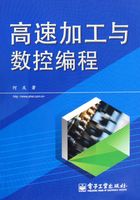
第1章 绪论
1.1 HSM概述
1.1.1 HSM的基本概念
高速加工(High Speed Machining,HSM)也称高速切削(High Speed Cutting,HSC)。国内外文献对HSM的描述主要有以下几种:
(1)国际生产工程科学院(CIRP)切削委员会在1978年提出,线速度在500~7000m/min的切削加工为高速切削加工。
(2)德国Darmstadt工业大学生产工程与机床研究所(PTW)提出,以高于普通切削速度5~10倍的切削加工为高速加工。
(3)对铣削加工,从刀具夹持装置达到平衡要求时的速度来定义高速加工,ISO 1940标准提出,主轴转速超过8000r/min为高速加工。
(4)从主轴设计的角度,以沿用多年的主轴转速特征值DN值来定义高速加工,DN值在(5~15)×105mm·r/min时为高速加工。
(5)从主轴和刀具的动力学角度来进行定义,它取决于刀具振动的主模式频率,在ANSI/ASME标准中用来进行切削性能测试时选择转速范围。
一般认为,高速加工是指采用比常规切削速度和进给速度高得多(一般要大于5~10倍)的速度,来进行高效加工的先进制造技术。HSM一般采用高的主轴转速n、高的进给速度vf,较小的切削深度ap,其切削速度伴随着刀具材料的超硬耐磨性的发展而不断提高,现阶段一般把主轴转速在10000~20000r/min、进给速度在30~100m/min范围的切削,划归为高速加工,图1-1表示为不同材料的切削速度与切削温度HSM曲线图。超过此速度范围,即为超高速切削(Ultra High Speed Cutting,UHSC)。

图1-1 不同材料的切削速度与切削温度HSM曲线图
HSM与普通数控加工在切削参数、刀具、机床等方面,是有一定的区别,如表1-1所示。
表1-1 HSM与普通数控加工的区别

1.HSM的特点
1)减少机加工时间,获得高的加工效率
高速加工采用高的切削速度和进给速度,使单位时间内金属切除量 Zw(Zw=v·f·ap)增大,生产效率得到提高。高速铣削一般只需进行粗、精加工,半精和清根加工则可省略,工艺方案可简化,机加工设备种类也有所减少。此外,高速加工后的表面粗糙度已接近磨削加工的程度,因此可以用HSM来部分代替磨削。以某模具零件的加工为例,传统加工方法和高速加工的工艺路线如图1-2所示。

图1-2 模具传统加工与HSM工序路线图
2)获得高的加工精度和表面质量
(1)HSM时由于ap小,对同样的切削层,表现为切削力下降,工件变形减小。
(2)由于切削速度高,对工件切削作用时间短,大量的切削热来不及传导,就随切屑排出,切削温度下降;工件的热变形小,仅受一次热冲击,工件表面损伤轻,使得表面粗糙度降低,可保持良好的表面机械性能,呈压应力状态。
(3)HSM时与主轴转速有关的激振频率远远高于工艺系统的固有频率,对切削加工的不利因素如振动等被削弱。
3)有利于薄壁件加工
在常规切削条件下,由于切削力大,工件易变形,尤其是薄壁件变形更大。而HSM时,随着切削速度的提高,切削剪切区温度升高,工件材料软化,材料屈服强度降低,使得单位切削力下降,如图1-3所示,利用这一特性可加工薄壁件,且加工时间短,工件变形小,易保证加工质量。在航空工业上,特别是铝的薄壁件加工目前已经可以切出厚度为0.1mm的成形曲面。

图1-3 F-V曲线
4)属于环境友好型加工方式
在一些精密加工中,如模具制造中,型面加工多采用电加工,由于电加工会产生一些有害的气体和烟雾,生产效率也不高,这同目前低能耗、与环境相协调的“绿色制造”的发展方向不相一致,用高速铣削来代替特种加工是模具制造业的一个发展方向。HSM可以获得较好的表面质量(Ra可达0.4μm),这不仅可省去电火花加工后的磨削、抛光等工序,而且在工件表面上可形成压应力,提高模具的寿命。
2.HSM的应用
高速加工机床进给速度可达80m/min,甚至更高,空运行速度可达100m/min左右。目前世界上许多汽车生产家厂,包括我国的上海通用汽车公司,已经采用以高速加工中心组成的生产线部分替代组合机床。美国Cincinnati公司的hypermach机床进给速度最大达60m/min,快进时为100m/min,加速度达20m/s2,主轴转速已达60000r/min。加工一薄壁飞机零件,只用30min,而同样的零件在一般数控铣床加工需3h,在普通铣床加工需8h。
此外,高速加工后的表面粗糙度已接近磨削加工的程度,因此可以用高速切削来部分代替磨削,简化工艺,减少机加工设备,在现代制造中显示出较大的优越性。
1)难加工材料的高速切削
难加工材料(如钛合金、高温合金、不锈钢及高强度合金钢等)在宇航和国防等领域的应用越来越广,但它们的切削加工性差,普通加工只能采用低速切削,制造和应用都受到限制;采用高速切削后,切削热大部分被切屑带走,工件温升不高,制造难度下降。
2)重切削
大型或重型零件在切削加工时,普遍存在的问题是:切削深度大,切削力大,切削时间长,生产效率低。而在高速加工时,由于机床和刀具的性能都较好,且切削力下降。这对提高大型工矿设备的制造效率,有着重要的意义。以新日本工机(SNK)生产大型轧辊为例,采用高速加工后生产效率比普通加工提高了5倍。
3)精密机械制造
在精密机械或光学仪器的制造中,尺寸精度、加工稳定性等往往要求较高。采用高速加工时激振频率很高,工作平稳,易获得较高的尺寸精度。日本研制的转速为55000r/min的超精密铣床,在微细加工方面,它的生产率和相对精度均超过了光刻技术。
此外,HSM在干式切削、石墨电极的高速加工等方面都有着良好的应用前景。