成型的极限变形参数得到提高。
(3)消除毛坯变形区的局部硬化层或其他易于引起应力集中而可能导致破坏的各种因素。例如,将带毛刺的毛坯表面置于弯曲模中朝向冲头的方向等方法,可减少伸长类成型中的开裂现象。
提高压缩类成型的极限变形参数的措施有以下几方面:
(1)提高传力区的承载能力和降低变形区的变形抗力、摩擦阻力等。例如,通过建立不同的温度条件而改变传力区和变形区的强度性能的拉深方法,如局部加热拉深、局部深冷。
(2)采取各种有效的措施,防止毛坯变形区的失稳起皱。例如,有效的压边方法、足够大的压边力,有利于防止起皱的模具工作部分的形状和尺寸、合理的中间毛坯的形状等。
(3)以降低变形区的变形抗力为主要目的的退火。例如,多次拉深时的中间退火,这时的退火与伸长类成型时以恢复材料的塑性为主要目的的退火之间有很大的差别,进行退火的意义和方法也不相同,如以极限拉深系数进行一次拉深工序之后,如不退火,仍然可以继续进行下次变形程度较小的拉深工序,但以极限胀形系数进行一次胀形加工后,如不经恢复塑性的退火,再继续进行胀形是不可能的。
3.冲压成型过程中的变形趋向性及其控制
在冲压过程中,成型毛坯的各个部分在同一个模具的作用下,有可能发生不同形式的变形,即具有不同的变形趋向性。保证在毛坯需要变形的部位产生需要的变形,排除其他一切不必要的和有害的变形,是合理制订冲压工艺及合理设计模具的目的。
1)冲压变形的趋向性
(1)冲压毛坯的多个部位都有变形的可能时,变形在阻力最小的部位进行,即“弱区必先变形”。
下面以缩口为例加以分析(图1.7)。稳定缩口时坯料可分为图1.7所示的3个区域,在外力作用下,A、B两区都有可能发生变形,A区可能会发生缩口塑性变形;B区可能会发生镦粗变形。但是由于它们可能产生的塑性变形的方式不同,而且也出于变形区和传力区之间的尺寸关系不同,总是有一个区需要比较小的塑性变形力,并首先进入塑性状态,产生塑性变形。因此,可以认为这个区是个相对的弱区。为了保证冲压过程的顺利进行,必须保证在该道冲压工序应该变形的部分成为弱区,以便在把塑性变形局限于变形区的同时,排除传力区产生任何不必要的塑性变形的可能。

图1.7 变形趋向性对冲压工艺的影响
A-变形区;B-传力区;C-已变形区
“弱区必先变形,变形区应为弱区”的结论,在冲压生产中有着很重要的实用意义。例如,有些冲压工艺的极限变形参数(拉深系数、缩口系数等)的确定,复杂形状零件的冲压工艺过程设计等,都是以这个道理作为分析和计算的依据。
下面仍以缩口为例来说明这个道理。在图1.7所示的缩口过程中,变形区A和传力区B的交界面上作用有数值相等的压应力σ,传力区B产生塑性变形的方式是镦粗,其变形所需要的压应力为σs,所以传力区不致产生镦粗变形的条件是:
σ<σs
变形区A产生的塑性变形方式为切向收缩的缩口,所需要的轴向压应力为σk,所以变形区产生缩口变形条件是:
σ≥σk
由上面两式可以得出在保证传力区不致产生塑性变形下能够进行缩口的条件为:
σk<σs
σk的数值决定于缩口系数d/D。
此外,在设计工艺过程、选定工艺方案、确定工序和工序间尺寸时,也必须遵循“弱区必先变形,变形区应为弱区”的道理。
(2)当变形区有两种以上的变形方式时,需要最小变形力的变形方式首先实现。在工艺过程设计和模具设计时,除要保证变形区为弱区外,同时还要保证变形区必须实现的变形方式要求最小的变形力。例如在缩口时,变形区A可能产生的塑性变形是切向收缩的缩口变形和变形区在切向压应力作用下的失稳起皱;传力区B可能产生的塑性变形是直筒部分的镦粗和失稳。这时,为了使缩口成型工艺能够正常进行,就要求在传力区不产生上述两种之一的任何变形的同时,变形区也不要发生失稳起皱,而仅仅产生所要求的切向收缩的缩口变形。在这4种变形趋向中,只能实现缩口变形的必要条件是与其他所有变形方式相比,缩口变形所需的变形力最小。
2)变形趋向性的控制
在冲压生产中,对毛坯变形趋向性的控制,是冲压过程顺利进行和获得高质量冲压件的根本保证,毛坯的变形区和传力区并不是固定不变的,而是在一定的条件下可以互相转化的。因此改变这些条件,就可以实现对变形趋向性的控制。控制毛坯的变形趋向性的措施有下列几个方面:
(1)变形毛坯各部分的相对尺寸关系是决定变形趋向性最重要的因素,所以在设计工艺过程时要合理地确定初始毛坯的尺寸和中间毛坯的尺寸,保证变形的趋向符合工艺的要求。
(2)改变模具工作部分的几何形状和尺寸能对毛坯变形的趋向性进行控制。
(3)改变毛坯与模具接触表面之间的摩擦阻力,达到控制毛坯变形的趋向。
(4)采用局部加热或局部深冷的办法,降低变形区的变形抗力或提高传力区的强度,都能达到控制变形趋向性的目的,可使一次成型的极限变形程度加大,提高生产效率。例如,在拉深和缩口时采用局部加热变形区的工艺方法,就是基于这个道理。