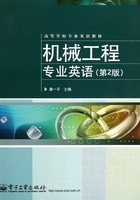
6.5 Laser Beam Machining (LBM)
LASER is an acronym for Light Amplification by Stimulated Emission of Radiation. Although the laser is used as a light amplifier in some applications, its principal use is as an optical oscillator or transducer for converting electrical energy into a highly collimated beam of optical radiation. [6] The light energy emitted by the laser has several characteristics which distinguish it from other light sources: spectral purity, directivity and high focused power density.
Laser machining is the material removal process accomplished through laser and target material interactions. Generally speaking, these processes include laser drilling, laser cutting, laser welding, and laser grooving, marking or scribing.
Laser machining (Fig.6.4) is localized, non-contact machining and is almost reacting-force free.[7] This process can remove material in very small amount and is said to remove material “atom by atom”. For this reason, the kerf in laser cutting is usually very narrow, the depth of laser drilling can be controlled to less than one micron per laser pulse and shallow permanent marks can be made with great flexibility. In this way material can be saved, which may be important for precious materials or for delicate structures in micro-fabrications. The ability of accurate control of material removal makes laser machining an important process in micro-fabrication and micro-electronics. Also laser cutting of sheet material with thickness less than 20mm can be fast, flexible and of high quality, and large holes or any complex contours can be efficiently made through trepanning.

Fig.6.4 Schematic diagram of laser beam machining device
HHHeat Affected ZoneHH (HAZ) in laser machining is relatively narrow and the re-solidified layer is of micron dimensions.[8] For this reason, the distortion in laser machining is negligible. LBM can be applied to any material that can properly absorb the laser irradiation. It is difficult to machine hard materials or brittle materials such as ceramics using traditional methods, laser is a good choice for solving such difficulties.
Laser cutting edges can be made smooth and clean, no further treatment is necessary. High aspect ratio holes with diameters impossible for other methods can be drilled using lasers. Small blind holes, grooves, surface texturing and marking can be achieved with high quality using LBM. Laser technology is in rapid progressing, so do laser machining processes. Dross adhesion and edge burr can be avoided, geometry precision can be accurately controlled. The machining quality is in constant progress with the rapid progress in laser technology.