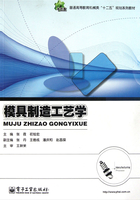
2.1 模具制造的技术要求
模具零件的加工制造要求是保证模具质量的基础。在实际加工中,根据模具的使用情况,各零件的加工制造技术要求不同。下面介绍冷冲模和塑料模加工制造技术要求。
2.1.1 冷冲模制造的技术要求
1.冲裁模的制造要求
在冷冲模制造中,冲裁模的尺寸、形状精度,凸模与凹模的间隙及其均匀性等方面的要求,对冲裁件质量影响最大。冲裁模的凸模与凹模的加工原则如下:
① 落料时,落料制件的尺寸精度取决于凹模刃口尺寸。因此,在加工落料凹模时,应使凹模刃口尺寸与最小极限尺寸相近。凸模刃口的基本尺寸,则应按凹模刃口的基本尺寸减小一个最小间隙值。
② 冲孔时,冲孔制件的尺寸精度取决于凸模刃口尺寸。因此,在加工冲孔凸模时,应使凸模尺寸与孔的最大极限尺寸相近,而凹模基本尺寸,则应按凸模刃口尺寸加上一个最小间隙值。
③ 对于单件生产的冲裁模和复杂形状制件的冲裁模,其凸模与凹模应采用配做法加工。即先按图样尺寸加工凸模(凹模),然后以此为基准,配做凹模(凸模),并加上间隙值。落料时,先制造凹模,凸模以凹模配制加工;冲孔时,先制造凸模,凹模则以凸模配制加工。
④ 由于凸模与凹模长期工作受磨损会使间隙加大,因此,在制造冲模时,应采用最小合理间隙值,同一副模具的凸模与凹模间隙应力求在各个方向上均匀。
⑤ 凸模与凹模的精度,应随制件的精度而定。一般情况下,圆形凸模与凹模应按IT5~IT6精度加工,而非圆形凸模与凹模,可取制件精度的1/4来作为凸模与凹模的加工精度。
2.冲裁模各零件的热处理
冲裁是冷冲压的基本工序之一,它是利用冲裁模在压力机上把被冲材料分离的一种冲压工序。冲裁时切刃陷进被冲材料之中,并承受着强烈的冲击和材料的剧烈摩擦,使刃口部位严重磨损,由开始的锋利到最后变成圆钝,影响了后续制件的质量。为了保证制件质量的长期稳定性,要求冲模的凸模有较高的耐磨性,而且还要有一定的抗压强度、抗弯强度和一定的冲击韧性。而对于凹模,除抗弯强度要求不高外,其抗压强度、韧性及硬度的要求应比凸模更高。因此,在冲裁模凸模与凹模制造时,应正确选用材料,并且用合理的热处理工艺来保证其硬度、韧性等要求。冲裁模各类零件的热处理要求见表2-1和表2-2。
表2-1 冲裁模工作零件的热处理要求
表2-2 冲裁模辅助零件的热处理要求
3.弯曲模的制造要求
弯曲模零件的加工方法与冲裁模基本相同。下面主要介绍凸模与凹模的制造要求。
① 弯曲模工作部分一般形状比较复杂,几何形状及尺寸精度要求较高。在制造时,凸模与凹模工作表面的曲线和折线需要用事先做好的样板及样件来控制,以保证制造精度。样板与样件的精度一般应为±0.05mm。由于回弹的影响,加工出来的凸模与凹模的形状不可能与制件最后形状完全相同,因此,必须要有一定的修正值。该值应根据操作者的实践经验或反复试验后确定,并根据修正值来加工样板及样件。
② 弯曲凸模与凹模的淬火工序是在试模以后进行的。压弯时,由于材料的弹性变形,使弯曲件产生弹性回弹。因此,在制造弯曲模时,必须要考虑材料的回弹值,以便使所弯曲的制件能符合图样所规定的技术要求。影响回弹的因素很多,要求设计得完全准确是不可能的,这就要求在制造模具时,对其反复试验与修正,根据实际情况,对凸模与凹模的尺寸和形状进行精修,直到制品达到规定的要求为止。为了便于修整,弯曲模的凸模与凹模形状及尺寸经试模确定后,才能进行淬硬成型。
③ 弯曲凸模与凹模的加工顺序,应按制件外形尺寸标注情况来选择。对于尺寸标注在内形的制件,一般先加工凸模,而凹模按凸模配制加工,并保证规定的间隙值;对于尺寸标注在外形的制件,应先加工凹模,凸模按凹模配制加工,并保证规定的间隙值。
④ 弯曲凸模与凹模的圆角半径及间隙应加工均匀,工作部位表面应进行抛光,表面粗糙度小于Ra0.40μm。
4.拉深模的制造要求
拉深又称拉延和压延。它是利用模具使平面材料变成开口空心零件的冷冲压方法。其机理是利用拉深凸模与凹模使材料在一定的压力下,产生塑性变形,制造出与拉深模型腔相仿的制件。
(1)拉深模的制造要求
① 拉深模的凸模与凹模工作部分边缘应加工成光滑的圆角。其圆角大小应符合图样规定要求,并经反复试验直到合格时为止。
② 拉深模凸模与凹模表面粗糙度一般要求较高(小于Ra0.40μm),一般可在修整尺寸合格后进行抛光、研磨或镀铬。
③ 拉深模的凸模与凹模的间隙在装配时要均匀。通常在模具装配之前,钳工应首先按制件图样制成一个样件,以便在装配模具时作为样板调整间隙值及检验时用。
④ 拉深模的凸模与凹模热处理淬硬工序,一般在装配试模合格后进行。
⑤ 对于大、中型拉深模,其凸模应留有通气孔,以便于制件拉深后容易卸出。
⑥ 拉深件的毛坯尺寸与形状,通过理论计算很难计算得特别准确。故要通过试模后才能确定其毛坯尺寸及形状。因此,拉深模的加工顺序应该是先制造拉深模,待拉深模试模合格后,再以其所需要的毛坯尺寸制造首次落料拉深模。
(2)拉深模热处理
为适应拉深的工艺特点,拉深模的凸模与凹模应具有高硬度、良好的耐磨性和抗黏附性能。所以,拉深模在热处理时,应注意以下几点:
① 拉深模在淬火过程中,往往会产生表面脱碳或造成软点,使模具的表面硬度和耐磨性降低,造成模具在使用中“拉毛”,影响模具寿命和产品质量。所以,在热处理过程中,应设法防止表面脱碳和出现软点。
② 拉深模工作零件采用的材料,如T10、CrWMn等,经淬火后表面硬度尽管较高,但因其所含高硬度的合金碳化物较少,致使耐磨性较低。工作时,在较大的表面压力下由于被拉深材料的流动与模具型腔表面硬的微凸体尖峰剧烈摩擦,形成了加工硬化结点,加剧了相互摩擦,引起金属材料与模具的咬合。热处理时可采用渗氮等化学处理的方法,减少这种咬合现象。实践证明,模腔表面经化学热处理渗氮后,使其表面形成0.02~0.04mm的化合物强化层,可起到减少磨损和提高表面硬度的作用,使模具寿命大大提高。
总之,拉深模的热处理要求,可根据所采用材料来确定。一般中、小型拉深模,采用T10A、9Mn2V、Cr12、Cr12MoV等材料,热处理的硬度要求:凸模为58~62HRC;凹模为60~64HRC。
5.冷挤压模的制造要求
冷挤压是在常温条件下,利用模具在压力机作用下对金属以一定的速度施加相当大的压力,使金属发生塑性变形,从而获得所需要的形状和尺寸零件的一种加工方法。冷挤压模的制造要求基本上与普通冲模相同。但由于冷挤压时,其模具在压力下强迫金属流动,所需要的挤压力很大,而且磨损遍及凸模与凹模的整个表面。
(1)冷挤压模凸模与凹模的加工
① 在加工凸模时,凸模的两端应预留磨削时打中心孔所需的凸台,并在磨削后切除。
② 凸模在最终加工后,其工作部分应加工出光滑的圆角过渡,即尺寸的变化程度要小,防止在使用时由于应力集中而使凸模被挤裂损坏。
③ 凸模经最后磨削加工后,工作部位应与紧固部位保持同心。工作部位的形状也应严格保持对称,否则不仅会使挤出的制件壁厚不均,而且凸模本身也由于单边受力而被折断。
④ 凸模与凹模在磨削加工前,表面粗糙度应不大于Ra3.2μm,表面不允许有凹凸不平现象。凸模与凹模留磨余量应不小于0.1mm。磨削后应进行研磨抛光,研磨量应不小于0.01~0.02mm。研磨后的表面粗糙度应小于Ra0.20μm。
(2)预应力圈的加工
在冷挤压模具中,为了预防凹模的碎裂,提高其强度,节约贵重的金属材料,一般采用预应力圈组合凹模结构。预应力圈组合凹模的预应力圈可以是单层,也可以是两层以上。其预应力一般是由预应力圈之间的过盈配合获得的。所以在加工时,应特别注意其尺寸配合精度。
(3)冷挤压模热处理
零件在冷挤压时,模具工作部分的凸模与凹模要承受强大的压力,并且工作温度可高达300~400℃。因此,凸模与凹模受压力及热疲劳影响,若强度不足会被镦粗或折断,这就要求模具应具有高强度以及足够的韧性与硬度,同时还需要具有一定的红硬性,即回火稳定性。
冷挤压常用的凸模材料可选Cr12MoV、W18Cr4V,要求硬度为60~62HRC;凹模材料可选Cr12、W18Cr4V、Cr12MoV,要求的淬火硬度为58~60HRC。预应力圈的中圈可采用5CrNiMo、40Cr等材料制成;而外圈则用45、40Cr、35CrMoAlA材料制成,热处理硬度为42~44HRC。
2.1.2 塑料模制造的技术要求
下面讨论塑料注射模和压塑模的制造技术要求。
1.注射模的制造要求
① 零件的加工顺序:成型零件难以加工且热处理易变形,故成型零件应优先加工,如凸模型芯、凹模型腔等零件,并以此作为基准,配作其他零件。
② 成型零件一般均应钳工修整。修整的原则:凸模尽可能修整到最大极限尺寸;凹模尽可能修整到最小极限尺寸,这样可以延长模具的使用寿命。
③ 型腔加工后一般要进行抛光,其抛光纹路原则上应与脱模方向一致。
④ 模具与塑料接触部位的表面粗糙度为Ra0.32~1.25μm。
2.压塑模的制造要求
① 压塑模的型芯与型腔应配合加工。经配合加工后,可用石蜡或橡皮泥边试边修整。待检验合格后,再淬硬及修磨。
② 为了便于取出制品,型芯与型腔应加工出脱模斜度。
③ 导柱、导套安装孔位应一致,配合间隙应合适。成型孔、嵌件孔、型芯固定板上的型芯固定孔等均应与导柱、导套孔保持一定的位置精度,以便模具装配后运动灵活。
④ 成型零件应进行抛光和镀铬,使其表面粗糙度小于Ra0.02μm。
⑤ 顶杆的位置和分布,除按设计加工外,一般应在试模修整后,保证压出的制品不变形来确定顶杆分布位置。
⑥ 储料槽与溢料槽的形状和尺寸,一般也应根据试模情况边试边修整。
3.塑料模的热处理
塑料模一般形状比较复杂,外观及表面质量要求较高。在热处理时一定要控制和避免表面氧化脱碳。而工作部位在工作时,都会承受压力、热及摩擦力,致使型腔和凸模有磨损、开裂、凹陷的危险。故工作部位一定要有较高的硬度和足够的耐磨性,同时还应具有可抛光性及尺寸的稳定性。压塑模具一般不要求整体淬透,只要求有一定的淬硬层。塑料模各类零件的热处理要求见表2-3和表2-4。
表2-3 塑料模工作零件热处理要求
表2-4 塑料模辅助零件热处理要求