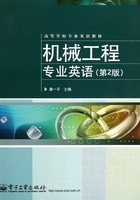
3.2 Sand Casting
The traditional method of casting metals is in sand molds and has been used for millennia. Simply stated, sand casting consists of (1) placing a pattern having the shape of the desired casting in sand to make an imprint, (2) incorporating a gating system, (3) filling the resulting cavity with molten metal, (4) allowing the metal to cool until it solidifies, (5) breaking away the sand mold, and (6) removing the casting.
The following are the major components of sand molds:
1. The mold itself, which is supported by a flask. Two-piece molds consist of a cope on top and a drag on the bottom. The seam between them is the parting line. When more than two pieces are used, the additional parts are called cheeks.
2. A pouring basin or pouring cup, into which the molten metal is poured.
3. A sprue, through which the molten metal flows downward.
4. The runner system, which has channels that carry the molten metal from the sprue to the mold cavity. Gates are the inlets into the mold cavity.
5. Risers, which supply additional metal to the casting as it shrinks during solidification. Fig.3.1 shows two different types of risers: a blind riser and an open riser.
6. Cores, which are inserts made from sand. They are placed in the mold to form hollow regions or otherwise define the interior surface of the casting. Cores are also used on the outside of the casting to form features such as lettering on the surface of a casting or deep external pockets.
7. Vents, which are placed in molds to carry off gases produced when the molten metal comes into contact with the sand in the mold and core. They also exhaust air from the mold cavity as the molten metal flows into the mold.
Patterns are used to mold the sand mixture into the shape of the casting. They may be made of wood, plastic, or metal. The selection of a pattern material depends on the size and shape of the casting, the dimensional accuracy, the quantity of castings required, and the molding process.

Fig.3.1 Schematic illustration of a sand mold