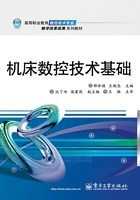
第1章 数控机床的概念及组成
1.1 数控机床的产生与发展
随着社会生产和科学技术的不断进步,各类工业新产品层出不穷。机械制造产业作为国民经济的基础,其产品日趋精密、复杂,特别是宇航、航海、军事等领域所需的机械零件,精度要求更高,形状更为复杂,且往往批量较小,加工这类产品需要经常改装或调整设备,普通机床或专业化程度高的自动化机床无法适应其要求。同时,随着市场竞争日益加剧,生产企业迫切需要进一步提高生产效率,提高产品质量及降低生产成本。在这种背景下,一种新型的生产设备——数控机床应运而生。它综合应用了电子计算机、自动控制、伺服驱动、精密测量及新型机械结构等多方面的技术成果,形成了今后机械工业的基础,并指明了机械制造工业设备的发展方向。
1.1.1 数控机床的产生
数控机床的研制最早是从美国开始的。1948年,美国帕森斯公司(Parsons Co.)在完成研制、加工直升机桨叶轮廓用检查样板的加工机床任务时,提出了研制数控机床的初步设想。1949年,在美国空军后勤部的支持下,帕森斯公司正式接受委托,与麻省理工学院伺服机构实验室(Servo Mechanism Laboratory of the Massachusetts Institute of Technology)合作,开始数控机床的研制工作。经过3年的研究,世界上第一台数控机床试验样机于1952年试制成功。这是一台采用脉冲乘法器原理的直线插补三坐标连续控制系统铣床,其数控系统全部采用电子管元件,其数控装置的体积比机床本体还要大。后来经过3年的改进和自动编程研究,该机床于1955年进入试用阶段。此后,其他一些国家(如德国、英国、日本、苏联和瑞典等)相继开展数控机床的研制开发和生产。1959年,美国克耐·杜列克公司(Keaney & Trecker)首次成功开发了加工中心(Machining Center),这是一种有自动换刀装置和回转工作台的数控机床,可以在一次装夹中对工件的多个平面进行多工序的加工。但是,直到20世纪50年代末,由于价格和其他因素的影响,数控机床仅限于航空、军事工业应用,品种多为连续控制系统。直到20世纪60年代,由于晶体管的应用,数控系统进一步提高了可靠性,且价格下降,一些民用工业开始发展数控机床,其中多数为钻床、冲床等点定位控制的机床。数控技术不仅在机床上得到实际应用,而且逐步推广到焊接机、火焰切割机,。
1.1.2 数控机床的发展概况
数控机床的核心就是CNC系统(简称数控系统)。从自动控制的角度看,数控系统就是一种轨迹控制系统,其本质是以多执行部件(各运动轴)的位移量为控制对象,并使其协调运动的自动控制系统,是一种配有专用操作系统的计算机控制系统。
1.1.3 数控系统的发展史
自从20世纪50年代世界上第一台数控机床问世至今,已经历50余年。数控机床经过了2个阶段和6代的发展历程。
(1)第1阶段是硬件数控(NC)
第1代1952年的电子管;
第2代1959年晶体管(分离元件);
第3代1965年小规模集成电路。
(2)第2阶段是软件数控(CNC)
第4代1970年的小型计算机,中小规模集成电路;
第5代1974年的微处理器,大规模集成电路;
第6代1990年的基于个人PC。
1.数控(NC)阶段(1952—1970年)(Numerical Control)
早期计算机的运算速度低,虽然对当时的科学计算和数据处理影响还不大,但不能适应机床实时控制的要求。人们不得不采用数字逻辑电路“搭”成一台机床专用计算机作为数控系统,称为硬件连接数控(Hard-Wired NC),简称为数控(NC)。随着元器件的发展,这个阶段历经了三代,即1952年的第一代——电子管;1959年的第二代——晶体管;1965年的第三代——小规模集成电路。
(1)常见的电子管是真空式电子管,不管是二极、三极,还是更多电极的真空式电子管,它们都具有一个共同结构,就是由抽成接近真空的玻璃(或金属、陶瓷)外壳及封装在壳里的灯丝、阴极和阳极组成(见图1-1)。直热式电子管的灯丝就是阴极,三极以上的多极管还有各种栅极。以电子管收音机为例,这种收音机普遍使用五六个电子管,输出功率只有1W左右,耗电却要四五十瓦,功能也很有限。打开电源开关,要等1分多钟才会慢慢地响起来。如果用于数控机床,可想而知其耗电量和控制速度。

图1-1 电子管
(2)晶体管是用来控制电路中的电流的重要元件。1956年,晶体管由贝尔实验室发明成功,并因此荣获“诺贝尔物理学奖”,创造了企业研发机构有史以来因技术发明而获诺贝尔奖的先例。晶体管的发明对今后的技术革命和创新具有重要的启示意义。晶体管的发明,终于使由玻璃封装的、易碎的真空管有了替代物。同真空管相同的是,晶体管能放大微弱的电子信号;不同的是,它廉价、耐久、耗能小,并且几乎能够被制成无限小。
晶体管(其实物见图1-2)是现代科技史上最重要的发明之一,究其原因有三个方面。第一,它取代了电子管,成为电子技术的最基本元件,原因是性能好、体积小、可靠性高和寿命长。第二,它是微电子技术革命的发动者,信息时代至今的发展就是由微电子技术、光子技术和网络技术三次技术革命推动的,所以它的出现成为报晓信息时代的使者。第三,晶体管是集成电路和芯片的组成单元,也是光电器件和集成光路的基本组成单元,更是网络技术的基础,只不过光电子晶体管是微电子晶体管的演变或发展罢了。由于这三方面的原因,晶体管的发明在信息科技的迅速发展中起了决定性的重要作用,其意义远远超出了一种元器件的发明范围,成为开创现代技术新领域和变革几乎各种技术基础的关键。所以,晶体管发明过程中的突出特点,对于其他科技的产生和发展有重要的参考和启示意义。

图1-2 晶体管实物
(3)小规模集成电路:晶体管诞生后,首先在电话设备和助听器中使用。逐渐地,它在任何有插座或电池的东西中都能发挥作用了。将微型晶体管蚀刻在硅片上制成的集成电路,在20世纪50年代发展起来之后,以芯片为主的计算机很快就进入了人们的办公室和家庭。
2.计算机数控(CNC)阶段(1970年至今)(Computer Numerical Control)
到1970年,通用小型计算机出现并成批生产。于是人们将它移植过来作为数控系统的核心部件,从此进入了计算机数控(CNC)阶段(把计算机前面应有的“通用”两个字省略了)。
到1971年,美国Intel公司在世界上第一次将计算机的两个最核心的部件——运算器和控制器,采用大规模集成电路技术集成在一块芯片上,称之为微处理器(Microprocessor),又称为中央处理单元(简称CPU)。
到1974年,微处理器被应用于数控系统。这是因为小型计算机功能太强,控制一台机床能力有富裕(故当时曾用于控制多台机床,称之为群控),不如采用微处理器经济、合理。而且当时小型机的可靠性不理想。早期微处理器的速度和功能虽然不够高,但可以通过多处理器结构来解决。由于微处理器是通用计算机的核心部件,故仍称为计算机数控。
到了1990年,PC(个人计算机,国内习惯称为微机)的性能已发展到很高的阶段,可以满足作为数控系统核心部件的要求。数控系统从此进入了基于PC的阶段。最常用的形式是:CNC嵌入PC型,在PC内部插入专用的CNC控制卡。
将计算机用于数控机床是数控机床史上的一个重要里程碑,因为它综合了现代计算机技术、自动控制技术、传感器技术及测量技术、机械制造技术等领域的最新成就,使机械加工技术达到了一个崭新的水平。随着科技的发展,晶体管的体积越来越小,已达到纳米(nm)级(1m=1×109nm)。纳米晶体管的出现,将导致未来可以制造出更强劲的计算机芯片。把20nm的晶体管放进一片普通集成电路,形同将一根头发放在足球场的中央。现代微处理器包含上亿的晶体管。
CNC与NC相比有许多优点,最重要的是:CNC的许多功能是由软件实现的,可以通过软件的变化来满足被控机械设备的不同要求,从而实现数控功能的更改或扩展,为机床制造厂和数控用户带来了极大的方便。
总之,计算机数控阶段也经历了三代,即1970年的第四代——小型计算机;1974年的第五代——微处理器和1990年的第六代——基于PC(国外称为PC-Based)。
对于基于PC的运动控制器,目前最流行的是PMAC。
PMACI型多轴运动控制卡(见图1-3)简介如下:
① 总线:ISA、VME、PC104(见图1-4)、PCI。
② 电机类型:交流伺服、直流电机(有刷、无刷、直线)、交流异步电机、步进电机。
③ 控制码:PMAC(类似BASIC ASICII命令)、G代码(机床)、AutoCAD转换。
④ 反馈:增量编码器(直线、旋转)、绝对编码器、旋转变压器等。

图1-3 DeltaTauPMACI型多轴运动控制卡

图1-4 PMAC运动控制卡(PC104)
PMAC(Program Multiple Axises Controller)是美国Delta Tau公司生产制造的多轴运动控制卡。
(1)计算机直接数控系统
所谓计算机直接数控(Direct Numerical Control,DNC)系统,即使用一台计算机为数台数控机床自动编程,编程结果直接通过数据线输送到各台数控机床的控制箱。中央计算机具有足够的内存容量,因此可统一存储、管理与控制大量的零件程序。利用分时操作系统,中央计算机可以同时完成一群数控机床的管理与控制,因此也称为计算机群控系统。
目前DNC系统中的各台数控机床都有各自独立的数控系统,并与中央计算机连成网络,实现分级控制,而不再考虑让一台计算机去分时完成所有数控装置的功能。
随着DNC技术的发展,中央计算机不仅用于编制零件的程序以控制数控机床的加工过程,而且进一步控制工件与刀具的输送,形成了一条由计算机控制的数控机床自动生产线,为柔性制造系统的发展提供了有利条件。
(2)柔性制造系统
柔性制造系统(Flexible Manufacturing System,FMS)也叫做计算机群控自动线,它是将一群数控机床用自动传送系统连接起来,并置于一台计算机的统一控制之下,形成一个用于制造的整体。其特点是由一台主计算机对全系统的软硬件进行管理,采用DNC方式控制两台或两台以上的数控加工中心机床,对各台机床之间的工件进行调度和自动传送;利用交换工作台或工业机器人等装置实现零件的自动上料和下料,使机床每天24小时均能在无人或极少人的监督控制下进行生产。如日本FANUC公司有一条FMS由60台数控机床、52个工业机器人、两台无人自动搬运车、一个自动化仓库组成,这个系统每月能加工10000台伺服电机。
(3)计算机集成制造系统
计算机集成制造系统(Computer Integrated Manufacturing System,CIMS),是指用最先进的计算机技术,控制从订货、设计、工艺、制造到销售的全过程,以实现信息系统一体化的高效率的柔性集成制造系统。它是在生产过程自动化(例如计算机辅助设计、计算机辅助工艺规程设计、计算机辅助制造、柔性制造系统等)的基础上,结合其他管理信息系统的发展逐步完善的,有各种类型计算机及其软件系统的分析、控制能力,可把全厂的生产活动联系起来,最终实现全厂性的综合自动化。
1.1.4 我国数控机床发展概况
我国从1958年开始由北京机床研究所和清华大学等单位首先研制数控机床,并试制成功第一台电子管数控机床。从1965年开始研制晶体管数控系统,直到20世纪60年代末至70年代初,研制的劈锥数控铣床、非圆插齿机等获得成功。与此同时,还开展了数控铣床加工平面零件自动编程的研究。1972—1979年是数控机床的生产和使用阶段,例如清华大学成功研制了集成电路数控系统;在车、铣、镗、磨、齿轮加工、电加工等领域开始研究和应用数控技术;数控加工中心机床研制成功;数控升降台铣床和数控齿轮加工机床开始小批生产供应市场。从20世纪80年代开始,随着改革开放政策的实施,我国先后从日本、美国、德国等国家引进先进的数控技术。如北京机床研究所从日本FANUC公司引进FANUC3、FANUC5、FANUC6、FANUC7系列产品的制造技术;上海机床研究所引进美国GE公司的MTC-1数控系统等。在引进、消化、吸收国外先进技术的基础上,北京机床研究所开发出BSO3经济型数控系统和BSO4全功能数控系统,航空航天部706所研制出MNC864数控系统等。到“八五”末期,我国数控机床的品种已有200多个,产量已经达到年产10000台的水平,是1980年的500倍。我国数控机床在品种、性能以及控制水平上都有了新的飞跃,数控技术进入了一个继往开来的发展阶段。
1.1.5 数控机床的发展趋势
从数控机床的技术水平看,高精度、高速度、高柔性、多功能和高自动化是其重要的发展趋势。对于单台主机,不仅要求提高其柔性和自动化程度,还要求具有更高层次的柔性制造系统和计算机集成系统的适应能力。我国国产数控设备的主轴转速已达10000~40000r/min,进给速度达到30~60m/min,换刀时间t<2.0s,表面粗糙度Ra<0.008μm。
在数控系统方面,目前世界上几个著名的数控装置生产厂家,如日本的FANUC公司、德国的SIEMENS公司和美国的A-B公司,其产品都在向系列化、模块化、高性能和成套性方向发展。它们的数控系统都采用16位和32位微处理器,标准总线及软件模块和硬件模块结构的内存容量扩大到1MB以上,机床分辨率可达0.1μm,高速进给速度可达100m/min,控制轴数可达16个,并采用先进的电装工艺。
在驱动系统方面,交流驱动系统发展迅速。交流驱动已由模拟式向数字式方向发展,以运算放大器等模拟器件为主的控制器正被以微处理器为主的数字集成元件所取代,克服了零点漂移、温度漂移等弱点。